Messtechnik macht Batterien für die E-Mobilität serienreif
Die Zukunft der Automobilindustrie liegt in der E-Mobilität. Und die Zukunft ist bereits serienreif – dank moderner Qualitätssicherungslösungen für die benötigten, sicherheitsrelevanten Komponenten. Beispiele sind aktuell auf der Messe Control zu sehen.
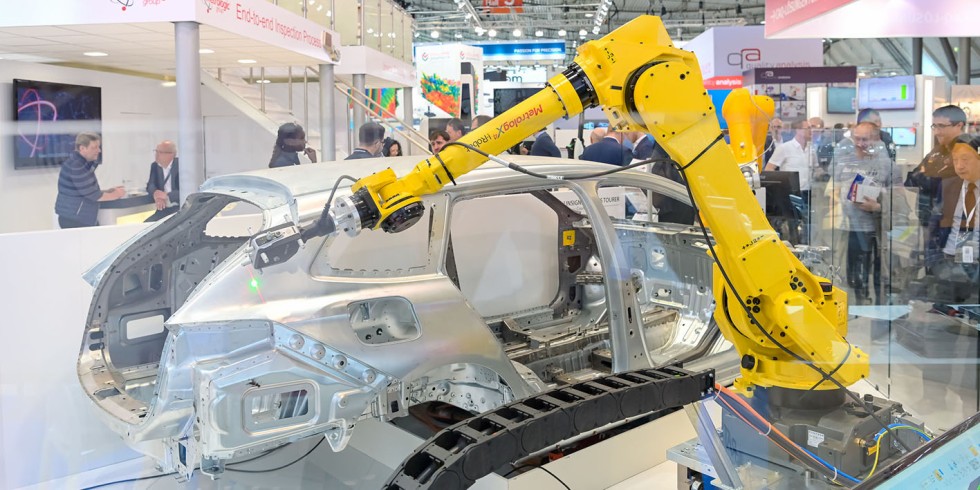
Die auf der Messe Control vertretenen Hersteller von Qualitätssicherungs-Equipment verhelfen den produzierenden Unternehmen mit ihren Innovationen zu mehr Wettbewerbskraft.
Foto: P.E.Schall
Aussteller und Fachbesucher können sich nun endlich wieder auf der „Control“ – 34. Internationale Fachmesse für Qualitätssicherung (QS) treffen, die vom 3. bis zum 6. Mai 2022 in Stuttgart stattfindet. Die Messe beleuchtet in Theorie und Praxis das aktuelle Weltangebot an nutzbaren Technologien, Verfahren und Systemlösungen zur industriellen Qualitätssicherung.
Breites Spektrum an QS-Technologien
Im Fokus stehen auch 2022 Neuheiten aus den Bereichen Vision-Technologie, Bildverarbeitung, Sensortechnik sowie Mess- und Prüftechnik. Mehr als ein Drittel der angemeldeten Aussteller kommen aus dem Ausland. Die Internationale Fachmesse für Qualitätssicherung gilt als Leitmesse für die Messtechnik und ist seit Jahrzehnten ein ideales Forum für den persönlichen Kontakt und den geschäftlichen Fachaustausch. Nach zwei Jahren Zwangspause trifft das ganz besonders zu.
Der Bedarf an fachlicher Diskussion über Neuentwicklungen der QS-Branche ist groß. Viele Unternehmen führen aktuell erweiterte oder ganz neue QS-Systeme ein – angetrieben durch Trends wie zunehmende Automatisierung und Digitalisierung, vermehrte kontaktlose Abläufe, Remote-Services, kleinere Losgrößen und Null-Fehler-Fertigung. Die Notwendigkeit der Qualitätsüberprüfung jeglicher Prozesse samt Datenanalyse und einer durchgehenden Rückverfolgung betrifft inzwischen fast alle Branchen – sowohl aus dem industriellen, als auch dem Dienstleistungsumfeld. Lösungen und Systeme der Mess- und Prüftechnik, Werkstoffprüfung, Analysegeräte, Visionstechnologie, Bildverarbeitung, Sensortechnik sowie Wäge- und Zähltechnik sind in den vergangenen zwei Jahren wesentlich weiterentwickelt worden. Auf der Control 2022 werden sie nun endlich wieder auf ein hochinteressiertes Fachpublikum treffen.
