Direktcompoundierung für die Medizintechnik
In diesem Beitrag wird die Entwicklung des Direktcompoundierens (Direktspritzguss und Direktextrusion) als Alternative zum konventionellen zweistufigen Prozess, der aus dem Compoundieren und anschließender Verarbeitung in der Kunststofftechnik besteht, vorgestellt. Bei der Direktcompoundierung werden Mischen, Schmelzen und Formen zu fertigen Produkten kombiniert. Ein Vorteil hierbei ist die Möglichkeit von Produktindividualisierungen durch die direkte Einflussnahme und Anpassung der Materialrezeptur.
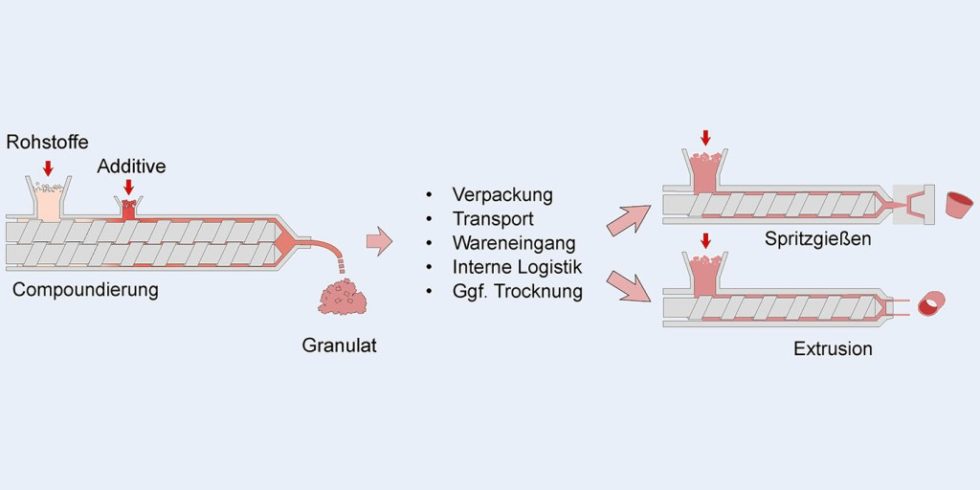
Bild 1. Standardprozesskette aus Compoundieren mit nachfolgendem Spritzgießen oder Extrudieren.
Foto: Institut für Werkstofftechnik-Kunststofftechnik, Universität Kassel
Ausgabe 6-2021, S. 435
1 Einleitung
Medizinische Einwegprodukte bestehen zu einem großen Teil aus Kunststoffen. Das Produktionsspektrum reicht von Massenprodukten mit Stückzahlen von hundert Millionen bis hin zu individuell auf bestimmte klinische Anwendungsbereiche zugeschnittenen Kleinserien. Besondere Anforderungen wie Sterilisierbarkeit und Biokompatibilität erfordern oft den Einsatz von individuell angepassten Materiallösungen. Diese werden bisher in verschiedenen Aufbereitungsverfahren (Compoundierung) durch Einmischen von Additiven in Standardkunststoffe hergestellt um medizintechnisch geeignete Thermoplaste zu erhalten. Anschließend erfolgt im Extrusions- oder Spritzgießverfahren die Weiterverarbeitung zu Produkten. Potenziale zur Produktindividualisierung und Produktfunktionalisierung können so aufgrund der geringen Flexibilität der Großindustrie oft nicht ausgeschöpft werden. Auch die Herstellung von Produkten mit kleineren Stückzahlen ist nicht oder nur unter wirtschaftlich unattraktiven Bedingungen möglich, da die Bereitstellung von kleinen Materialmengen unrentabel ist.
Ein Ansatz zur Bewältigung der genannten Herausforderungen ist die Kombination aus Aufbereitungs- und Formgebungsprozess. Das Forschungsprojekt zielt darauf ab, den Aufbereitungsschritt in die Extrusion und das Spritzgießen zu integrieren. Dies soll dazu führen, dass Medizintechnikunternehmen für Spezialanwendungen und Kleinserien nicht mehr auf das Angebot der Compoundeure/Materialhersteller angewiesen sind und schnell auf Änderungen reagieren können. Dadurch wird auch ermöglicht komplexe Produkte und/oder kleine Stückzahlen effizient und wirtschaftlich zu fertigen.
