Herstellung von medizintechnischen Multifunktionsteilen
Medizintechnische Produkte wie beispielsweise Katheter, Infusionsleitungen oder -pumpen bestehen aus Multifunktionsteilen, die Aufgaben wie Durchfluss-, Dichtungs- und Dosierungsfunktionen erfüllen müssen. Dies erfordert eine Kombination von festen Thermoplasten in Verbindung mit elastischem Silikon. Hier besteht durch eine geeignete Produktionstechnologie, welche die Verarbeitung von Thermoplasten und Silikon kombiniert, das Potenzial, die bisher aufwendige Fertigung und Montage der Einzelkomponenten abzulösen. Eine derartige integrierte Fertigungstechnologie ermöglicht es, leistungsfähige neue Produkte wirtschaftlich zu realisieren und durch die vereinfachte Herstellung zugleich die Produktsicherheit für den Patienten zu verbessern.
![Bild 1. „Easypump“ II ST/LT der B. Braun Melsungen AG [2].
Foto: B. Braun Melsungen](https://www.ingenieur.de/wp-content/uploads/2021/07/wbk_BMBF_Mekome_Bild-1-980x489.jpg)
Bild 1. „Easypump“ II ST/LT der B. Braun Melsungen AG [2].
Foto: B. Braun Melsungen
Ausgabe 6-2021, S. 440
Im Folgenden steht dabei besonders das Mehrkomponenten-Spritzgießen von LSR und Standardthermoplasten wie etwa ABS (Acryl-Nitril-Butadien Styrol) oder PP (Polypropylen) im Fokus. Nach einer Studie führender Unternehmen und Branchenverbänden hat die Medizintechnikbranche in Deutschland 271 000 t Kunststoffe im Jahr 2019 verarbeitet. [1]
Silikonelastomere, insbesondere Flüssigsilikonkautschuke (Liquid Silicone Rubber oder kurz: LSR), eignen sich aufgrund ihres besonderen Eigenschaftsprofils sehr gut für den Einsatz in der Medizintechnik. Sie sind über einen weiten Temperaturbereich einsetzbar, physiologisch gut verträglich und können auf verschiedene Weisen sterilisiert werden. Als Funktionselemente in medizinischen Komponenten wie etwa Dichtungen, Membranen oder Ventilen werden diese nach Stand der Technik über Füge- und Montageprozesse in Gehäuse aus Thermoplasten (kurz: TP) integriert. Eine Substitution durch einen Mehrkomponenten-Spritzgießprozess (kurz: MK-Spritzgießprozess), der eine wirtschaftlichere, höher automatisierte und qualitativ hochwertigere Produktion ermöglichen würde, ist aktuell für eine Kombination aus Standard-Thermoplast und Flüssigsilikonkautschuk nicht realisierbar, da die Verarbeitungs- und Werkzeugtemperaturen deutlich voneinander abweichen. Durch die bisher erforderlichen Füge- und Montageschritte ist die Produktion von Multifunktionsbauteilen aus thermoplastischem Gehäuse mit silikonbasierten Funktionselementen gegenwärtig zeit- sowie kostenaufwendig. Zugleich erschwert die mehrschrittige Prozesskette die Gewährleistung der erforderlichen Hygiene- und Prozesssicherheit.
Um hier die Vorteile des Mehrkomponentenspritzgießens mit dem Einsatz von Standard-Thermoplasten verbinden zu können, ist die Entwicklung einer variothermen Prozessführung nötig. Die unteren und oberen Zieltemperaturen legen dabei die materialspezifischen thermischen Eigenschaften fest. Um hier eine möglichst hohe Bandbreite an Standard-Thermoplasten (ABS, MABS, PMMA, PP) einsetzen zu können, muss die untere Werkzeug-Temperatur der LSR-Kavität etwa 80 °C beziehungsweise unter der Wärmeformbeständigkeitstemperatur des Thermoplastes betragen, die obere Temperatur zur raschen Vulkanisation des Flüssigsilikonkautschuks mindestens 140 °C. Hintergrund ist, dass beim Overmolding mit LSR der Thermoplast-Vorspritzling in die beheizte Kavität eingelegt werden muss. Bild 2 illustriert die Problemstellung bei der Herstellung unter der Verwendung einer statischen Werkzeug-Temperierung von 140 °C (oben) und im Vergleich dazu die dynamische Temperierung ohne Deformation (unten). Bei 140 °C erweicht der Thermoplast, in diesem Fall ABS, und dieses führt nach der Entformung zu Verzug am Bauteil.