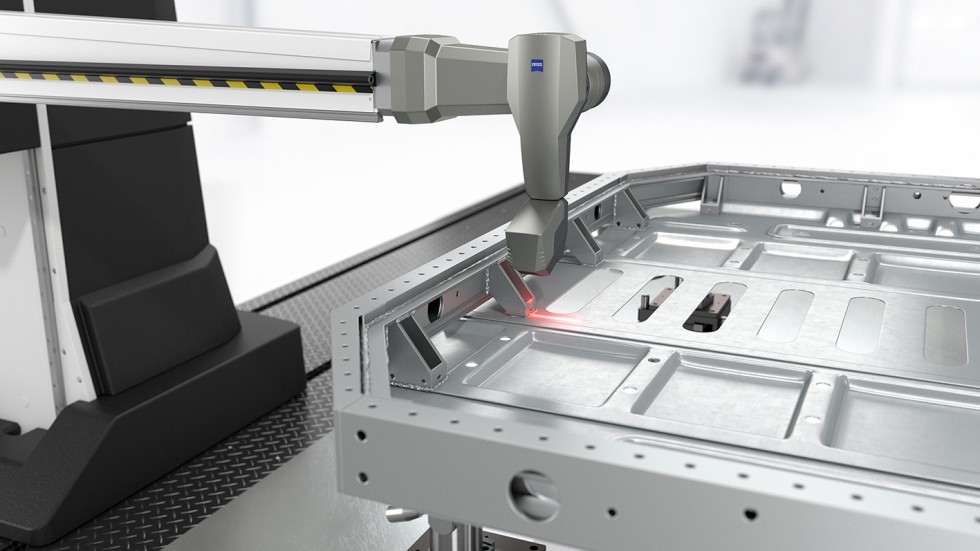
Diverse Mikroskope sowie Computertomografen, Koordinatenmessgeräte und optische 3D-Messmaschinen ermitteln die sicherheitsrelevanten Daten von Batterien.
Foto: Zeiss
Gemeinsam die Zukunft „auf die Straße bringen“
Auch die Automobilindustrie hat großes Interesse an den vorgestellten Lösungen. Der Markt für Elektrofahrzeuge wächst weltweit rasant. Im Jahr 2021 war in Europa erstmals ein E-Fahrzeug der meistverkaufte Pkw – das „Tesla Model 3“. Die steigende Nachfrage nach New Energy Vehicles (NEVs) bedeutet für Hersteller und deren Zulieferer eine höhere Geschwindigkeit in der Entwicklung und der Produktion. Und das stellt den Qualitätssicherungs (QS)-Prozess vor neue Herausforderungen. Insbesondere die Batterien sind sicherheitsrelevante und strukturgebende Komponenten im E-Fahrzeug.
Gleichzeitig steigen die Erwartungen an die Leistungsfähigkeit der Batterietechnik, also die Reichweite mit einer Ladung. Wer zuverlässige Batterien mit langer Lebensdauer bauen will, kommt um höchste Qualitätsstandards nicht herum: Zellen, Module und Wanne müssen in sehr engen Toleranzen gefertigt werden. Daher sind sowohl für Forschung und Entwicklung als auch die QS von Batterien und -wannen unterschiedliche Lösungen für Bildgebung, Analyse und Messtechnik entscheidend.
„Für das Kernstück von Elektrofahrzeugen, die Batterie, hat Qualitätssicherung bei den Herstellern oberste Priorität. Sie ist ein Muss.“ Albert Mo, Competence Center Manager Zeiss eMobility Solutions.