Das aktuelle, vom Bundesministerium für Bildung und Forschung (BMBF) geförderte Projekt „MeDiComP“ (Entwicklung von Direkt-Compoundier-Prozessen für die Herstellung medizinischer Einmalprodukte) steht in direktem Zusammenhang mit den Zielen des Gesamtforschungsprogramms „Innovationen für die Produktion, Dienstleistung und Arbeit von morgen“, da durch die angestrebte integrierte Produktionstechnik nicht nur die Variabilität und Flexibilität und Reaktionsfähigkeit, sondern auch die Produktivität erhöht wird. Resultierend daraus wird eine sozialverträgliche Arbeitsgestaltung ermöglicht und zugleich die Zukunftsfähigkeit des Produktionsstandorts Deutschland unterstützt.
2 Stand der Wissenschaft und Technik
Die Standardprozesskette bei der Kunststoffverarbeitung kann anhand von Bild 1 beschrieben werden. Die Ausgangskomponenten (Polymere und Additive) werden in der Regel mit einem Doppelschneckenextruder gemischt und das daraus entstehende Granulat wird anschließend zu Produkten weiterverarbeitet. Die Prozesskette ist dabei örtlich getrennt und wird meist durch spezialisierte Unternehmen (Zulieferer und Verarbeiter) umgesetzt. In der Verarbeitung nimmt sowohl der Spritzguss als auch die Extrusion eine übergeordnete Rolle ein. Ein Nachteil der getrennten Vorgehensweise besteht darin, dass das Compound in der Regel vom Compoundeur zum Spritzgießer transportiert werden muss. Hieraus folgen Arbeitsschritte wie Transport, Lagerung, Wareneingang, interne Logistik und gebenenfalls Trocknung, die sich in den Prozesskosten niederschlagen [1–3].
Im Gegensatz dazu beschreibt der Begriff Direktcompoundierung die Kombination von Aufbereitung (Compoundieren) und Formgebung (Spritzgießen oder Extrudieren) in einem Prozess. Das wiederholte Aufschmelzen und Abkühlen sowie die Granulierung des Compounds entfällt, was auch hinsichtlich der Energiebilanz als Vorteil angesehen werden kann.
Bei diesem Projekt werden bei der Direktextrusion alle notwendigen Aufbereitungsschritte in einem Doppelschneckenextruder durchgeführt und anschließend mit einer Schmelzepumpe der notwendige Druck aufgebaut, um das Material durch das Werkzeug in Form zu bringen. Beim direkten Spritzgießen gibt es zwei Varianten:
- Variante A: Ein Einschneckenextruder wird auf eine konventionelle Spritzgießmaschine adaptiert. Alle Materialkomponenten werden im Extruder gemischt und aufgeschmolzen, danach direkt in den Zylinder der Spritzgießmaschine übergeben und schließlich direkt in das Werkzeug eingespritzt.
- Variante B: Ziel ist die Integration des Compoundierprozesses in den regulären Spritzgießprozess unter Verwendung einer speziell für die Anwendung ausgelegten Schneckengeometrie.
- Das Konzept des Direktcompoundierens führt im Gegensatz zur üblichen Vorgehensweise zu einer drastischen Reduzierung der Arbeitsschritte durch die Integration der Materialaufbereitung/ Compoundierung in den Verarbeitungsprozess, wie Bild 2 zeigt.
