Wie sich Neuinvestitionen zur Wertstromoptimierung nutzen lassen
Ein effizienter Wertstrom hängt von einer intelligenten Produktstruktur, einer durchdachten Planung und Steuerung sowie optimalem Materialfluss ab. Neuinvestitionen in Produktionsanlagen bieten zur Optimierung stets große Chancen – wie lassen sie sich nutzen?
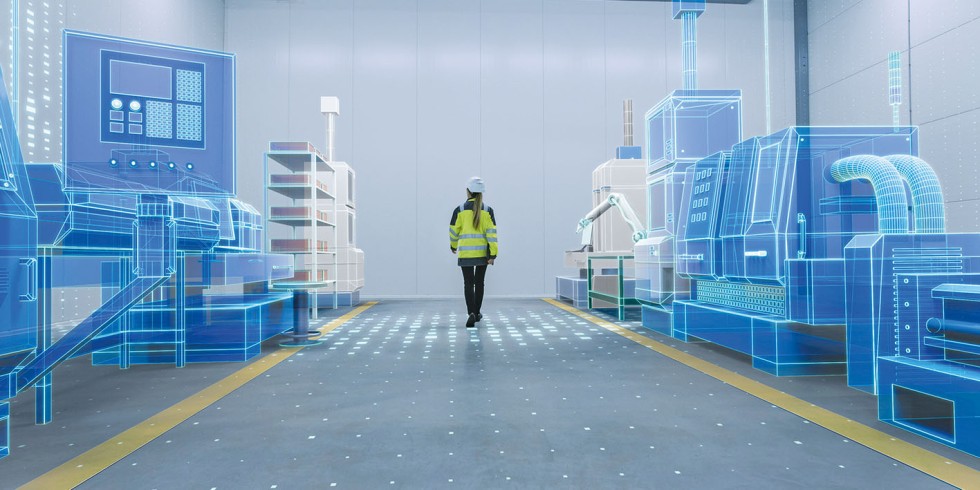
Bei der Erweiterung von Produktionskapazitäten ergeben sich viele Ansatzpunkte zur Optimierung des Wertstroms. Aber oft fehlt die ganzheitliche Betrachtung der Verhältnisse - aus Zeitgründen oder wegen fehlendem Know-how. Grafik: Shutterstock
Wenn Produktionskapazitäten ausgebaut werden oder Ersatzinvestitionen in neue Maschinen und Anlagen anstehen, sorgt das im Unternehmen für eine ideale Gelegenheit, die bisherige Produktionssystematik zu hinterfragen. Bei Erweiterungsinvestitionen ist es sinnvoll, auch den Wertstrom effizient auszurichten. Diese Chance haben auch die beiden Unternehmen Mepa Pauli und Menden GmbH (kurz: Mepa), Rheinbreitbach, sowie die Otto Junker CM GmbH (kurz: Junker), Lammersdorf, genutzt – gezeigt wird, wie dies gelungen ist.
Oberstes Ziel: Verschwendung beseitigen
Mit der Erweiterung beziehungsweise Erneuerung von Produktionskapazitäten sind in den meisten Unternehmen drei Bereiche beschäftigt: die Produktion legt die Anlage technologisch aus, das Controlling berechnet die Wirtschaftlichkeit und der Einkauf verhandelt dann das „Objekt der Begierde“. Eine ganzheitliche Betrachtung, was die Neuinvestition für Auswirkungen auf den Wertstrom hat und welche Ansatzpunkte sich zu dessen Optimierung ergeben, fehlt dabei aus Zeitgründen oder aber fehlendem Methoden-Know-how meistens. Im Ergebnis wird die Anlage dann dorthin gestellt, wo gerade Platz ist – und die vorhandene Verschwendung wird 1:1 übernommen.