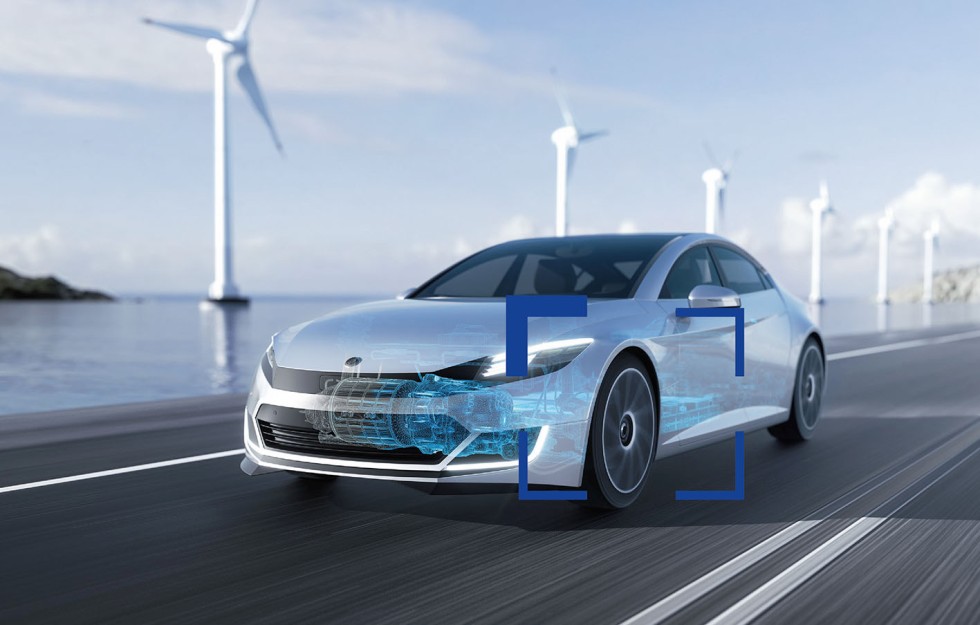
Elektrofahrzeuge werden immer häufiger gekauft und permanent weiterentwickelt. Die steigende Nachfrage stellt bei den Herstellern und deren Zulieferern auch den Qualitätssicherungsprozess vor neue Herausforderungen.
Foto: Zeiss
QS betrifft alle Lebenszyklusphasen bei Batteriemodulen
Der Qualitätssicherungsprozess für Batterien ist komplex: Batterieeigenschaften werden auf den Ebenen von Material, Elektrode, Zelle, Modul und Batteriewanne mithilfe verschiedener Messtechnologien überprüft:
- Bereits in der Batterieentwicklung gestattet industrielle Mikroskopie die Analyse der Mikrostruktur und von möglichen Verunreinigungen.
- In der Batterieproduktion wiederum ist die zerstörungsfreie Analyse der Batteriezellen und -module notwendig, hier kommen verstärkt X-Ray-Systeme und Computertomografie zum Einsatz.
- Licht-, Elektronen- und Röntgenmikroskope sowie Computertomografen (CT), Koordinatenmessgeräte (KMG) und optische 3D-Messmaschinen stellen die relevanten Daten bereit, um die Sicherheit und Leistungsfähigkeit der Batterien zu gewährleisten.
