Sensoren als „Nervensystem“ von Rotorblättern
Windenergie ist einer der wichtigsten Bausteine, um die anstehende Energiewende zu bewältigen. Entsprechend bedeutsam ist die Grundlagenforschung an den beteiligten Komponenten. Was kann moderne Sensorik zur Verbesserung des Wirkungsgrads beitragen?
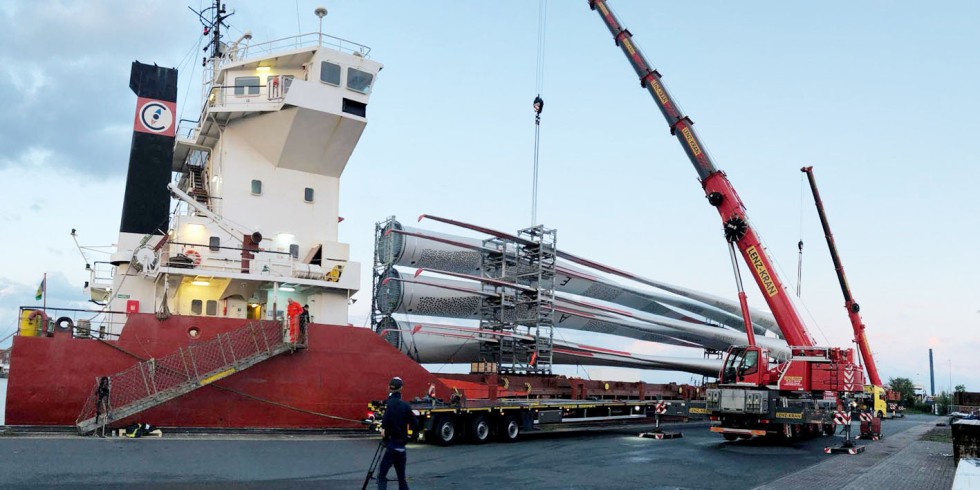
Nach ihrer Schiffsreise von Portugal nach Deutschland hatten die sechs riesigen Rotorblätter noch einen Zwischenstopp in Bremerhaven für Tests vor sich, bevor sie jetzt im Forschungspark in Krummendeich montiert werden.
Foto: DLR
Der Energieträger Wind ist kostenlos und unbegrenzt verfügbar. Windenergieanlagen nutzen die Bewegungsenergie des Windes, die durch unterschiedliche Luftdruckverhältnisse in der Nähe der Erdoberfläche entsteht. Um diesen „Rohstoff“ zu erschließen, formt der Rotor der Anlage die Bewegungsenergie des Windes zunächst in mechanische Rotationsenergie um. Ein Generator wandelt diese anschließend in elektrische Energie um. Entscheidend für einen hohen Stromertrag sind vor allem hohe mittlere Windgeschwindigkeiten und die Größe der Rotorfläche.
Rotorblätter gehören also zu den Kernkomponenten einer Windenergieanlage. Sie sind bis zu 70 Meter lang und wiegen zwischen 15 und 20 Tonnen. Um Windenergieanlagen in Zukunft effizienter zu betreiben und auch Standorte nutzen zu können, die weniger windintensiv sind, sind noch größere und gleichzeitig leichtere Blätter vonnöten. Wie sich das realisieren lässt und welche technischen Herausforderungen damit verbunden sind, untersucht das Deutsche Zentrum für Luft- und Raumfahrt (DLR) mit Partnern aus Forschung und Industrie.
Einmalige Chance: Wissenschaft im „Realmaßstab“ im Forschungspark betreiben
Der im Aufbau befindliche Forschungspark Windenergie des DLR – genannt „WiValdi“ (Wind Validation) – der künftig in Krummendeich betrieben wird, bietet dazu eine einmalige Gelegenheit: Über mehrere Wochen haben im Frühjahr 2022 Wissenschaftlerinnen und Wissenschaftler die Produktion von sechs Rotorblättern für die beiden Windenergieanlagen des Forschungsparks begleitet. Beteiligt waren daran die beiden DLR-Institute für Aeroelastik sowie für Faserverbundleichtbau und Adaptronik, außerdem die zum Zentrum für Windenergieforschung „ForWind“ gehörende Leibniz Universität Hannover.

