Netzwerkunterstützung durch Digitale Zwillinge
Bisherige Ansätze des Digitalen Zwillings beschränken sich auf die digitale Nachbildung einer Maschine insbesondere in deren Betriebsphase. Im Projekt „Co-TWIN“ wird dieses Konzept zum kollaborativen Digitalen Zwilling erweitert, der die Zusammenarbeit nicht nur lebenszyklus- sondern auch wertschöpfungspartnerübergreifend unterstützt. Dieser Beitrag zeigt die Grundidee des kollaborativen Digitalen Zwillings auf und präsentiert den aktuellen Stand der technischen Umsetzung der Co-TWIN-Plattform.
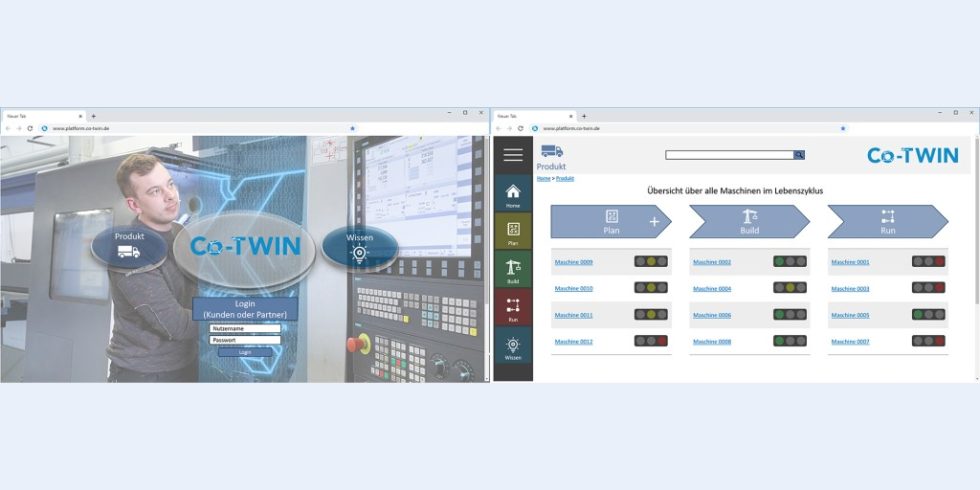
Bild 1. Prototypische User Interfaces der Co-TWIN-Plattform.
Foto: BAM GmbH; TU Chemnitz, PSP/WI, René Apitzsch
Ausgabe 4-2021, S. 243
1 Ausgangssituation und Motivation
Der Maschinen- und Anlagenbau unterzieht sich, wie andere Industriezweige, aktuell einem fundamentalen Wandel. Auslöser und Förderer dieses Wandels in der Industrie sind verschiedene Phänomene der digitalen Transformation, die weitläufig unter dem Begriff Industrie 4.0 zusammengefasst werden [1]. Zugehörige Technologien und Konzepte können zu Wettbewerbsvorteilen beitragen, indem sie die Zusammenarbeit in den Wertschöpfungsnetzwerken des Maschinen- und Anlagenbaus effizient gestalten. Denn dieser zeichnet sich in Deutschland durch eine Vielzahl dezentral organisierter, mittelständisch geprägter Produktions- und Zulieferernetzwerke aus.
Ein Grundpfeiler für Industrie 4.0 ist das Konzept der Digitalen Zwillinge, welche eine Verbindung zwischen physischen Gegenständen in der Realwelt und virtuellen Gegenstücken in der digitalen Welt herstellen [2]. Dabei bildet die virtuelle Seite stets den aktuellen Zustand des physischen Gegenstandes (Asset) ab. Ein Regelkreis gewährleistet, dass Daten in Echtzeit ausgetauscht und ausgewertet werden, wodurch eine Steuerung ermöglicht wird. Neben den Echtzeitdaten stehen ebenfalls historische Daten zum automatisierten Weiterentwickeln von virtuellen Modellen zur Verfügung. Der Digitale Zwilling kann Daten aus allen Lebenszyklusphasen des Assets enthalten. So können Dienstleistungen wie Analysen, Vorhersagen oder Empfehlungen auf der Basis von erhobenen Daten und Analysemodellen angeboten werden. Das aktuelle Verständnis und der Entwicklungsstand Digitaler Zwillinge in der Industrie realisiert die umfangreichen Potenziale des Konzeptes jedoch noch nicht vollständig [3].