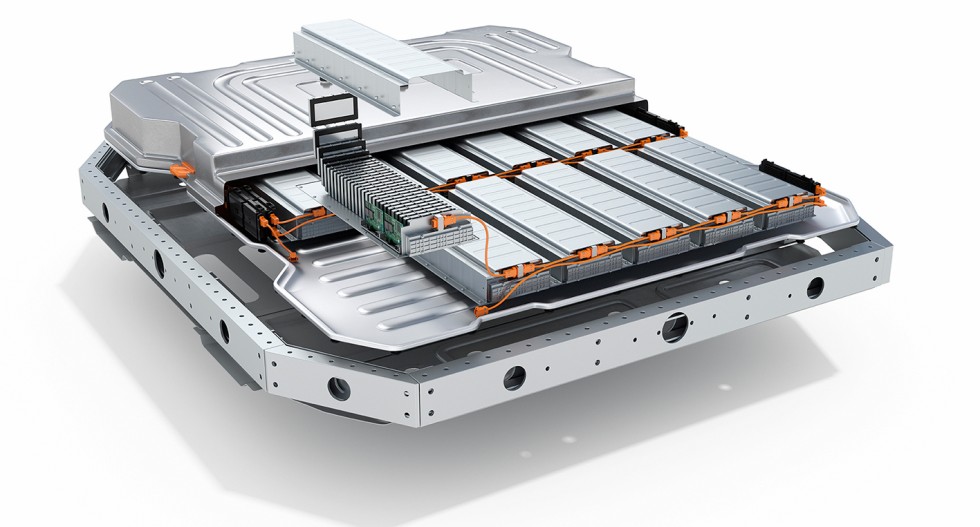
Explosionszeichnung einer Batterie: Zellen, Module und Wanne müssen in engen Toleranzen gefertigt werden. Grafik: Zeiss
Computertomograf erkennt versteckte Defekte in dichten Bauteilen
Mit dem Computertomografen „VoluMax 9 titan“ von Zeiss können dichte Bauteile wie Batteriemodule effektiv durchleuchtet werden. Das System mit 450 Kilovolt Beschleunigungsspannung und einer Röhrenleistung von 1500 Watt ist es aktuell das kompakteste seiner Klasse, weshalb es sich bestens für die QS in der Produktionslinie eignet. Generiert werden 3D-Volumendatensätze mit besonders hoher Voxel-Auflösung. So erkennt das Gerät versteckte Defekte bei dichten Bauteilen. Mehr Voxel heißt mehr sehen: zum Beispiel Elektrodendefekte, Fehlausrichtungen, Überhänge, Gehäuseeinschlüsse und Partikelkontaminationen. Letztere sind ein großes Sicherheitsrisiko und dürfen im Endprodukt nicht vorkommen. Auch bei der Schweißnahtkontrolle bleibt keine Unregelmäßigkeit unentdeckt.
Um der Nachfrage nach Elektrofahrzeugen mit höherer Reichweite gerecht zu werden, muss eine immer höhere Energiedichte in den Zellen erreicht werden, ohne dass diese dabei schwerer und größer werden. Die Materialdichte nimmt demnach zu, was eine zerstörungsfreie Inspektion durch das „Durchleuchten“ zu einem anspruchsvollen Prozessschritt macht. Die zu prüfenden Details haben sich dabei deutlich verkleinert: Heute geht es zum Teil um Merkmale, die nur noch 10 Mikrometer groß sind.
