Produktionsplanung mit dem digitalen Zwilling
Die Produktionsplanung ist ein zentraler Bestandteil des Produktionsmanagements industrieller Unternehmen. Hieraus resultiert die Wettbewerbsfähigkeit des Wertschöpfungsprozesses, weshalb die Planung so umfassend, präzise und effizient wie möglich sein sollte. Ein hilfreiches Werkzeug ist der digitale Zwilling, der jedoch selten eingesetzt wird. Dieser Beitrag stellt einen Ansatz für die Produktionsplanung durch ein effizientes Erstellen eines digitalen Zwillings vor.
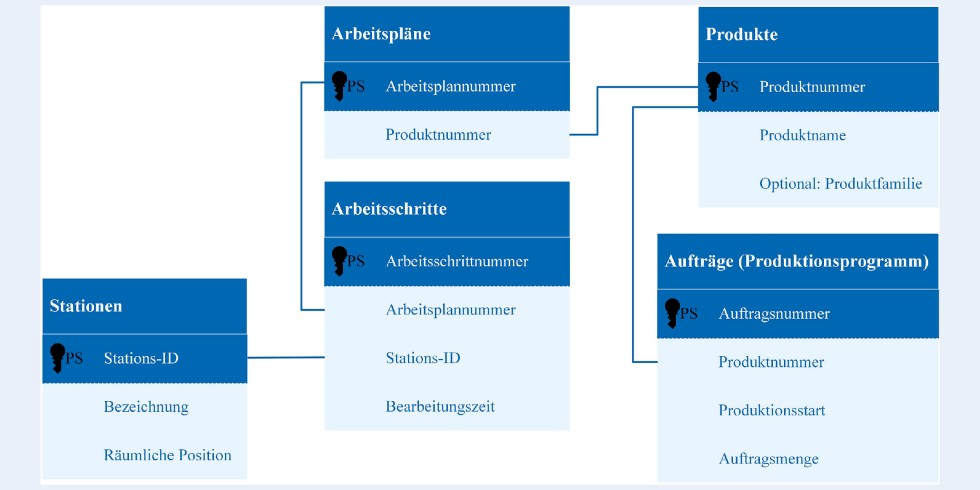
Bild 1. Datenbankmodell. Bild: Leibniz Universität Hannover, IFW
Ausgabe 10-2020 / S. 661
1 Einleitung
In der Produktionsplanung werden Planungsaufgaben durchgeführt, die für die Gestaltung der Produktion notwendig sind. Diese Aufgaben sind zentrale Funktionen eines Industrieunternehmens und entscheidend für die Wettbewerbsfähigkeit [1]. Ziel der Produktionsplanung ist die termin-, kapazitäts- und mengenbezogene Auslegung der Produktionskapazitäten und -ressourcen [2]. Insbesondere sind betriebswirtschaftliche Aufgaben, wie die Mengenplanung, fabrikplanerische Aufgaben, wie die Vorplanung, und technische Aufgaben, wie die Transportsteuerung, als Planungsvorgänge der Produktionsplanung relevant [3]. Für diese Planungsaufgaben werden manuelle, auf Erfahrung basierende Vorgehen oder mathematische Optimierungsverfahren genutzt. Sie können jedoch die zeitdynamischen Interdependenzen der einzelnen Produktionssystemelemente und statisch verteilte Unsicherheiten nicht vollumfänglich berücksichtigen [4, 5].
Aus diesem Grund werden Materialflusssimulationen, die als Kernelement der Digitalisierung gesehen werden, verwendet, um den Materialfluss der Produktion zu planen und so die unternehmerischen Zielgrößen zu erreichen [6]. Für eine Materialflusssimulation wird ein digitales Modell der realen Produktion erstellt, mit dem Experimente virtuell durchgeführt werden, die wiederum Erkenntnisse für den realen Produktionsprozess generieren [3]. Die Anbindung dieses digitalen Modells an das reale System führt zu einem digitalen Zwilling des Produktionssystems. Ein digitaler Zwilling ist dabei definiert als eine digitale Repräsentation, die ausgewählte Merkmale, Eigenschaften, Bedingungen und Verhaltensweisen in Modellen, Informationen und Daten umfasst [7].