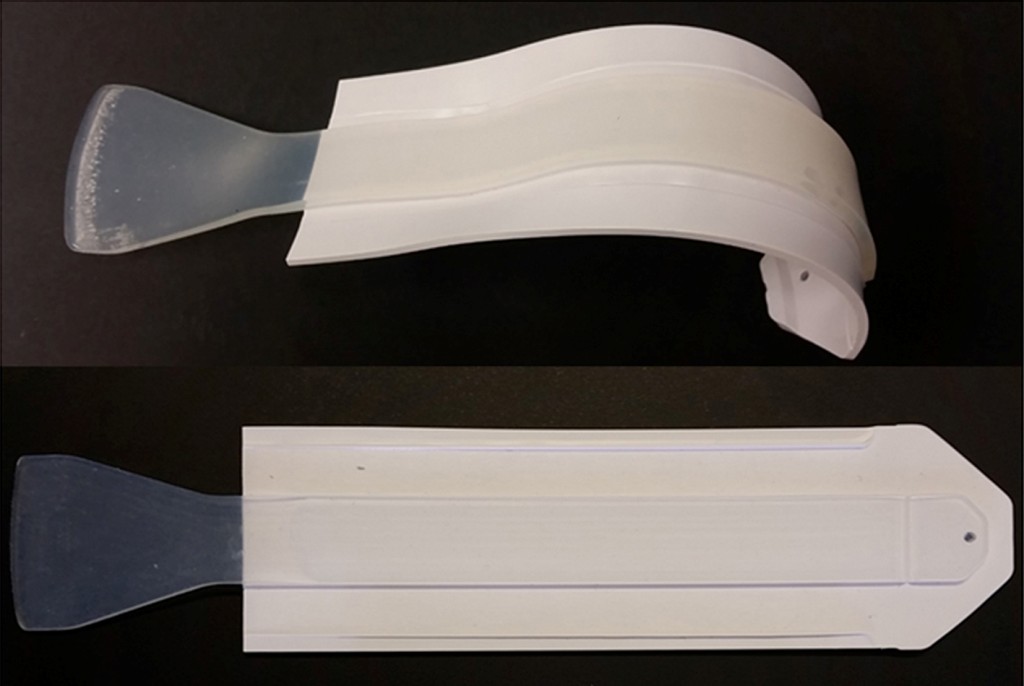
Bild 2. Herstellung der Multikomponentenbauteil ohne und mit der dynamischen Temperierung.
Foto: Institut für Werkstofftechnik-Kunststofftechnik, Universität Kassel
Eine Möglichkeit Standardthermoplaste mit geringer Wärmeformbeständigkeit im TP/LSR-Spritzguss einzusetzen, ist die Nutzung der dynamischen Temperierung des Werkzeugs (Variothermie). Durch die Verwendung und Weiterentwicklung der variothermen Temperierung des in den Spritzgießprozess integrierten Werkzeugs ist es realisierbar, Werkzeugtemperaturen (zum Beispiel von 80 °C auf 180 °C) in einem Zyklus im Sekundenbereich hin- und herzuschalten. Dies ermöglicht die Vulkanisation des LSR bei gleichzeitiger Formstabilität des Thermoplasts.
