Effiziente Fertigung von Leichtbau-Batteriegehäusen
Das Verbundprojekt HyFiVe befasst sich unter anderem mit der Entwicklung seriennaher Fertigungsprozesse für die Herstellung großformatiger Kunststoff-Metall Hybridstrukturen am Beispiel eines Batteriesystemgehäuses. Dabei wird neben der Massereduktion insbesondere das Potenzial zur CO2-Einsparung und die Effizienz und Skalierbarkeit integrierter Fertigungsprozesse aufgezeigt.
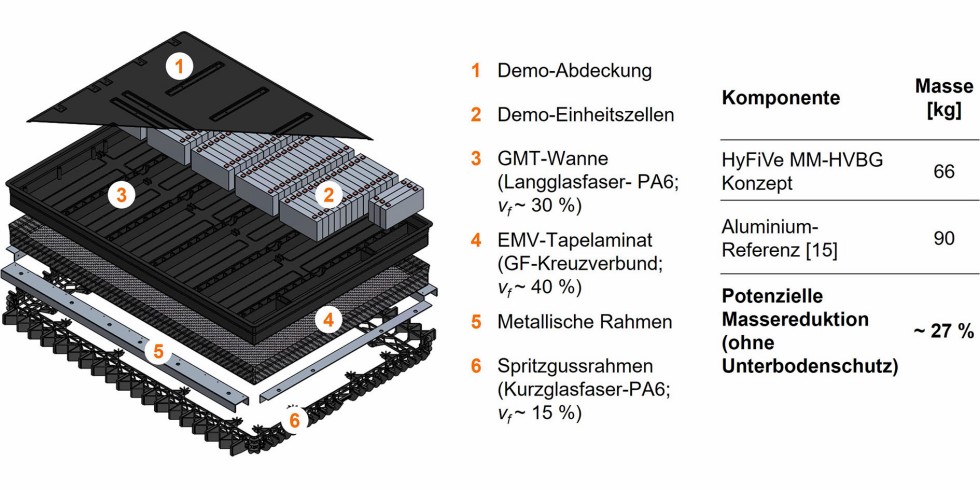
Bild 1. Konzept des Multi-Material Batteriesystemgehäuses. Grafik: TU Braunschweig, IWF
Efficient manufacturing of lightweight battery cases
Abstract: The joint research project HyFiVe focuses, amongst other issues, on the development of close-to-production manufacturing processes for the manufacturing of large-format plastic-metal hybrid structures on the example of a battery system case. In addition to mass reduction, the high potential for CO2-saving and the efficiency and scalability of integrated manufacturing processes are highlighted.
1 Einleitung
Die Transformation der Automobilindustrie hin zur Elektromobilität bringt nicht nur neue Herausforderungen im Bereich der Energiespeichertechnik mit sich. Durch die Integration von Batteriesystemen erhöht sich das Fahrzeuggewicht um mehrere hundert Kilogramm im Vergleich zu Fahrzeugen mit Verbrennungsmotor der gleichen Fahrzeugklasse (zum Beispiel Golf 8 ~1400 kg zu ID.3 ~1800 kg). Hohe bewegte Massen führen im Bereich der E-Mobilität zu geringeren Reichweiten und über Sekundäreffekte zur Notwendigkeit einer widerstandsfähigeren Auslegung weiterer Fahrzeugkomponenten (zum Beispiel Fahrwerk, Bremsen oder Reifen). Auch im Falle eines Crashs steigt bei höherer Fahrzeugmasse die abzubauende kinetische Energie und die Intrusionslast in die Fahrgastzelle. Die Batteriezellen müssen jedoch vor Intrusion geschützt werden, da es sonst zum thermischen Durchgehen des Systems kommen kann. Daher sind die Anforderungen an Crash-Strukturen im Unterbodenbereich stark gestiegen, was oftmals durch einen höheren Materialeinsatz gelöst wird. Angesichts der rasanten Entwicklung von E-Fahrzeugen haben sich daher Lösungen etabliert, die sowohl Leichtbau- als auch Sicherheitsaspekte adressieren. Viele Fahrzeughersteller setzen Aluminium als hauptsächlichen Konstruktionswerkstoff ein [1–3]. Aluminium bietet den Vorteil guter spezifischer mechanischer Eigenschaften und der Verarbeitbarkeit in etablierten Metallverarbeitungs-Prozessketten. Jedoch kann auch mit Aluminium das Leichtbaupotenzial noch nicht ausreichend ausgeschöpft werden. Darüber hinaus ist die Herstellung von Aluminium sehr energieintensiv [4] und umweltschädlich [5, 6]. Mit circa 8,6 kg CO2eq / kg [7] bringt Aluminium ein vergleichsweise hohes materialbezogenes Global Warming Potenzial (GWP) mit sich. Im Vergleich dazu liegen andere Konstruktionswerkstoffe, wie Stahl mit 2–3 kg CO2eq / kg [8] oder technische Kunststoffe beziehungsweise Faserverbundwerkstoffe (basierend auf PA6) mit 2–4 kg CO2eq / kg [9] deutlich niedriger.
