Der Forschungscampus für Arbeit, Mobilität und Produktion der Zukunft
Arbeit, Mobilität und die Produktion der Zukunft sind die Kernthemen des Forschungscampus ARENA2036 (Active Research Environment for the Next Generation of Automobiles in 2036). Ausgehend von vier BMBF-geförderten Projekten, arbeiten Forscher aus Wissenschaft und Industrie an mittlerweile über 90 Projekten zu den zentralen ARENA2036-Forschungsbereichen. Partner sind die Universität Stuttgart, außeruniversitäre Forschungseinrichtungen, große sowie kleine und mittelständische Unternehmen.
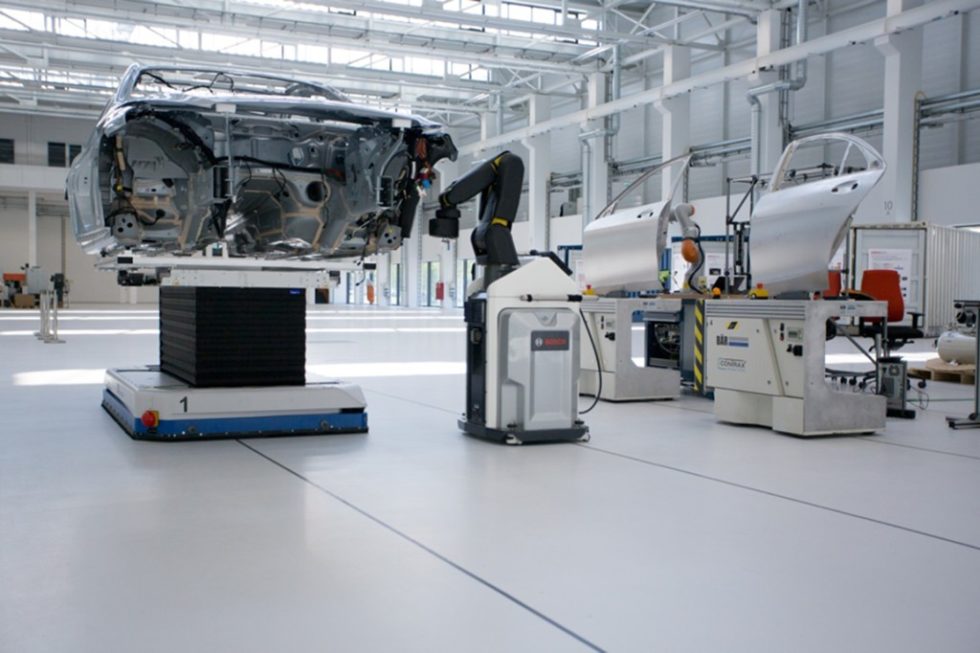
Groß-FTF zum Transport ganzer Autokarossen und adaptierte Klein-FTFs Bild: Arena2036
Eine solche interdisziplinäre Partnerstruktur und der Mix an unterschiedlichsten Kompetenzen, beispielsweise im Bereich Simulation, Konstruktion, Flugzeugbau, Materialien, Produktionstechnik oder auch der Arbeitswissenschaft, sind entscheidende Faktoren, um innovative Projektideen zu generieren und diese gemeinsam unter einem Dach zu erforschen.
Die Forschungsthemen der ARENA2036 orientieren sich entlang der gesamten Wertschöpfungskette einer Produktentstehung – von der Idee über die digitale Verarbeitung bis hin zur Produktion. Auf diese Themenfelder konzentriert sich der Forschungscampus seit dem Projektstart im Juli 2013 in den vier Kernprojekten „LeiFu“ (Intelligenter Leichtbau durch Funktionsintegration), „DigitPro“ (Digitaler Prototyp), „ForschFab“ (Forschungsfabrik: Produktion der Zukunft) und „Khoch3“ (Kreativität, Kooperation, Kompetenztransfer).
Die ersten drei Forschungsbereiche sind technisch ausgerichtet und werden im Folgenden konkret erläutert. Das vierte Verbundprojekt Khoch3 ist ein Querschnittsbereich, der übergreifend über die technischen Themen die Ausgestaltung von Arbeitsstrukturen, der Forschungsumgebung und Prozessabläufe unter arbeitswissenschaftlichen Gesichtspunkten erforscht, so dass sich Kreativität, Ideenfindung und Teamgeist der Expertinnen und Experten optimal im Forschungscampus entfalten können.