2 Stand der Technik
Die Verwendung einer dynamischen Temperierung in der Kunststofftechnik ist nicht neu und wird zur Steigerung der Bauteilqualität, Verringerung der Zykluszeit und Herstellung dünnwandiger Bauteile benutzt. Der Einsatz einer dynamischen Temperierung zur Herstellung eines LSR/TP-Verbundbauteils hat die Herausforderung, dass die Wärme einseitig in den Silikonkautschuk gebracht wird und dennoch ein hoher Vernetzungsgrad im Bauteilinneren erreicht werden muss. Die silikonspezifische geringe Wärmeleitfähigkeit steht dieser Anforderung hemmend gegenüber. Ein weiterer wichtiger Punkt beim MK-Spritzgießen ist darüber hinaus der Adhäsionsmechanismus zwischen den verschiedenen Materialien. Bei dauerhafter chemischer Anbindung kann eine Mediendichtigkeit erreicht und auf Durchbrüche oder Hinterschnitte zur mechanischen Verankerung am Substratbauteil verzichtet werden. Signifikanten Einfluss auf die Verbundhaftung haben die chemische und physikalische Kompatibilität der Materialkombinationen und die Verarbeitungsbedingungen. Zur Haftungserzeugung zwischen den Komponenten könnte eine UVC-Oberflächenvorbehandlung, Beflammung mit Pyrosil oder Plasmavorbehandlung, abhängig der jeweiligen Kombinationen, vorgenommen werden. [3] [4]
2.1 Mehrkomponentenspritzgießen
Am Institut für Werkstofftechnik, Fachgebiet Kunststofftechnik der Universität Kassel ist eine 2K-Spritzgießmaschine und ein Versuchswerkzeug vorhanden, mit dem Schälprüfkörper aus Thermoplast und LSR nach VDI-Richtlinie 2019 hergestellt werden können (Bild 3).
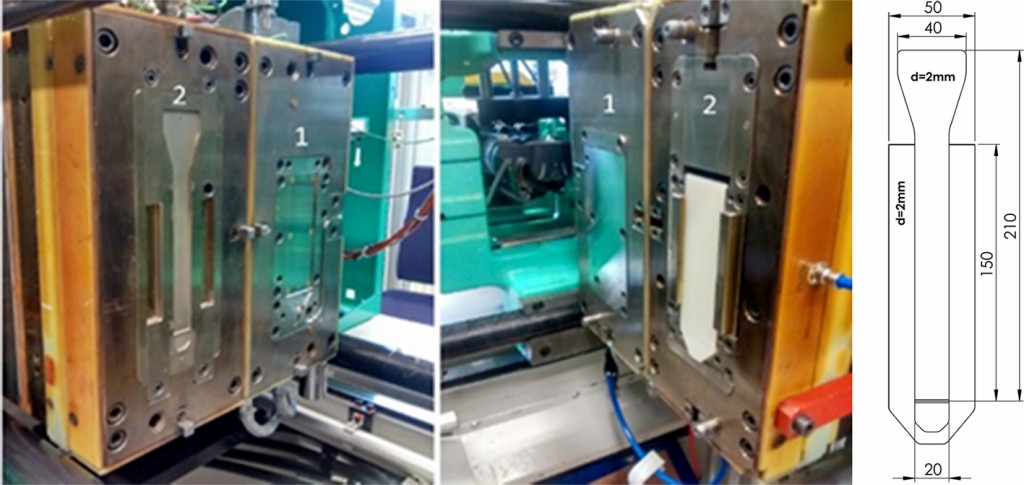
Bild 3. Spritzgießwerkzeug und Schälprüfkörpern nach VDI-Richtlinie 2019, Kennzeichnung 1: Thermoplast-Kavität, Kennzeichnung 2: LSR-Kavität.
Foto: Institut für Werkstofftechnik-Kunststofftechnik, Universität Kassel
Die VDI-Richtlinie stellt ein standardisiertes Verfahren zur Bestimmung von Haftung spritzgegossener Verbundprüfkörper dar. Das Spritzgießwerkzeug verfügt über eine Thermoplast- und eine LSR-Kavität, mit dem sowohl das Spritzgießen einer thermoplastischen Grundplatte als auch das Überspritzen jener mit LSR in einem Schritt möglich ist. Das Werkzeug eignet sich aufgrund einer konventionellen Beheizung der LSR-Kavität nicht, um MK-Bauteile aus ABS und LSR herzustellen. Üblicherweise beträgt die Werkzeugtemperatur 140 °C bis 180 °C, um eine Vulkanisation wirtschaftlich im Sekunden- bis Minutenbereich zu erzielen. Angenommen der Vorspritzling aus ABS wird in die heiße LSR-Kavität eingelegt, so erweicht dieser und eine anschließende Entformung nach dem Überspritzen und Vulkanisieren des LSR ohne Deformation ist nicht möglich. Aus diesem Grund wurde für das vorhandene Werkzeug ein Formeinsatz entwickelt, welcher dynamisch temperiert werden kann, das heißt innerhalb eines Spritzgießzyklus sind unterschiedliche Werkzeugwandtemperaturen wirksam. Die Erfahrungen, die hierbei gesammelt werden, sollen dabei mit in die Entwicklung des späteren Demonstratorwerkzeuges für einen medizintechnischen Prototyp eingehen.
