Einzelzahnspulen für leistungsstarke Motoren
Zunehmend steigende Anforderungen an die Effizienz und Leistung elektrischer Maschinen für den Einsatz in Fahrzeugen machen neue Herstellungsverfahren für Statorwicklungen notwendig. Daher wurde in Zusammenarbeit mit der RWTH Aachen University sowie den beiden Firmen Schaeffler und Breuckmann ein serientaugliches Herstellungsverfahren entwickelt, mit dem querschnittsvariable Einzelzahnspulen für den Einsatz in elektrischen Motoren mit hoher Drehmomentdichte hergestellt werden können.
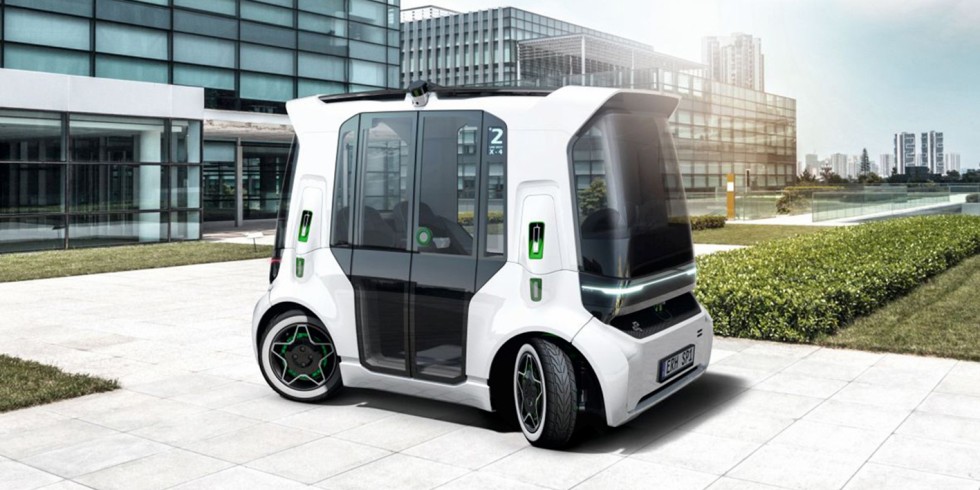
Bild 7. Schaeffler-Mover. Grafik: Schaeffler Technologies AG & Co. KG
Ausgabe 10-2021, S. 718
1 Motivation und Stand der Technik
Zunehmend steigende Anforderungen an die Effizienz und Leistung elektrischer Maschinen für den Einsatz in Fahrzeugen führen zu der Notwendigkeit, neue Herstellungsverfahren für Statorwicklungen zu entwickeln und zu optimieren. Das Ziel ist, die Lücke zwischen den Prozessgrenzen bei der herstellbaren Wicklungsgeometrie und der in Anbetracht der elektromagnetischen Performance optimalen Wicklungsgeometrie zu schließen.
Ein Weg, die Effizienz einer elektrischen Maschine zu steigern, ist, den elektrischen Nutfüllfaktor zu erhöhen. Dabei wird der Herstellungsprozess der Statorwicklung so ausgelegt, dass beim Zusammenbau die Statornut optimal mit elektrisch leitfähigem Material ausgenutzt wird. Wie der elektrische Nutfüllfaktor erhöht wird, ist abhängig von der Statorwicklungstopologie. Prinzipiell werden verteilte und konzentrierte Statorwicklungen unterschieden, die sich im Wesentlichen durch den Fertigungsprozess, die Größe des Wickelkopfes und die Geräuschentwicklung beim Betrieb der elektrischen Maschine unterscheiden [1].