2 Der Kollaborative Digitale Zwilling
Neben diesem Einsatzzweck im Rahmen von Analysen und Optimierungen erlauben Digitale Zwillinge weitere Mehrwerte für Unternehmen, speziell im Bereich des Produktlebenszyklusmanagements (PLM). Die Grundidee des PLM, der Integration aller Informationen, die im Lebenszyklus eines Produktes entstehen, lassen sich mit einem Digitalen Zwilling umsetzen [3]. Statt wie bisher die Anwendungsbereiche der Produktentwicklung, Fertigungsplanung, Steuerung der Fertigungsanlagen und der Produktionsaufträge getrennt zu betrachten, kann mit Digitalen Zwillingen eine Integration der Systeme und Datenbasis inklusive Kontext- und Produktnutzungsdaten erfolgen.
Da der deutsche Maschinen- und Anlagenbau, wie bereits eingangs erwähnt, durch die dezentrale Organisation von vielen kleinen und mittleren Unternehmen, die sich auf einzelne Schritte in der Wertschöpfungskette spezialisiert haben, geprägt ist, wird eine unternehmensübergreifende Zusammenarbeit notwendig, um ihren Kunden Mehrwerte liefern zu können. Hier unterstützt ein Digitaler Zwilling umfassend, indem er die unterschiedlichen Wertschöpfungspartner digital verbindet und die Daten eines Produktes unternehmensübergreifend in sich vereint. So wird durch die Abstraktion von spezifischen Unternehmensgegebenheiten wie IT-Schnittstellen und Datenformaten zu einem einheitlichen, abgestimmten Standard eine reibungslose Kommunikation und Zusammenarbeit zwischen einzelnen Wertschöpfungspartnern gewährleistet. Eine partner- und lebenszyklusübergreifende Integration von Daten bietet speziell für kleine und mittlere Unternehmen mit begrenzten Ressourcen weitreichenden Nutzen [4].
3 Die Co-Twin-Plattform
Die Ziele des Forschungsprojektes Co-TWIN sind die Konzeption und prototypische Entwicklung einer Plattform, die auf die Aspekte der lebenszyklusphasenübergreifenden Integration von Daten speziell im Kontext von Wertschöpfungsketten eingeht und dadurch die integrierende Rolle von Digitalen Zwillingen von Einzelunternehmensebene auf interorganisationale Zusammenarbeit erweitert. Die Co-TWIN-Plattform ist ein IT-System, mit dem geplante und reale Maschinen in untereinander verknüpften, digitalen Sichten abgebildet werden können. Dadurch wird es unternehmensinternen und/oder -externen Stakeholdern ermöglicht, kollaborativ in verschiedenen Phasen des Maschinenlebenszyklus zusammenzuarbeiten [4]. Bild 1 zeigt exemplarisch die im Projekt entwickelten grafischen Benutzeroberflächen der Plattform.
In Kooperation von zwei Universitäten mit vier Sondermaschinenbauunternehmen realisieren im Projekt zwei IT-Unternehmen konkrete betriebliche Anwendungsfälle. Im weiteren Verlauf gibt der Beitrag einen Einblick in die aktuelle Entwicklung der Co-TWIN-Plattform. Dabei wird zum einen auf die Konfiguration von Sondermaschinen mit dem Kunden unter Einsatz von moderner Virtual Reality (VR) Technologie eingegangen. Zum anderen wird eine Microservice-Architektur beschrieben, die durch ihre Modularität die Co-TWIN-Plattform als zwischen den Wertschöpfungspartnern verteiltes Informationssystem realisiert. Des Weiteren wird aufgezeigt, wie die Verwaltungsschale als etablierter Kommunikationsstandard für Industrie 4.0 in der Co-TWIN-Plattform genutzt wird, um die Systemkomponenten zu einem zusammenhängenden Gesamtsystem zu vernetzen.
4 Technische Realisierung der Co-TWIN-Plattform
4.1 Virtual Reality Technologie für geführte Konfiguration von Sondermaschinen
Zur Unterstützung der Kundenkommunikation entwickelt die Technische Universität Chemnitz mit der Schmale Maschinenbau GmbH einen VR-basierten Konfigurator, der auf eine interaktive Konfiguration von Maschinen aus Standardkomponenten abzielt. Dabei können einzelne Funktionskomponenten an Arbeitswänden entsprechend dem Bearbeitungsprozess virtuell zusammengestellt und montiert werden (Bild 2).
