Automobilbau: Qualitätsprüfung mit Augmented Reality
Augmented-Reality-Technologien des Fraunhofer-Instituts für Graphische Datenverarbeitung IGD vereinen reale und digitale Produktionsumgebung und lassen so auf den ersten Blick Abweichungen zwischen Ist und Soll erkennen.
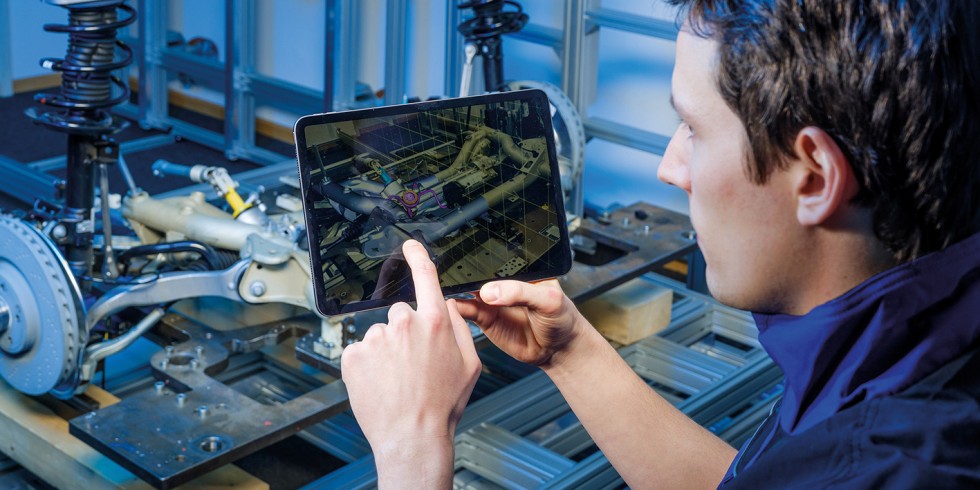
Für den Soll-Ist-Abgleich mithilfe des mobilen AR-Prüfsystems nimmt der Prüfingenieur die Bauteile auf, die lagerichtig mit den CAD-Modellen überlagert werden.
Foto: Fraunhofer IGD
Die fertigende Industrie bedarf einer verlässlichen Qualitätskontrolle, die sich dennoch nahtlos in den Fertigungsprozess eingliedert. Ohne die Produktivität zu gefährden, müssen moderne Systeme der Qualitätssicherung dennoch so agil sein, dass sie an verschiedene Produktkonfigurationen angepasst werden können. Automatisierte, durch Computer-Vision unterstützte Systeme sollen jetzt die Qualitätskontrolle in der Automobilproduktion objektivieren. Das Fraunhofer IGD hat gemeinsam mit der Daimler AG, der Tigris Elektronik GmbH und der Ensenso GmbH im Rahmen des Projektes „Scrutinize3D“ ein vollautomatisches System zur optischen Qualitätssicherung im Fahrzeugbau entwickelt. Ziel war die Etablierung einer Methodik, die modellbasiert eine Qualitätskontrolle für zusammengesetzte Bauteile an der Produktionslinie durchführt. Das Projekt wurde Anfang 2019 abgeschlossen und das System ist nun einsatzbereit – im Automobilbau oder anderen Bereichen der fertigenden Industrie.
Qualitätsprüfung ist direkt an der Produktionslinie möglich
Wenn eine AR-basierte Qualitätsprüfung direkt in die Produktionslinie integriert wird, ist ein weitestgehend automatisiertes Qualitätskontrollverfahren wesentlich. Gerade im Automobilbau ist zu beachten, dass in ein und derselben Linie unterschiedlichste Produktkonfigurationen gefertigt werden. Eine Umstellung der Prüfverfahren auf die unterschiedlichen Konfigurationen kann daher am einfachsten über die zugehörigen CAD-Modelle erfolgen, welche als Grundlage für den Prüfprozess dienen.
Konkret sieht das Prüfsystem folgendermaßen aus: An einer Produktionslinie werden mehrere miteinander synchronisierte Kameras fest verbaut. Man spricht von einem Kameraarray. Das Qualitätskontrollsystem bekommt von der Produktionssteuerung eine Meldung, welche Produktkonfiguration als nächstes gefertigt wird. Das entsprechende CAD-Modell wird als Referenzdatensatz herangezogen. Die Prüfkameras erfassen Position und Ausrichtung der Prüfteile.