Im Falle verteilter Wicklungen kann der elektrische Nutfüllfaktor durch die Verwendung von Hairpins zum Aufbau der Statorwicklung erhöht werden. Dabei wird massiver Rechteckdraht, dessen Abmessungen optimal in die Statornut passen, zu haarnadelförmigen Leitern gebogen, in den Stator gesteckt und dann zu einer Wicklung verschweißt [2]. Andere Konzepte zur Herstellung verteilter Wicklungen versuchen den bei Runddrahtwicklungen vorhandenen Nachteil der schlechten Ausnutzung der Statornut zu beseitigen, indem nach der Herstellung der Wicklung mittels herkömmlicher Wickelverfahren ein weiterer umformtechnischer Prozessschritt genutzt wird, um die Wicklung kompakter zu gestalten. Beim sogenannten Kompaktwickelverfahren werden lose Luftspulen mit Linearwickeln hergestellt, anschließend in einem Kompaktierschritt verpresst und während der Statormontage radial in die Statornut als verteilte Wicklung eingeschoben [3].
Neben dem elektrischen Nutfüllfaktor ist bei manchen Anwendungsfällen auch der zur Verfügung stehende Motorbauraum ein entscheidendes Kriterium für die Auslegung und Herstellung der Statorwicklung. Ein Beispiel für eine Anwendung mit hoher Bauraumbeschränkung ist der elektrische Radnabenmotor, dessen Bauraum in radialer Richtung durch den Felgendurchmesser und in axiale Richtung durch die Felgenbreite limitiert ist. Daher ist für eine gute Performance des elektrischen Motors ein hoher elektrischer Füllfaktor bei gleichzeitig kleinem Wickelkopf der Statorwicklung erforderlich [4]. Konzentrierte Wicklungen sind für diese Anwendung besser geeignet, da sie einen kleineren Wickelkopf aufweisen als verteilte Wicklungen [5]. Um die Effizienz des Radnabenmotors weiter zu erhöhen, sollten die Statorzähne parallelflankig ausgelegt sein. Dies führt zu einer gleichmäßigeren magnetischen Ausnutzung des Statoreisens und es steht mehr Platz für elektrisch leitfähiges Material in der Statornut zur Verfügung [6]. Die zuvor genannten Anforderungen an den Stator eines elektrischen Radnabenmotors können durch querschnittsvariable Einzelzahnspulen, deren Geometrie in Bild 1 gezeigt ist, erfüllt werden.
![Bild 1. Geometrie querschnittsvariabler Einzelzahnspulen [6]. Grafik: IBF der RWTH Aachen University](https://www.ingenieur.de/wp-content/uploads/2021/11/WBK_BMBF_FlexiCoil_Bild_1.jpg)
Bild 1. Geometrie querschnittsvariabler Einzelzahnspulen [6]. Grafik: IBF der RWTH Aachen University
Aufgrund des massiven Leiterquerschnitts der querschnittsvariablen Einzelzahnspulen ist die Effizienz des mit ihnen bestückten Motors im unteren Drehzahlbereich am größten, da bei höheren Drehzahlen die Kupferverluste aufgrund von Skin- und Proximity-Effekten ansteigen [6].
Die Spulengeometrie in Bild 1 ist mittels Gießtechnologie herstellbar [7]. Aufgrund der hohen Energiekosten und des großen Werkzeugverschleiß ist ein umformtechnisch wirtschaftliches Herstellungsverfahren wünschenswert, um auch größere Stückzahlszenarien zu erschließen. Verschiedene Ansätze für ein Umformverfahren zur Herstellung querschnittsvariabler Einzelzahnspulen werden aktuell erforscht [8, 9].
Dieser Beitrag beschreibt einen serientauglichen, umformtechnischen Ansatz, mit dem durch CNC (Computerized Numerical Control)-Biegen und einen mehrstufigen Umformprozess querschnittsvariable Einzelzahnspulen hergestellt werden können. Zudem wird das Potenzial dieser Spulengeometrie beispielhaft beim Einsatz in einem elektrischen Radnabenmotor der Firma Schaeffler dargestellt.