1 LeiFu – Leichtbau durch Funktionsintegration
Fahrzeuge der Zukunft sind leicht, verbrauchen wenig Energie und sind kostengünstig, da Gewicht, Bauteile und Energie eingespart werden. Leichtbaumaterialien bieten hierfür ideale Voraussetzungen und hervorragende Möglichkeiten, Einzelfunktionen wie Schall- und Wärmedämmung, thermische, sensorische oder elektrische Funktionen in das Bauteil zu integrieren. Die Gewichtsreduktion von Fahrzeugkomponenten ist ein wesentlicher Beitrag zur Reduzierung der Kohlendioxid-Emission herkömmlicher Kraftfahrzeuge beziehungsweise zur Steigerung der Reichweite von Elektrofahrzeugen und ein essentieller Forschungsbestandteil des Verbundprojektes „LeiFu“. Das Projekt wurde, wie auch die anderen Verbundprojekte, im Jahr 2013 mit einer Projektlaufzeit von fünf Jahren gestartet, um ein Leichtbau-Bodenmodul zu entwickeln, welches den hohen Anforderungen an eine erfolgreiche Gewichtsreduktion entspricht. Die Verringerung des Gewichts des Bodenmoduls wird hier auf zweifache Weise erreicht. Zum einen wird das Potenzial von Leichtbaumaterialien und Sandwichstrukturen genutzt, zum anderen wurden Einzeltechnologien entwickelt, die direkt in das Bodenmodul integriert sind.
1.1 Gewichtsoptimierung im Bodenmodul
Kohlefaserverstärkte Kunststoffe (CFK) steht für eine geringe Masse bei gleichzeitig hoher Steifigkeit. Diese Eigenschaften werden im LeiFu-Bodenmodul, welches sich zurzeit im Aufbau befindet, genutzt.
Als Konstruktion wurde eine Sandwichbauweise gewählt, bei der Ober- und Unterschale aus CFK-Bauteilen bestehen und das Innere des Sandwichs ein Schaumkern ist. Damit konnten die gewünschten mechanischen Eigenschaften des Bodenmoduls, bei gleichzeitiger Integration verschiedener Einzeltechnologien, umgesetzt werden. Diese Integration ist sowohl innerhalb des CFK-Materials, als auch im Schaumkern möglich. Das verwendete Schaummaterial erzeugt darüber hinaus die gewünschte thermische Isolation.
Ein Beispiel für Funktionsintegration ist die Nutzung von Sitzquerträgern und anderen lasttragenden Verstärkungsprofilen als Medienleitung, beispielsweise für die Innenraumbelüftung. Als weiteres Beispiel kann die aktive Heizfunktion aufgeführt werden, bei der auf Kohlefaser-Gewebe aufgedruckte Silberschichten als ohmscher Widerstand Wärme liefern. Zudem werden die Kohlefaser-Rovings teilweise mit speziellen Webtechniken (ORW (Open Reed Weaving)-Technologie) und Flechttechniken zur Strukturverstärkung verarbeitet. Eine weitere zu integrierende Einzeltechnologie ist die elektrische Spule für das induktive Laden der Fahrzeugbatterie, die ebenfalls Bestandteil des LeiFu-Bodenmoduls ist.
1.2 Crashuntersuchungen zur Erhöhung der Vorhersagegüte
Die Konstruktion des Bodenmoduls wurde umfangreichen Crashsimulationen unterworfen, deren Ergebnisse an die Konstruktion zurückgespiegelt und in diese integriert. Auf diese Weise konnte in mehreren Stufen ein finales Konzept erarbeitet werden, das die oben beschriebenen Anforderungen erfüllt. Zudem dienten reale Crashtests an Teilaufbauten der Verifikation der Simulationsergebnisse. Darüber hinaus erfolgten Robustheitsanalysen, um sicherzustellen, dass das verwendete Konzept im Crashfall ein vorhersagbares Versagen aufweist.
1.3 Sensorintegration in der Laderaummulde
Im Verlauf des Projekts wurde darüber hinaus eine Laderaummulde mit integrierten Sensoren entwickelt, um die Möglichkeit zur Integration von Funktionen in einem weiteren Bauteil zu erforschen. Die Laderaummulde ist das Bauteil, welches sich unterhalb des Kofferraumbodens im Heck des Fahrzeugs befindet.