Anwendungsbeispiel: Integration einer neuen Verpackungsanlage
Genau diesen Fehler wollte Uwe Milhamke, Gesamtbetriebsleiter bei Mepa, nicht machen. Vor dem Hintergrund einer Neuinvestition in eine Verpackungsanlage stellte er die bisherige Produktionssystematik in Frage und beauftragte CIM Aachen mit der Optimierung des Wertstroms sowie der Planung des zukünftigen Hallenlayouts. Das deutliche Wachstum des Herstellers von Vorwandinstallationssystemen machte es erforderlich, sowohl in den Bereichen Einkauf und Planung, insbesondere aber in der Logistik und in der Produktion, entsprechende Maßnahmen einzuleiten. Ziel war es, das zukünftige Mengengerüst effizient handhaben zu können.
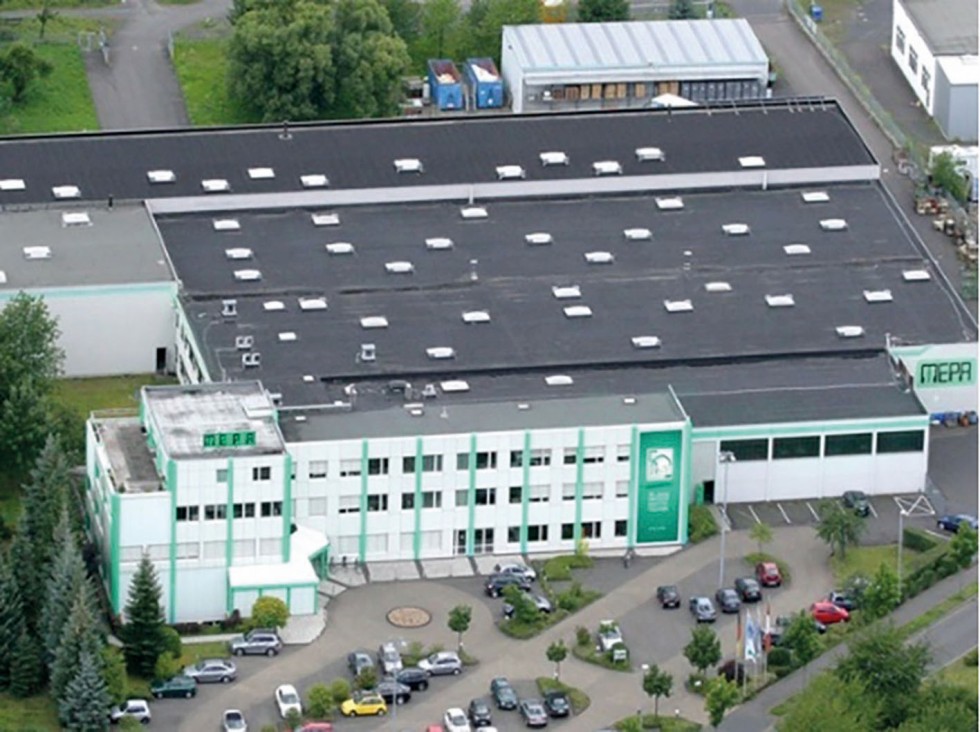
Firmensitz von Mepa in Rheinbreitbach: Die gesamte bisherige Produktionssystematik wurde auf den Prüfstand gestellt.
Foto: Mepa Pauli und Menden GmbH
Im ersten Schritt wurde die bisherige Produktionssystematik auf den Prüfstand gestellt und optimiert. Dies betraf unter anderem die Erarbeitung eines Konzepts zur Einplanung übergroßer Abrufmengen, die frühzeitige Identifizierung kritischer Artikel mit langen Wiederbeschaffungszeiten sowie die Einführung einer „frozen zone“ zur Beruhigung der Fertigung und Optimierung der Rüstreihenfolge. Hieraus abgeleitet, ergaben sich diverse Anpassungsbedarfe für das bereits zuvor gut eingestellte SAP-System.