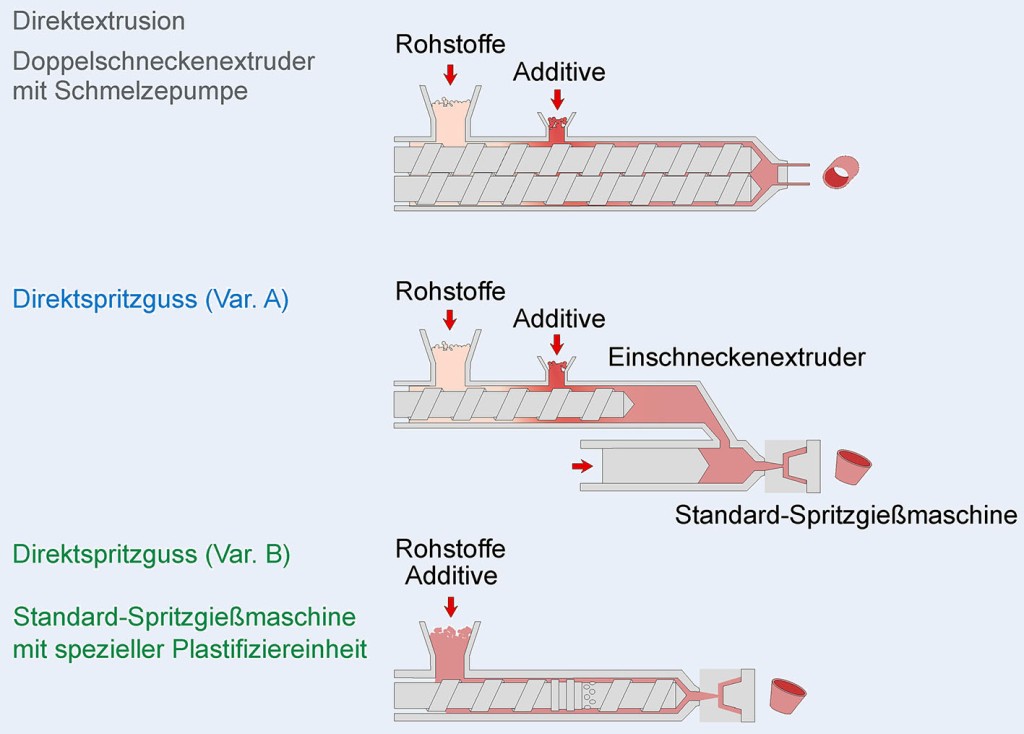
Bild 2. Konzepte des Direktcompoundierens.
Foto: Institut für Werkstofftechnik-Kunststofftechnik, Universität Kassel
3 Projektkonsortium und Aufgaben der einzelnen Projektpartner
3.1 Projektstruktur
Insgesamt sind sechs Projektpartner an dem MeDiComP-Projekt beteiligt: B. Braun Melsungen AG, KraussMaffei Technologies GmbH, Hübner GmbH & Co. KG, Pape GmbH, Zeppelin GmbH und die Universität Kassel. Bild 3 veranschaulicht die Struktur und Rolle der Projektpartner.
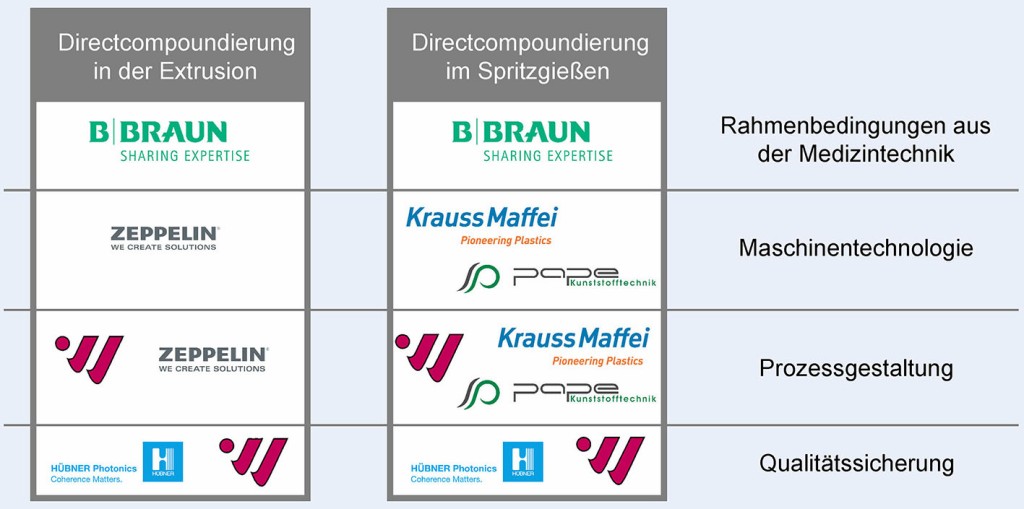
Bild 3. Projektstruktur und Rolle der Projektpartner.