2.2 Fluidische dynamische Temperierung
Durch die Verwendung einer fluidischen dynamischen Temperiereinheit, von der Wenz Kunststoff GmbH & Co. KG aus Lüdenscheid können Temperaturen im Bereich von 60 °C bis 180 °C in kurzer Zeit dynamisch erreicht werden (Bild 4).
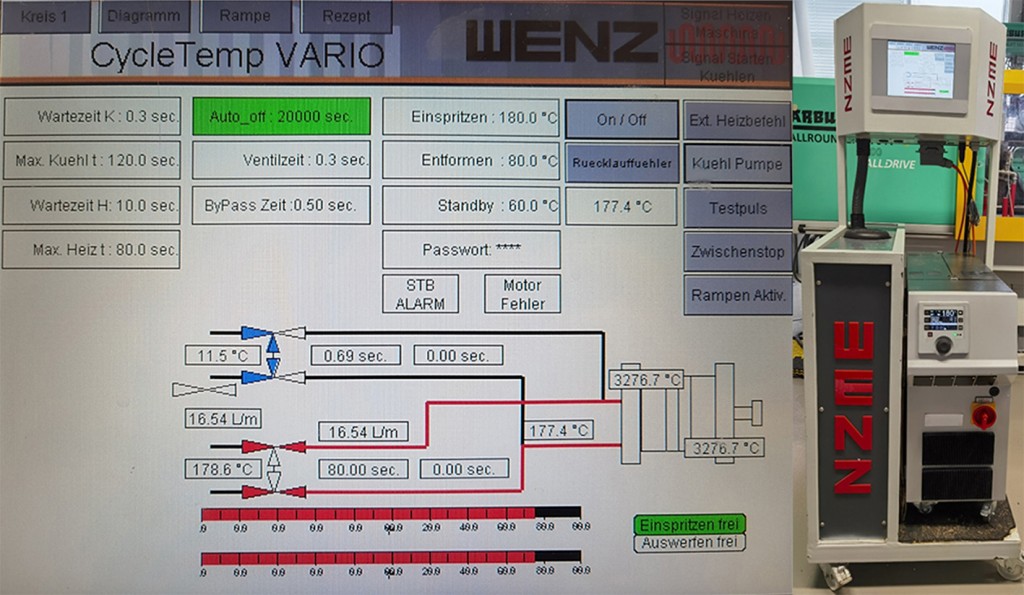
Bild 4. Dynamische Temperiereinheit und Menüs auf dem Touchpanel.
Foto: Institut für Werkstofftechnik-Kunststofftechnik, Universität Kassel
Sie schaltet zyklisch kalte und heiße Wasserreservoirs durch das Werkzeug hin und her. Die Heißwassertemperatur und der Wechsel zur Kaltwassertemperatur werden an einer Temperiereinheit eingestellt und über diese gesteuert. Unterstützt durch einen Booster erhitzt die Einheit das Wasser des Heißwasserkreislaufs. Mit folgenden Programmabläufen wird dieses Gerät bedient: Das Wasser wird im Heißbehälter auf die voreingestellte Temperatur erwärmt. Durch das Signal der Spritzgießmaschine läuft nun Heißwasser durch das Werkzeug. Mit einer eingegebenen Haltezeit wird die Temperatur im Werkzeug bis zu einem definierten Maximum, welches niedriger als die eingestellte Temperatur ist, erreicht und bleibt dann während des Spritzgießzyklus annähernd konstant. Das darauffolgende Signal pumpt Kühlwasser durch das Werkzeug, bis die voreingestellte Entformungstemperatur erreicht ist. Danach schaltet die Steuerung der Temperiereinheit in den By-Pass-Modus und hält die Temperatur konstant bis zum Beginn des nächsten Zyklus. [5]
2.3 Werkzeug-Einsatz mit der fluidischen, dynamischen Temperierung
Als Technologie zur dynamischen Temperierung wurde eine fluidische Temperierung mit Wasser ausgewählt. Der Formeinsatz wurde derart ausgelegt, dass dieser mit konturnahen Bohrungen zur Fluidführung versehen ist (Bild 5). Durch die geringe thermische Masse bis zur Werkzeugoberfläche sind sehr hohe Aufheiz- und Abkühlraten möglich. [6] Als Zielgrößen werden hier ~20 °C/s angestrebt. Dementsprechend führen die Aufheiz- und Abkühlrampen nur zu einer moderaten Erhöhung der Zykluszeit: Eine wirtschaftliche Produktion ist möglich.