Sensoren zur Überwachung von Druck, Temperatur und Feuchtigkeit, die in dieses Bauteil integriert wurden, sind insbesondere auch für den Einsatz in der Batteriebox von Bedeutung. Während die Batteriebox noch im Entstehen ist, wurde für die Laderaummulde ein bereits vorhandenes Werkzeug für die RTM (Resin Transfer Moulding)-Fertigung dieses CFK-Bauteils verwendet. Im Verlauf des Forschungsprojektes hat sich immer deutlicher herausgestellt, dass das Thema Sensorintegration zukünftig eine entscheidende Rolle spielen wird. Daher wurden unabhängig von Bodenmodul und Batteriebox mehrere Laderaummulden als Technologieträger aufgebaut. Im Folgenden wird auf die in der Laderaummulde realisierten Technologien näher eingegangen.
1.4 Sensorik
Es ist gelungen, Sensoren unter Verwendung des RTM-Verfahrens in die Faserverbundstruktur einer Laderaummulde zu integrieren. Analog zum LeiFu-Bodenmodul besitzt auch die Laderaummulde einen Schaumkern. Hier konnten neben Sensoren auch Induktionsspulen zur drahtlosen Energieübertragung und Bluetooth-Module zur drahtlosen Datenübertragung eingebracht und so eine Multifunktionsmulde als Technologieträger hergestellt werden.
Ein weiterer Vorteil ist, dass die Sensorik sowohl im Herstellprozess der Mulde als auch im fertigen Bauteil eingesetzt werden kann: Sensoren zur Temperatur-, Druck- und Feuchtigkeitsmessung können in einer Batteriebox den Zustand der Batterie überwachen. Während der Bauteilherstellung im RTM-Verfahren können die gleichen Sensoren die Prozesstemperatur und den Prozessdruck überwachen und gleichzeitig, im Fall der Feuchtigkeitssensoren, die Harzfließfront detektieren. Piezo-Sensorik kann den Aushärtevorgang des Harzes bei der Herstellung überwachen und später im Rahmen des Zuverlässigkeits-Monitorings zur Crash- beziehungsweise Impact-Lokalisierung eingesetzt werden.
1.5 Recycling
Die Wettbewerbsfähigkeit von CFK-Bauteilen scheitert häufig an den hohen Kosten für Kohlefasern. Auf der anderen Seite fallen bei der Herstellung der Preforms oft große Mengen an Verschnitt an. Anhand der Laderaummulde wurde untersucht, ob die Ökobilanz eines CFK-Bauteils durch den Einsatz von Kohlefaser-Recycling-Material verbessert werden kann. Es ist gelungen, eine Laderaummulde unter Verwendung von Recyclingmaterial herzustellen und so ökologische und ökonomische Vorteile zu erreichen. Dazu wurden die inneren Lagen der Kohlefaser-Gelege durch ein Kohlefaser-Vlies ersetzt. Dieses Vlies wurde wiederum unter Verwendung von Kohlefaser-Verschnitt hergestellt.
Das funktionsintegrierte LeiFu-Bodenmodul und die Batteriebox wurden erfolgreich als Realbauteil aufgebaut. Zudem konnten mehrere Technologieträger in Form von Laderaummulden hergestellt und positiv getestet werden. Es wurde gezeigt, dass Sensoren erfolgreich in CFK-Bauteile integriert werden können. Zudem wurden in der aktuellen Aufbaustufe eine drahtlose Energieversorgung und eine drahtlose Datenübertragung realisiert.
2 DigitPro: Ganzheitlicher digitaler Prototyp im Leichtbau für die Großserienproduktion
Ziel des Projektes „DigitPro“ ist es, anhand von Bauteilen einer Fahrzeugkarosserie die Durchgängigkeit der Herstellprozesssimulationskette in ihrer Gesamtheit aufzuzeigen. Dafür wird die Integration von Flecht- und Infiltrationssimulationen sowie die Entwicklung einer CAM (Computer Aided Manufacturing)-Schnittstelle für Roboter und Flechtmaschinen erforscht, denn für die eigentlichen Herstellungsprozesse rückt immer mehr die Verwendung von Faserverbundstrukturen in den Fokus. Grund hierfür ist die Erkenntnis, dass ein optimaler Leichtbau nicht nur durch die Verwendung neuer leichter Materialien, sondern auch durch deren richtige Verarbeitung und somit die optimale Ausnutzung der Materialeigenschaften erreicht wird.
