Stanzen von Kunststoffelementen ohne Grat- und Flusenbildung
Verdrahtungskanäle aus Polymerblend sind wichtige Bauelemente, die für eine strukturierte Leitungsführung im Schaltschrank sorgen. Beim Herstellungsschritt Stanzen treten jedoch Grate und Flusen auf, die bisher einen zusätzlichen, teuren Arbeitsschritt nötig machten.
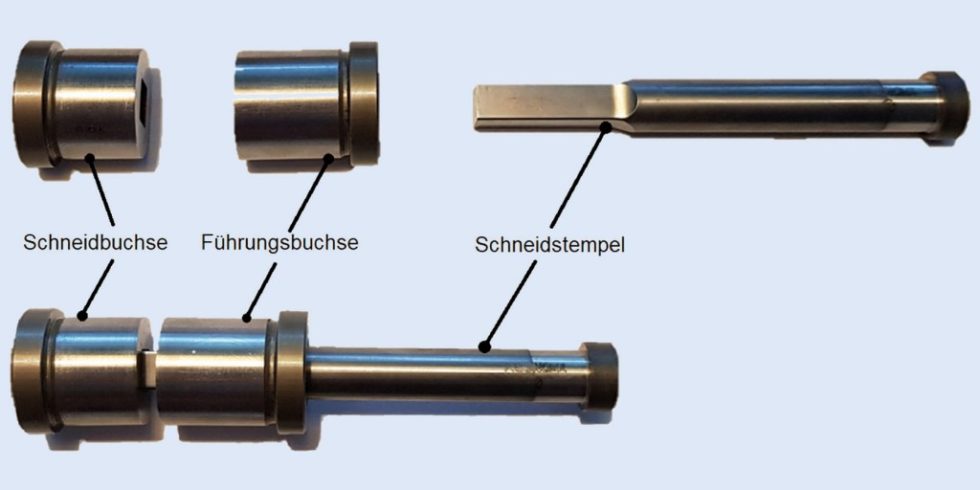
Werkzeugaktivelemente, die in den Stanzversuchen zur Auswertung nach der DOE-Methode (statistische Versuchsplanung) eingesetzt wurden.
Foto: HTW
Wie sich der Aufwand bei der Herstellung verringern lässt, haben Wissenschaftler der Hochschule für Technik und Wirtschaft (HTW) Berlin untersucht. Mit Erfolg setzen sie dabei auf eine Methode der statistischen Versuchsplanung: DoE (Design of Experiments) dient zur Prozessoptimierung und stellt Zusammenhänge zwischen den Eingangsgrößen (Faktoren) und den Ausgangsgrößen (Qualitätsmerkmale) dar. Durch eine Optimierung der mathematischen Modelle zeigt sich der Schneidspalt als entscheidende Größe.
Probleme beim Stanzen verteuern das Endprodukt
Bei der Fertigung von Verdrahtungskanälen entstehen während des Stanzens von Polycarbonat/Acrylnitril-Butadien-Styrol (PC/ABS) Grate und Flusen, welche die Qualität des Endprodukts verringern und einen teuren Entgratungsschritt erfordern [1], Bild 1. Lassen sich diese dank einer Prozessoptimierung vermeiden, kann ein „alter Stanzer-Traum“ wahr werden.
![Bild 1. Grat- und Flusenbildung an einer Ausstanzung eines Verdrahtungskanals aus PC/ABS nach [2]. Foto: HTW](https://www.ingenieur.de/wp-content/uploads/2021/02/ZB_-PC-ABS_Stanzen_1.jpg)
Bild 1. Grat- und Flusenbildung an einer Ausstanzung eines Verdrahtungskanals aus PC/ABS nach [2].
Foto: HTW
Stanzeinheit und untersuchte Qualitätsmerkmale
Bei der verwendeten Stanzeinheit „FlexSpee“ [5], Bild 2, der Firma Stanova Stanztechnik aus Berlin kommen Schneidstempel ISO 8020 sowie Schneid- und Führungsbuchsen ISO 8977 mit rechteckigem Querschnitt (7 mm x 7 mm) als Werkzeugaktivelemente zum Einsatz [1]. Die Werkzeugaktivelemente werden in einem Stanzwerkzeug montiert, das von der FlexSpee-Stanzeinheit mittels Zahnstangenantrieb betrieben wird. Hierbei sind Stanzgeschwindigkeiten bis zu 500 mm/s möglich.
