DiProLeA – Digitale Produktentstehungsprozesse
In Zeiten von kürzeren Entwicklungszyklen und gleichzeitig einer höheren Komplexität von Produkten steigen die Anforderungen an die Digitalisierung von Prozessen. Unternehmen verwalten dabei produktspezifische Informationen des Produktentstehungsprozesses häufig aufgabenbezogen in heterogenen Systemen. Mit digitalen Werkzeugen sollen Arbeiter unterstützt und Prozesse sicherer gestaltet werden. Das Projekt DiProLeA erforscht ein ganzheitliches Assistenzsystem für den Produktentstehungsprozess vom Produktdesign bis zur Fertigung. Das Konzept wird anhand zweier Anwendungsfälle veranschaulicht. Das Projekt wurde in der Fördermaßnahme „Beherrschung der Komplexität soziotechnischer Systeme“ eingereicht und bildet damit einen Beitrag zum Advanced Systems Engineering für die Wertschöpfung von morgen.
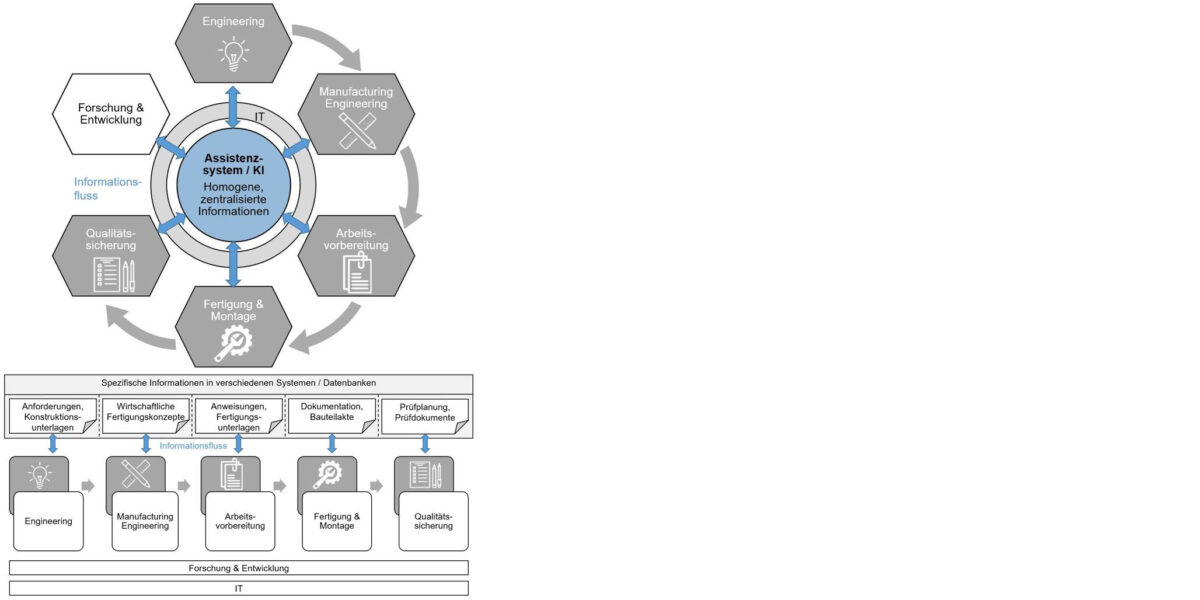
Bild 1. Heterogene Datenquellen, die im Assistenzsystem für die Produktentstehung zusammengeführt werden. Grafik: Hutchinson PFW Aerospace GmbH
End-to-end socio-technical assistance systems for product creation – DiProLeA – Digital product creation processes
Abstract: Due to shorter development cycles and, at the same time, greater product complexity, the requirements for the digitalization of processes are increasing. Companies often manage product-specific information from the product development process in heterogeneous systems on a task-specific basis. Digital tools are intended to support workers and make processes more secure. The DiProLeA project is researching a holistic assistance system for the product development process from product design to production. The concept is illustrated using two use cases. The project was submitted as part of the funding measure „Mastering the complexity of socio-technical systems“ and represents a contribution to advanced systems engineering for the value creation of tomorrow.