2 Problemstellung
Der digitale Zwilling bietet in der Anwendung als Instrument der Produktionsplanung den Industrieunternehmen große Vorteile. Er wird bei der Bewertung, Optimierung sowie Vorhersage genutzt und unterstützt so die eingangs aufgeführten Planungsaufgaben. Jedoch werden die Vorteile, vor allem in kleinen und mittleren Unternehmen (KMU), kaum genutzt, wie eine Studie des Bundesministeriums für Wirtschaft und Energie zeigt [8]. Die Hindernisse liegen vor allem
- in im Vorfeld nicht abschätzbaren Anschaffungskosten,
- in fehlendem Fachwissen in der Informationstechnik,
- am Mangel an Informationen zu Simulationswerkzeugen und
- unbekannten Anwendungsfällen sowie erreichbaren Optimierungspotenzialen [8–10].
Um diese Hindernisse zu überwinden und insbesondere KMU die Verwendung eines digitalen Zwillings zu ermöglichen, wird im Folgenden ein Ansatz vorgestellt, der einen digitalen Zwilling im hohen Grade automatisiert erzeugt und simulationsbasierte Analysen vordefiniert. Planungsaufgaben der Produktionsplanung, die mit diesem Ansatz gelöst werden können, sind
- Fabrikplanung,
- Investitionsplanung,
- Kapazitätsplanung,
- Engpassanalysen,
- Bestandsmanagement und
- Materialflussanalysen [11].
Das Vorgehen wird in diesem Beitrag beispielhaft anhand einer Materialflussanalyse verdeutlicht. Ziel soll sein, ein Sankey-Diagramm als anschaulichen Teil der Materialflussanalyse zu erstellen. Sankey-Diagramme sind Darstellungen von Flüssen, bei denen Pfeile die Flussrichtung und die Dicke der Pfeile mengenproportional die Flussdichte visualisieren.
3 Auslegen der Planungsaufgabe
In mehrstufigen Produktionssystemen entstehen durch asynchrone Prozesse Engpässe und unterschiedliche Materialflüsse, welche in der Produktionsplanung berücksichtigt und ausgelegt werden müssen. Ein hilfreiches Instrument ist hier das Sankey-Diagramm, das den Materialfluss visualisiert. Zur Erstellung des Diagramms werden Eingangsdaten für den abzubildenden Produktionsablauf benötigt. Zentral für das Flussdiagramm ist das Layout des Produktionssystems, welches die jeweiligen Stationen, die ein Produkt durchläuft, enthält und die Oberfläche für das Sankey-Diagramm darstellt. Zur einfacheren Interpretation durch die späteren Anwender ist ein maßstabgetreues Modell des Produktionssystems notwendig.
Die Flüsse des Sankey-Diagramms repräsentieren Produkte, die durch das Produktionssystem laufen. Entsprechend notwendig sind einige Informationen zu den Produkten. Als Mindestanforderung sind dabei die Produktbezeichnungen zu unterscheiden. Zu den einzelnen Produkten werden zusätzlich die Arbeitspläne benötigt, das heißt die Reihenfolge der Arbeitsschritte, die zur Produktion durchgeführt werden müssen, inklusive eines Verweises auf die Stationen, an denen die jeweiligen Produktionsschritte erbracht werden. Weiterhin ist ein Produktionsprogramm nötig.
In Bild 1 werden die oben genannten notwendigen Informationen zusammenfassend in einem Datenbankmodell dargestellt. Die jeweiligen Entitäten sind als Kästen abgebildet. Jede Entität besitzt einen Primärschlüssel (PS), der einen Datensatz eindeutig bezeichnet. Die darunter eingefügten Attribute entsprechen den Spalten in einer zugehörigen Datentabelle.
4 Erstellen des digitalen Zwillings
Für die Erstellung des digitalen Zwillings wird ein Vorgehen verwendet, das im Forschungsprojekt DigiTwin entwickelt wurde. Der Gesamtprozess ist dabei in Bild 2 und Bild 3 dargestellt und wurde ausführlich in [11] publiziert.