Foto: Institut für Werkstofftechnik-Kunststofftechnik, Universität Kassel
Im Folgenden werden die Aufgaben der einzelnen Partner beschrieben.
3.2 B. Braun Melsungen AG
Die B. Braun Melsungen AG hat sich zum Ziel gesetzt, die neuartigen Verfahren der Direktextrusion und des Direktspritzgießens anhand von Demonstratorprozessen zu erproben und zu optimieren sowie die Voraussetzungen für den Einsatz dieser Verfahren in der Medizintechnik zu schaffen. Eines der Teilziele ist die Anpassung der derzeit eingesetzten Werkstoffe für die Schlauchextrusion in Bezug auf Qualität und Ausstoß durch das Demonstratorverfahren zur Direktextrusion.
3.3 KraussMaffei Technologies GmbH
KraussMaffei entwickelt eine geeignete Maschinentechnik für den Direktspritzguss, und implementiert einen Demonstratorprozess aus dem Bereich der Medizintechnik. Im weiteren Projektverlauf soll die neuartige Maschinentechnik optimiert und ergänzt werden durch die Integration einer Inline-Qualitätsüberwachung zur Messung der Schmelzequalität und deren Einbindung in das Anlagenkonzept. Eine Schmelzequalitätsanalyse, direkt am oder im Prozess, ist ein essenzieller Baustein bei der Qualitätsüberwachung von Direktverfahren und erleichtert nicht nur die im Projekt weiterentwickelten Schneckengeometrien mit optimierter Homogenisierung und Dispergierung zu bewerten, sondern wird im Demonstratorprozess, exemplarisch für eine Produktionsanlage, den Nachweis der Einhaltung der geforderten Mischqualität sowie Dosierkonstanz liefern.
3.4 Hübner GmbH & Co. KG
Die Integration komplexer mehrstufiger Prozessketten bringt viele Vorteile, allerdings gibt es keine zwischengeschalteten Qualitätskontrollen. In der üblichen Prozesskette werden die Kunststoffe zunächst von einem Compoundeur verarbeitet, dann wird das Granulat nach entsprechender Qualitätskontrolle der Weiterverarbeitung zugeführt. Bei einem integrierten Prozess entfällt die Zwischenproduktion von Granulat. Um Informationen über die Qualität des Prozesses zu erhalten, möchte Hübner seine Erfahrungen im Bereich der Laborausrüstung für die Analyse mittels Terahertz (THz)-Spektroskopie auf einen industriellen Inline-Test im laufenden Prozess übertragen. Ziel ist eine Adaption der bisher nur in Analysegeräten eingesetzten THz-Spektroskopie für eine Inline-Messung für die Bewertung der Mischqualität von Kunststoffschmelzen. Anhand von Korrelationen zwischen den THz-Messungen und Materialeigenschaften, wie zum Beispiel spezifische Materialzusammensetzung oder Homogenität, wird ein Qualitätsprüfkonzept entwickelt. Die Validierung des Systems durch Vergleich der Messergebnisse von Inline- und Labormessungen ist grundlegender Bestandteil des Projektes.
3.5 Pape GmbH
Die Firma Pape hat sich zum Ziel gesetzt, die Compoundierprozesse auf einer Standard-Spritzgießmaschine zu realisieren, indem spezielle, neue Einschneckengeometrien, die zum Einmischen von Additiven geeignet sind, ausgelegt, getestet und bewertet werden. Die Idee ist, eine Schnecke zu entwickeln, die eine gute Mischqualität bietet. Dies ist eine besondere Herausforderung, da große Bereiche der ohnehin vergleichsweise kurzen Spritzgießschnecke bereits für Grundfunktionen, wie das Aufschmelzen, genutzt werden müssen. Somit steht nur eine geringe verfahrenstechnisch aktive Länge für Misch- und Homogenisierprozesse zur Verfügung.