Einleitung
Die umfassende und konsistente Digitalisierung von Produktionsprozessen stellt nach wie vor eine der großen Herausforderungen für den Wirtschaftsstandort Deutschland dar. Während in Teilbereichen die digitale Erfassung und Optimierung von Abläufen oftmals erfolgreich funktioniert, insbesondere unter Einsatz von Methoden des maschinellen Lernens, ist eine durchgängige Betrachtung von Entwicklung und Produktion eines Artikels bislang kaum realisiert. Dies hat verschiedene Ursachen: Zum einen ist die Standardisierung der sehr heterogenen, teilweise unstrukturierten Datenquellen eine gewaltige Aufgabe für sich. Aber selbst mit standardisierten Daten, die ohne Beziehung zueinanderstehen, lassen sich keine tief gehenden Erkenntnisse gewinnen. Hier ist eine semantische Verknüpfung, bspw. über eine Ontologie, erforderlich. Auch was die Bereitstellung der Daten angeht, stellen sich Herausforderungen: Da oft verschiedene Bereiche im Unternehmen, und ggf. auch externe Partner (Kunden, Zulieferer), zu diesen beitragen, sind Themen des Datenschutzes und der Datensicherheit ebenfalls relevant. Im Idealfall nutzt man hier Distributed Ledger Technologien, bekannt durch die Blockchain, um eine manipulationssichere Vertrauensinfrastruktur zu schaffen. Schließlich ist auch die Wissensvermittlung ein wichtiger Punkt, gerade in Zeiten von Fachkräftemangel und nichtmuttersprachlichen Arbeitskräften. Hier bietet bspw. der Einsatz von Extended Reality (XR) einen intuitiven Zugang. Die Implementierung und Einführung all dieser neuen Technologien erfordert am Ende auch ein komplexes Veränderungsmanagement, das nicht nur die Stakeholder, sondern auch die späteren Anwender mit ins Boot nehmen soll und dadurch die Menschen in den Fokus stellt. All diesen Herausforderungen widmet sich das vom BMBF geförderte Forschungsprojekt „DiProLeA“. Es betrachtet branchenübergreifend an verschiedenen Anwendungsfällen aus der verarbeitenden Industrie, wie ein durchgängiger digitaler Entwicklungs- und Produktionsprozess gestaltet, und die Produktion mithilfe eines sozio-technischen Assistenzsystems unterstützt werden kann.
Einbeziehung der Mitarbeitenden
Die erfolgreiche Integration von Digitalisierung, Automatisierung und Dokumentation in Produktionsprozesse erfordert eine sorgfältige Berücksichtigung der Mitarbeiterbelange. Damit Innovationen in diesen Bereichen zuverlässig und nachhaltig funktionieren, ist die Akzeptanz, die aktive Nutzung und der Einsatz erarbeiteter Prozesse und Technologien durch die Mitarbeitenden entscheidend. Um eine hinreichende Akzeptanz der Mitarbeitenden zu erreichen, ist eine Zentrierung auf die Nutzenden bei der Technologieentwicklung sowie dem Veränderungsprozess entscheidend. Diese Ansätze minimieren einerseits eine Überforderung und erhöhen andererseits die Akzeptanz und damit die effektive Nutzungsbereitschaft von Mitarbeitenden. Im Forschungsprojekt DiProLeA erweiterte Projektpartner YOUSE den User-Centred Design Prozess [1] um den Aspekt der Implementierung, hin zum User-Centred Change (UCC) Prozess, der den mit der Technikimplementierung einhergehenden Transformationsprozess berücksichtigt. Während des Forschungsprojektes erfolgte bereits früh der partizipative Einbezug von Mitarbeitenden der Anwenderunternehmen, z. B. über qualitative Interviews. Dadurch können einerseits Erwartungen und Bedürfnisse ausreichend adressiert und Fehlentwicklungen vermieden werden [2]. Andererseits wurden innerhalb der Interviews relevante Aspekte der Unternehmens- und Führungskultur exploriert und die Ergebnisse in eine Studie, das sogenannte Narrativ, überführt. Dieses dient als Grundlage für die Gestaltung eines Change-Management-Konzeptes zur Gestaltung des Transformationsprozesses. Dieser Ansatz wird darüber hinaus durch die Durchführung eines sog. ELSI-Workshops mit dem gesamten Konsortium erweitert. Hierbei werden die ethischen, sozialen und legalen Implikationen des DiProLeA-Demonstrators untersucht. Eine Berücksichtigung ethischer Aspekte gewinnt gerade vor dem Hintergrund des Einsatzes von KI-Technologien zunehmend an Relevanz [3].
Konzept
Das DiProLeA-Konzept zielt darauf ab, ein Assistenzsystem für Produktingenieure und Montagearbeiter zu entwickeln, das den Produktlebenszyklus mit einer vollständigen, nahtlosen Prozesskette abdeckt. Die Unterstützung der digitalen Transformation auf mehreren Unternehmensebenen ermöglicht die nachhaltige Einführung eines durchgängigen digitalen Prozessmanagements, das die Grundlage für die erfolgreiche Implementierung eines KI-basierten Assistenzsystems bildet. Erreicht wird dies durch die Entwicklung semantischer Informationsmodelle und deren Integration in eine Systemarchitektur, die wissensbasiertes Engineering ermöglicht. Die semantischen Informationsmodelle werden logisch interpretiert, z.B. für die Rückverfolgbarkeit entlang der Wertschöpfungskette oder die Synthese von Arbeitsanweisungen.