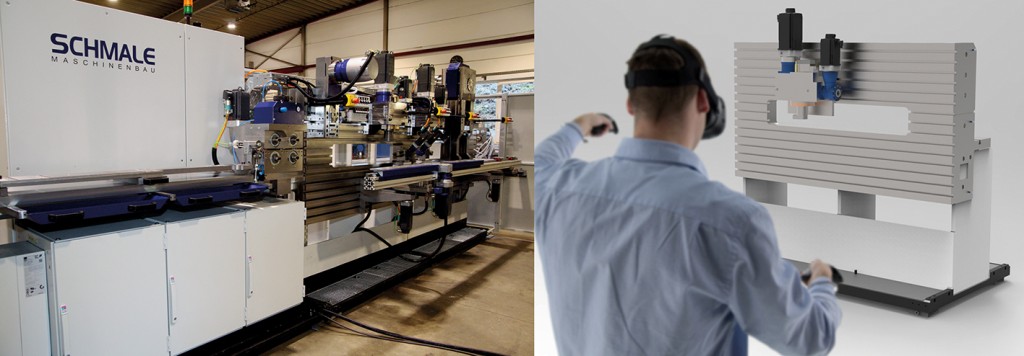
Bild 2. Drahtbiegeanlage und deren Konfiguration in Virtual Reality.
Foto: Schmale Maschinenbau GmbH; TU Chemnitz, PSP
Eine Anforderung an die Umsetzung ist die interaktive Nutzung wahlweise an einem Mobilgerät oder mithilfe eines Head-Mounted Display in VR. Um die Anwendung möglichst universell verwendbar zu machen, wird der Demonstrator auf Basis der WebXR-Schnittstelle umgesetzt. Dies erlaubt den Zugriff auf VR-Geräte und grafische Ressourcen aus kompatiblen Webbrowsern. Hierfür können sowohl autarke VR-Brillen als auch Laptops als Endgeräte verwendet werden. Die Darstellung von Modellen innerhalb solcher WebXR-Anwendungen erfolgt auf Basis des Dateiformates GLTF/GLB. Um die für die Bibliothek der möglichen (Standard-)Komponenten notwendigen Modelle zu erzeugen, wurde ein möglichst einfacher Workflow entwickelt, der diese auf Basis vorhandener CAD-Daten generiert. Die hierfür genutzten Standardexportschnittstellen des verwendeten CAD-Systems gewährleisten in Verbindung mit dem 3D-Modellierungswerkzeug Blender, dass der Workflow prinzipiell automatisierbar ist. Dabei stellt das Aussehen der Materialoberflächen bei den einzelnen Komponenten eine Herausforderung dar, da zum einen durch den Export beziehungsweise die Wandlung des Dateiformates Materialinformationen verlorengehen und zum anderen WebXR nicht alle Darstellungsmöglichkeiten unterstützt. Hierfür wurde eine Bibliothek von Standardmaterialien definiert, die per Skript in die Modelle integriert werden können. Gleichzeitig sorgt dieses Vorgehen für ein gleichartiges Aussehen der verwendeten Funktionsgruppen. Die Co-TWIN-Plattform stellt in diesem Zusammenhang die Bibliothek der möglichen Komponenten und deren 3D-Modelle zur Verfügung. Die entstehende Konfiguration wird als Bestandteil des Digitalen Zwillings einer möglichen Maschine erfasst, ein von der Plattform zur Verfügung gestellter Service soll die Erzeugung eines 3D-PDFs für die erleichterte Kommunikation ermöglichen.
4.2 Microservices als Architekturmuster der Co-TWIN-Plattform
Im Rahmen des Projektes wird, angeführt durch die N+P Informationssysteme GmbH, eine Plattform zur Bereitstellung von Services des Digitalen Zwillings entlang des gesamten Lebenszyklus eines physischen Assets (eine Anlage, ein Ersatzteil oder sogar ein Gebäude) entwickelt. Die dabei entstehende Co-TWIN-Plattform, deren Grundstruktur in Bild 3 dargestellt wird, ist keine klassische Client-/Server-Anwendung mit einer zentralen Datenbank, sondern eine Cloud-Anwendung mit Microservice-Architektur.