Hierfür werden unterschiedliche Prozesse beleuchtet und digital abgebildet. Als Formgebungsprozess liegt der Fokus auf sogenannten ORW-Geweben und deren Umformung sowie auf dem Flechtprozess und der anschließenden Harzinjektion. Für die Durchgängigkeit der Prozesskette (Bild 4) wird ein neuer Datencontainer im HDF5-Format (HDF5 Hierarchical Data Format) definiert.
Dieser nimmt alle anfallenden Daten der Input- und Output-Dateien der einzelnen Simulationsschritte auf, dient also als Datenspeicher, aber auch zur Dokumentation der zugehörigen virtuellen Prozesskette. In diesem digitalen Prototyp eines jeden Bauteils können neben den Simulationsdaten auch alle Realdaten des Herstellungsprozesses, der Qualitätssicherung, auch des Testings abgespeichert werden. Durch eine klare Zuordnung der Daten zum jeweiligen Bauteil kann dann die gesamte Historie des Bauteils zum Beispiel durch Near-Field-Communication oder Barcode-Systeme jederzeit, auch später in der finalen Baugruppe, abgefragt werden. Somit dient der digitale Prototyp als Grundlage für eine Produktion im Sinne von Industrie 4.0. Von den Simulationsschritten werden integrierte Log-Files hinterlegt, in denen die aufeinanderfolgenden Prozesse in den verwendeten Derivaten gelistet werden. Die Daten selbst werden in einem neutralen HDF5-Format abgelegt und in einer Cloud gespeichert. Beim Verwenden von unterschiedlichen Software-Tools für die verschiedenen Simulationsschritte werden durch eigens geschriebene Parser die notwendigen Daten aus dem Container geholt und die Ergebnisse nach der Simulation anschließend wieder in das Format übersetzt. Somit können die Ergebnisse der Formgebungssimulation, zum Beispiel der Flechtsimulation, direkt an die nachfolgende Infiltrationssimulation und diese Ergebnisse dann wiederum an die Struktursimulation übergeben werden.
Der definierte Datencontainer ist dabei so aufgebaut, dass neue Prozesse direkt ergänzt und in den Digitalen Prototyp integriert werden können. Aus diesem Datencontainer können, neben der Übergabe der notwendigen Daten von einer Simulation in die folgende, auch die Randbedingungen für den Realprozess extrahiert werden. Hierfür sind eine direkte Anbindung der Simulation an den realen Prozess sowie ein direkter Übertrag der virtuell bestimmten Randbedingungen notwendig. Die sogenannte und hierfür notwendige CAM-Schnittstelle ist ebenfalls Teil der Forschungsaktivitäten im ARENA2036-Projekt DigitPro.
Diese CAM-Schnittstelle sorgt dafür, dass Randbedingungen der realen Produktionsprozesse in der Simulation vorhergesagt und automatisch an die jeweilige Produktionsstätte übermittelt werden. Die Produktionsstätte scannt das einfahrende Bauteil und organisiert die benötigte Herstellungsperipherie und den Materialfluss selbstständig. Materialförderoperationen werden ausgelöst und eine Umstrukturierung der Produktionshalle kann nach Bedarf stattfinden. Die Vision ist eine völlig autonome, sich selbst reorganisierende Produktionsstätte.
3 ForschFab – die wandlungsfähige Automobilproduktion der Zukunft
Forschungsgegenstand des Projekts ForschFab ist die wandlungsfähige Automobilproduktion der Zukunft. Ziel ist es dabei, Lösungen für die immer größer werdende Varianz im Automobilbau zu finden. Diese Problematik wird insbesondere durch neue Antriebskonzepte, die Unsicherheit bezüglich der zeitlichen Durchsetzung dieser Antriebskonzepte am Markt, und neue Materialien und Fügeverfahren im Fahrzeug verschärft. Die Projektpartner Daimler, Bosch, Bär-Automation, Fraunhofer IPA, die Institute IFF, ISW und IFT der Universität Stuttgart und weitere assoziierte Partner forschen gemeinsam nach zukünftigen Lösungen dieser Herausforderung.