Die Einbindung aller relevanten Personen des gesamten Produktentstehungsprozesses ist entscheidend, um sicherzustellen, dass alle benötigten Informationen erfasst und berücksichtigt werden (siehe Bild 1). Produktingenieure arbeiten mithilfe von standardisierten Prozessen, z.B. Advanced Product Quality Planning (APQP), die die grundlegenden Daten, Informationen und Abhängigkeiten der Produktentwicklung erfassen und dem Assistenzsystem zur Verfügung stellen. Die Montagearbeiter, die immer komplexere Fertigungsprozesse bewältigen müssen, werden durch das Assistenzsystem geführt, das die Arbeitsergebnisse dokumentiert, verifiziert und dem Nutzer somit die nötige Sicherheit vermittelt. Das System ist zudem in der Lage, bei Onboarding-Maßnahmen zu unterstützen, um die Auswirkungen der Personalfluktuation auf die Produktivität zu verringern.
Semantische Wissensbasis
In DiProLeA wurden durch den Projektpartner fortiss ontologiebasierte, semantische Beschreibungssprachen entwickelt, die relevantes Wissen über den Fertigungsprozess, das entworfene und zu montierende Produkt und die an diesen Aktivitäten beteiligten Ressourcen beschreiben [4]. Dazu gehören die Modellierung von Produktionsschritten, ihre logischen und zeitlichen Abhängigkeiten, Fertigungsparameter sowie automatisch abgeleitete Anforderungen, die Maschinen und Arbeiter und ihre Werkzeuge erfüllen müssen. Für die formale Modellierung mechanischer Produkte wird die CAD-Ontologie OntoBREP verwendet, um geometrische Informationen auf einer semantischen Ebene darzustellen [5]. Zusätzliche Annotationen zu Produkteigenschaften und der APQP-geführten Produktentwicklung können daher auf jede geometrische Teilmenge der OntoBREP-Repräsentation angewendet werden. So kann sich die Prozessbeschreibung direkt auf einzelne Punkte, Kurven oder Flächen des Geometriemodells des Produkts beziehen und so ein besseres Verständnis der Beziehungen zwischen Kundenanforderungen, Produktionsprozessen und dem Produkt selbst herstellen. Darüber hinaus kann die Parametrisierung von Teilaufgaben der Fertigungsprozesse oder von Produktmerkmalen zum Teil automatisch abgeleitet werden.
Während Geometriemodelle automatisch aus Industrieformaten (z.B. STEP) konvertiert werden können, müssen Prozesse oft über grafische Benutzerschnittstellen spezifiziert werden. Individuelle menschliche Fähigkeiten werden dabei explizit modelliert und decken allgemeine Best Practices ab, z. B. vorgeschlagene Belastungsgrenzen und benötigte Qualifikationsniveaus. Dabei werden auch werkzeuginduzierte Fähigkeitserweiterungen der Werker erfasst und automatisiert abgeleitet. Technische Ressourcen, d. h. die Komponenten des Assistenzsystems in der Montagezelle, werden semantisch beschrieben und in einem Fähigkeitsabgleichsprozess verwendet, um festzustellen, ob eine Arbeitszellenkonfiguration mit einer bestimmten Montageaufgabe kompatibel ist.
Die vorgestellten Beschreibungssprachen liefern das Vokabular zur Beschreibung relevanter Entitäten und ihrer Beziehungen in der Anwendungsdomäne. Für spezifische Anwendungsfälle müssen diese Konzepte instanziiert werden. Die miteinander verknüpften semantischen Instanzmodelle bilden einen Wissensgraphen, der persistent in einer Wissensbasis gespeichert wird. Diese Wissensbasis bietet Mittel zur automatischen Schlussfolgerung durch logische Inferenz und semantischen Abfragen. Dadurch können viele explizite und implizite Aspekte für die Entscheidungsfindung im Allgemeinen und die Anpassung der Kommunikationsmodalitäten und -inhalte des Assistenzsystems im Besonderen berücksichtigt werden.
Anwendungsfall – Semantische Process Execution Assistenz für die Montage von Laufringlagern
Die IBO GmbH entwickelt und fertigt als Projekt- und Anwendungspartner Wälzlagersysteme für komplexe Anwendungen von Automation bis Luftfahrt und Verteidigung. Als KMU (kleines und mittleres Unternehmen) ist IBO auf Prozesse, Ressourcen und Systeme angewiesen, die zum einen die hohen Qualitätsanforderungen sicherstellen und zum anderen eine effiziente und flexible Abwicklung von Aufgaben ermöglichen. Vor diesem Hintergrund ist die IBO kontinuierlich bestrebt seine Daten und Prozesse zu strukturieren, miteinander zu verknüpfen, sowie Informationen und Arbeitsschritte zu automatisieren.