Der elektrische Antriebsstrang und insbesondere das Batteriesystem bieten jedoch großes Potenzial, mit alternativen Leichtbauwerkstoffen in einem intelligenten Multi-Material-Mix sowohl den hohen Fahrzeuggewichten entgegenzuwirken, als auch im Vergleich zum CO2-intesiven Aluminium ökologischere Lösungen anbieten zu können. Unter dem Ziel das richtige Material an der richtigen Stelle unter Maximierung der ökologischen Effizienz einzusetzen, sind in den letzten Jahren diverse Konzepte für Multi-Material-Batteriegehäuse in verschiedenen Maßstäben und Reifegraden durch die Forschung und Entwicklung vorgestellt worden [10–13]. Hier wurden viele Aspekte der Eignung von Faserverbunden, Kunststoffen und Multi-Material Lösungen hinsichtlich der Anforderungen in Batteriesystemen (mechanische Eigenschaften, Flammschutz, etc.) thematisiert und geeignete Konzepte identifiziert. Eine wenig adressierte Herausforderung hinsichtlich der Funktion eines kunststoffbasierten Batteriesystemgehäuses (BSG) ist die elektromagnetische Verträglichkeit (EMV).
Darüber hinaus werden die Möglichkeiten zur serienfähigen Produktion solcher Lösungen bisher wenig diskutiert. Die effiziente und serienfähige Herstellung ist jedoch ein entscheidender Punkt für den Transfer der Konzepte in die industrielle Serienproduktion. Insbesondere die Bestrebungen von Fahrzeugherstellern die Fahrzeugplattformen verschiedener Fahrzeugvarianten noch weiter zu vereinheitlichen [14], resultieren in zukünftig weiter steigenden Anforderungen an die Effizienz des Herstellungsprozesses und dessen Skalierbarkeit.
Im Verbundprojekt HyFiVe (FKZ 02P18Q740) wurde daher unter anderem ein Multi-Material Batteriesystemgehäuse (MM-BSG) und ein dazugehöriger, großserienfähiger und skalierbarer Fertigungsprozess entwickelt. Im Folgenden wird zunächst die erarbeitete Systemlösung inkl. des virtuellen Funktionsnachweises vorgestellt, bevor die Fertigungsprozesskette und die Werkzeugtechnik näher erläutert werden. Der Beitrag schließt mit einer Bewertung der entwickelten Lösung und des Transferpotenzials.
2 Design und Auslegung des Batteriesystemgehäuses
Die Umsetzung einer Multi-Material Leichtbaulösung für BSG kann durch verschiedene Designs und Materialien erfolgen. Wie zuvor beschrieben, gibt es hier sowohl im industriellen als auch im Forschungskontext diverse Ansätze. Die allgemeine Motivation ist es, Gewicht zu reduzieren, die Nachhaltigkeit zu steigern, und Kosten einzusparen. Aus technischer Sicht müssen Sicherheits- (zum Beispiel Crash, Brandsicherheit) und Funktionsanforderungen (zum Beispiel Dichtigkeit, EMV-Schutz) erfüllt werden. In Bezug auf das Gesamtfahrzeugsystem ist es darüber hinaus erstrebenswert eine hohe Energiedichte zu erzielen. Zukünftige Batteriesystementwicklungen müssen diese und weitere gesetzliche Anforderungen berücksichtigen.