3.6 Zeppelin GmbH
Zeppelin hat sich zum Ziel gesetzt, durch die Entwicklung, Konstruktion und das zur Verfügung stellen von Maschinentechnik die Direktextrusion von PVC und TPE mit einem Doppelschneckenextruder zu ermöglichen. Das Ziel bei der Herstellung von PVC-Schläuchen besteht darin, mindestens 80 % der Leistung des derzeitigen konventionellen mehrstufigen Verfahrens und bei TPE-Schläuchen mindestens 40 % eines Teils des PVC-Verfahrens zu erreichen.
3.7 Universität Kassel
Ziel des Instituts für Werkstofftechnik, Fachgebiet Kunststofftechnik der Universität Kassel ist es, Wechselwirkungen von Prozess- und Materialeigenschaften zu analysieren und Potenziale für die Entwicklungsaufgaben aller beteiligten Partner zu identifizieren. Dazu gehört die Untersuchung und Bewertung von Werkstoffen, die Qualifizierung der Terahertz-basierten Inline-Messmethodik sowie die Identifizierung von Grenzwerten hinsichtlich der erreichbaren Materialeigenschaften. Des Weiteren ist die Entwicklung einer allgemeinen Entscheidungsmatrix zur Beurteilung der Anwendbarkeit der betrachteten Direktspritzgieß- und Direktextrusionsverfahren für weitere Produkte aufgrund ihrer Materialzusammensetzung und Bauteilgeometrie Bestandteil des Projekts.
4 Entwicklung von Technologien und Verfahren zur Direktextrusion
4.1 Entwicklung der Direktextrusion von PVC
Die Verarbeitung von PVC auf einem Doppelschneckenextruder wird von der Firma Zeppelin Systems so entwickelt, dass die Maschinentechnik den Anforderungen der Medizintechnik entspricht. Die vorhandene Pilotanlage muss zudem mit einem geeigneten Steuerungskonzept ausgestattet werden. Der integrierte Demonstratorprozess enthält eine Adaption der Doppelschneckenextruderlösung für die Direktcompoundierung der Firma Zeppelin im B. Braun-Technikum und die Konstruktion und Fertigung eines Doppelauslaufteils für die Doppelstrangextrusion mit zwei Schmelzepumpen.
Nach dem Start des Demonstratorprozesses erfolgt die Optimierung hinsichtlich wirtschaftlicher Zielparameter (Ausstoßleistung) und qualitätsrelevanter Eigenschaften (Einschlüsse, nicht aufgeschmolzenes Material), Schlauchabmessungen, Oberflächenrauheit, mechanische Eigenschaften, chemische und mikrobiologische Eigenschaften).
4.2 Entwicklung einer Direktextrusion für TPE
Der mehrstufige Prozess der TPE-Verarbeitung wird auf einem Doppelschneckenextruder realisiert, der die Direktextrusion eines Schlauches ermöglicht. Die für die Aufbereitung erforderlichen Schritte müssen in verschiedene Zonen des Doppelschneckenextruders verlagert werden. Dies erfordert eine Erweiterung der Verfahrenseinheit von konventionellen 32 L / D auf bis zu 52 L / D sowie eine rheologische Weiterentwicklung der Schneckenelemente, der Schneckenkonfiguration, der Rohstoffzuführung und der Dosiertechnik (Art und Zeitpunkt im Prozess).
4.3 Verfahrensentwicklung für das Direktspritzgießen (Variante A)
Der Ansatz der KraussMaffei Technologies GmbH ist, die Kombination einer Spritzgießmaschine mit einem diskontinuierlichen Einschneckenextruder im Start-Stopp-Betrieb zu untersuchen. Mit dieser Technologie können beispielsweise bei der Herstellung von Compounds unerwünschte Einflussfaktoren auf die Materialqualität verringert, der Materialpreis gesenkt und der CO2 Footprint minimiert werden. Die dafür notwendigen speziellen Schneckengeometrien mit optimierten Homogenisier- und Dispergiereigenschaften werden entwickelt, erstellt und erprobt. Die Arbeiten auf diesem Gebiet enthalten weiter die Überprüfung der Übertragbarkeit auf ähnliche Anwendungen und Branchen.