Eine zentrale Schlüsselkomponente zur Beherrschung dieser Herausforderungen besteht aus dem selbstentwickelten Assistenzsystem trustkey, ein fortschrittliches Process Execution System, das über die Grenzen traditioneller Produktionsmethoden hinausgeht. trustkey zeichnet sich durch seine Fähigkeit aus, flexible Process Experiences zu bieten, die sich nahtlos in die täglichen Arbeitsabläufe integrieren lassen. Diese Flexibilität ermöglicht es trustkey, verschiedenste Technologien – von intuitiven Benutzeroberflächen über maschinelles Lernen bis hin zu fortschrittlichen Sensorik- und Transaktionssystemen – in einem kohärenten Rahmen zu verknüpfen. trustkey arbeitet nach den Grundsätzen Strukturieren, Verknüpfen und Automatisieren. Daten und Prozesse werden basierend auf ihrem Inhalt in Aktionspakete, Ressourcen und Wissen gegliedert und strukturiert, Bild 2. Diese Organisation ermöglicht die Verknüpfung von Informationen sowohl intern als auch mit Systemen von Drittanbietern, wie z. B. mit der zuvor eingeführten semantischen Wissensbasis. Zudem können wiederkehrende Aufgaben und Abläufe für eine effizientere Bearbeitung automatisiert werden.
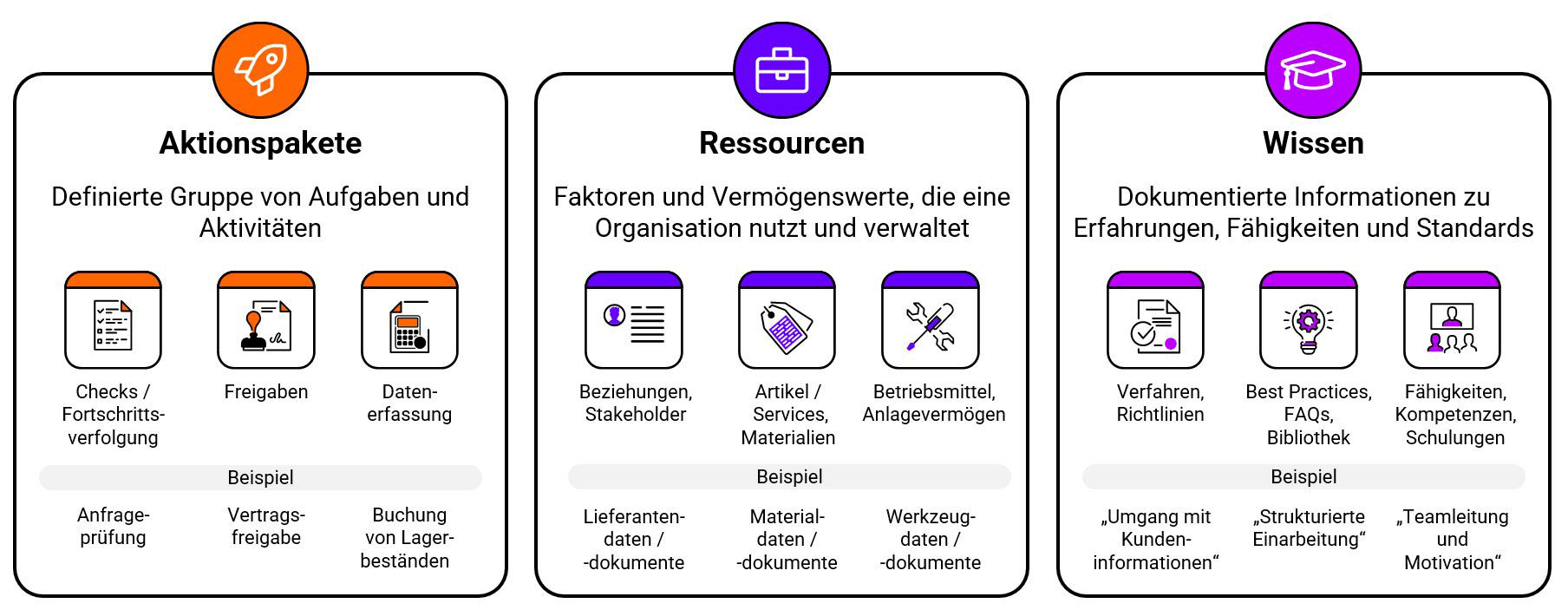
Bild 2. Gliederung von Daten und Prozessen einer Produktion in die drei Bereiche Aktionspakete, Ressourcen, und Wissen. Entstehenden Informationen lassen sich anhand der definierten Bereiche in vorhandenen Templates strukturiert ablegen. Grafik: IBODigital GmbH
Ein solcher Anwendungsfall ist für die IBO die Fertigung von Laufringlagern. Laufringlager sind komplexe Leichtbaueinheiten, deren Montage höchste Genauigkeit und ein tiefes Verständnis der Mechanik erfordert. Schon bevor das eigentliche Teil gefertigt wird, hat trustkey Zugriff auf eine Wissensdatenbank, die alle relevanten Informationen über den Produktionsprozess, die erforderlichen Werkzeuge und die spezifischen Fähigkeiten eines Werkers beinhaltet, um so einen optimalen Ablauf planen zu können. Dies ermöglicht eine nahtlose Anpassung des Arbeitsprozesses an die jeweiligen Bedingungen und verfügbaren Ressourcen.
