Kaltumgeformte Präzisionsteile direkt im Fertigungsprozess prüfen
Die energieeffiziente Herstellung von Bauteilen ist ein Trendthema in der Industrie. Die Umformtechnik bietet bisher noch unerschlossene Chancen. Doch wie lassen sich die geforderten hochgenauen Fertigungstoleranzen schon frühzeitig sicherstellen?
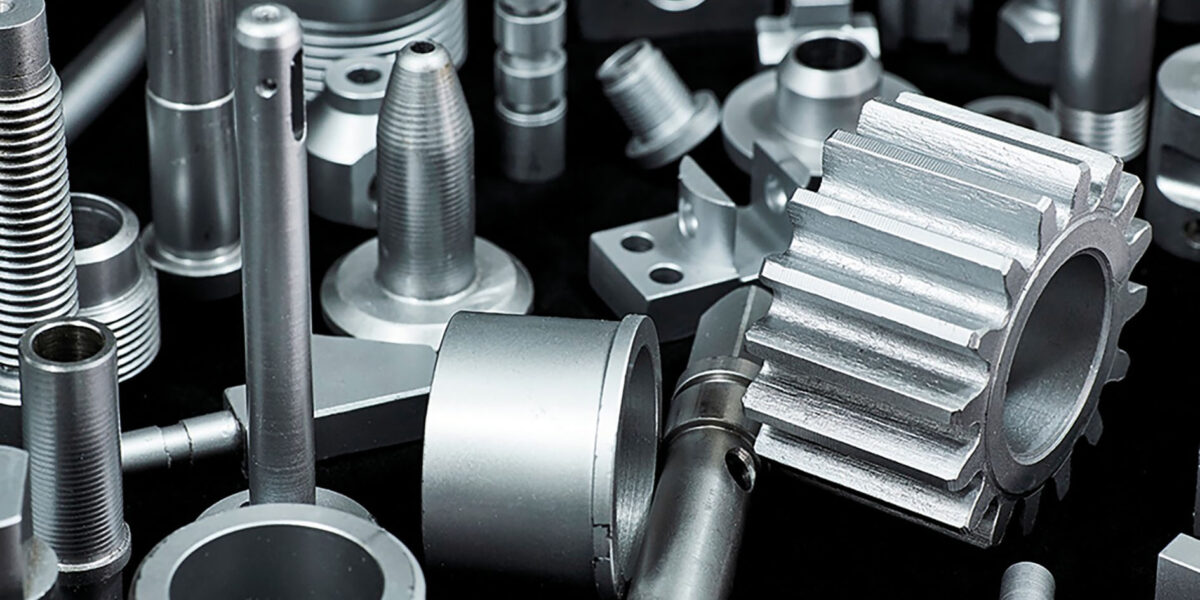
Umgeformte Metallteile: Inline-Messtechnik und Bauteilrückverfolgung schaffen die Grundlage für einen breiteren Einsatz energiesparender Umformverfahren. Gleichzeitig liefern sie digitale Daten für eine optimierte Produktion.
Foto: Shutterstock
Eine innovative Neuheit zu diesem Thema hat ein Institut der Fraunhofer-Gesellschaft entwickelt und stellt dieses in Kürze offiziell vor. Das entstandene optische Inspektionssystem prüft erstmals die Maßhaltigkeit und Oberflächenqualität kaltumgeformter Bauteile bereits während der Produktion. Überzeugend am Verfahren ist unter anderem, dass die Kontrolle mit einer Genauigkeit im Bereich von einigen hundertstel Millimetern möglich ist. Die Technologie soll es erlauben, benötigte Komponenten mit geringen Fertigungstoleranzen in Zukunft durch Umformung statt durch energieintensives Zerspanen herzustellen.
Verantwortlich für die Entwicklung zeichnet das Fraunhofer-Institut für Physikalische Messtechnik IPM in Freiburg. Es präsentiert den Demonstrator des Systems auf der „Hannover Messe“ vom 22. bis zum 26. April 2024.
Warum besser Umformen anstatt zerspanen?