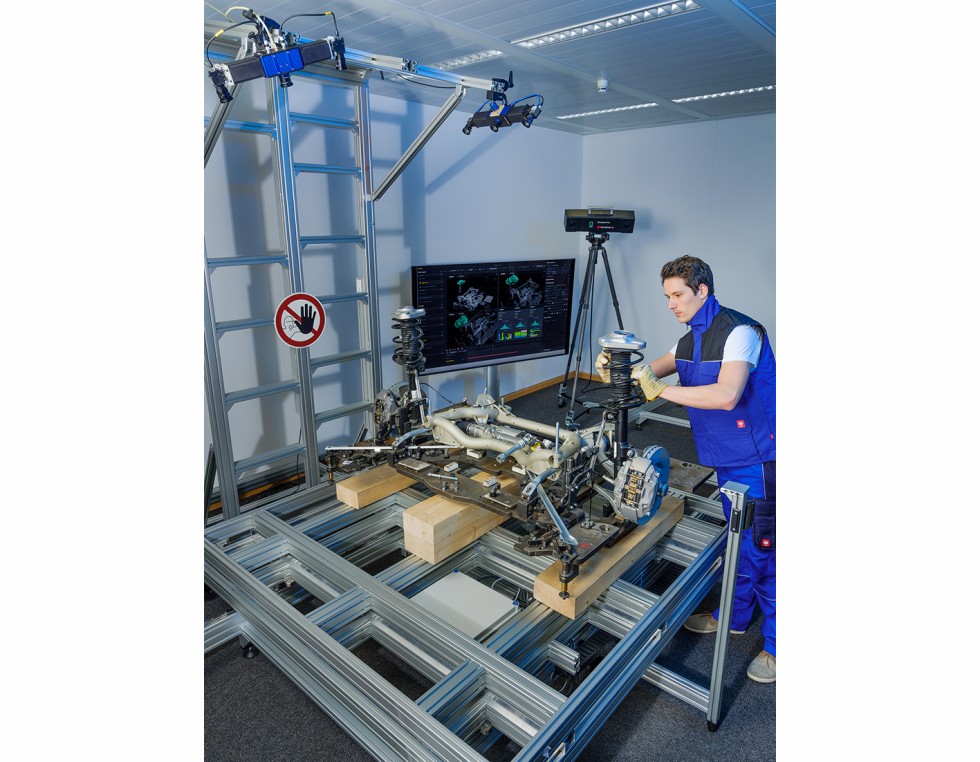
Für das Qualitätskontrollsystem, das an der Produktionslinie installiert wird, werden mehrere Kameras um die Linie herum aufgebaut.
Foto: Fraunhofer IGD
Das Produktionskontrollsystem prüft nun mithilfe der vom Fraunhofer IGD integrierten Algorithmen, ob ein Bauteil für den nächsten Verarbeitungsschritt korrekt positioniert ist. Es wird als „nicht in Ordnung“ (n.i.O.) eingestuft, wenn es von der Spezifikation im CAD-Datensatz abweicht. Außerdem prüft das System, ob alle Prüfbauteile, die im CAD-Datensatz enthalten sind, im Kamerabild detektiert werden. Sprich: Es wird kontrolliert, ob ein Bauteil fehlt.
Erkennt das System eine Abweichung, stoppt es das Band und signalisiert den Werkern die Notwendigkeit zum Eingreifen.
Live-Abgleich mit den CAD-Daten gibt Gewissheit
Der entscheidende Vorteil gegenüber vergleichbarer und am Markt etablierter Systeme liegt auf der Hand: Durch den Live-Abgleich mit den CAD-Daten, also den ursprünglichen Konstruktionsdaten, wird der Qualitätscheck nicht nur besonders genau, sondern auch schnell. Alternative Lösungen arbeiten auf Basis von Referenzbildern, das heißt, dass Kamera und System viele Hundert Beispielbilder brauchen, um Abweichungen von der Norm zu erkennen. Das bedeutet ein langwieriges Anlernen, das jedes Mal wiederholt werden muss, wenn sich die Produktvariante oder einzelne Bauteile ändern. Auch hier zeigt das Fraunhofer-System seine Stärken: Ändern sich Fahrzeugkomponenten und damit die Anforderungen an die Qualitätsprüfung, greift es einfach auf eine andere CAD-Datenbasis zu. Damit ist es sehr flexibel und schnell in neuen Situationen einsatzbereit. Prüfverfahren erhalten so eine Agilität, welche sie vorher nicht hatten.
Eine Hürde galt es bei der Entwicklung des Systems zu nehmen: zwar erkennt das AR-System die relative Ausrichtung zwischen Prüf- und Referenzteil, nicht jedoch, wenn ein Bauteil an sich fehlerhaft oder deformiert ist. Deshalb wurde das Kameraarray um 3D-Stereokameras ergänzt. Diese rekonstruieren die exakte Geometrie des Bauteils und vergleichen das so entstandene 3D-Duplikat mit dem CAD-Modell.