Projektpartner TH Aschaffenburg hat eine Montagezelle für Demonstrationszwecke aufgebaut, in die sowohl die semantische Wissensbasis als auch das Process Execution System integriert sind [6]. In der Montagezelle kommen hochauflösenden Kameras in Verbindung mit modernen DeepLearning-Methoden zum Einsatz, die jeden Schritt des Fertigungsprozesses nachverfolgen. Diese Kameras erfassen kontinuierlich, wie der Werker das Bauteil bearbeitet, welche Werkzeuge verwendet werden und wie die einzelnen Arbeitsschritte ausgeführt werden. Die erfassten Daten werden in Echtzeit mit der Wissensdatenbank abgeglichen, wodurch eine lückenlose digitale Abbildung des gesamten Prozesses entsteht, Bild 3. Sollte die Erkennung zu einem Zeitpunkt nicht mehr gegeben sein, kann das System fehlende Informationen beim Werkenden anfragen, um sich selbstständig an den Prozess anzupassen.
![Bild 3. Darstellung der Demonstrator-Montagezelle (links) und Visualisierung der digital erfassten Daten der Arbeitszelle während eines Montagevorgangs. Grafik aus [6]](https://www.ingenieur.de/wp-content/uploads/2024/03/W_BMBF_Projekt-DiProLea_Bild-3.jpg)
Bild 3. Darstellung der Demonstrator-Montagezelle (links) und Visualisierung der digital erfassten Daten der Arbeitszelle während eines Montagevorgangs. Grafik aus [6]
Die kontinuierliche, digitale Abbildung des Systems bietet mehrere Vorteile: 1) Automatische Fehlererkennung, etwa bei falscher Werkzeugnutzung oder fehlerhaften Arbeitsschritten; 2) proaktive Unterstützung der Werker mit Echtzeit-Anweisungen; 3) Identifikation und Optimierung ineffizienter Arbeitsschritte durch Datenanalyse. So wird die Produktqualität und Produktivität gesteigert, sowie die Arbeitszufriedenheit durch Systemunterstützung verbessert und Produktfehler minimiert.
Zusammenfassend lässt sich sagen, dass der Einsatz von Wissensdatenbanken in Verbindung mit Methoden der künstlichen Intelligenz und Process Execution Systemen wie trustkey einen Fortschritt in der Fertigungseffizienz und Qualitätssicherung durch Assistenzsysteme darstellt. Diese Technologien bieten eine präzise Nachverfolgung und Unterstützung, die es ermöglichen, Produkte mit höchster Qualität herzustellen, während gleichzeitig die Flexibilität und Anpassungsfähigkeit an individuelle Bedürfnisse gewährleistet wird.
Anwendungsfall – Wissensgraph-basierte XR-Werkerassistenz in der Montage von Rohrkomponenten
Die Fertigung von Rohr- und Strukturkomponenten bei Anwendungspartner Hutchinson PFW Aerospace ist geprägt von manuellen Montage- und Schweißtätigkeiten, welche ein umfangreiches spezifisches Fachwissen für die jeweiligen Baugruppen erfordern. Dabei müssen hohe Qualitätsstandard eingehalten und dokumentiert werden. Zur Unterstützung des Werkers müssen viele prozessrelevante Daten bereitgestellt werden. Diese zu Beginn unvernetzten Daten werden in sogenannten Ausführungsanweisungen verknüpft und aufbereitet. Diese Anweisungen enthalten somit Fertigungsinformationen bzgl. Varianten der zu verwendenden Fertigungs- und Hilfsmittel und unterstützen den Arbeiter bei der Bauteilherstellung. DiProLeA zielt auf die flexible, und teil-automatische Erstellung und Analyse der Ausführungsanweisungen, mithilfe der von Projektpartner Cognition Factory entwickelten Wissensplattform „xLenz“, sowie der gezielten und ansprechenden Visualisierung von Informationen mittels XR-Technologien durch Lösungen von Projektpartner SKM Informatik.
xLenz ist eine innovative Wissensplattform, die KI-Methoden nutzt, um Daten aus verschiedenen Quellen zusammenzuführen und miteinander zu verknüpfen. Ursprünglich wurde die Plattform entwickelt, um Produktionslinien mit Maschinen hierarchisch zu modellieren und die entsprechenden Daten wie technische Zeichnungen, Wartungsdokumentation, Materialien, Bilder und physikalische Parameter hierarchisch zu strukturieren. Dazu werden KI-Methoden wie die Dokumentenanalyse, Bilderanalyse und Graphenanalyse eingesetzt, um Datenpunkte miteinander zu verknüpfen und damit zugreifbares „Wissen“ zu erhalten. Mithilfe von entwickelten Suchalgorithmen, werden Informationen schnell erreichbar, die vorher in unterschiedlichen Dateien oder Datenbanken aufwendig zu suchen waren.