Auf Basis dessen wurde im Projekt HyFiVe ein Konzept für ein MM-BSG mit funktionsintegrierten Materialien sowie der dazugehörige Fertigungsprozess entwickelt. Das Konzept besteht aus vier Einzelkomponenten, die in einem integrierten Fertigungsverfahren hergestellt werden (vgl. Kapitel 3). In Bild 1 sind die Einzelkomponenten in einer Explosionsdarstellung illustriert. Die Hauptstruktur bildet eine „Wanne“ (3) aus einem glasmattenverstärkten Thermoplast (GMT). Dieses kann als vorimprägniertes Material bezogen und durch Pressverfahren formgegeben werden. Diese Innenstruktur wird von einem Tape-Laminat (4) umgeben dessen Einzellagen in einem robotergeführten Tapelegeverfahren zu dreidimensionalen Preforms in einem symmetrischen Kreuzverbund [0/90]S aufgebaut werden. Die Rahmenstruktur des Systems besteht aus einer Kombination von Aluminium-Profilen (5) mit einer hinterspritzten Rippenstruktur (6), wodurch sowohl Verstärkungsstrukturen als auch Funktionselemente abgeformt werden.
Während die meisten der verwendeten Materialien kommerziell am Markt erhältlich sind, ist das EMV-Tapelaminat eigens im Projekt entwickelt worden. Hierdurch wird ein alternativer Ansatz geboten, in kunststoffintensiven Batteriesystemgehäusen die EMV-Schutzwirkung sicherzustellen.
Unerwünschte Kopplungen zwischen den elektrischen Modulen durch elektromagnetische Wellen müssen zwingend vermieden werden. Da sowohl Kunststoffe, als auch Glasfasern dielektrisch sind, können Störsignale ungeschwächt passieren. Hierdurch können Streufelder von den einzelnen elektrischen Komponenten ausgehen und diese wiederum Störungen in benachbarten Schaltungsteilen bis hin zu signifikanten Ausfällen der Elektronik erzeugen.
Die geforderte Schutzwirkung wird im Projekt durch ein metallbedampftes Polymergewebe realisiert, welches mittels einer thermoplastischen Haftvermittlerfolie an ein konventionelles UD-Tape gefügt wird. Als schirmungstechnisches Auslegungskriterium dient das in der Automobilindustrie etablierte 70/40 Kriterium. Dies beschreibt eine linearabnehmende Mindestdämpfung von 70 dB bei einer Frequenz von 150 kHz hin zu 40 dB bei 120 MHz. Durch die Integration der Funktionsschicht in das Tape-Halbzeug kann ein kostengünstiger EMV-Schutz bereitgestellt werden, ohne die Fertigungsprozesskette zu verlängern, oder übermäßig viel Material durch bspw. vollflächige metallische Abschirmungen einsetzen zu müssen.
Hierdurch verändert sich im Tape-Halbzeug jedoch der Faservolumengehalt, was sich wiederum auf die mechanischen Eigenschaften auswirkt. In Zugversuchen konnte eine Reduktion der Zugfestigkeit auf circa 400 MPa gegenüber 720 MPa am nicht modifizierten Tape festgestellt werden. Dies ist hinsichtlich der Auslegung mit dem funktionalisierten Halbzeug zu beachten. Darüber hinaus wurden Schälversuche durchgeführt, wobei die hier gemessene Festigkeit einen Richtwert für die Widerstandsfähigkeit gegen Delamination des Tapes von den Funktionslagen angibt. Dies ist wiederum hinsichtlich der Strukturfestigkeit und Lebensdaueranforderungen relevant. In Bild 2 sind die ermittelten Schälfestigkeiten für die untersuchten Kombinationen von glasfasergelegeverstärkten PA6-Tapes mit metallbedampften Funktionsschichten dargestellt. Die Ergebnisse zeigen einen großen Einfluss der metallischen Beschichtung. Auf Basis der Messungen wurde ein EMV-Schirm aus Ripstop Gewebe mit reiner Silberbeschichtung ausgewählt, wobei die Wahl des Trägermaterials auch hinsichtlich der notwendigen Umformfestigkeit im nachgelagerten Pressprozess getroffen wurde.