Im Rahmen des Projektes ForschFab wird der Ansatz verfolgt, den festen Takt und die feste mechanische Verkettung der Linien in der Automobilproduktion aufzubrechen und damit neue Freiheiten für die Planung und Steuerung von Automobilproduktionen zu schaffen [1]. Hierzu wurden verschiedene Organisationsprinzipien der Produktion systematisch miteinander verglichen. Es hat sich gezeigt, dass die Aufhebung von Band und Takt hohes Potenzial für Verbesserung von Flächenverbrauch und Verfügbarkeit der Anlagen birgt. Dies trifft insbesondere auf Produktionsumfänge mit vielen indirekten Arbeiten, zum Beispiel im Falle einer separaten Set-Bildung bei sehr hoher Varianz, zu. Der Ansatz dabei ist, die fest verketteten Linien durch einen losen Verbund sogenannter Fertigungsmodule zu ersetzen. Die Fertigungsmodule sind dabei untereinander flexibel über FTF (Fahrerloses Transportfahrzeug) miteinander verkettet.
3.1 Planungsmethode für wandlungsfähige Produktionen
Für die Planung wandlungsfähiger Automobilfabriken ohne Band und Takt wurde im Projekt ForschFab eine Planungsmethode entwickelt [2, 3]. Diese Methode baut auf dem Ansatz des Axiomatic Design auf und adaptiert diesen für die Anwendung in der Produktion. Hierfür wurde ein Katalog von Fertigungsmodulen erstellt, dessen Elemente bei der Anwendung der Planungsmethode zur modularen Fabriklayouts gemäß dem Produktionsbedarf kombiniert werden.
Bei der Analyse der Wandlungsfähigkeit der entstehenden Fabriklayouts zeigt sich, dass eine Erhöhung der Wandlungsfähigkeit der einzelnen Fertigungsmodule entscheidend ist. Die Aufhebung der festen Verkettung und von Band und Takt ermöglicht es, einzelne Betriebsmittelmodule aus dem Produktionsfluss zu nehmen und umzurüsten. Um diese Fähigkeit optimal nutzen zu können, sind jedoch leicht umbaubare und insbesondere leicht in Betrieb zu nehmende Fertigungsmodule erforderlich. Hierzu wurden im Rahmen des Projekts verschiedene Lösungen entwickelt.
3.2 Schnelle Rekonfiguration von Steuerungstechnik und Industrial-IT
Eine zentrale Rolle für die Nutzung von Wandlungsfähigkeit kommt der Industrial-IT zu. Während heutige Lösungen der Industrial-IT in der Regel auf einer homogenen Geräte- und Softwareinfrastruktur aufbauen, war das Ziel des Projekts, ein System zu realisieren, das auch mit stark heterogenen Infrastrukturen umgehen kann und damit den häufig beobachteten Lock-in Effekt etablierter Lösungen umgeht. Gleichzeitig sollte für die Echtzeitkommunikation nach wie vor auf etablierte Kommunikations- und Busstandards zurückgegriffen werden. Um diesen Anforderungen gerecht zu werden, wurden im Rahmen des Projekts die sogenannten „Gelben Seiten der Produktion“ entwickelt [4, 5]. Die Gelben Seiten ermöglichen es beliebigen Teilnehmern über den OPC-UA (Open Platform Communications – United Architecture) eine Selbstbeschreibung mit eigenen Services und unterstützten Kommunikationsprotokollen anzubieten. Die Gelben Seiten agieren demnach als Verzeichnisdienst, mit dessen Hilfe es möglich ist, die Teilnehmer im Produktionssystem, deren Fähigkeiten und unterstützte Schnittstellen durch Ansprache eines Softwareservices in Erfahrung zu bringen.
Eng mit der Industrial-IT verbunden ist die Herausforderung der heute mangelnden Rekonfigurierbarkeit der Steuerungstechnik [6]. Um dieser Herausforderung zu begegnen, wurde der Ansatz Plug and Produce in einem durch den Werker rekonfigurierbaren Kleinmontagearbeitsplatz umgesetzt [7, 8]. Hierbei melden sich smarte Produktionsmodule zentral an einem System an und können durch eine standardisierte Selbstbeschreibung Informationen über die eigenen Fähigkeiten und Anforderungen bereitstellen. Eine integrierte und zum Patent angemeldete Lokalisierungsfunktion ermöglicht es den Modulen, selbsttätig ihre Position auf dem Montagetisch zu bestimmen und anderen Komponenten mitzuteilen. Dies ermöglicht es dem Werker, die Elemente des Produktionssystems frei auf der Montagefläche zu positionieren. Ein Fertigungsablauf kann nun sehr einfach durch die Kombination verschiedener Schritte, zum Beispiel Aufnehmen, Prüfen, Ablegen, erstellt und ausgeführt werden. Die technische Basis des Labordemonstrators bilden die Gelben Seiten der Produktion.