In DiProLeA wird eine Werkerassistenz mithilfe von xLenz umgesetzt. Dazu werden vorhandene Ausführungsanweisungen analysiert und die Arbeitsschritte hierarchisch aufbereitet. So können nun neben der textuellen Beschreibung der Arbeitsschritte auch CAD-Modelle, technische Zeichnungen, Bilder, sowie relevante Dokumente, wie Normen oder Zertifikate, direkt mit den jeweiligen Arbeitsschritten verknüpft werden. Zudem können webbasiert fehlende und zusätzliche Informationen der Arbeitsplanung, Arbeitsvorbereitung oder auch Arbeitsdurchführung dynamisch ergänzt werden. Dadurch verfeinern sich die Arbeitsanweisungen immer weiter und erlauben ein schnelles Einlernen sowie Durchführen der Arbeitsschritte.
Die gesammelten und aufbereiteten Informationen können entweder direkt in xLenz betrachtet und verwendet werden, Bild 4, als auch von anderen Werkerassistenzsystemen, wie der im Folgenden vorgestellten XR-Technologie, benutzt werden, um den Mitarbeitern die Informationen anzuzeigen, die gerade relevant sind.
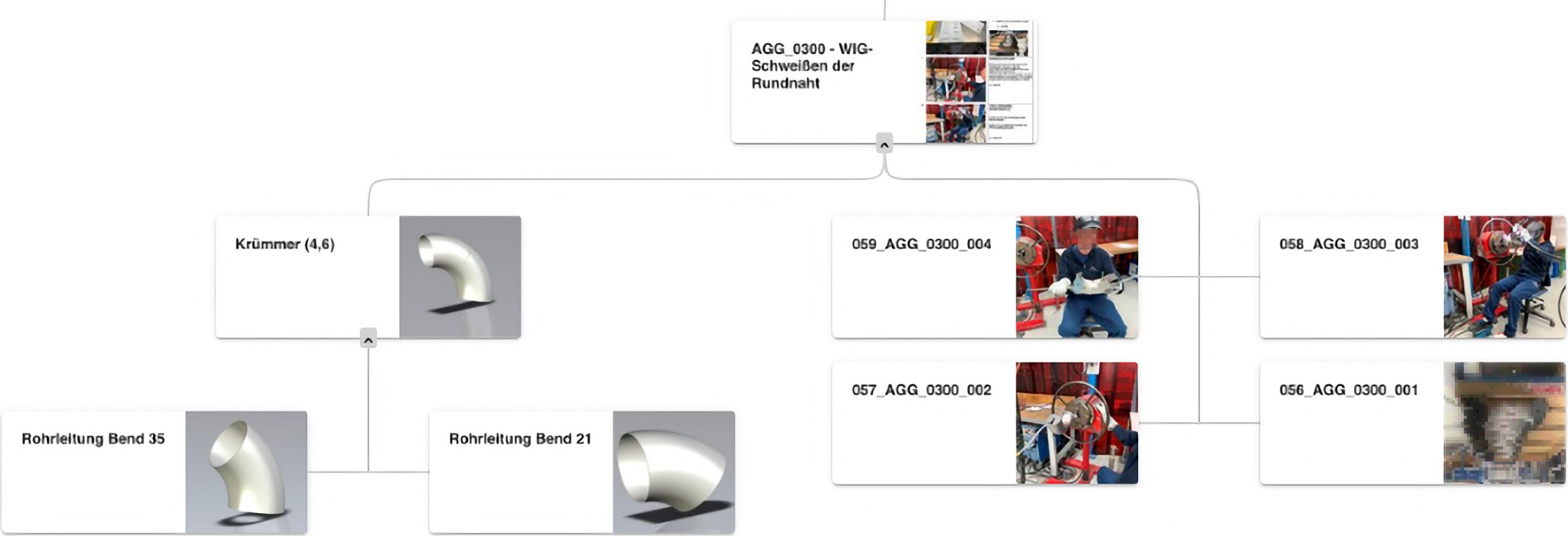
Bild 4. Abhängigkeitsvisualisierung von Bauteilen und zugehörigen Arbeitsschritten in xLenz. Grafik: Cognition Factory GmbH
Die von SKM Informatik entwickelte SKMx Technologie bietet ein einheitliches plattformübergreifendes Datenkonzept, welches mit allem SKM XR Viewer Apps genutzt werden kann, sowie Tools zur Aufbereitung und Publizierung von XR Datensätzen, wie dem SKM XR Publisher und den SKMx Webservice. Dabei transportiert der gesicherte SKMx Datencontainer alle für die Visualisierung in XR relevanten Daten: 3D-Modelle mit Metadaten, Mediendaten, Geoinformationen und Points of Interest (POIs).
Um gezielt Information am 3D-Modell bereitzustellen und Mediendaten mit dem 3D-Modell zu verknüpfen, können verschiedene POI-Typen konfiguriert werden. Diese enthalten die Verknüpfung von Mediendaten (PDF, Bild, Video, Audio), das Anzeigen von Textinformationen, die Verlinkung mittels URLs und die Positionierung der 3D-Daten.
Abfolgen und Arbeitsanweisungen werden mit sogenannten Szenen und Panels erstellt. Dabei definieren Szenen welche Modelle und POIs im Szenenkontext referenziert werden und Panels steuern den Ablauf, Sichtbarkeitsstaus, Interaktion und Lagetransformation innerhalb einer Szene.