2 Querschnittsvariable Einzelzahnspulen durch mehrstufigen Umformprozess
Zur Herstellung querschnittsvariabler Einzelzahnspulen sind mehrere Umformverfahren denkbar. Ein mehrstufiger Umformprozess, der einen mittels CNC-Biegen hergestellten Spulenrohling auf die gewünschte Endgeometrie formt, ist der beste Kompromiss aus Wirtschaftlichkeit und Anforderungen an die geometrische Gestalt der Spule [9]. Die Herstellung des für den mehrstufigen Umformprozess benötigten Spulenrohlings ist in Bild 2 gezeigt. Profildraht mit einer an die Endgeometrie der Spule angepassten Querschnittsform wird entlang einer Achse entsprechend der Spulenlänge und Spulenbreite vorgeschoben und mit einem rotierenden Formwerkzeug um einen Biegedorn zu einer Einzelzahnspule mit konstanter Drahtquerschnittsform gebogen.
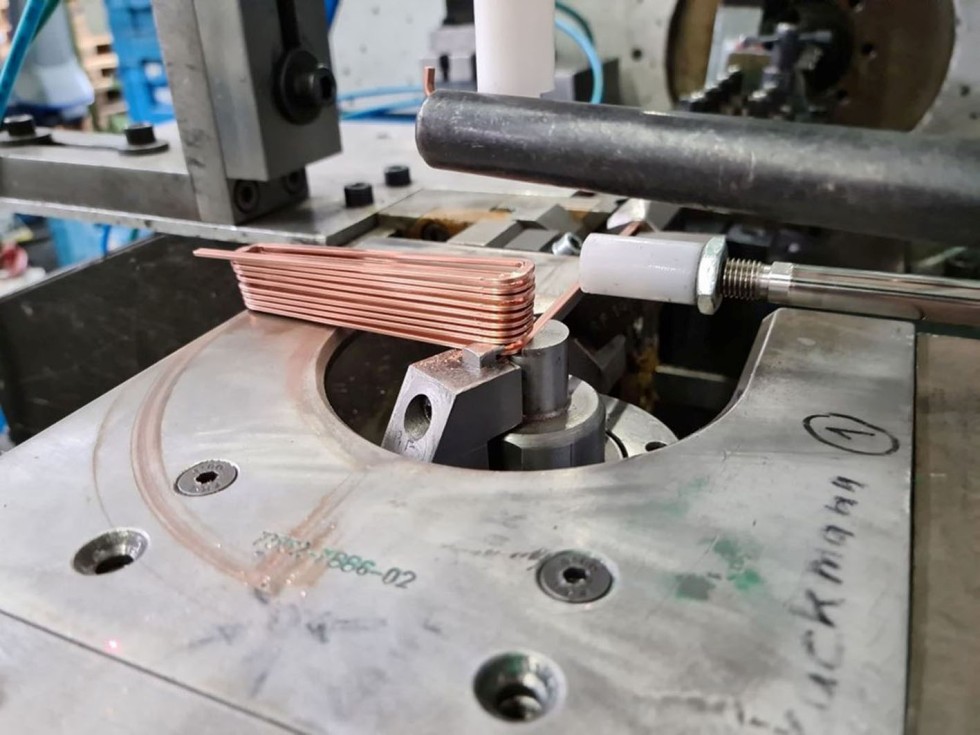
Bild 2. CNC (Computerized Numerical Control)-Biegen des Spulenrohlings.
Foto: Johann Vitz GmbH & Co. KG
Beim anschließenden mehrstufigen Umformprozess wird die Einzelzahnspule in einem Umformspalt zwischen einem Kern und einem Container gestaucht. In Bild 3 ist ein Auszug des formgebenden Teils des bei der Firma Breuckmann industriell eingesetzten mehrstufigen Umformwerkzeugs zu sehen. Durch den Kern wird die innere Form der Spule vorgegeben, während durch Stempel, Matrize und die Formwände die äußere Formgebung umgesetzt wird.