Reorganisation eines Teilbereichs hat Auswirkungen auf die gesamte Produktion
Mit den vorliegenden Kenntnissen wurde dann gemeinsam im Team das neue Hallenlayout erarbeitet. Ziel dabei war es in erster Linie, unter den vorliegenden „Brownfield“-Bedingungen ein materialflussoptimiertes Konzept zu erarbeiten. Damit sollte das erwartete Umsatzwachstum möglichst reibungslos umgesetzt werden. Hierzu wurden mittels der „Table-top-Methode“ diverse Szenarien mit unterschiedlichen Auswirkungen auf die restliche Fertigung erarbeitet. Im Fokus stand hierbei in erster Linie die effiziente Gestaltung der Produktversorgungsbereiche. Für diese sollten einerseits entsprechende Lagerplätze vorgehalten werden, andererseits musste eine möglichst optimale Materialver- und -entsorgung konzipiert werden.
Schlussendlich fiel die Entscheidung auf eine Variante, die nicht nur einen optimalen Materialfluss sicherstellt, sondern die es Mepa mittelfristig ermöglicht, bis zu 122 verschiedene Artikel im Model-Mix auf der Anlage zu produzieren. Spannender Nebeneffekt: durch die Reorganisation des „Next-VIT“-Fertigungsbereichs werden gleichzeitig auch andere Fertigungsbereiche materialflussoptimiert angeordnet.
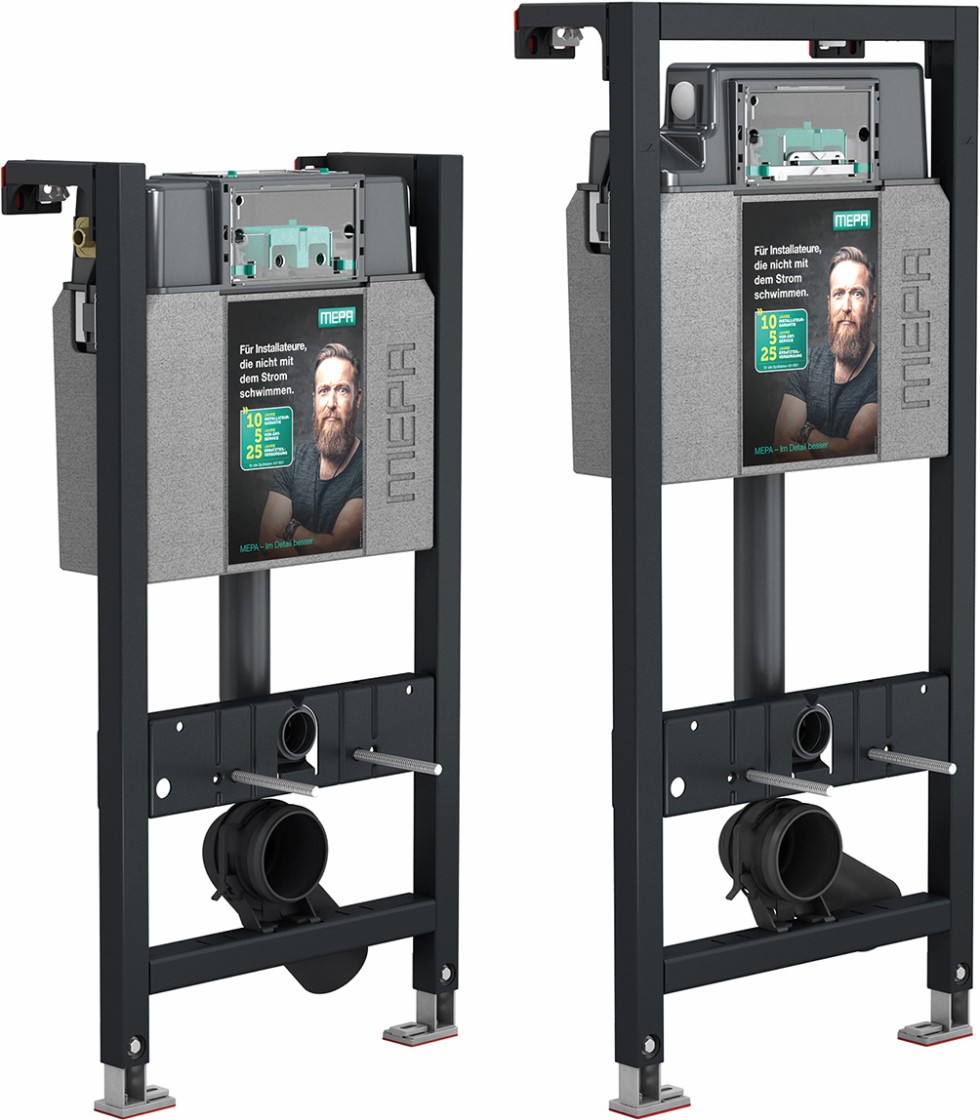
Ein Vorwandinstallationssystem „NextVIT“: Das deutliche Wachstum des Herstellers erforderte Optimierungen in den Bereichen Einkauf, Planung, Logistik und Produktion.