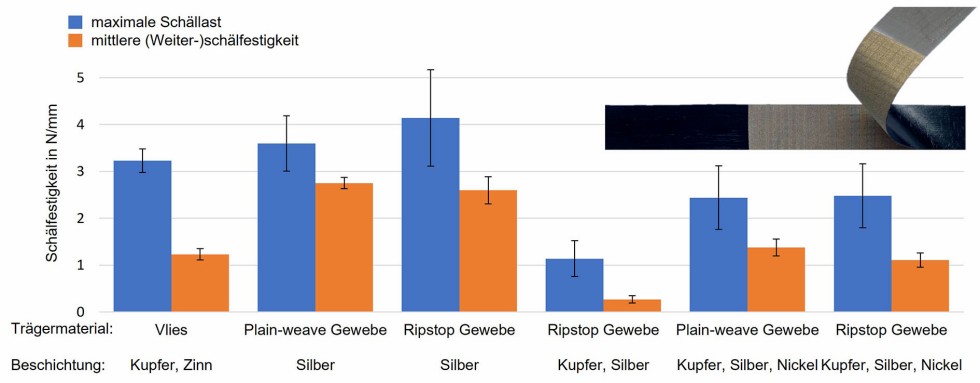
Bild 2. Erreichbare Schälfestigkeit funktionalisierter Tapes mit unterschiedlichen Trägermaterialien und Beschichtungen der EMV-Schutzschicht. Grafik: Hochschule Bielefeld, BifAM
Alle weiteren für die virtuelle Auslegung des Systems relevanten Materialdaten der verschiedenen Systemkomponenten (vgl. Bild 1) wurden aus den Datenblättern der Hersteller entnommen und anschließend in die FE-Modelle für die virtuelle Auslegung des Gesamtsystems überführt.
2.1 Virtuelle Absicherung
Schon in der Konstruktion wurde durch ein „simulation driven design“ eine geeignete Gestalt des Systemgehäuses durch richtungsweisende Simulationen identifiziert. Im Rahmen des Projekts werden die nach industriellen Standards bekannten Lastfälle (crash, crush, shock und bottom impact) sowie Modalanalysen des Systems durch Simulationen abgesichert.
Insbesondere der Seitenaufprall [16] stellt als Lastfall aufgrund des sehr lokalen und hohen Energieeintrags die höchsten mechanischen Anforderungen an die Struktur. Hierzu wurden die Schnittenergien aus einer Gesamtfahrzeugsimulation extrahiert und das System mit einem Sicherheitsfaktor von 1,5 für den Seitenaufprall konservativ ausgelegt. Das Zielkriterium war, dass bei der Pfahlintrusion die Zellen nicht berührt werden. In Bild 3 a) ist zu erkennen, dass der Energieeintrag aufgrund des relativ zur Gesamtlänge des Systems schmalen Pfahlkörpers sehr lokal erfolgt.
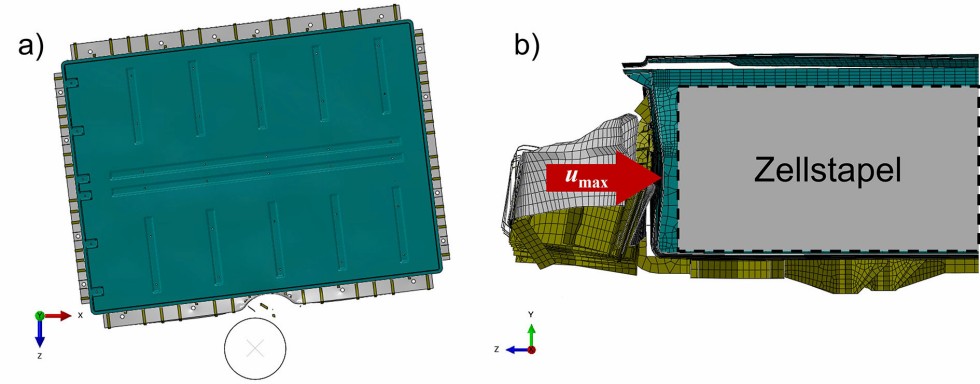
Bild 3. a) Ergebnis der Crash-Simulation (Seitenaufprall mit 32 km/h; SF 1,5) und b) Schnittansicht an der Position mit maximaler Intrusion umax. Grafik: TU Braunschweig, IWF
Da ein Pfahlaufprall prinzipiell über die gesamte Länge des Systems auftreten kann, bedingt dies ein lokal redundantes Strukturdesign. In dieser Lösung wird daher ein Aluminium U-Profil mit einer hinterspritzten, sich wiederholenden, Rippenstruktur kombiniert. Das Aluminiumprofil dient neben der Energieabsorption im Crash durch plastische Deformation der einfachen Montagefähigkeit des Gehäuses an den Fahrzeugunterboden. Die Rippenstruktur ist so ausgelegt, dass hier insbesondere Energie durch die Zerstörung (Freisetzung von Bruchenergie) absorbiert wird.