Arbeiten in einer Blatthälfte: Von der Spitze bis zur Rotorblattwurzel wurde modernste Messtechnik für die Untersuchungen installiert.
Foto: DLR
Im portugiesischen Werk des Industriepartners Enercon rüstete das 30-köpfige Team die Rotorblätter mit rund 1.500 Sensoren aus. Von der Blattspitze bis zur Blattwurzel steht damit nun modernste Messtechnik bereit. Diese gestattet es erstmalig, das Schwingungs- und Belastungsverhalten sowie die Aerodynamik und Statik einer Windenergieanlage im Realmaßstab und Praxisbetrieb umfassend wissenschaftlich zu untersuchen.
Informationen sammeln: 1.500 Sensoren für das „Rotorblatt der Zukunft“
„Wenn man große und leichte Blätter hat, werden diese sehr elastisch und flexibel. Sie biegen sich unter Windlast durch. Damit sind neue technische Herausforderungen verbunden, die es genau zu erforschen gilt“, erklärt Dr.-Ing. Yves Govers vom DLR-Institut für Aeroelastik und Leiter des Arbeitspakets zur Instrumentierung. Die Rotorblätter der beiden Windenergieanlagen des Forschungsparks sind 57 Meter lang und können sich mehrere Meter durchbiegen.
Das DLR-Institut für Aeroelastik ist führend auf den Gebieten Aeroelastik, Strukturdynamik, instationäre Aerodynamik und dynamische Lasten. Es beschäftigt in Göttingen mehr als 90 Mitarbeitende. Für grundlagen- und anwendungsorientierte Experimente am Boden, in Windkanälen bzw. im Flugversuch werden drei DLR-Großanlagen betrieben.
„Die Sensoren kann man sich wie das menschliche Nervensystem vorstellen. Sie sammeln Informationen, überwachen und geben Hinweise, wo ein Problem auftauchen könnte“, veranschaulicht DLR-Forscher Govers. Im Inneren der Rotorblätter sind elektrische und optische Sensoren verbaut. Sie messen zum Beispiel die Beschleunigung an unterschiedlichen Stellen der Blätter und ermöglichen so Aussagen über das Schwingungsverhalten. Faseroptische Dehnungssensoren, die mit Lasertechnologie arbeiten, zeichnen die Belastungen auf, die auf das Material wirken. Ein Netzwerk aus piezoelektrischen Wandlern empfängt und sendet Ultraschallsignale und kann entstehende Schäden im Rotorblatt direkt erkennen. Weitere Kameras im Umfeld der Windenergieanlagen schauen sich die Rotorblätter von außen an. Als Referenz für deren Messungen ist auf mehreren Abschnitten der Blätter ein Muster aus Punkten lackiert.

Die Sensoren sammeln Informationen, überwachen das Blatt und geben Hinweise, wo ein Problem auftauchen könnte.
Foto: DLR
Schwingungen, Materialbelastung, Stabilität: umfassende Daten erfassen
Werden die Blätter immer länger und die Anlagen dadurch größer, entstehen neue Effekte: Zum Beispiel können sich Schwingungen der Rotorblätter gegenseitig verstärken und die Stabilität der Anlage beeinflussen. „Das Schwingungsverhalten und damit auch die Materialbelastung konnten im Betrieb bisher kaum erfasst werden. Hier werden wir mit unserer umfassenden Sensorik wertvolle Daten sammeln und die Simulationen weiter verbessern können. Dieses Wissen hilft Forschung und Industrie dabei, genauere Vorhersagen zu treffen sowie noch leichter und stabiler zu bauen“, beschreibt Govers.

Die Mitarbeitenden begeben sich für ihre Arbeiten auch ins Innere des Rotorblatts, das bis zu 57 Meter lang ist.
Foto: DLR
Schon heute vereinen Rotorblätter Leichtbau mit Stabilität. Sie bestehen aus zwei zusammengeklebten Schalen, die innen weitgehend hohl und mit Stegen verbunden sind. Zum Einsatz kommen Sandwich-Materialien: Sie haben oben und unten eine Decklage aus Hightech-Kunststoffen, die mit Glasfasern verstärkt sind, dazwischen befindet sich Kunststoffschaum oder sehr leichtes Balsaholz.