Foto: Mepa Pauli und Menden GmbH
„Die Anregungen und kritischen Fragen des CIM-Teams haben uns sehr geholfen, kreative Ansätze für ein neues Layout zu finden“, so Uwe Milhamke. „Auch in Bezug auf die Spezifikation unserer neuen Anlage gab es zahlreiche Hinweise, die wir dankend in unsere Ausschreibungsunterlagen aufgenommen haben“. Hierfür liegt beim Beratungsunternehmen langjährige Expertise vor: Seit der Gründung im Jahr 1987 arbeiten die Spezialisten der CIM Aachen GmbH aus der Nutzenperspektive an der Steigerung der Fabrikleistung
Erweiterung der mechanischen Fertigung beim Komponentenhersteller
Auch bei Otto Junker standen die Verantwortlichen vor der Aufgabe, ihre Fabrikleistung nachhaltig zu steigern. Der Zulieferer von Maschinenkomponenten für die Halbleiterindustrie sieht sich derweil mit nahezu einer Verdopplung der Stückzahlen innerhalb eines einzigen Jahres konfrontiert.
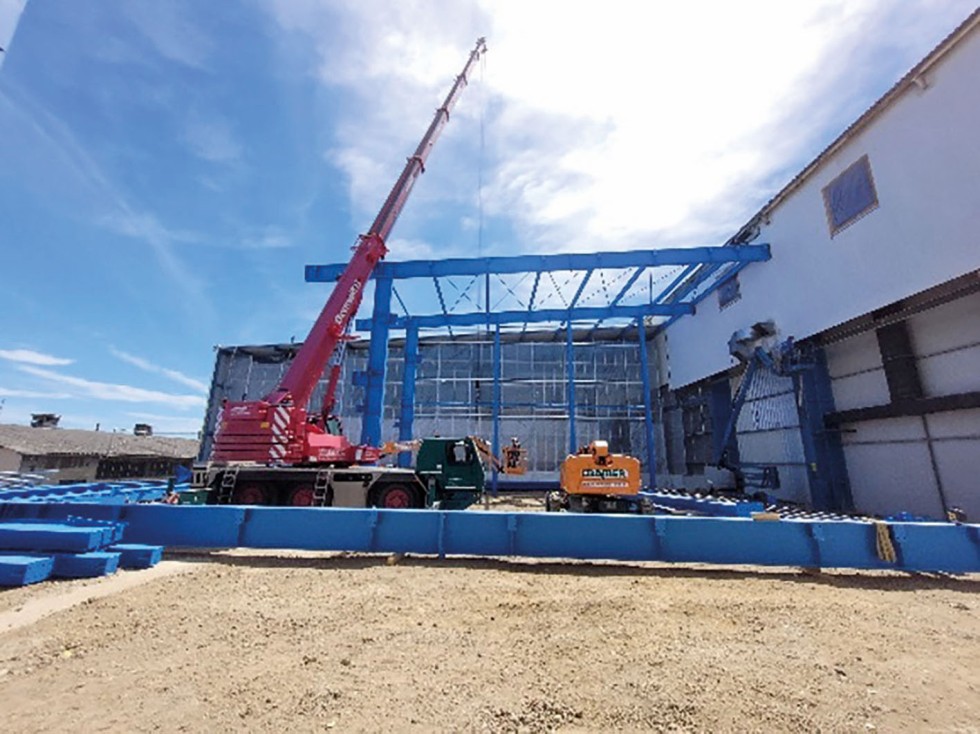
Bau der neuen Produktionshalle in Lammersdorf. Stellhebel zur Steigerung der Fabrikleistung war hier die Umstellung auf eine auftragsneutrale Fertigung von speziellen Maschinenkomponenten.