![Bild 2. Für dieVersuche wurde die „Flexspee“-Zahnstangenpresse der Firma Stanova Stanztechnik [5] eingesetzt. Foto: HTW](https://www.ingenieur.de/wp-content/uploads/2021/02/ZB_-PC-ABS_Stanzen_2.jpg)
Bild 2. Für dieVersuche wurde die „Flexspee“-Zahnstangenpresse der Firma Stanova Stanztechnik [5] eingesetzt.
Foto: HTW
Ablauf der DOE-Analyse
Die zu untersuchenden Faktoren werden in einem „Ishikawa“ (auch Fischgrät)-Diagramm dargestellt und anschließend mithilfe der Fehlermöglichkeits- und Einflussanalyse (kurz FMEA) bewertet. Hierbei lassen sich die einzelnen Faktoren sowie deren jeweilige negative Auswirkung auf die Grat- und Flusenbildung (je nach Auswirkungsausmaß und der Auftretens- sowie der Entdeckungswahrscheinlichkeit) bewerten. Danach wurden die Faktoren – ihrer Gewichtung nach abfallend – aufgelistet und nach dem Pareto-Prinzip (80 % der Arbeit in 20 % der Zeit) selektiert. Die Faktorstufen wurden mithilfe von Erfahrungswerten, die aus aus Voruntersuchungen stammen, definiert [1; 6].
Zur Untersuchung der für die Qualitätsmerkmale ausschlaggebenden Einflussgrößen (Screening) und deren Zusammenhänge wurde ein „D-optimaler Screening-Versuchsplan“ mit der Software „Modde V 12.1“ der Firma Sartorius Stedim Data Analytics AB, Umeå/S [7], generiert. Für die Screeningversuche wurden die Faktoren Stanzgeschwindigkeit, Rauigkeit, Beschichtung (Stempel), Schneidspalt, Federkonstante (Niederhalter) und Block genutzt.
Zum Arbeitspaket zählt die Definition von Faktoren und die Auswahl des Versuchsplans, wobei die mögliche Auswahl an Versuchsplänen von der Kombination aus Faktoranzahl, Faktorstufenanzahl, mathematischem Typ der Faktoren und vor allem der Kombination zuvor genannter Eigenschaften abhängig ist. Vereinfacht kann gesagt werden: Je unterschiedlicher die Faktoren, desto weniger verschiedene Versuchspläne stehen zur Auswahl. Der Versuchsplan selbst wird nach der Art des Vorhabens (z.B. Screening), dem gewünschten Ergebnis (z.B. Effektplot) und der durchzuführenden Anzahl an Versuchen ausgewählt. Anschließend wurde das gestanzte Material bezüglich der Qualitätsmerkmale mithilfe von bebilderten Bewertungskatalogen ganzzahlig kategorisch bewertet, Bild 3.
Welche Relevanz haben die ausgewählten Faktoren?
Die Ergebnisse aus Versuchsdurchführung und Bewertung werden in den Versuchsplan der Software Modde eingepflegt. Diese errechnet anschließend, welche Beziehungen zwischen den Faktoren und den Qualitätsmerkmalen bestehen, und bedient sich hierfür eines eigenständigen mathematischen Modells für jedes Qualitätsmerkmal. Die relevanten Ergebnisse lassen sich übersichtlich als Effektplot darstellen, Bild 4.
Die Effekte der Faktoren auf die jeweiligen Qualitätsmerkmale sind hierbei absteigend nach der jeweiligen Einfluss- beziehungsweise Effektstärke angeordnet. Die Höhe der einzelnen Balken steht stellvertretend für die Größe / Auswirkung des Effekts. Das Vorzeichen steht für die jeweilige Effektrichtung. Der Fehlerbalken um die Effekte beschreibt die Standardabweichung um die Effektstärke. Ist diese größer als die eigentliche Effektstärke, sind die Ergebnisse eigentlich statistisch nicht signifikant.
Die Ergebnisse lassen sich wie folgt zusammenfassen:
- Bezüglich der Stanzgeschwindigkeit v sind lediglich geringfügige Effekte auf die Gratentstehung, die Einzugsverrundung und die plastische Deformation an der Unterseite zu sehen.
- Die Rauigkeit R der Schneidstempel-Mantelflächen hat im betrachteten Versuchsraum keinen Einfluss.