Das Produktionssystem wird im ersten Schritt mit einer speziellen Stereokamera mit einer großen Basisweite, einer Handykamera mit Tiefensensor oder Laserscanner gescannt. Das Produktionssystem wird aufgenommen und mit KI-Methoden eine 3D-Punktewolke erzeugt. Weitere Informationen zum Scanprozess wurden in [12] publiziert. Die reine Punktewolke ist aber für die Materialflussanalyse nicht ausreichend, da keine Verbindung zu den Objekten, also beispielsweise Maschinen, besteht. Hierzu müssen Anhäufungen von Punkten identifiziert und interpretiert werden.
Hierzu wird in einem zweiten Schritt eine Objekterkennung durchgeführt. Diese sucht in der Punktewolke nach Clustern, in denen Punkte gehäuft auftreten. Die gefundenen Cluster werden mit einer Referenzdatenbank abgeglichen. In dieser Referenzdatenbank sind typische Objekte von Produktionssystemen abgelegt. Sie wird von den Projektpartnern des Förderprojekts kontinuierlich mit weiteren Objekten befüllt. Der Vergleich von Clustern der Punktewolke mit den Referenzobjekten wird durch ein sogenanntes gefaltetes Neuronales Netzwerk (Convolutional Neural Network) durchgeführt. Details zu diesem Vorgang wurden in [13] publiziert. Ergebnis der Objekterkennung ist eine interpretierte Punktewolke.
Dieses Zwischenergebnis wird im dritten Schritt in ein CAD-Modell übertragen. Das Ergebnis der Objekterkennung wird dabei genutzt, um den identifizierten Objekten eine räumliche Anordnung zuzuweisen. Da die Referenzdatenbank zusätzlich zur Punktewolke auch CAD-Modelle enthält, können diese Modelle in die definierten Standorte der Objekte eingesetzt werden. Durch dieses sukzessive Vorgehen entsteht ein CAD-Modell. An dieser Stelle sei betont, dass bereits dieses Ergebnis einen Mehrwert für viele KMU liefert, die häufig kein CAD-Modell der Produktion besitzen.
Mit dem CAD-Modell wird im vierten Schritt ein Simulationsmodell aufgebaut. Hierzu wird eine XML-Schnittstelle verwendet. Ein Export aus einer CAD-Software erstellt zu diesem Zweck eine XML-Datei, die Informationen für den Simulationsmodellaufbau enthält. Die XML-Datei wird anschließend durch einen Import in die Simulationssoftware eingelesen. Zusätzlich wird in diesem Prozessschritt wieder auf die Referenzdatenbank zugegriffen, um auf in der Datenbank hinterlegte Objektinformationen, wie Maschinendaten, zuzugreifen. Für die Materialflussanalyse liegt nach diesem Prozessschritt somit das Layout vor.
Der fünfte Schritt besteht in der Datenakquise für das Simulationsmodell. Das entwickelte Importwerkzeug stellt die Tabellen zur Verfügung, sodass die benötigten Daten in die Software eingelesen werden können. Mit der Implementierung von Schnittstellen für diesen Vorgang wird das Simulationsmodell definitionsgemäß zum digitalen Zwilling der Produktion, wie in [4] konzeptionell beschrieben. Die Struktur der Daten entspricht dem Datenbankmodell aus Bild 1. So liegen mit Fertigstellung dieses Prozessschritts im Ergebnis alle benötigten Informationen für die Materialflussanalyse vor. Bild 4 enthält eine Übersicht über die beschriebenen Informationen und deren Ursprung.