Die Spule wird im Umformspalt zwischen Formwänden und Kern durch den vertikal beweglichen Stempel in mehreren Umformstufen gestaucht. Außenliegende Schiebereinheiten sorgen dafür, dass während der Umformung auftretende Horizontalkräfte kompensiert werden und stabilisieren somit die Position der Formwände. Unter Beibehaltung eines hohen Formzwangs wird der Umformspalt durch das Austauschen von Container und Stempel in diskreten Stufen an die Endgeometrie der Spule angepasst [10]. Dazu kann ein Linearschlittensystem genutzt werden, womit nach jeder Umformstufe der alte Stempel sowie die alten Formwände entfernt und neue Komponenten in das Werkzeug eingeführt werden können. Bei einer benötigten Anzahl von fünf Umformstufen können durch diesen effizienten Wechsel der Werkzeugkomponenten umgeformte Einzelzahnspulen ausgehend vom Spulenrohling mit einer geringen Taktzeit von knapp über 30 Sekunden hergestellt werden [6].
Mit der hier beschriebenen Umformtechnologie wurden querschnittsvariable Einzelzahnspulen hergestellt und deren Potenzial hinsichtlich der Maschineneffizienz im unteren Drehzahlbereich an einem Radnabenantrieb der Firma Schaeffler auf einem Prüfstand am Institut für Elektrische Maschinen der RWTH Aachen University, IEM, gemessen [6]. Die wesentlichsten Ergebnisse dieser Messung sind in Abschnitt 4 zusammengefasst. Die Ausnutzung der Statornut mit umgeformten Einzelzahnspulen zeigt Bild 4. Gut zu erkennen ist die über die Spulenhöhe variable Querschnittsform und der verglichen mit herkömmlichen Runddrahtwicklungen hohe elektrische Nutfüllfaktor.
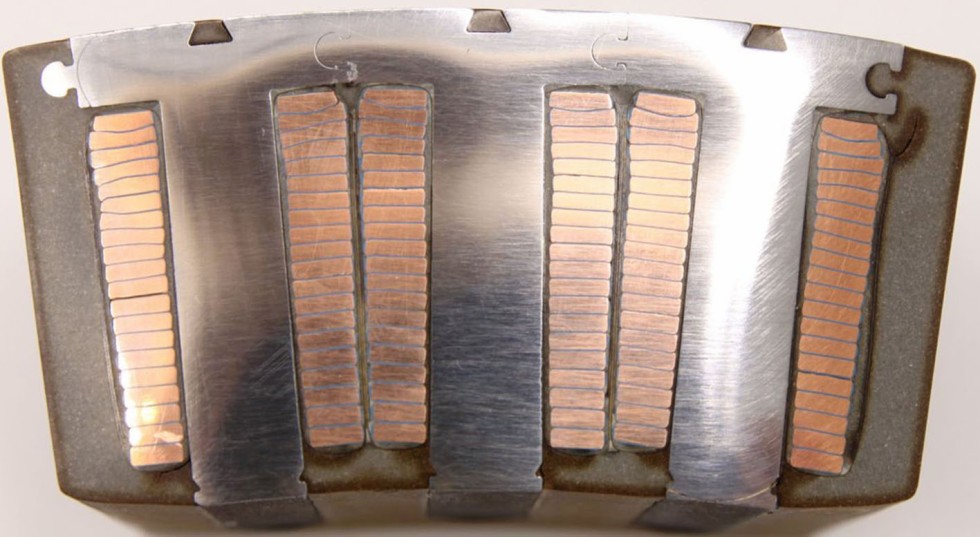
Bild 4. Optimale Ausnutzung der Statornut durch querschnittsvariable Einzelzahnspulen.