Der XR-Datensatz wird per QR-Code (online) oder Dateitransfer (offline) auf die jeweiligen Endgeräte geladen, Bild 5.
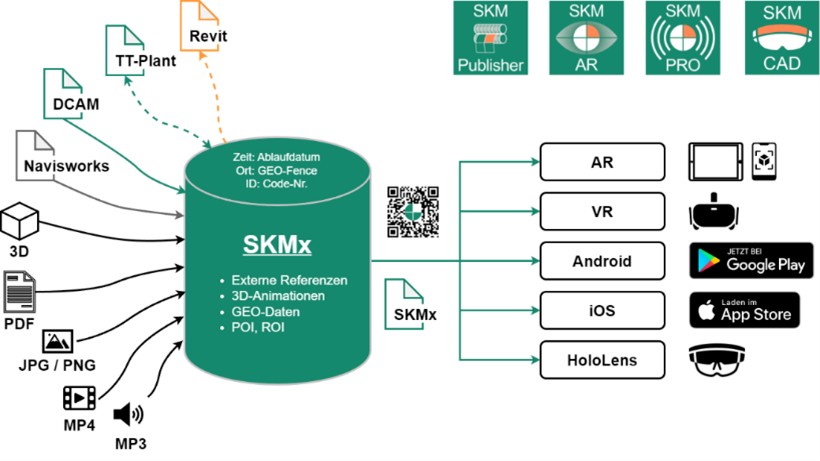
Bild 5. SKMx-Datenkonzept zur Beschreibung von Geometriedaten und zusätzlichen Metainformationen und verschiedene Anzeigekanäle mit XR. Grafik: S.K.M. Informatik GmbH
Im Rahmen des DiProLeA Projektes wurde das SKMx Konzept um eine Schnittstelle zur xLenz Plattform erweitert. Über diese werden die aufbereiteten und strukturierten Daten an den SKM XR Publisher übergeben, der die weitere Bearbeitung ermöglicht. Der Anwender fügt dem Datensatz Panels hinzu, die den Arbeitsablauf mithilfe der genannten Funktionen abbilden, Bild 6.
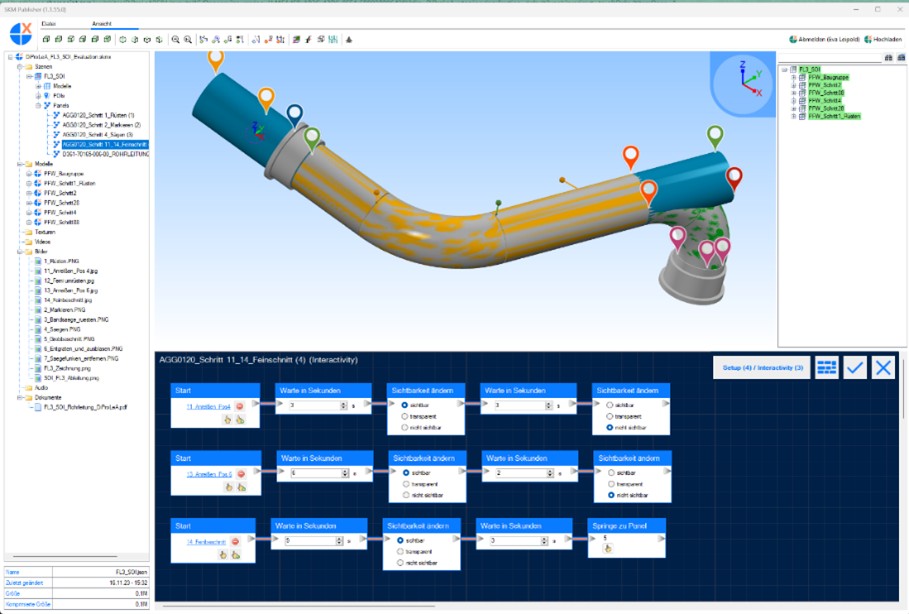
Bild 6. Generierung eines SKMx-Datencontainers für ein Beispiel-Rohrsegment aus dem Flugzeugbau. Grafik: S.K.M. Informatik GmbH
Die XR-Daten können nach dem Transfer auf die HoloLens in der realen Umgebung platziert werden. Danach lassen sich die zuvor erstellten Abläufe durch den Nutzer gesteuert wiedergeben. POIs stellen durch interaktive Schaltflächen zusätzliche Daten und Informationen bereit deren Inhalte in virtuellen Fenstern dargestellt werden. Diese können ebenfalls den Anforderungen des Arbeitsplatzes entsprechend angeordnet werden.