5 Durchführen der Materialflussanalyse
Mit dem erstellten digitalen Zwilling wird anschließend die Materialflussanalyse durchgeführt. Hierzu wird ein Simulationslauf ausgeführt, der Ergebnisdaten, also Durchlaufrouten und -mengen, erzeugt. Das Sankey-Diagramm wird anhand der Ergebnisdaten erstellt. Hierfür kann eine vorprogrammierte Funktionalität der Simulationssoftware Plant Simulation genutzt werden. An dieser Stelle sei jedoch erwähnt, dass weitere generische Funktionalitäten entwickelt werden, die auch ohne Softwarekenntnisse ausgeführt werden können. Das Sankey-Diagramm wird visuell im Modell dargestellt. Ein Beispiel ist in Bild 5 zu sehen, in dem wegen vertraulichen Details des Produktionssystems des Anwendungspartners, ein fiktives Produktionssystem abgebildet ist.
Die grünen Verbindungspfeile im Bild 5 stellen den Materialfluss dar. Auch wurde in Bild 5 eine Planungsansicht hinzugefügt.
Das Sankey-Diagramm wird schließlich verwendet, um eine Interpretation der Untersuchung durchzuführen und Maßnahmen einzuleiten. Insbesondere
- werden Engpässe an Stellen identifiziert, an denen sich der Materialfluss staut,
- wird das Layout so angepasst, dass gerichtete Materialflüsse entstehen und Transportwege möglichst kurz werden sowie
- der interne Materialtransport ausgelegt, indem zum Beispiel fahrerlose Transportsysteme für hochfrequentierte Transportwege beschafft werden.
Die möglichen Maßnahmen sollten dabei unter Verwendung des digitalen Zwillings in unterschiedlichen Szenarien simuliert und getestet werden.
6 Zusammenfassung und Ausblick
Die Produktionsplanung wird durch den Einsatz eines digitalen Zwillings effizienter, präziser und umfangreicher, sodass vor allem KMU diesen für ihre Planungsaufgaben nutzen sollten. Der vorgestellte Ansatz schafft es, die Hindernisse zu überwinden, die aktuell die Verwendung verhindern. Möglich wird dies durch die geringen Anschaffungskosten, da der digitale Zwilling mit dem vorgestellten Ansatz kostengünstig erstellt werden kann. Lediglich der Scanvorgang wird manuell durchgeführt. Die übrigen vorgestellten Prozessschritte weisen einen fast durchgängig automatisierbaren Prozess auf, der nur durch manuelle Prozesse überwacht und gegebenenfalls korrigiert werden muss. Ebenso ist für die Verwendung kein zusätzliches IT-Wissen oder Kenntnisse über Simulationswerkzeuge notwendig. Die Produktionsplanung wird generisch vordefiniert, sodass eine Anwendung effizient möglich ist und sich Optimierungspotenziale im Vorfeld abschätzen lassen. Das dargestellte Beispiel der Materialflussanalyse lässt sich auf weitere Planungsaufgaben, wie Investitions- oder Kapazitätsplanung, ausweiten.
Die zukünftigen Forschungstätigkeiten konzentrieren sich auf die Erweiterung der Planungsaufgaben. Außerdem werden die einzelnen Prozessschritte laufend optimiert und validiert, sodass ein höherer Automatisierungsgrad erreicht werden kann. Darüber hinaus wird die Referenzdatenbank laufend erweitert, um die Qualität der Objekterkennung zu erhöhen.
Das Forschungsprojekt DigiTwin wird durch das Bundesministerium für Bildung und Forschung (BMBF) in der Fördermaßnahme „KMU-innovativ: Produktionsforschung“ (Förderkennzeichen 02K18K000 bis 02K18K003) gefördert und vom Projektträger Karlsruhe (PTKA) betreut. Die Autoren danken für die Förderung und Unterstützung im Forschungsvorhaben.