3.3 Kollaborierender Roboterassistent ermöglicht Produktionsskalierung
Insbesondere die Skalierung der Ausbringung stellt eine wesentliche Anforderung an die wandlungsfähige Produktion da. Lösungsansätze hierzu werden durch einen ortsflexiblen, kollaborativen Leichtbauroboter demonstriert. Dieser macht eine gleitende Arbeitsteilung zwischen Mensch und Roboter realisierbar [9].
Dies wiederum ermöglicht es, auf Kapazitätsschwankungen zu reagieren. Der Roboter ist auf einem Werkstattwagen fahrbar, was es ermöglicht, den Roboter wie ein Werkzeug zu einer Arbeitsaufgabe hinzuzuziehen.
Für den Roboter wurden zudem intelligente Werkzeugelemente entwickelt. Hierbei handelt es sich zum einen um ein hybrides Schraubgerät, das sowohl vom Werker, als auch sicher durch den Roboter bedient werden kann. Des Weiteren wurde ein sicherer Greifer mit neuen Sicherheitsprinzipien in Form einer Widerstandsmessung zwischen den Greifbacken entwickelt. Kernelement zur Realisierung der gleitenden Automatisierung ist die Integration einer intuitiven Programmierumgebung namens „drag and bot“, die es dem Werker erlaubt, Produktionsabläufe auf intuitive Weise zu definieren. Der dabei verwendete Abstraktionsgrad entspricht der menschlichen Kommunikation. Dieser Ansatz ist ein erster Schritt zur menschzentrierten Produktion im Automobilbau. Der Roboter ist über die Gelben Seiten an das Gesamtsystem angebunden.
3.4 FTF erlauben wandlungsfähige Produktion und Logistik
Die lose Verkettung von Produktionsprozessen zieht insbesondere grundlegende Änderungen in der Produktionslogistik nach sich [10–12]. Der bisher in der Automobilproduktion an vielen Stellen verwendete Ansatz einer festen Sequenzierung von Material (Just-in-Sequence) funktioniert in einer lose verketteten Fertigung nicht mehr. Um diesem Problem zu begegnen, wurde eine systematische Analyse der Kosten für verschiedene Logistikformen erstellt und in Form eines Berechnungswerkzeugs dokumentiert. Auf dieser Basis wurden neue Logistikkonzepte für die Automobilindustrie entwickelt. Eine entscheidende Innovation stellt dabei das im nächsten Bild gezeigte Riegelsystem dar, mit der eine Materialbereitstellung in beliebiger Reihenfolge möglich ist.
Darüber hinaus wurde insbesondere auch an der Schnittstelle von FTF und Produktionssteuerung gearbeitet. So wurde für die Groß-FTF zum Transport ganzer Autokarossen und adaptierte Klein-FTFs eine universelle Schnittstelle implementiert, die es den FTF ermöglicht, mit den Gelben Seiten zu kommunizieren. Hierbei wurde eine Lösung entwickelt, die auch für ältere Maschinen nachträglich mit geringem Aufwand adaptierbar ist. Auf dieser Basis wird momentan eine Steuerungsschnittstelle entwickelt, welche die Fahrkinematik des konkreten FTF kapselt und somit das Ansprechen der Transportdienstleistung verschiedener FTF über eine einheitliche Schnittstelle ermöglicht.
Die entwickelten Technologien wurden erfolgreich am Beispiel der Türmodulmontage von Fahrzeugtüren angewendet.
Dieser Produktionsumfang bildet dabei zahlreiche Fertigungsherausforderungen des Gesamtfahrzeugs repräsentativ ab.