Zusammenfassung
Der aktuelle Trend in der Fertigung zu höherer Produktkomplexität und Variantenvielfalt sowie zu kleineren Losgrößen ist durch eine Vielzahl unterschiedlicher Tätigkeiten in den Bereichen Produktdesign, Entwicklung, Produktion, Montage und Qualitätssicherung gekennzeichnet. Eine kontinuierliche Verbesserung dieser Prozesse ist notwendig, um der Forderung nach erhöhter Effizienz, verkürzten Lieferzeiten und der Überprüfung von Kundenanforderungen gerecht zu werden. Das Konzept eines wissensbasierten, soziotechnischen Assistenzsystems unterstützt die Koordination zwischen den Funktionsbereichen. Es kann sowohl die Effektivität als auch die Effizienz der produzierenden KMU durch verschiedene Einflüsse verbessern:
- Die Produktentwicklungszyklen können durch die integrierte Nutzung von Informationen über alle Systeme, alle Wertschöpfungsstufen und deren individuelle Aufbereitung für den jeweiligen Empfänger sowie entsprechende Rückkopplungsschleifen verkürzt werden.
- Durch den Einsatz von assistiven Technologien können Fehler zuverlässiger vermieden und damit verbundene Risiken des Faktors Mensch reduziert werden.
- Schulungs- und Onboarding-Prozesse können durch den Einsatz eines Systems, das das Selbstlernen der Mitarbeiter fördert, beschleunigt werden.
- Der Handlungsspielraum der Mitarbeiter kann durch systemisch geführtes Empowerment erweitert werden.
Das wissensbasierte Assistenzsystem erleichtert zudem die Nachweisführung und -verfolgung über die gesamte Wertschöpfungskette durch den Einsatz eines verketteten Identitätsmanagementsystems, wodurch die Produktauthentizität sichergestellt und der Produktionsplanungsprozess sowie der Einsatz entsprechender Ressourcen verbessert werden.
Förderhinweis: Dieses Forschungs- und Entwicklungsprojekt wird mit Mitteln des Bundesministeriums für Bildung und Forschung (BMBF) im Programm „Zukunft der Wertschöpfung – Forschung zu Produktion, Dienstleistung und Arbeit“ (Förderkennzeichen 02J19B120 ff.) gefördert und vom Projektträger Karlsruhe (PTKA) betreut. Die Verantwortung für den Inhalt dieser Veröffentlichung liegt bei den Autoren.
Literatur
- Deutsches Institut für Normung: DIN EN ISO 9241–210:2011–01, Ergonomie der Mensch-System-Interaktion – Teil 210: Prozess zur Gestaltung gebrauchstauglicher interaktiver Systeme. Deutsche Fassung EN ISO 9241–210:2010. Berlin: Beuth Verlag, 2011
- Gemser, G.; Perks, H.: Co-Creation with Customers: An Evolving Innovation Research Field. Journal of Product Innovation Management, 32 (2015), S. 660–665
- Bundesregierung: Strategie Künstliche Intelligenz der Bundesregierung, 2018. Internet: www.bundesregierung.de/resource/blob/997532/1550276/3f7d3c41c6e056957 41273e78b8039f2/2018–11–15-ki-strategie-data.pdf
- Perzylo, A.; Kessler, I.; Profanter, S.; Rickert, M.: Toward a Knowledge-Based Data Backbone for Seamless Digital Engineering in Smart Factories. Proceedings of the IEEE International Conference on Emerging Technologies and Factory Automation (ETFA), 2020
- Perzylo, A.; Somani, N.; Rickert, M.; Knoll, A.: An ontology for CAD data and geometric constraints as a link between product models and semantic robot task descriptions. Proceedings of the IEEE/RSJ International Conference on Intelligent Robots and Systems (IROS), 2015
- Mittel, D.; Hubert, A.; Ding, J.; Perzylo, A.: Towards a Knowledge-Augmented Socio-Technical Assistance System for Product Engineering. Proceedings of the IEEE International Conference on Emerging Technologies and Factory Automation (ETFA), 2023
Pia Diekmann
YOUSE GmbH
Florastr. 47, 13187 Berlin
pia.diekmann@youse.de
www.youse.de
Anika Holl
Hutchinson PFW Aerospace GmbH
Am Neuen Rheinhafen 10, 67346 Speyer
anika.holl@hutchinson.com
www.pfw.aero
Andreas Hubert
Technische Hochschule Aschaffenburg
Würzburger Str. 45, 63743 Aschaffenburg
andreas.hubert@th-ab.de
www.th-ab.de
Michael Kröhn
ROBUR Automation GmbH
Hansaring 18, 63843 Niedernberg
michael.kroehn@robur-automation.com
www.robur-automation.com
Eva Leipold
S.K.M. Informatik GmbH
Eckdrift 95, 19061 Schwerin
eleipold@skm-informatik.com
www.skm-informatik.com
Daniel Lemberger
IBO GmbH
Ammerthalstr. 9, 85551 Kirchheim b. München
daniel.lemberger@ibo-tec.de
www.ibo-tec.de
Claus Lenz
Cognition Factory GmbH
Frei-Otto-Str. 22, 80797 München
lenz@cognitionfactory.com
www.cognitionfactory.com
Dominik Mittel
Alexander Perzylo
fortiss – Landesforschungsinstitut des Freistaats Bayern
und An-Institut der Technischen Universität München
Guerickestr. 25, 80805 München
{mittel, perzylo}@fortiss.org
www.fortiss.org