Die jeweiligen Services werden dabei durch einzelne Microservices umgesetzt. Jeder Microservice besitzt eine eigene Datenhaltung mit nur den Daten, die er für seinen Prozess benötigt. Die Kapselung von In- und Output eines Microservices ist standardisiert, damit die Services sinnvoll miteinander interagieren können. Die Orchestrierung aller Services, also die Verwaltung des Zusammenspiels, übernimmt Kubernetes. Dabei werden die Microservices als Container (zum Beispiel Docker) deployed und entsprechend der Lastanforderung skaliert. Damit die Services sich auf ihren Prozess fokussieren können, gibt es zwischen ihnen und Kubernetes noch eine Zwischenschicht, welche zum Beispiel die Anbindung von Datenbanken realisiert sowie die Authentifizierung übernimmt. Mit dem Aufbau der Plattform wird die Integration von Drittanbieter-Services unterstützt, um zusätzlich die Kompetenzen von Partnern und Kunden in die Plattform zu integrieren.
Ziel des Digitalen Zwillings innerhalb der Plattform ist jedoch das Zusammenbringen aller Informationen, die während des Lebenszyklus des Assets entstanden sind. Das heißt, es müssen die über die Microservices verteilten Daten wieder aggregiert werden. Zu diesem Zweck bietet sich die Verwendung der Verwaltungsschale an. Durch deren flexible Struktur (Details nachfolgend) können die Informationen für zum Beispiel Konstruktion, Fertigung und Service in einem „Dokument“ zusammengefasst, anderen Unternehmen (Kunden, Lieferanten) zur Verfügung gestellt und für Kollaborationen verwendet werden. Die Plattform liefert hierfür die Grundlage, entsprechende Informationen flexibel zu verarbeiten.
4.3 Verwaltungsschale als Kommunikationsstandard der Industrie 4.0
Für den essentiellen Austausch von Informationen zwischen den Netzwerkpartnern und damit zur Unterstützung digitaler Wertschöpfungsnetzwerke benötigt die Co-TWIN-Plattform einen Service, der maßgeblich von der chemmedia AG entwickelt und umgesetzt wird. Die im Maschinen- und Anlagenbau verwendeten Digitalen Zwillinge beschreiben vielfältige Objekte, wie Bauteile, Baugruppen, Maschinen und Anlagen. Für eine maschinenlesbare Beschreibung von Digitalen Zwillingen wurde mit der bereits genannten Verwaltungsschale von der Plattform Industrie 4.0 ein Standard entwickelt, der als „Asset Administration Shell“ veröffentlicht wurde [5]. Er definiert eine gemeinsame Sprache für die Beschreibung eines Industrieguts (Asset). Die digitale Hülle (Shell) enthält dessen Identifikation, Eigenschaften in Form von wiederverwendbaren Submodellen, Zugriffsberechtigungen und Schnittstellen (Commands).
Dieser Service nutzt Asset Administration Shells als standardisierte Datenstruktur für den Austausch zwischen der Co-TWIN-Plattform und den Microservices / IT-Systemen der Anwendungspartner. Somit können Daten unterschiedlicher Struktur und Herkunft (Stammdaten, 3D-Modelle, Sensordaten, Meldungen) von Produkten, Bauteilen oder Anlagen in die Co-TWIN Datenbasis importiert werden. Mithilfe eines eindeutigen Schlüssels werden Daten aus verschiedenen Quellsystemen identifiziert, miteinander verknüpft und zu einem ganzheitlichen Modell aggregiert. Die Anreicherung dieses Datenmodells kann dabei durch alle am Prozess beteiligten Akteure, zum Beispiel Zulieferer, eigene Fertigung oder Kunden erfolgen. Somit wird eine intensivere Kollaboration möglich, wobei jeder dieser Akteure stets seine eigene Sicht auf den gemeinsam genutzten Digitalen Zwilling wählt (Bild 4).
Um diese Möglichkeiten bereitstellen zu können, verfügt die Co-TWIN-Schnittstelle über eine Reihe von Methoden, um Assets in verschiedenen Granularitätsstufen in der Plattform zu verwalten. So können entweder gesamte Assets erstellt, bearbeitet und wieder entfernt oder auch nur auf deren Teilkomponenten zugegriffen werden, um sie zu aktualisieren oder mit anderen Assets zu verknüpfen. Erstellte Asset Shells können Betriebs- und Sensordaten senden und empfangen. Außerdem ist es möglich, Zugriffsrechte und Sichten für andere Akteure zu definieren.
Je nach Anwendungsfall und Zielvorgaben können „Rest“-Webservicemethoden oder „MQTT“-Subscriptions eingesetzt werden (Bild 5).