4.4 Entwicklung einer geeigneten Maschinentechnik für das Direktspritzgießen (Variante B)
Die Hauptidee ist die Übertragung der derzeit verwendeten Zweischneckenverfahren auf spritzgießende Einschneckenmaschinen unter Berücksichtigung der allgemeinen verfahrenstechnischen Einschränkungen von Einschneckenmaschinen. Zu diesem Zweck werden verschiedene abschnittsweise geometrische Elemente entwickelt. Anschließend werden die Elemente hinsichtlich ihrer Machbarkeit bewertet: Produktionskosten, Herstellbarkeit, Festigkeit.
In allen Teilprojekten stellt der zweistufige Prozess den Benchmark hinsichtlich Mischqualität und Prozessschwankungen dar. Aus diesem Grund ist die Bewertung der Qualtitätsmerkmale von zentraler Bedeutung. Mithilfe der Mikrotomographie kann insbesondere die Mischgüte von Feststoffen wie Kreidepulver in einer Kunststoffmatrix sehr gut bewertet werden [4]. Darüber hinaus bietet die THz-Technologie die Möglichkeit einer zerstörungsfreien hyperspektralen Bildgebung (sogenannte „THz-Imaging“), welches zur Offline-Analyse der Endprodukte herangezogen werden kann. Die Bild 4 (a und b) zeigen Proben, welche mittels Terahertz-Bildgebung untersucht wurden. Bild 4 a zeigt eine Mischung aus Thermoplastischen Elastomer (TPE), PP und Calcit. Der Probekörper in Bild 4 b enthält die gleichen Komponenten, jedoch ist zusätzlich ein Rußpigment hinzugefügt worden. Die dunkleren Regionen in Bild 4 a repräsentieren Calcitagglomerate, woraus deutlich wird, dass aktuell noch ein Mischproblem vorliegt. Auch die Beimischung des Rußpigments in Bild 4 b ist deutlich erkennbar. Am Institut für Werkstofftechnik der Universität Kassel wurden die gleichen Proben mittels Mikrotomographie untersucht, wobei Bild 4 c die Proben aus Bild 4 a und Bild 4 d die Proben aus 4 b zeigt. Beide Methoden können genutzt werden, um verschiedene Materialkomponenten zu visualisieren, allerdings ist die Technik der Terahertz-Bildgebung bedeutend schneller.
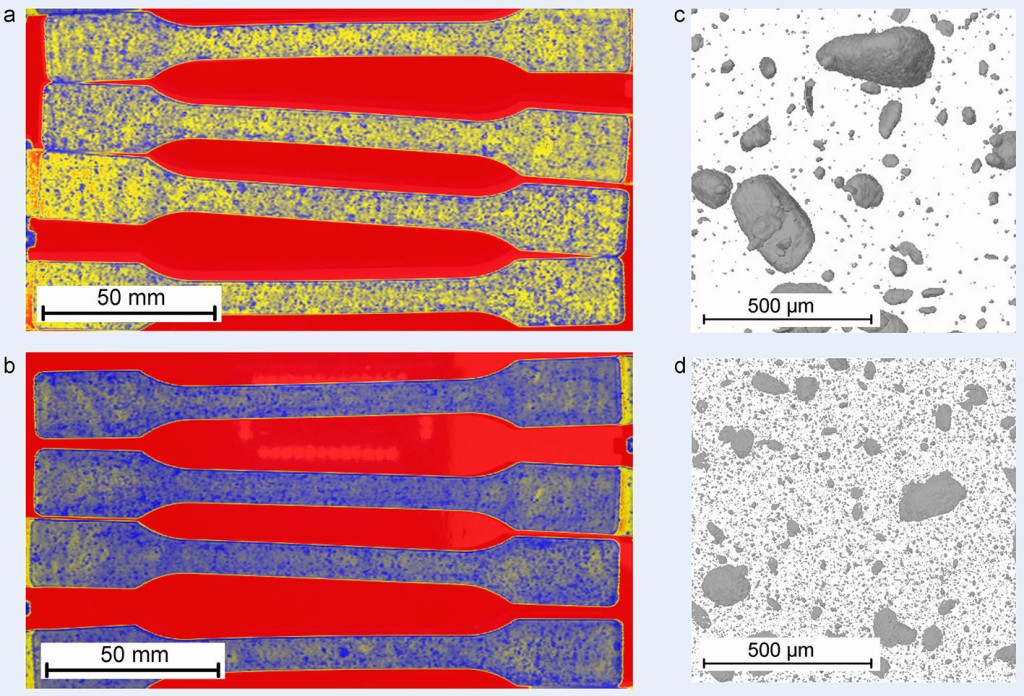
Bild 4. Vergleich von bildgebender Terahertz-Spektroskopie (Hübner GmbH & Co. KG) und Mikrotomographie (Universität Kassel) für dieselben Proben.