Neben den kritischen Lastfällen ist insbesondere die Absicherung der Herstellbarkeit der erarbeiteten Designvarianten durch begleitende Prozesssimulationen notwendig. Da im vorliegenden Konzept eine Prozesskombination in einem integrierten Fertigungsschritt vorgesehen wird (vgl. Kapitel 3), müssen die Einzelprozessschritte sowohl in sich, als auch unter gegenseitiger Beeinflussung der Prozessgrößen, evaluiert werden. Hierdurch können die Verfahren des Fließpressens und Spritzgießens bereits in der Prozessauslegungsphase optimiert werden, um die Bauteilqualität zu erhöhen und die Anzahl experimenteller Trial-and-Error-Versuche zu reduzieren. Neben dem Materialfluss im Werkzeug können dabei auch Druck- und Temperaturverteilungen ausgewertet und somit Werkzeugbelastungen abgeschätzt werden. Dazu wurden mithilfe der kommerziellen Software Autodesk „Moldflow“ numerische Simulationen durchgeführt. Beim Fließpressen lag der Fokus darauf, eine vollständige Formfüllung in möglichst kurzer Zeit bei einer homogenen Druck- und Temperaturverteilung zu gewährleisten.
Das Ergebnis des Fließpressens ist von zahlreichen Einflussfaktoren abhängig, wie beispielsweise der eingelegten Menge und Verteilung der GMT-Zuschnitte sowie den Prozessparametern Temperatur, Presskraft und -geschwindigkeit. Die Eingangsparameter wurden aus den Randbedingungen der Fertigungsanlage und der geplanten Prozessführung (vgl. Bild 5) abgeleitet. Zum Start des Pressvorgangs wurde für die GMT-Zuschnitte eine Temperatur von 260 °C angenommen. Die maximale Presskraft und -geschwindigkeit wurden unter Berücksichtigung der Maschinenrestriktionen mit 3600 t und 20 mm/s festgelegt. Zur Ermittlung eines optimalen Zuschnittes wurde die initiale Menge und Verteilung der GMT-Masse variiert und die Auswirkung auf die Formfüllung und den Werkzeuginnendruck ausgewertet (Bild 4).