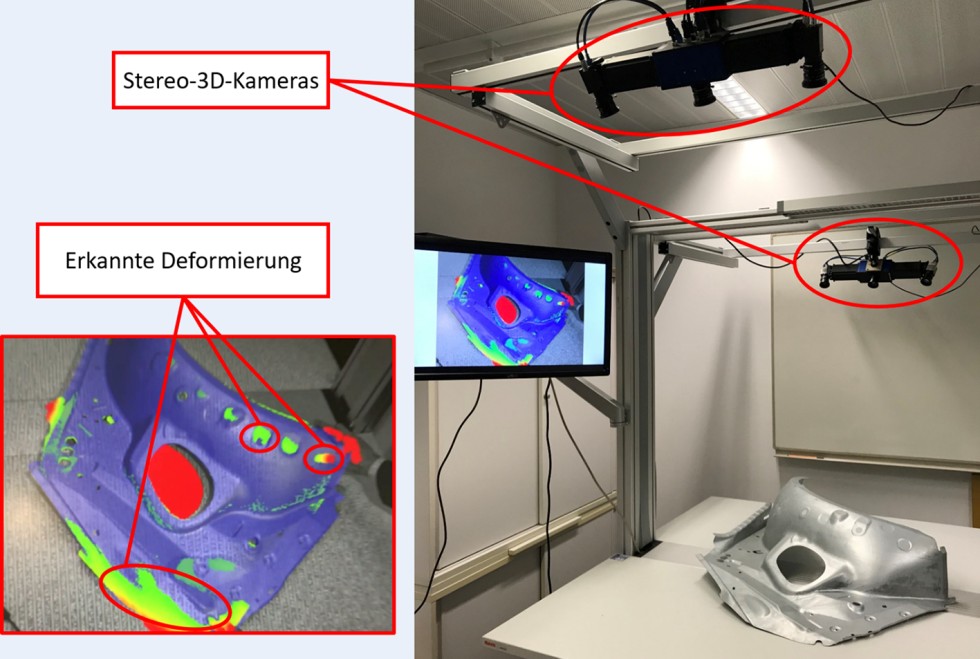
Durch die Verwendung von 3D-Kameras kann die Geometrie der Bauteile rekonstruiert und mit dem CAD-Modell verglichen werden. Dadurch werden beschädigte oder verformte Bauteile identifiziert.
Foto: Fraunhofer IGD
Differenzen zwischen 3D-Rekonstruktion und CAD-Geometrie werden pixelweise berechnet und in Falschfarben dargestellt – fehlerhafte Bauteile werden so auf einen Blick erkannt.
Mobile Qualitätsprüfung nützt auch in weiteren Bereichen
Auch abseits der Produktionslinie ist eine schnelle und zuverlässige Qualitätssicherung gefragt, zum Beispiel in der Warenein- oder -ausgangskontrolle. AR-basierte Systeme ermöglichen Prüfingenieuren, Bauteile mit der Handy- oder Tabletkamera zu erfassen und kontinuierlich und lagerichtig mit dem CAD-Datensatz zu überlagern. In Echtzeit werden nun die fehlerhaft verbauten oder fehlenden Bestandteile visualisiert.
Zusätzlich ermöglicht dies auch eine Qualitätsprüfung außerhalb des Werkes – bei bereits ausgelieferten Kundenproduktionen oder Zulieferern.
Das Fraunhofer-Institut für Graphische Datenverarbeitung IGD ist die international führende Einrichtung für angewandte Forschung im Visual Computing. Ein Schwerpunkt liegt in der Entwicklung von Industrie 4.0- Technologien. Dabei decken die Forschungen den gesamten Produktzyklus ab, angefangen bei der Konzeption, der digitalen Konstruktion und der Produktionsvorbereitung über das Prototyping bis hin zur Fertigung und Qualitätskontrolle. Holger Graf leitet die Abteilung „Virtual & Augmented Reality“, die zahlreiche Industrieprojekte zur Anwendung der Technologien in den Bereichen „Produktion“, „Wartung“ und „Qualitätskontrolle“ durchführt.
www.igd.fraunhofer.de
Das könnte Sie auch interessieren:
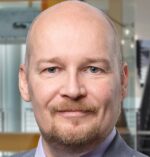
Dipl. Math.-Techn. Holger Graf, M. Sc., ist Head of Competence Center Virtual & Augmented Reality am Fraunhofer-IGD in Darmstadt.