Umformverfahren haben nach Meinung der Forschenden am Fraunhofer IPM einige entscheidende Vorteile, wenn es um die Produktion von Bauteilen aus metallischen Werkstoffen geht. Zur Herstellung sei im Vergleich zur Zerspanung weniger als die Hälfte an Energie nötig. Besonders gering fällt der Energieaufwand bei der Kaltumformung aus. Außerdem: Der große Anteil an (zum Teil verschmutzten) Spänen, der anschließend wieder aufwendig aufbereitet werden muss, entfällt ebenfalls. Ein weiteres Plus: Die Teile haben hervorragende mechanische Eigenschaften, bedingt durch Gefügeveränderungen, die im Umformprozess entstehen.
Der Nachteil bisher: Für Präzisionsbauteile reicht die Genauigkeit bei der Umformung oftmals nicht aus. Daher kommen bei hohen Anforderungen in aller Regel zerspanende Verfahren zum Einsatz, weil sie präziser sind. Voraussetzung für eine breitere Nutzung der Umformung ist somit auch eine hochgenaue Inline-Qualitätskontrolle. Hier setzt das entwickelte Verfahren an: Ein optisches Freifall-Inspektionssystem prüft kaltumgeformte Bauteile mit Genauigkeiten im Bereich einiger hundertstel Millimeter auf geometrische Maßhaltigkeit und Oberflächenqualität. Es wurde im Rahmen eines vom Bundesministerium für Wirtschaft und Klimaschutz geförderten Forschungsprojekts entwickelt.
Prüfung zu 100 Prozent im freien Fall
Eingesetzt werden soll das System am Ende von mehrstufigen Umformprozessen. Dort werden die Bauteile, ohne dass zusätzliches Handling vonnöten ist, über ein Förderband im Sekundentakt einzeln in eine Hohlkugel befördert. Sechzehn gleichmäßig über die Oberfläche der Kugel verteilte Kameras nehmen das Bauteil im freien Fall durch die Kugel gleichzeitig auf, sodass jede Stelle des Teils mindestens einmal abgebildet wird. Das System prüft Bauteile mit einer Kantenlänge von 0,5 cm bis 6 cm.
Eine schnelle Datenauswertung ermöglicht die direkte Rückkopplung in den Produktionsprozess. Prozessparameter lassen sich rasch anpassen und damit Ausschuss reduzieren. Bei Einfahrprozessen oder möglichen Änderungen von Materialeigenschaften, zum Beispiel bei einem Coil-Wechsel, unterstützt die Messtechnik dabei, den Prozess schneller zu adaptieren.
„Fingerprint“ der Bauteiloberfläche für die Rückverfolgung
In vielen Branchen mit sicherheitskritischen Anforderungen wird erwartet, die Entstehung von Zulieferteilen genau rückverfolgen zu können. Zusätzlich zur Qualitätsprüfung soll es daher in Zukunft möglich sein, bei der Bildaufnahme die individuelle Oberflächenstruktur an einer definierten Stelle hochaufgelöst aufzunehmen. Diese lässt sich quasi als Fingerabdruck des Bauteils für die Rückverfolgung in einer Datenbank registrieren. So können die Bauteile später – durch eine erneute Bildaufnahme der Oberflächenstruktur an der Fingerprint-Stelle – identifiziert werden. Damit lassen sich die Prozessparameter oder Qualitätsmerkmale den individuellen Bauteilen zuordnen. Mit der Möglichkeit zur Rückverfolgung legt das Inline-Inspektionssystem zudem die Grundlage für eine selbstlernende Optimierung von Umformprozessen.
Das Fraunhofer IPM präsentiert das Inline-Messystem gemeinsam mit der Firma Sotec als Demonstrator auf der Hannover Messe: Zu sehen ist es am Gemeinschaftsstand des Bundesministeriums für Wirtschaft und Klimaschutz BMWK in Halle 2, Stand A18.
Das könnte Sie auch interessieren:
Qualität in der Industrie sichern mittels Terahertz-Spektroskopie
Geprüfte Brennstoffzellen-Komponenten als Wegbereiter für klimaneutrale Mobilität
Zuverlässig inspizierte Turbolader dank Bildverarbeitung
Perfekte Steckverbinder dank Inline-Prozessüberwachung beim Stanzen