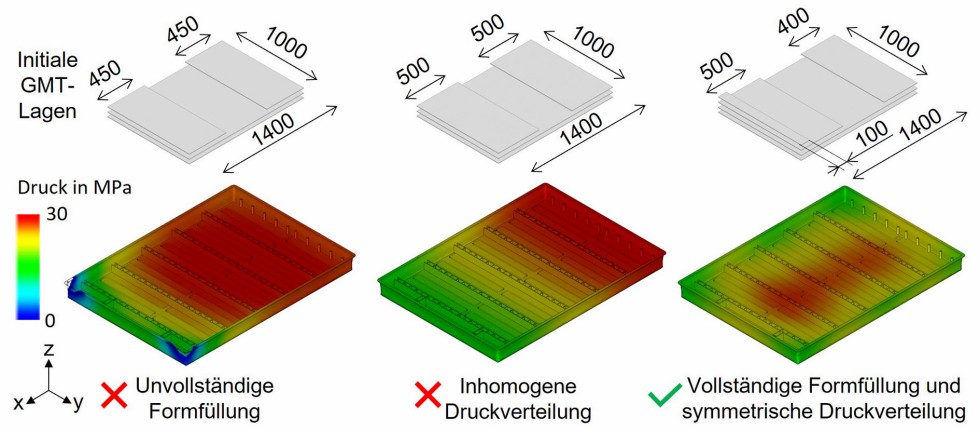
Bild 4. Numerisch ermittelte Verteilung des GMT für eine optimierte Formfüllung. Grafik LU Hannover, IFUM
Der dem Fließpressen nachgelagerte Spritzgießprozess beginnt, sobald die Zuhaltekraft (entspricht der finalen Press- und Haltekraft des Fließpressvorgangs) durch die Schließung der Werkzeughälften aufgebaut wurde. Mithilfe einer Spritzgießsimulation kann dann ein zielführender Prozessparameterraum eingegrenzt werden, der zu einem qualitativ hochwertigen Fertigungsergebnis führen kann. Darüber hinaus liefern die Simulationsergebnisse wichtige Erkenntnisse zur Bauteilfüllung, der resultierenden Maßhaltigkeit oder auch potenziellen Fehlstellen, woraufhin die Auslegung des Fertigungswerkzeugs optimiert werden kann. Hieraus resultieren auf lange Sicht geringere Produktionskosten und eine höhere Bauteilqualität.
3 Fertigungsprozess und Werkzeugtechnik
Der anvisierte Fertigungsprozess zur Herstellung der MM-BSG basiert auf dem Ansatz sogenannter „one-shot“-Prozesse, welche im Kontext der Herstellung von Leichtbaustrukturen insbesondere synonym für Hinterspritzprozesse verwendet wird, bei denen in einem Fertigungsschritt mehrere Teilschritte (zum Beispiel Umformung und Umspritzung) integriert werden. Im Allgemeinen bieten diese Prozesse einen konkurrierenden Ansatz zu Füge- und Montagereihenfolgen von komplexen Baugruppen, wobei sie sich insbesondere hinsichtlich der Anzahl von Einzelteilen und der notwendigen Prozessschritte unterscheiden.
Der hier vorgestellte Fertigungsprozess enthält im Gegensatz zu bekannten „one-shot“-Prozessbeispielen eine deutlich erhöhte Komplexität. Neben metallischen Einlegeteilen müssen lang- und endlosfaserverstärkte Halbzeuge im erwärmten, biegeschlaffen Zustand prozesssicher verarbeitet werden. Darüber hinaus wird durch die Schließbewegung des Formwerkzeugs mittels Prägefunktion der Spritzgießanlage der Pressprozess für das GMT-Material realisiert. Schlussendlich erfolgt die Hinterspritzung mit Versteifungs- und Funktionselementen. Die Prozesskette mit den zeitlichen Anteilen des jeweiligen Prozessschritts an der Gesamtzykluszeit ist exemplarisch in Bild 5 dargestellt.
Diese Prozessgestaltung stellt besondere Anforderungen an die Gestaltung und Ausführung des Formwerkzeugs, woraus sich besondere Spezifikationen ableiten.
In der Unterhälfte des Werkzeugs werden die Metalleinleger positioniert und mittels vier hydraulisch betriebenen Backenschiebern geklemmt, sodass die Kavität hinsichtlich der eingespritzten Kunststoffmasse abgedichtet wird und hinterschnittige Umspritzungen realisiert werden können. Danach wird das bereits vorgeformte (preform) und vorgewärmte Tape-Laminat zusammen mit der Fließpressmasse auf voreilenden Segmenten abgelegt, welche einerseits der minimalen Wärmeabfuhr der vorgeheizten Halbzeuge dienen und zusätzlich die Entformung des fertigen Bauteils unterstützen. Anschließend wird das Formwerkzeug geschlossen und mithilfe der Prägefunktion der Spritzgießanlage ein hoher Pressdruck ausgeübt, sodass sich die eingelegte Fließpressmasse in der Kavität, welche durch Tauchkanten, die sich in den Backenschiebern befinden, abgedichtet wird, verteilt. Das bereits aus Tapes, Fließpressmasse und Metallprofilen bestehende Teil wird im Anschluss im selben Werkzeug mit der Spritzgießmasse funktionalisiert und verbunden. Zur Entformung gibt es ein beidseitiges Auswerferpaket, sodass die Fließpressmasse mit den tiefen Rippen im Oberteil und die Spritzgießstruktur im Unterteil entformt werden kann. Durch eine konturnahe Werkzeugtemperierung werden die Kunststoffmassen auf die Entformtemperatur heruntergekühlt, sodass schlussendlich das fertige Bauteil entnommen werden kann. Das Gesamtwerkzeug ist exemplarisch in Bild 6 dargestellt.