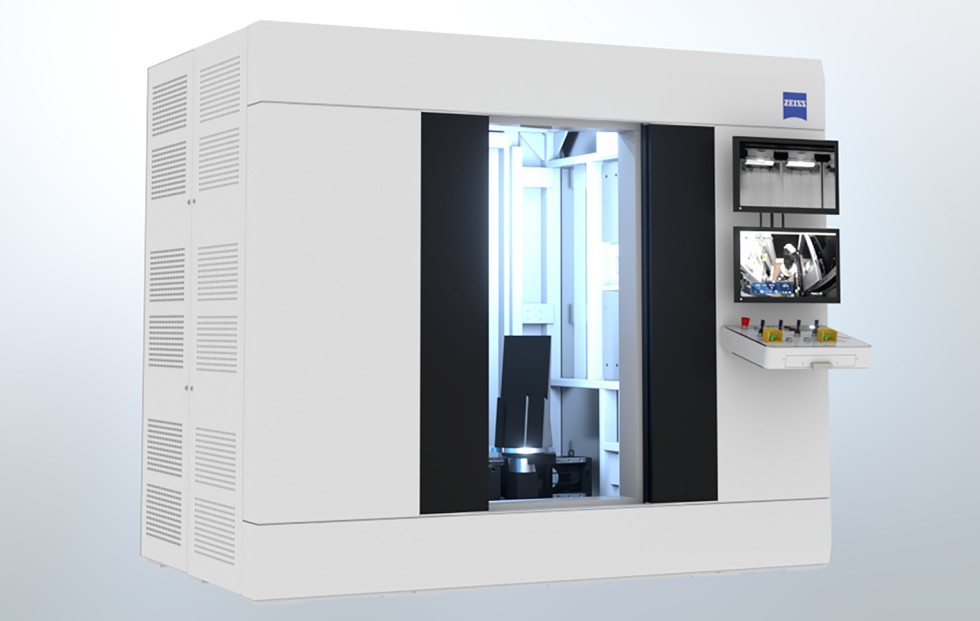
Der Computertomograf „VoluMax 9 titan“ durchleuchtet dichte Bauteile wie Batteriemodule. Das besonders kompakte Gerät eignet sich ideal für die QS in der Produktionslinie.
Foto: Zeiss
Batteriewannen in ihrer Gesamtheit prüfen
Die Batteriewanne – auch Batterieträger genannt – ist eine weitere wichtige Komponente in New Energy Vehicles. Sie ist nicht mehr nur ein Bauteil, sondern vollständig in die Karosserie integriert und dadurch mitentscheidend für deren Stabilität. Der Produktionsprozess von Batteriewannen umfasst mehrere Quality Gates, die durchlaufen werden müssen, um Sicherheitsanforderungen zu erfüllen und die Qualität des Fahrzeugs zu gewährleisten.
Eines dieser Gates stellt dabei die Bewertung der Geometrie als Ganzes dar. Ebenheit, Passgenauigkeit und Dichtungsbereiche des Batterieträgers haben Einfluss auf die Maßhaltigkeit der gesamten Karosserie. Die Batteriemodule müssen mit Wärmeleitpaste korrekt in die Batteriefächer eingepasst werden, um einen sicheren Betrieb zu gewährleisten.
Software in der Messmaschine automatisiert den Prüfprozess
Die optische 3D-Messmaschine „Atos ScanBox“ in Kombination mit der Software „GOM Inspect Pro“ misst das Bauteil automatisch und erstellt einen digitalen geometrischen Zwilling sowohl von der Batteriewanne als auch vom Batteriepack selbst. Eine vollständige Inspektion der relevanten Merkmale, wie Ebenheit der Batteriefächer und Position von Verbindungslöchern, dauert nur Minuten. Prozessrelevante Prüfmerkmale lassen sich dabei auch statistisch im Trend auswerten, um etwa Spaltmaßänderungen durch thermische Verformung der Batteriemodule zu erkennen.
Virtuell wird schließlich die Montage von Wanne und Modulen in der Karosserie samt Verkabelung simuliert, um die Qualität des Montageprozesses prognostizieren zu können. Die Analyse umfasst alle wichtigen Schritte der Batteriewannenproduktion – vom Aluminium-Strangpressen über das Gießen und Schweißen, den Klebstoffauftrag bis hin zum Fräsen sowie Bohr- und Nietanwendungen.
Besonders effizient: In der Software der optischen 3D-Messmaschine werden Roboterposition und -pfad vollautomatisch anhand der CAD-Daten des Bauteils eingelernt. Komplette Geometrien werden bei geringem Rauschpegel erfasst – auch bei dunklen oder glänzenden Oberflächen. Die fortschrittliche Messtechnik ist rückführbar und entspricht dem ISO-10360-Standard.
Das könnte Sie auch interessieren:
Warum wasserdicht nicht gleich wasserdicht ist
Positionserkennung: Garant für hohe Qualität in der Motoren-Manufaktur
Vorausschauende Überwachung von Schmiedeprozessen