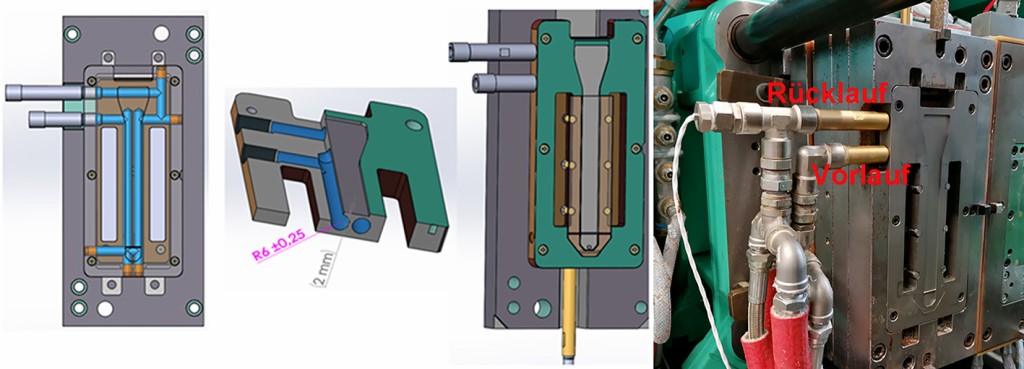
Bild 5. Entwicklung des Formeinsatzes zur dynamischen Temperierung.
Foto: Institut für Werkstofftechnik-Kunststofftechnik, Universität Kassel
2. 4 Temperaturverläufe
Mithilfe einer Wärmebildkamera wurde das Aufheiz- und Abkühlverhalten der Werkzeugoberflächentemperatur ermittelt und mit der gemessenen Temperatur der Thermokopplung des Rücklaufs verglichen (Bild 6). Hier zeigte sich eine deutliche Diskrepanz zwischen dem Thermofühler in der Rücklaufleitung der Temperiereinheit und der tatsächlich vorliegenden Oberflächentemperatur. Mithilfe eines Versuchsplans wurden die Differenzen ermittelt, um so die tatsächlichen Oberflächentemperaturen steuern und bewerten zu können. Grundlegend ist die Machbarkeit der variothermen Temperierung in Bezug auf den Anwendungsfall gegeben. Eine Zykluszeit von 80 Sekunden liegt je nach LSR-Typ, trotz nur einseitigem Wärmeeintrag, im realisierbaren Bereich.
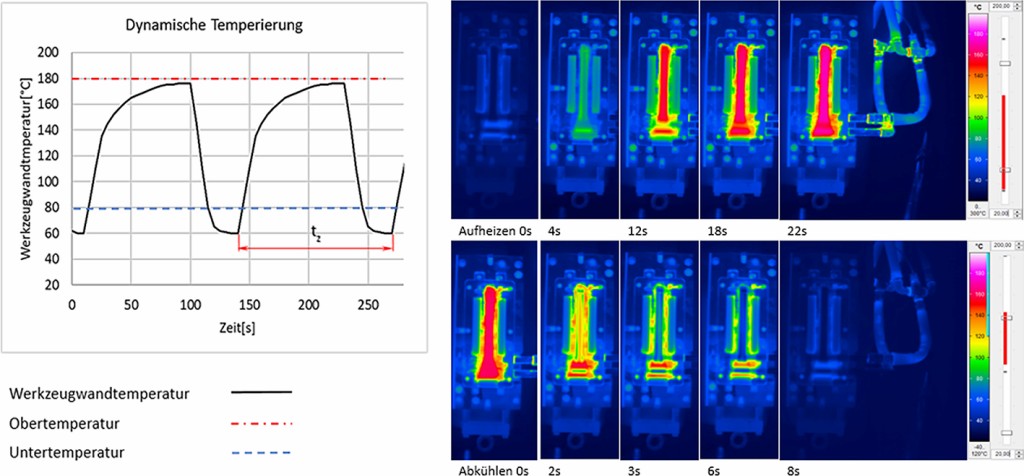
Bild 6. Wärmebildaufnahmen der zeitlichen Temperaturentwicklung des Formeinsatzes beim Aufheizen (oben) und Abkühlen (unten).
