Ressourceneffiziente Zerkleinerungswerkzeuge
Der Beitrag enthält ein innovatives Konzept zur Reduzierung anfallenden Metallschrotts aus Schneidmessern für Schredderanlagen. Die Messer werden durch die Cutmetall Sales GmbH mithilfe eines hybriden Ansatzes nach ihrer Funktion gestaltet. Dabei entwickelt die Drei Bond GmbH ein reversibles Fügeverfahren für die Verbindung mit einem kostengünstigen Träger, auf dem sich die hochverschleißfesten Schneiden befestigen lassen, die mittels additiver Fertigung am Fraunhofer-Institut für Fertigungstechnik und angewandte Materialforschungv IFAM aufgebaut werden. Nach der Abnutzung der Schneiden können so ca. 60 % Messermasse wiederverwendet werden.
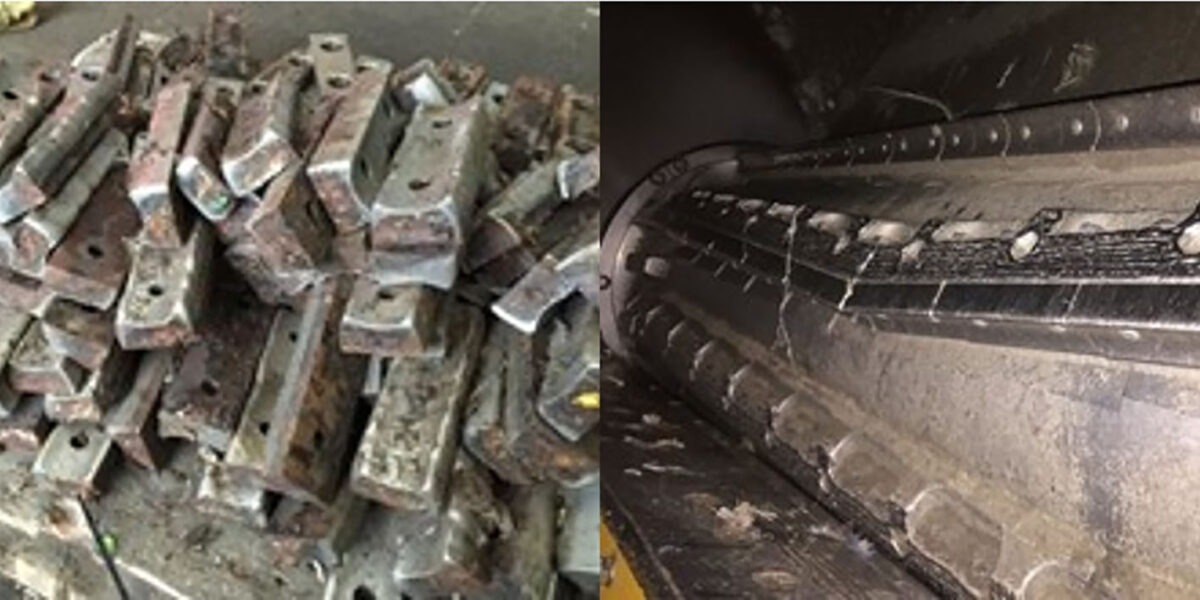
Bild 1. Verschlissene Schneidmesser (links), Schneidwerkzeuge in einer Zerkleinerungsmaschine (rechts), Fotos: Cutmetall Sales GmbH
Improved wear resistance of cutting blades for the production of alternative fuels – Recource-efficient cutting tools
Abstract The article contains an innovative concept for reducing metal scrap from cutting knives for shredding systems. CUTMETALL Sales GmbH uses a hybrid approach to design the knives according to their function. Drei Bond GmbH is developing a reversible joining process for the connection with a cost-effective carrier to which the highly wear-resistant blades can be attached, which are built up using additive manufacturing at Fraunhofer IFAM. After the blades have worn out, around 40% of the blades can be recycled.