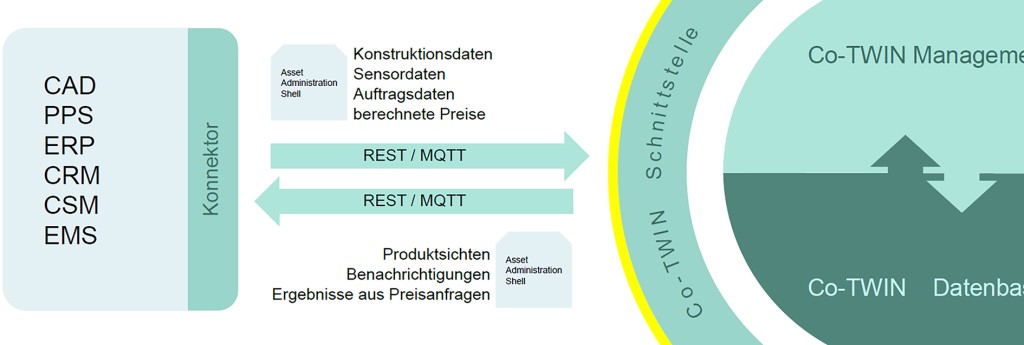
Bild 5. Kommunikation zwischen Softwaresystemen einer Organisation und kollaborativen Digitalen Zwillingen in der Co-TWIN-Plattform.
Foto: chemmedia AG
5 Zusammenfassung und Ausblick
In diesem Beitrag wird der aktuelle Entwicklungsstand der Co-TWIN-Plattform mit den drei Technologieschwerpunkten Virtual Reality, modulare Microservice-Architektur und Verwaltungsschale aufgezeigt. Die Zusammenführung der drei Schwerpunkte zeigt zum einen auf, wie moderne Anwendungsfälle auf der Co-TWIN-Plattform realisiert werden können und zum anderen, wie die Plattform hierfür strukturell aufgebaut werden muss und wie die Kommunikation der Bestandteile gelöst werden kann.
Der lebenszyklus- und wertschöpfungspartnerübergreifende Ansatz der Co-TWIN-Plattform, bei dem moderne digitale Technologien zum Einsatz kommen, hilft dabei, die Vision der Industrie 4.0 im deutschen Mittelstand zu realisieren und damit die Zukunftsfähigkeit des Industriezweigs des Maschinen- und Anlagenbaus am Produktionsstandort Deutschland nachhaltig zu stärken.
Literatur
- Lasi, H.; Fettke, P.; T. Feld, T.; Hoffmann, M.: Industry 4.0, Bus. Inf. Syst. Eng., 6 (2014) 4, pp. 239–242
- Tao, F.; Zhang, M.; Nee, A. Y. C.: Digital Twin Driven Smart Manufacturing. London: Academic Press, 2019
- Wache H.; Dinter, B.: The Digital Twin – Birth of an Integrated System in the Digital Age. In: 53rd Hawaii International Conference on System Sciences, 2020
- Ramm, S.; Wache, H.; Dinter, B. C.; Schmidt, L. S.: Der Kollaborative Digitale Zwilling Herzstück eines integrierten Gesamtkonzepts. ZWF Zeitschrift für Wirtschaftlichen Fabrikbetrieb, 115 (2020) April, pp. 94–96
- Bedenbender, H. et al.: Verwaltungsschale in der Praxis. Berlin, 2019
Das könnte Sie auch interessieren:
Prof. Dr. Barbara Dinter
Hendrik Wache, M. Sc.
Saskia Ramm, M. Sc.
Professur Wirtschaftsinformatik – Geschäftsprozess- und Informationsmanagement
Dipl.-Wirt.-Ing. Eckhart Wittstock
Professur Produktionssysteme und -prozesse
Technische Universität Chemnitz, 09107 Chemnitz, Tel. +49 371 / 531-39228, barbara.dinter@wirtschaft.tu-chemnitz.de, www.tu-chemnitz.de/wirtschaft/wi1/
Dipl.-Wirtsch.-Inf. (BA) Frank Otto
N+P Informationssysteme GmbH, An der Hohen Str. 1, 08393 Meerane, Tel. +49 3764 / 4000-622, otto@nupis.de, www.nupis.de
Dipl.-Wirt.-Inf. Alexander Maasch
chemmedia AG, Parkstr. 35, 09120 Chemnitz, Tel. +49 371 / 49370-170, maasch@chemmedia.de, www.chemmedia.de