Anlagen optimal steuern für Effizienz und lange Betriebsdauer
Unter Belastung verbiegt sich das Rotorblatt nicht nur, sondern verdreht sich zusätzlich. Die Sensoren im Inneren der Blätter zeichnen auch das auf. Diese Daten können helfen, neue Ansätze für die Regelung von Windenergieanlagen zu entwickeln, um sie effizienter und länger zu betreiben. Das DLR arbeitet dazu an Konzepten für eine lastadaptive Regelung von Anlagen: Kommt eine Böe auf, drehen spezielle Motoren an der Blattwurzel das Rotorblatt aus dem Wind. Sie verkleinern also den Winkel, in dem der Wind auf das Blatt trifft, und verringern die Belastung. In Verbindung mit Sensoren im Umfeld der Windenergieanlagen soll es so möglich werden, sehr kurzfristig und flexibel auf die lokalen Wetterbedingungen vor Ort zu reagieren.
Ausgefeilte Regelungstechnik ist gefragt
Auch zwei hintereinanderstehende Windenergieanlagen – wie im Forschungspark des DLR – sind eine Herausforderung für die Regelungstechnik. In der Praxis kommt dies häufig vor und gibt Anlass für Untersuchungen und Optimierungen. Den Grund erklärt Yves Govers: „Die zweite Anlage steht im Nachlauf der ersten. Das heißt, sie bekommt die verwirbelte Luft der ersten Anlage ab. Deshalb wollen wir herausfinden, wie die zweite Anlage gesteuert werden muss, damit sie trotzdem möglichst viel Strom produziert und materialschonend betrieben werden kann.“
Auch hier setzen die Forschenden auf die große Menge an Daten aus den vielzähligen Sensoren. Die Nachfrage nach solchen neuen Regelungskonzepten ist groß. Denn schon heute stehen in Windparks die teilweise über hundert Anlagen so dicht zusammen, dass sie sich alle gegenseitig beeinflussen.

Sensorik und Verkabelung im Rotorblatt: Für Regelungskonzepte in kompletten Windparks ist eine große Menge an Daten aus den vielzähligen Sensoren nötig.
Foto: DLR
Auf Biegen und Schwingen – intensive Tests vor dem Praxiseinsatz
Nach ihrer Schiffsreise von Portugal nach Deutschland Mitte Mai 2022 hatten die sechs Rotorblätter noch eine weitere Station vor sich. Bevor sie im Forschungspark in Krummendeich montiert werden, legten sie für zwei Monate einen Zwischenstopp in Bremerhaven ein. Am Fraunhofer-Institut für Windenergiesysteme (IWES) standen intensive Tests an Prüfständen auf dem Plan. Das Institut vereint fachliche Kompetenz mit einer umfangreichen und weltweit einmaligen Prüfinfrastruktur, um Entwicklungsrisiken von innovativen Produkten systematisch zu identifizieren und zu minimieren. Somit wird die Zertifizierung und Markteinführung beschleunigt und das Qualitätsniveau der Bauteile gesteigert. Beispielhaft hierfür steht der durchgängige Prozess zur Rotorblattentwicklung, bei dem von der Beschreibung des Windfeldes über die Material- und Bauteilqualifikation bis zum Test kompletter Rotorblätter alle relevanten Entwicklungsschritte abgedeckt und validiert werden können.
Für die Tests im beschriebenen Projekt hängt das Team die Rotorblätter mit Gummiseilen an einen Kran und versetzt sie in Schwingung. Damit werden vor allem die vielen Sensoren eingerichtet und getestet. Bei einem zweiten großen Test montieren die Forschenden die Blätter an einen Prüfstand und bringen eine Zugkraft auf, um so Statik, Deformation und innere Belastung zu testen. Nach Abschluss dieser Versuche ist die Montage der Hightech-Rotorblätter noch im Jahr 2022 geplant.
Das könnte Sie auch interessieren:
Hobelwerkzeug in Extrem-Leichtbauweise optimiert Produktivität und CO2-Footprint