Literatur
[1] Dietz, T.; Foith-Förster, P.; Hägele, M.; Bauernhansl, T.: Agile production of vehicles with multi-material structures. 2nd International Merge Technologies Conference, IMCT 2015, Lightweight Structures, Chemnitz, Zwickau, 2015
[2] Fechter, M.; Foith-Förster, P.; Pfeiffer, M. S.; Bauernhansl, T.: Axiomatic design approach for human-robot collaboration in flexibly linked assembly layouts. CIRP Design Conference 26, Stockholm, 2016
[3] Foith-Förster, P.; Bauernhansl, T.: Changeable and reconfigureable assembly systems: A structure planning approach in automotive manufacturing. 15th Stuttgart International Symposium – Automotive and Engine Technology, Stuttgart, 2015
[4] Kretschmer, F.; Lechler, A.; Verl, A.: Gelbe Seiten für Industrie 4.0. VDI Automation, 2016
[5] Kretschmer, F.: Gelbe Seiten für Industrie 4.0, Automat!on praxis, 2016.
[6] Vorderer, M.; Junker, S.: Highly Versatile Plug&Produce Assembly Systems. 16th Stuttgart International Symposium, Automotive and Engine Technology, Wiesbaden, 2016
[7] Vorderer, M.; Junker, S.; Lecher, A.; Verl, A.: Wandlungsfähiges Konzept für die Montage 4.0. Erhöhung der Wandlungsfähigkeit von automatisierten Montageanlagen, wt Werkstattstechnik online 106 (2016), Nr. 5, S.314–319
[8] Vorderer, M.; Junker, S.; Lechler, A.; Verl, A.: CESA³R: Highly Versatile Plug-and-Produce Assembly System. IEEE International Conference on Automation Science and Engineering (CASE), Fort Worth, Texas/USA, 2016
[9] Naumann, M.; Fechter, M.: Robots as enablers for changeability in assembly applications. 15th Stuttgart International Symposium – Automotive and Engine Technology, 2015, pp. 357–373
[10] Wehking, K.-H.; Popp, J.: Linked logistics concepts for future automobile manufacturing using innovative equipment. 16. Internationales Stuttgarter Symposium, 2016, pp. 537–545
[11] Wekhing, K.-H.; Popp, J.: Automobilproduktionslogistik – heute, morgen und übermorgen. BVL-Kongressband, 2015, p. 324
[12] Popp, J.; Wehking, K.-H.: Neuartige Produktionslogistik für eine wandelbare und flexible Automobilproduktion. Tagungsband 11. Fachkolloquium der Wissenschaftlichen Gesellschaft für Technische Logistik (WGTL), 2015, pp. 257–261
[13] Vorderer, M.; Fechter, M.; Kretschmer, F.; Verl, A.: Wandlungsfähige Produktion von Morgen, wt Werkstattstechnik online 106 (2016), Nr. 7/8, S. 533–538
Dipl.-Ing. Patrick Böhler Institut für Flugzeugbau, Universität Stuttgart Allmandring 5b, 70569 Stuttgart Tel. +49 (0)711 / 685-60466 patrick.boehler@ifb.uni-stuttgart.de www.ifb.uni-stuttgart.deDipl.-Ing. Thomas Dietz Fraunhofer-Institut für Produktionstechnik und Automatisierung IPA Nobelstr. 12, 70569 Stuttgart Tel. +49 (0)711 / 970-1152 thomas.dietz@ipa.fraunhofer.de www.ipa.fraunhofer.deDipl.-Ing. Jörg Dittmann Institut für Flugzeugbau, Universität Stuttgart Allmandring 5b, 70569 Stuttgart Tel. +49 (0)711 / 685-68484 joerg.dittmann@ifb.uni-stuttgart.de www.ifb.uni-stuttgart.deDr. Klaus Fürderer Daimler AG, 89013 Ulm Tel. +49 (0)731 / 5052887 klaus.fuerderer@daimler.com www.daimler.com/deDr. Max Hoßfeld ARENA2036 e.V. Pfaffenwaldring 19, 70569 Stuttgart Tel.: +49 (0)711 / 685-68368 info@arena2036.de www.arena2036.deDas Forschungs- und Entwicklungsprojekt „ARENA2036“ wird mit Mitteln des Bundesministeriums für Bildung und Forschung (BMBF) im Rahmen der Förderinitiative „Forschungscampus – öffentlich-private Partnerschaft für Innovationen“ gefördert und vom Projektträger Karlsruhe (PTKA) betreut. Die Verantwortung für den Inhalt dieser Veröffentlichung liegt beim Autor.