Foto: IEM der RWTH Aachen University
3 Isolierung umgeformter Einzelzahnspulen
Für die Primärisolierung der Spule kann Kupferlackdraht als Halbzeug verwendet werden. Dies hat den Vorteil, dass kein zusätzlicher Prozessschritt zur Isolierung der Spule nötig ist und die Herstellungskosten somit geringer sind. Allerdings darf die durch den Prozess verursachte Materialbeanspruchung nicht zu einer Beschädigung der Isolationsschicht führen. In Laborexperimenten mit ähnlicher Belastung des Kupferlackdrahts wie im Umformprozess wurde gezeigt, dass die Isolationsschicht an Stellen, an denen die Windungen miteinander in Kontakt stehen, mit zunehmendem Umformgrad ausdünnt [10]. Dies führt zu einer Abnahme der Teilentladungseinsetzspannung [11]. Daher muss die Isolation durch einen zusätzlichen Prozessschritt nach dem Umformprozess geschehen, der im Folgenden beschrieben wird.
Für die mit der in Abschnitt 2 beschriebenen Umformtechnologie hergestellten Einzelzahnspulen wurden unterschiedliche Beschichtungsverfahren getestet. Besonders geeignet erschienen dabei das Nassspritzverfahren und das elektrostatische Pulverbeschichtungsverfahren. Die Beschichtung umgeformter Einzelzahnspulen ist in Bild 5 zu sehen. Dabei wird der Lack zunächst mittels Verdünner auf eine passende Verarbeitungsviskosität eingestellt, bevor er durch eine Becherpistole oder ähnliche Spritzapparaturen auf die gereinigte Einzelzahnspule aufgetragen wird.
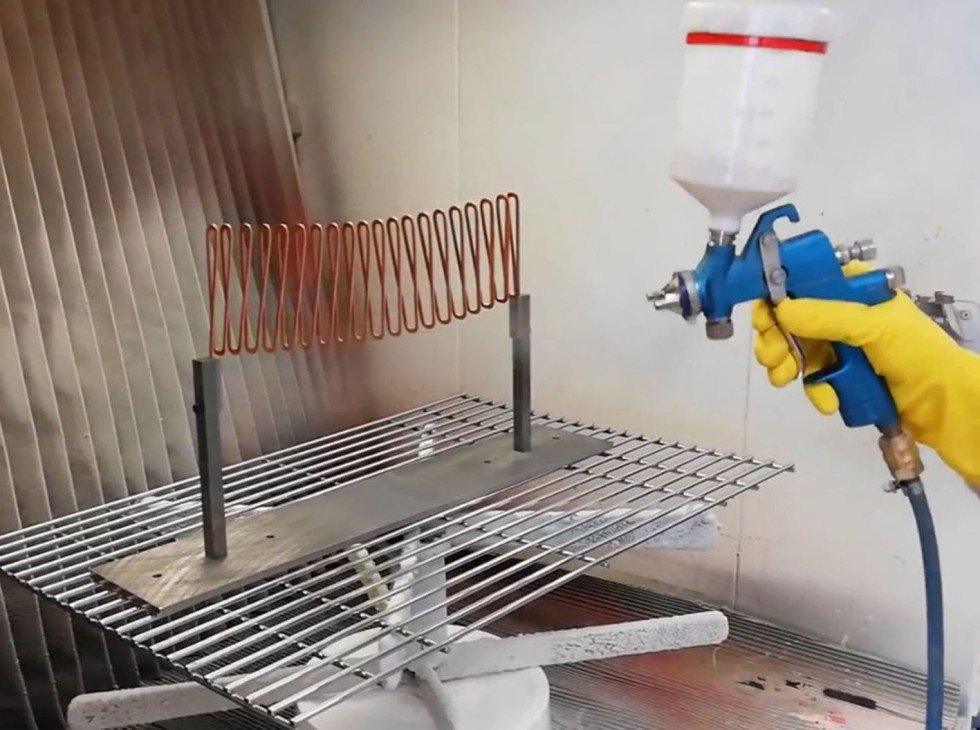
Bild 5. Beschichtung umgeformter Einzelzahnspulen mittels Nassspritzverfahren.