Foto: Institut für Werkstofftechnik-Kunststofftechnik, Universität Kassel
2.5 Ermittlung der Haftfestigkeit nach VDI-Richtlinie 2019
Zur Ermittlung der Hafteigenschaften von ABS/LSR Komponenten werden die hergestellten Prüfkörper einem Schälversuch, gemäß der VDI-Richtlinie 2019, unterzogen (Bild 7). Die Machbarkeit der grundlegenden Projektidee ist nur gegeben, wenn sich für die angestrebten Materialkombinationen eine Haftung realisieren lässt. Voruntersuchungen ergaben, dass dies nur mithilfe einer Oberflächenvorbehandlung für diese Materialkombination möglich ist. [7]
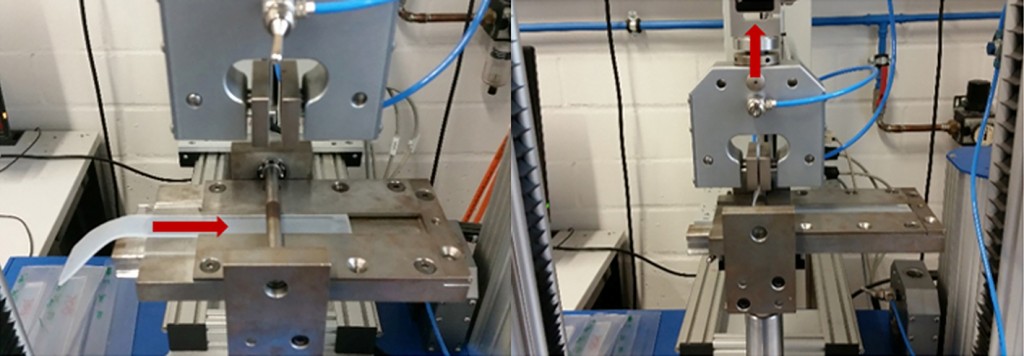
Bild 7. Ermittlung der Haftung nach VDI-Richtlinie 2019.
Foto: Institut für Werkstofftechnik-Kunststofftechnik, Universität Kassel
2.6 Methoden zur Oberflächenaktivierung
Die UVC-Strahlung bedient sich eines photochemischen Prinzips, das sich in zwei separat zu betrachtende Mechanismen unterteilen lässt. Die Photolyse beschreibt die Schwingungsresonanz zwischen den kovalenten Bindungen des Polymers und der absorbierten Strahlungsenergie, die proportional zur Wellenlänge ist. Da die eingesetzte UVC-Strahlung eine Wellenlänge von 180–260 nm aufweist, kann sie Bindungen in Polymeren (beispielsweise C-C, C=C, C-O) aufbrechen. Diese neu entstandenen reaktiven Polymerenden führen zur Erhöhung der Adhäsion zum LSR. Die Photo-Oxidation ist der weitere Mechanismus, der bei der Aktivierung zum Tragen kommt. Dabei wechselwirkt die UVC-Strahlung mit dem Luftsauerstoff und lässt reaktives Ozon entstehen, das sich an der Polymeroberfläche anlagert. Die Oberflächenaktivierung erhöht insbesondere den polaren Anteil der Oberflächenenergie. Für TP/LSR-Verbunde, die mit Polycarbonat realisiert wurden, gibt es entsprechende Ergebnisse, die auch für die Oberflächenaktivierung von Standard-Thermoplasten als grundlegende Erklärungen herangezogen werden können. [3]
Die Silikatisierung mittels Beflammung ist eine weitere Art der Oberflächenaktivierung, die im Rahmen dieses Projekts untersucht wurde. Bei diesem Verfahren wird eine Silikondioxid-Schicht, die hoch reaktiv ist, auf das Substrat aufgetragen. Als Brenngas in dieser Untersuchung diente Pyrosil, ein Gasgemisch aus Propan und Butan. Bei diesem Aktivierungsverfahren gibt es signifikante Unterschiede zwischen der Kurz- und Langzeitbeständigkeit der gesteigerten Oberflächenenergie. [4]
3 Ergebnisse
In zahlreichen Untersuchungen unterschiedlicher Materialkombinationen aus Thermoplasten und Flüssigsilikonkautschuken wurden zwei geeignete ausgewählt. Beide LSR-Typen zeigen nach einer Oberflächenaktivierung mittels UVC-Strahlung oder Beflammung eine gute Haftung auf allen ausgewählten ABS-Substraten (Bild 8).