Foto: Institut für Werkstofftechnik-Kunststofftechnik, Universität Kassel
Der weitere Forschungsansatz besteht darin, auch mehrphasige Systeme bestehend aus unterschiedlichen Thermoplasten identifizieren und bewerten zu können. Denn hier kommt auch die Mikrotomographie an ihre Grenzen. Mithilfe der THz-Technologie ist es jedoch möglich, über materialspezifische Brechungsindizes Mischgüte zu bewerten.
5 Schlussfolgerung und Ausblick
Die Direktcompoundierung ist ein perspektivisches Feld für Industrie und Wissenschaft. Im Bereich der Automobiltechnik findet sie schon Anwendung, daher wäre eine Übertragung auf die Medizintechnik durchaus denkbar. Diese Technologie kann auch bei bestehenden Anlagen nachgerüstet werden. Im Ausblick sucht die Universität Kassel aus der aktuellen Forschung nach Möglichkeiten der Übertragbarkeit auf andere Materialsysteme (zum Beispiel Systeme auf Basis anderer thermoplastischer Elastomere, Biopolymere), weitere Anwendungen in der Medizintechnik, den Vergleich von Verfahren und die Ableitung ihrer Einsatzgebiete, die Verallgemeinerung der Erkenntnisse, die Durchführung einfacher Simulationen und Experimente als Machbarkeitsstudien und die abschließende Bewertung des Einsatzpotenzials.
Literatur
- Feldmann, M.; Fuchs, J.: 5 – Injection Molding of Bio-Based Plastics, Polymers, and Composites. Specialized Injection Molding Techniques (2016), pp. 211–237
- Zhang, Y.; Sun, L.; Li, L.; Huang, B.; Wang, T.; Wang, Y.: Direct injection molding and mechanical properties of high strength steel/composite hybrids. Composite Structures 210 (2019), pp. 70–81
- Nouri, M.; Semnani, H. M.; Emadoddin, E.; Kim, H. S.: Investigation of direct extrusion channel effects on twist extrusion using experimental and finite element analysis. Measurement 127 (2018), pp. 115–123
- Sälzer, P.; Feldmann, M.; Heim, H.-P.: Wood-Polypropylene Composites: Influence of Processing on the Particle Shape and Size in Correlation with the Mechanical Properties Using Dynamic Image Analysis. International Polymer Processing 33 (2018), pp. 677–687
Das könnte Sie auch interessieren:
Industrieroboter fertigen additiv großvolumige Kunststoffbauteile
Prof. Dr.-Ing. Hans-Peter Heim
Guntis Japins
Michael Hartung
Universität Kassel
Institut für Werkstofftechnik / Kunststofftechnik IFW
Mönchebergstr. 3, 34125 Kassel
Tel. +49 561 / 804-3671
fedler@uni-kassel.de
www.uni-kassel.de/maschinenbau/institute/institut-fuer-werkstofftechnik/fachgebiete/kunststofftechnik/kunststofftechnik.html