Foto: Breuckmann GmbH & Co. KG
Das alternative Beschichtungsverfahren des elektrostatischen Pulverbeschichtens ist in Bild 6 zu sehen. Im Unterschied zum Nassspritzverfahren wird der Lack pulverförmig durch eine Pistole aufgetragen. Um eine gute Haftung zu gewährleisten, werden die beschichten Bauteile im Anschluss einer Wärmebehandlung unterzogen, damit eine feste Bindung zwischen Lack und Leitermaterial der Spule entsteht.
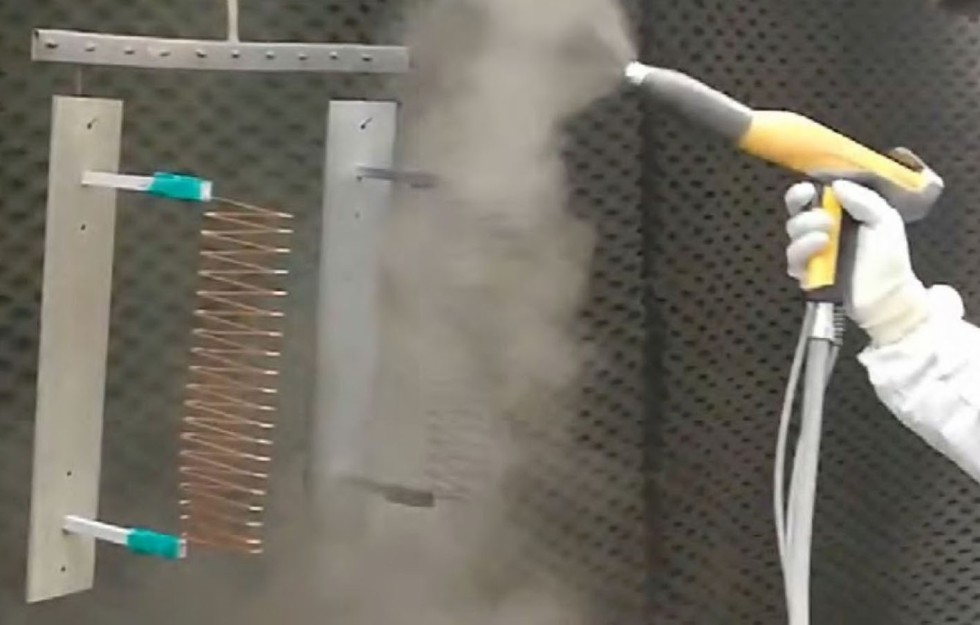
Bild 6. Beschichtung umgeformter Einzelzahnspulen mittels Pulverbeschichtungsverfahren.
Foto: Breuckmann GmbH & Co. KG
Sowohl mit dem Nassspritzverfahren als auch mit dem Pulverbeschichtungsverfahren konnte bei den untersuchten Einzelzahnspulen eine hinreichende Haftung des Lacks erzielt werden. Ein weiteres Kriterium ist die maximal zulässige Schichtdicke von 65 µm, um den anvisierten elektrischen Nutfüllfaktor größer 70 % zu erreichen. Auch hier konnte die Anforderung durch beide Verfahren erfüllt werden. Die Dauertemperaturbeständigkeit und die daraus resultierende Isolierstoffklasse der Statorwicklung sind hingegen nicht nur vom Verfahren, sondern auch vom verwendeten Lack abhängig. Bei der Prüfstandsmessung des mit umgeformten Einzelzahnspulen bestückten Technologieträgers am IEM der RWTH Aachen University wurde die Isolierstoffklasse E genutzt. In weiteren Tests konnten auch umgeformte Einzelzahnspulen mit Lacken der Isolierstoffklasse H erfolgreich isoliert werden.
4 Anwendung umgeformter Einzelzahn spulen in elektrischem Radnabenmotor
Bei Anwendungen mit starker Limitation des Motorenbauraums bieten umformtechnisch hergestellte Einzelzahnspulen die Möglichkeit, die Drehmomentdichte der elektrischen Maschine zu erhöhen. Ein Beispiel ist der hochintegrierte Radnabenantrieb von Schaeffler. Dieser wird vollständig innerhalb des begrenzten Bauraums der Felge des Fahrzeuges verbaut.