Literatur
- Schuh, G.; Stich, V.: Produktionsplanung und -steuerung 1, Grundlagen der PPS. Heidelberg: Springer Vieweg Verlag 2012
- Eversheim, W.: Organisation in der Produktionstechnik, Band 3: Arbeitsvorbereitung. Düsseldorf: VDI Verlag 2002
- VDI-Richtline 3633: Simulation von Logistik-, Materialfluss- und Produktionssystemen. Blatt 5: Integration der Simulation in die betrieblichen Abläufe. Düsseldorf: VDI Verlag 2000
- Donhauser, T.; Endter, U.; Schmidt, T. et al.: Echtzeitabbild der Produktion – Betriebsbegleitende Materialflusssimulation. WT Werkstattstechnik 110 (2020) 4, S. 214–219. Internet: www.werkstattstechnik.de. Düsseldorf: VDI Fachmedien
- Di Domenica, N.; Birbilis, G.; Mitra, G.; Valente, P.: Stochastic Programming and Scenario Generation within a Simulation Framework: An Information Systems Perspective. Decision Support Systems 42 (2007) 4, pp. 2197–2218
- Rudel, S.: Prozess-Simulation in kleinen und mittleren Unternehmen mittels des Bausteinkastensystems KMUSimMetall. In: Wenzel, S.; Peter, T. (Hrsg.): Simulation in Produktion und Logistik. Kassel: university press 2017, S. 433–442
- Stark, R.; Damerau, T.: Digital Twin. In: Chatti, S. et al. (Hrsg.): The International Academy for Production Engineering. CIRP Encyclopedia of Production Engineering. Heidelberg: Springer-Verlag 2019
- Bischoff, J. (Hrsg.): Erschließung der Potenziale der Anwendungen von „Industrie 4.0“ im Mittelstand. Studie im Auftrag des Bundesministeriums für Wirtschaft und Energie (BMWi). Stand: 2015. Internet: www.bmwi.de/Redaktion/DE/Publikationen/Studien/erschliessen-der-potenziale-der-anwendung-von-industrie-4–0-im-mittelstand.html. Zugriff am 19.10.2010
- Denkena, B.; Winter, F.; Hauck, S.: Anlernen von ablauforientierten Simulationsmodellen. ProductivITy 21(2016) 3, S. 52–54
- Weissman, A.; Wegerer, S.: Unternehmen 4.0: Wie Digitalisierung Unternehmen & Management verändert. In: Erner, M. (Hrsg.): Management 4.0. Berlin: Springer-Verlag 2019, S. 43–78
- Denkena, B.; Dittrich, M.-A.; Stobrawa, S.; Stjepandic, J.: Automated Generation of a Digital Twin Using Scan and Object Detection for Data Acquisition. 18. ASIM Fachtagung: Simulation in Produktion und Logistik, Wissenschaftliche Scripten, Auerbach 2019, S. 49–58
- Sommer, M.; Stjepandic, J.; Stobrawa, S.; von Soden, M.: Automatic Generation of Digital Twin ased on Scanning and Object Recognition, Transdisciplinary Engineering for Complex Socio-technical Systems. 26th ISPE Inc. International Conference on Transdisciplinary Engineering, IOS Press, Tokyo 2019, pp. 645–654
- Salem, B.; Stjepandic, J.; Stobrawa, S.: Assessment of Methods for Industrial Indoor Object Recognition. Transdisciplinary Engineering for Complex Socio-technical Systems, 26th ISPE Inc. International Conference on Transdisciplinary Engineering, IOS Press, Tokyo 2019, pp. 390–399
Prof. Dr.-Ing. Berend Denkena, Sebastian Stobrawa, M. Sc. – Institut für Fertigungstechnik und Werkzeugmaschinen, Leibniz Universität Hannover, An der Universität 2, 30823 Garbsen, Tel. +49 (0)511 / 7622553, denkena@ifw.uni-hannover.de, www.ifw.uni-hannover.de; Markus Sommer – isb innovative software businesses GmbH, Otto-Lilienthal-Str. 2, 88046 Friedrichshafen, Tel. +49 (0)7541 / 383414, sommer@isb-fn.de, www.isb-fn.de; Dr. Josip Stjepandic – PROSTEP AG, Dolivostr.11, 64293 Darmstadt, Tel. +49 (0)6151 / 9287363, Josip.Stjepandic@prostep.com, www.prostep.com; Moritz von Soden – Bornemann Gewindetechnik GmbH & Co. KG, Klus 3, 31073 Delligsen, Tel. +49 (0)5187 / 942222, m.vonsoden@bornemann.de, www.bornemann.de