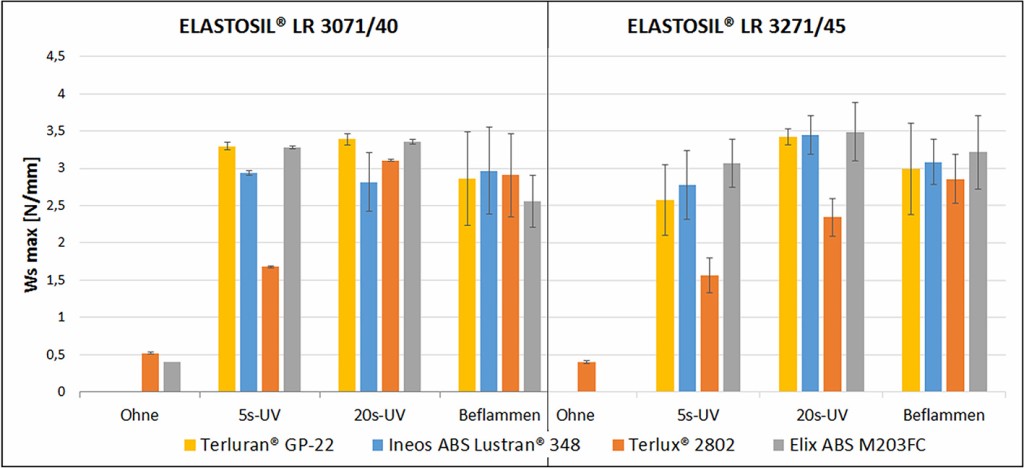
Bild 8. Vergleich der Schälwiderstände infolge der Oberflächenvorbehandlungen UVC und Beflammen an ausgewählten Materialkombinationen.
Foto: Institut für Werkstofftechnik-Kunststofftechnik, Universität Kassel
Eine Kombination aus Wacker Elastosil LSR 3071/40 und Terluran GP 22 natura erfüllt die Voraussetzungen hinsichtlich der Medizintechnik-Zulassungen und Adhäsion nach der Oberflächenvorbehandlung. Während ohne Aktivierung die Haftung zwischen LSR und TP sehr gering ist, zeigt diese Kombination bereits ab einer kurzen UVC-Bestrahlungszeit der ABS-Platte von 5 Sekunden eine homogene, hohe Verbundhaftung. Die nachfolgenden Diagramme zeigen weitere mögliche Materialkombinationen und stellen den Vergleich der unterschiedlichen Oberflächenvorbehandlungen in Form von UVC-Bestrahlung und Beflammung dar. Die Silikatisierung mittels Beflammung der Thermoplaste erweist sich als eine gute Alternative zur UVC-Bestrahlung hinsichtlich der Adhäsionseigenschaften. Nachteilig hier ist aber eine deutlich komplexere Prozesstechnik und Integrierbarkeit in den Produktionsprozess. Auch hinsichtlich der Reinraumeignung weist das Vorbehandeln mittels UVC-Strahlung deutliche Vorteile auf.