Der Stator des elektrischen Motors verfügt über Einzelzähne, auf welche die umgeformten Einzelzahnspulen aufgeschoben werden können. Da es sich bei dem Radnabenmotor um einen Direktantrieb handelt, werden von der E-Maschine vergleichsweise geringe Drehzahlen und hohe Drehmomente gefordert. Aufgrund des begrenzt zur Verfügung stehenden Bauraums ist eine hohe Drehmomentdichte wünschenswert. Eine Möglichkeit diese in der Praxis zu steigern, ist den Kupferfüllfaktor mittels Formspulen zu erhöhen. Aufgrund ihrer Geometrie weisen querschnittsvariable Einzelzahnspulen, insbesondere für Motoren mit niedrigen Drehzahlbereichen und hohem Drehmoment, entscheidende Vorteile bei Wirkungsgrad und Fahrleistung auf.
Im Forschungsprojekt FlexiCoil konnte durch den Einsatz querschnittsvariabler Einzelzahnspulen eine Erhöhung des Kupferfüllfaktors um 33 % gegenüber üblichen Runddrahtwicklungen aus Kupferlackdraht erreicht werden, was zu einer Reduktion der Energieverluste von bis zu 17 % führt. In Folge dessen konnte das Dauerdrehmoment des Radnabenmotors bei niedrigen und mittleren Geschwindigkeiten um circa 10 % erhöht werden. Damit ist diese Technologie prädestiniert für die Anwendung in Radnabenantrieben für städtische Lieferfahrzeuge oder autonome Shuttles wie beispielsweise den Schaeffler-Mover (Bild 7).
5 Zusammenfassung und Ausblick
Querschnittsvariable Einzelzahnspulen sind für Direktantriebe optimal geeignet, bei denen der Motorbauraum sowohl in radialer als auch axialer Richtung begrenzt ist. Durch ihre einzigartige Form führen querschnittsvariable Einzelzahnspulen zu einem hohen elektrischen Nutfüllfaktor und einer gleichmäßigen magnetischen Ausnutzung des Elektroblechs im Stator. Das Resultat ist eine hohe Drehmomentdichte und ein exzellenter Wirkungsgrad der elektrischen Maschine im unteren Drehzahlbereich.
In diesem Beitrag wurde ein umformtechnischer Ansatz vorgestellt, mit dem ausgehend von einer mittels CNC-Biegen hergestellten Einzelzahnspule effizient eine variable Leiterquerschnittsform hergestellt werden kann. Auch wurden zwei unterschiedliche Beschichtungsverfahren diskutiert, die eine Primärisolierung der Spule erlauben, wenn die Verwendung von Kupferlackdraht im Herstellungsverfahren nicht möglich ist. Anwendung finden querschnittsvariable Einzelzahnspulen beispielsweise bei Direktantrieben, wie am Beispiel des hochintegrierten Radnabenantriebs der Firma Schaeffler gezeigt wurde.
Die technologischen Vorteile querschnittsvariabler Einzelzahnspulen gehen mit höheren Herstellungskosten verglichen mit herkömmlichen Runddrahtwicklungen einher. Ein wesentlicher Kostentreiber ist das CNC-Biegen und der dafür benötigte Profildraht. Auch der zusätzliche Prozessschritt des nachträglichen Beschichtens erhöht die Herstellungskosten im Vergleich zu Runddrahtwicklungen. Aus wirtschaftlicher Sicht ist es demnach wünschenswert, gezogen Kupferrunddraht nutzen zu können und die Kosten des Beschichtungsverfahrens, beispielsweise durch eine Steigerung des Automatisierungsgrads, zu senken.
Dieses Forschungs- und Entwicklungsprojekt wurde durch das Bundesministerium für Bildung und Forschung (BMBF) im Programm „Innovationen für die Produktion, Dienstleistung und Arbeit von morgen“ gefördert und vom Projektträger Karlsruhe (PTKA) betreut. Die Verantwortung für den Inhalt dieser Veröffentlichung liegt bei den Autoren.