- Die untersuchten Beschichtungen („coat“) zeigen keinen Effekt auf die Gratentstehung, jedoch in geringem Umfang auf alle weiteren Qualitätsmerkmale.
- Auffallend ist, dass der größte Einfluss bei allen betrachteten Qualitätsmerkmalen vom Schneidspalt c ausgeht.
- Neben dem Schneidspalt ist die Federkonstante k beziehungsweise die Niederhalterkraft eine wichtige Größe.
- Die Blöcke b sowie der Tag des Versuchs hat lediglich einen Einfluss auf die Einzugsverrundung.
Welche Schlussfolgerungen lassen sich ziehen?
Es wird deutlich, dass der Schneidspalt die entscheidende Größe darstellt. Wird dieser zu groß gewählt, entsteht vermehrt Grat, wird dieser zu klein gewählt, bilden sich vermehrt Flusen. Somit können die Gratentstehung und die Flusenbildung durch entgegengesetzte Maßänderungen am Schneidspalt optimiert werden. Daraus folgt, dass wahrscheinlich ein idealer Schneidspalt existiert, mit dem sowohl ein Minimum an Flusen als auch ein kleinstmöglicher Grat erreicht wird.
Neben dem Schneidspalt ist eine Niederhaltung im Nahbereich der Ausstanzung während des Stanzens von PC/ABS essentiell für gute Stanzergebnisse [6].
Werden Faktoren oder Faktorstufen falsch gewählt, wird sich dies in den Ergebnissen zeigen. Werden Qualitätsmerkmale fehlinterpretiert, vermischt oder nicht entdeckt, können diese nicht korrekt ausgewertet bzw. optimiert werden.
Statistische Versuchsplanung definiert die Qualitätsmerkmale
Die Zusammenhänge zwischen den betrachteten Qualitätsmerkmalen und den ausgewählten Faktoren wurden mithilfe der statistischen Versuchsplanung – speziell eines D-Optimalen Screening Versuchsplans – mit Erfolg herausgestellt. Hierzu wurden der Prozess analysiert, entscheidende Faktoren identifiziert und Qualitätsmerkmale definiert. Die Ergebnisse aus Stanzversuchen ließen sich mittels bebilderter Bewertungskataloge kategorisch bewerten und die gezeigten Effekte der Faktoren auf die entsprechenden Qualitätsmerkmale berechnen. Schneidspalt und Niederhalter erwiesen sich als die wichtigsten Einflussgrößen für einen optimalen Stanzprozess von PC/ABS.
Literatur
- Noller, S. F.; Pfennig, A.; Heiler, R.: E3S Web Conf. Vol. 97 (2019), 06015.
- Noller, S. F.; Pfennig, A.; Heiler, R.: Mater. Sci. Forum Vol. 982 (2020), pp.135–42.
- Krache, R.; Debbah, I.: M. S. A. Vol. 02 (2011), pp. 404–10.
- Sze On Chan, H.: J. Fire Sci. Vol. 2 (1984), pp. 106–22.
- Informationen auf www.stanova.de, aufgerufen 13.11.2020.
- Noller, S. F.; Pfennig, A.; Heiler, R.: Int. J. Mech. Eng. Rob. Res. Vol. 9 (2020), pp. 1353–9.
- Sartorius Stedim Data Analytics: User Guide to MODDE Vol. 12 (2017).
Das könnte Sie auch interessieren:
Statistische Versuchsplanung – Methode zur Optimierung von Herstellungsverfahren
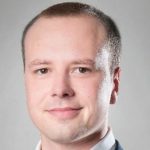
Sebastian F. Noller,
M.Sc., Jahrgang 1990, studierte Maschinenbau an der HS Ulm und der HTW Berlin und ist wissenschaftlicher Mitarbeiter am Fachbereich 2 der HTW Berlin.
Prof. Dr.-Ing. Anja Pfennig,
Jahrgang 1970, studierte Mineralogie an der Rheinischen Friedrich Wilhelm Universität zu Bonn, promovierte an der Friedrich Alexander Universität Erlangen-Nürnberg und ist seit 2009 Professorin an der HTW Berlin für Werkstofftechnik.
Prof. Dr.-Ing. Roland Heiler,
Jahrgang 1965, promovierte an der Universität Kassel und leitet seit 2008 das Labor für Fertigungstechnik, Fügetechnik und Montage an der HTW-Berlin.