4 Zusammenfassung und Ausblick
Die Umsetzung im Projekt wird unter Berücksichtigung technischer und regulatorischer Anforderungen der Medizintechnik dahingehend gestaltet, dass eine Übertragung auf eine hohe Anzahl von aktuellen und zukünftigen medizintechnischen Produkten möglich ist. Durch geeignete konturnahe Temperierkanäle und passender Temperiereinheit gelang eine vollständige Vulkanisation in angemessener Zykluszeit. Die Haftfestigkeit zwischen Silikonkautschuk und ABS konnte durch die passende Materialkombination und UVC-Bestrahlung ermöglicht werden. Verschiedene Anwendungsszenarien (zum Beispiel Anwendung im wässrigen Milieu) spielen für diesen Haftverbund ebenfalls eine wichtige Rolle. Eine Validierung des Produktionsprozesses für jedes einzelne Produkt soll abhängig von der Temperierungsmethode zum Nachweis der reproduzierbaren Qualität der Fertigung erbracht werden. Dadurch werden Coldspots beziehungsweise Hotspots im Werkzeug erkannt und gegebenenfalls mittels der Verwendung von thermisch kompatibler Werkzeugeinsätze entgegengewirkt. Die Machbarkeit eines solchen Prozessverlaufs kann nicht nur zu einer wirtschaftlicheren Produktion führen, sondern zugleich eine hygienesichere und montagefreie Produktion ermöglichen. Eine gesteigerte Bauteilqualität führt zur Erhöhung der Patientensicherheit. Die zukünftigen Forschungstätigkeiten konzentrieren sich auf die Erweiterung und Verbesserung der einzelnen Prozessschritte, so dass eine geringere Zykluszeit erreicht werden kann. Darüber hinaus werden die Versuche zur Haftungsermittlung verschiedener Materialkombinationen laufend erweitert, um die Produktqualität zu erhöhen. Dazu gehört auch die Wechselwirkung zwischen der Materialkombination und den Prozessparametern, die beispielsweise die Kristallinität der TP-Komponente, und somit die Oberflächenenergie, beeinflusst. [8]
Literatur
- Lindner, C. et al.: Stoffstrombild Kunststoffe in Deutschland 2019. Conversio Market & Strategy 08 (2020)
- N. N.: Easypump© II ST/LT. B.Braun Melsungen AG
- Hartung, M. et. al.: UV Surface Treatment of Polycarbonate for Adhesion Improvement to Liquid Silicone Rubber (LSR). Journal of Plastics Technology, Volume 15 (2019), Carl Hanser Verlag
- Rüppel, A. et. al.: Langzeitbeständigkeit der Silikatisierung und der Einfluss auf die Haftungseigenschaften zwischen Flüssigsilikonkautschuk-Thermoplastverbunden. KGK Kautschuk, Gummi, Kunststoffe, 71 (2018) 3, S. 20–25
- N. N.: Temperiergerät P140M/P160M/P180M/P160MD/P180MD. Betriebsanleitung, WENZ Kunststoff GmbH & Co. KG, Lüdenscheid
- Tromm, M. et. al.: Schaum nach Maß, Journal Kunststoffe 02 (2018), Carl Hanser Verlag
- Verein Deutscher Ingenieure: VDI 2019: Prüfung der Haftung von thermoplastischen Elastomeren (TPE) an Substraten. Berlin: Beuth Verlag 2016
- Güzel, K. et. al.: Influence of the degree of crystallinity and the surface free energy on the adhesion properties of different PLA/PBS blends in multicomponent injection molding. The 35th International Conference of the Polymer Processing Society (2020), Izmir, Turkey
Das könnte Sie auch interessieren:
Einzigartige Mikroskopie für den Blick bis zur molekularen Ebene
Prof. Dr.-Ing. Hans-Peter Heim
Dr.-Ing. Ralf-Urs Giesen
Mohammad Ali Nikousaleh
Michael Hartung
Universität Kassel
Institut für Werkstofftechnik / Kunststofftechnik IFW
Mönchebergstr. 3, 34125 Kassel
Tel. +49 561 / 804-3671
fedler@uni-kassel.de
www.uni-kassel.de/maschinenbau/institute/institut-fuer-werkstofftechnik/fachgebiete/kunststofftechnik/kunststofftechnik.html
Niklas Riemann
B.Braun Melsungen AG
Carl-Braun-Str. 1, 34209 Melsungen
Tel. +49 171 9016377
niklas.riemann@bbraun.com
www.bbraun.com