4 Potenzialbewertung und Technologietransfer
Multi-Material-Bauweisen bieten viele Vorteile, insbesondere in einer effizienten Materialausnutzung und einer integrierten Fertigungstechnik zur Reduktion von Prozessschritten, Bauteilanzahl und Füge- beziehungsweise Montageoperationen. Das im Rahmen des Projekts aufgezeigte Potenzial für ein MM-BSG liegt einerseits in der potenziellen Massereduktion von circa 30 % und weiterhin in der Reduktion des bauteilbezogenen GWP um circa 70 % im Vergleich zum Referenzbauteil aus Primäraluminium. Der entwickelte Fertigungsprozess eignet sich mit einer Zykluszeit von unter 2 min für eine Großserienproduktion. Aufgrund der prototypischen Umsetzung der Prozesskette im Rahmen des Projekts, können Hemmnisse zum Transfer in die industrielle Anwendung weiter abgebaut werden. Auch Materialsubstitutionen oder das Hinzufügen beziehungsweise Entfernen von Einlegeteilen, zum Beispiel bei der Herstellung anderer Systemvarianten, können mit diesem Fertigungskonzept einfach umgesetzt werden. Entscheidend für einen erfolgreichen Industrietransfer ist, dass unterschiedliche Fachbereiche bereits in frühen Entwicklungsphasen intensiv zusammenarbeiten, um die Abstimmung zwischen Design, Materialien, Auslegung, Werkzeug- und Prozesstechnik zu optimieren.
Kritisch hinterfragt werden müssen Multi-Material-Bauweisen hinsichtlich ihres Wiederverwertungspotenzials am End-of-Life. Hierzu zählen jedoch nicht nur Metall-Kunststoff-Verbindungen oder Faserverbundwerkstoffe, sondern auch Multi-Alloy Bauweisen, wie sie in am Markt befindlichen Aluminiumgehäusen eingesetzt werden. Um ein tatsächlich hochwertiges Recycling zu gewährleisten, müssen die verschiedenen Materialien und Legierungen sortenrein voneinander getrennt werden. Dies ist eine wichtige Basis für eine umweltfreundliche Umsetzung von Multi-Material-Bauweisen und wird in aktuellen Forschungsprojekten, wie beispielsweise „Zirkel“ (FKZ 02J21E040) adressiert.
Das Forschungsprojekt „HyFiVe“ (Förderkennzeichen 02P18Q740) wird durch das Bundesministerium für Bildung und Forschung (BMBF) in der Fördermaßnahme „Forschungscampus – öffentlich-private Partnerschaft für Innovationen“ gefördert und vom Projektträger Karlsruhe (PTKA) betreut. Die Verantwortung für den Inhalt dieser Veröffentlichung liegt bei den Autoren.