Literatur
- Doppelbauer, M.: Grundlagen der Elektromobilität. Technik, Praxis, Energie und Umwelt. Wiesbaden: Springer Vieweg Verlag 2020
- Wirth, F.; Kirgör, T.; Hofmann, J.; Fleischer, J.: FE-based Simulation of Hairpin Shaping Processes for Traction Drives. 2018 8th International Electric Drives Production Conference, Schweinfurt, Germany, 2018, pp. 1–5. Doi: 10.1109/EDPC.2018.8658278
- Sell-Le Blanc, F.; Weise, L.; Klusmann, B. et al.: Development of an alternative Round Wire Process Chain: Automated Trickle Winding. 2020 10th International Electric Drives Production Conference (EDPC), Ludwigsburg, Germany, 2020, pp. 1–8
- Petrell, D.; Teller, M.; Hirt, G. et al.: Economical production of conically shaped concentrated windings using forming technology for use in wheel hub engines. 2020 10th International Electric Drives Production Conference (EDPC), Ludwigsburg, Germany, 2020, pp. 1–8
- Hagedorn, J.; Sell-Le Blanc, F.; Fleischer, J.: Handbuch der Wickeltechnik für hocheffiziente Spulen und Motoren. Ein Beitrag zur Energieeffizienz. Heidelberg: Springer Vieweg Verlag 2016
- Hameyer, K. (Hrsg.): FlexiCoil: Entwicklung einer großserienfähigen und wirtschaftlichen Produktionstechnologie für umformtechnisch hergestellte Formspulen elektrischer Antriebe. Abschlussbericht. Düren: Shaker Verlag 2021
- Groninger, M.; Horch, F.; Kock, A. et al.: Cast coils for electrical machines and their application in automotive and industrial drive systems. 2014 4th International Electric Drives Production Conference (EDPC), Nuremberg, Germany, 2014, pp. 1–7
- Linnemann, M.; Bach, M.; Psyk, V. et al.: Resource-efficient, innovative coil production for increased filling factor. 2019 9th International Electric Drives Production Conference (EDPC), Esslingen, Germany, 2019, pp. 1–5
- Petrell, D.; Braun, A. ; Hirt, G.: Comparison of Different Upsetting Processes for the Production of Copper Coils for Wheel Hub Engines. Cham: Springer International Publishing 2019
- Petrell, D.; Teller, M.; Hirt, G. et al.: Manufacturing of Conically Shaped Concentrated Windings for Wheel Hub Engines by a Multi-Stage Upsetting Process. 2019 9th International Electric Drives Production Conference (EDPC), Esslingen, Germany, 2019, pp. 1–7
- Pauli, F.; Schroder, M.; Hameyer, K.: Design and Evaluation Methodology for Insulation Systems of Low Voltage Drives with Preformed Coils. 2019 9th International Electric Drives Production Conference (EDPC), Esslingen, Germany, 2019, pp. 1–7
Daniel Petrell, M. Sc.
Prof. Dr-Ing. Gerhard Hirt
Institut für Bildsame Formgebung der RWTH Aachen University
Intzestr. 10, 52072 Aachen
Tel. +49 241 / 80-95872
daniel.petrell@ibf.rwth-aachen.de
www.ibf.rwth-aachen.de
Stefan Börzel, B. Sc.
Waldemar Schäfer MBA
Betriebswirtschaft
Breuckmann GmbH & Co. KG
Dieselstr. 26–28, 42579 Breuckmann
Tel. +49 2056 / 5801-24
stefan.boerzel@breuckmann.de
www.breuckmann.de
Jens Kattner, M. Sc.
Schaeffler Technologies AG & Co. KG
Industriestr. 1–3, 91074 Herzogenaurach
Tel. +49 9132 / 82-85103
jens.kattner@schaeffler.com
www.schaeffler.com/de