Foto: Otto Junker CM GmbH
„Natürlich hatten wir diverse eigene Ideen, wie wir unser neues Bearbeitungszentrum in das bestehende Hallenlayout integrieren wollten. Mir war aber wichtig, dass uns ein Experte mit Blick von außen die Fragen stellt, auf die wir von alleine nie gekommen wären“, so Dr. Elmar Westhoff, Geschäftsführer von Junker aus Lammersdorf. Auch hier lag ein erhebliches Potential nicht allein in der Aufstellung der neuen Produktionsanlage, sondern in der Optimierung der bisherigen Produktionssystematik sowie der Steigerung der Produktivität bestehender Anlagen.
Auftragsneutrale Fertigung als Schlüsselfaktor
Wesentlicher Stellhebel zur Steigerung der Fabrikleistung war hier die Umstellung auf eine auftragsneutrale Fertigung der „AX“-Maschinenkomponenten, die zuvor per Einzelfertigung hergestellt worden waren. Durch die Verschiebung des Kundenentkopplungspunktes („order penetration point“) in eine spätere Phase der Wertschöpfung leiteten sich umfangreiche Maßnahmen für Planung und Steuerung, Fertigung und Logistik ab. Wesentliche Vorteile der Umstellung waren eine deutliche Reduzierung der kundenrelevanten Durchlaufzeit um 50 Prozent sowie der „Work-in-process“-Bestände um 32 Prozent.
Aufgrund der großen Komponentenabmessungen sowie spezifischen Lageranforderungen hatte die Berechnung der neuen Bestandsvolumina entlang der Wertschöpfungskette auch erheblichen Einfluss auf die Erarbeitung des neuen Hallenlayouts und Lagerkonzeptes. Insbesondere für die Auswärtsbearbeitung einzelner Arbeitsgänge in speziellen Transportgestellen als auch für den Versand der großen Maschinenkomponenten mussten entsprechende Lagerflächen vorgesehen und optimal in den Materialfluss integriert werden.
Potential erkennen und nutzen – trotz eingeschränktem Handlungsspielraum
„Die Freiheitsgrade für die Positionierung unseres neuen Bearbeitungszentrums waren leider nicht sehr groß. Vor dem Hintergrund bin ich aber umso zufriedener über die Ergebnisse, die wir in dem Projekt erzielen konnten“ resümiert Dr. Westhoff die Projektarbeiten.
Mit der zügigen Umsetzung wichtiger Maßnahmen aus dem Soll-Workshop hat Junker diese Voraussetzungen für eine erfolgreiche Layoutplanung geschaffen. Trotz der geringen Freiheitsgrade bei der Positionierung des neuen Bearbeitungszentrums von DMG Mori wurden 16 Fabrikszenarien erarbeitet und bewertet. Die finalisierte Version führte neben der wertstromoptimierten Aufstellung des neuen Bearbeitungszentrums auch zur Layout-Optimierung bei Mess-, Entgrat- und Waschprozessen.
Das könnte Sie auch interessieren:
Was hilft bei immer kürzeren (Investitions-) Planungszyklen?
Warum die schlanke Produktion derzeit eingeschränkt ist – und was hilft
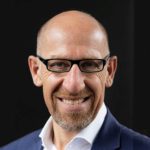
Ingo Laqua ist Geschäftsführer der CIM Aachen GmbH. Foto: CIM