Literatur
- E-Enginge: VW: so funktioniert die Batterie der MEB-Plattform. Stand: 2019. Internet: https://e-engine.de/vw-so-funktioniert-die-batterie-der-meb-plattform/. Zugriff am 19.03.2022
- Mercedes Benz Group AG: Die Batterie im Fokus der Kreislaufwirtschaft. Stand: 2023. Internet: https://group.mercedes-benz.com/nachhaltigkeit/ressourcen/batterie.html. Zugriff am 11.07.2023
- BMW AG Pressemitteilung: BMW Group etabliert geschlossenen Recycling-Kreislauf für Hochvoltbatterien in China. Stand: 2023. Internet: https://www.press.bmwgroup.com/deutschland/article/detail/T0393733DE/bmw-group-etabliert-geschlossenen-recycling-kreislauf-fuer-hochvoltbatterien-in-china?language=de. Zugriff am 11.07.2023
- Institut für seltene Erden und Metalle AG: Aluminium Preise, Vorkommen, Gewinnung und Verwendung. Stand: 2023. Internet: https://institut-seltene-erden.de/seltene-erden-und-metalle/basismetalle/aluminium/. Zugriff am 11.07.2023
- Umweltbundesamt GmbH: Prüfbericht Nr. 1010/431 „Bestimmung von Arsen, Quecksilber und Chrom (gesamt) in Rotschlamm“. 2010
- Umweltbundesamt GmbH: Prüfbericht Nr. 1010/441 „Schwermetallscreening und Bestimmung von Cr(VI) in Rotschlamm“. 2010
- European Aluminium: Environmental Profile Report – Life-Cycle inventory data for aluminium production and transformation processes in Europe. 2010
- World Steel Association: Life cycle inventory (LCI) Study Report. 2020.
- LANXESS: Zertifizierter CO2-Fußabdruck für Polyamid 6, PBT und Glasfasern, Pressemitteilung 09/2022. Internet: https://lanxess.com/de-DE/Presse/Presseinformationen/2022/09/LANXESS-Zertifizierter-CO2-Fussabdruck-fuer-Polyamid-6-PBT-und-Glasfasern. Zugriff am 13.03.2023
- Kautex Textron GmbH & Co. KG: Batteriesysteme. Stand: 2023. Internet: https://www.kautex.com/de/automotive/batteriesysteme. Zugriff am 11.07.2023
- TEIJIN: Automotive. Stand: 2023. Internet: https://teijinautomotive.com/expertise/automotive/. Zugriff am 11.07.2023.
- SABIC: SABIC Advances Thermoplastic Solutions for Critical EV Battery Technologies. Stand 2021. Internet: https://www.sabic.com/en/news/29554-sabic-advances-thermoplastic-solutions-for-critical-ev-battery-technologies. Zugriff am 11.07.2023
- AZL Aachen GmbH: EV Battery Casings Consultancy. Stand: 2023. Internet: https://azl-aachen-gmbh.de/de/battery-casing-products-and-services/. Zugriff am 17.07.2023
- Henßler, S.: VWs neue „elektrische Superplattform“ SSP als Basis für mehr als 40 Millionen Fahrzeuge. Stand: 2021. Internet: https://www.elektroauto-news.net/2021/vw-elektrische-superplattform-ssp-basis-40-millionen-fahrzeuge. Zugriff am 24.03.2022
- AZL Aachen GmbH: Concept Study & Development of a Multi-material Battery Casing. Projektinformation 2020.
- Euro NCAP: Side Pole. Stand: 2023. Internet: https://www.euroncap.com/en/vehicle-safety/the-ratings-explained/adult-occupant-protection/lateral-impact/side-pole/. Zugriff am 11.07.2023
Dipl.-Ing. Tim Ossowski
Prof. Dr.-Ing. Klaus Dröder
Technische Universität Braunschweig
Institut für Werkzeugmaschinen und Fertigungstechnik IWF
Langer Kamp 19b, 38106 Braunschweig
Tel. +49 172 / 3409582
t.ossowski@tu-braunschweig.de
www.tu-braunschweig.de/iwf
Philipp Althaus
Prof. Dr.-Ing. Bernd-Arno Behrens
Leibniz Universität Hannover
Institut für Umformtechnik und Umformmaschinen, IFUM
An der Universität 2, 30823 Garbsen
Tel. +49 511 / 7623825
althaus@ifum.uni-hannover.de
www.ifum.uni-hannover.de/de
Dipl.-Ing. Tristan Elsesser
Prof. Dr.-Ing. Angela Ries
Hochschule Bielefeld
Bielefelder Institut für Angewandte Materialforschung, BifAM
Interaktion 1, 33619 Bielefeld
Tel. +49 521 / 106-70390
tristan.elsesser@hsbi.de
www.hsbi.de/bifam
Daniel Maier
Siebenwurst GmbH & Co. KG
Industriestr. 31, 92345 Dietfurt
Tel. +49 8464 650-594
d.maier@siebenwusrt.de
www.siebenwurst.com