Einführung
Die Bedeutung der Müllaufbereitung in Deutschland zeigt sich im überdurchschnittlichen Abfallaufkommen [1]. Trotz politischer Bestrebungen werden mit bislang 53 % des Sperrmülls und nur 16 % des Hausmülls bei Weitem nicht alle Abfälle ausreichend recycelt. Die Notwendigkeit einer nachhaltigen Ressourcennutzung fordert Unternehmen zunehmend, Werk- und Wertstoffe im Kreislauf zu führen. Das Recycling ist dabei technisch sehr herausfordernd und beginnt mit der mechanischen Zerkleinerung. Aufgrund der Heterogenität und Störstoffanfälligkeit des Abfalls, verschleißen die Schneidmesser teilweise schnell, weil aus Kosten- und Effizienzgründen meist nur Werkzeugstahl zum Einsatz kommt. Daher sind häufige Messerwechsel notwendig, die zu erhöhtem Produktionsausfall bzw. Personalaufwand führen. Die Standzeit der Messer liegt je nach Anwendungsfall zwischen 80 h und 600 h bis sie vollständig verschrottet werden. Je nach Anlage werden jedes Mal bis zu über 100 Messer gewechselt. Zudem ist die Ressourceneffizienz niedrig, da die teils nur lokal verschlissenen Messer nach Gebrauch komplett verschrottet werden, Bild 1.
Die Entwicklung recyclebarer Messer mit hoher Standzeit steht daher für die Firma Cutmetall, einer der führenden Hersteller und Distributoren von Industriemessern, Ersatz- und Verschleißteilen [2], im Fokus. Ein Konzept aus einem kostengünstigen und leicht zu bearbeitenden Träger, etwa aus einem Material wie 1.0570 und einer Schneide aus hochfestem, aber noch zähem Kohlenstoffstahl, hier FeCr10V (auch AISI A11 (PM)), bilden die Grundlage des neuen Ansatzes, Bild 2.
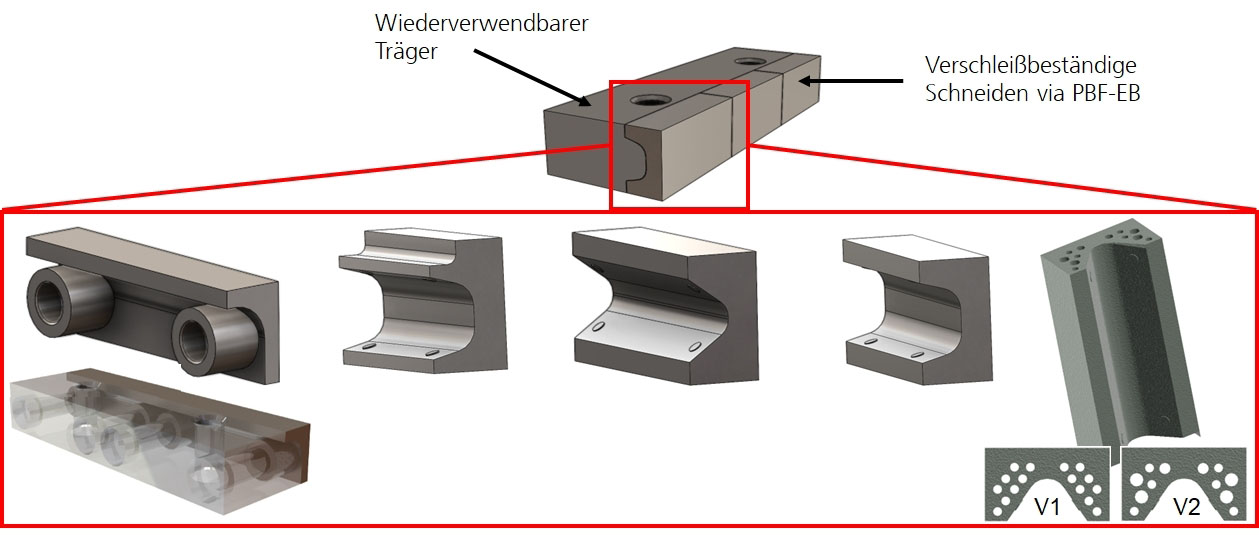
Bild 2. Konzept des hybriden Messers (Maße: 172 x 57 x 28 mm³) aus konventionell hergestelltem wiederverwendbarem Träger und additiv gefertigter Schneide mittels PBF-EB. Hier dargestellt sind erste Schneiden-Varianten, die im Rahmen des Projekts iterativ angepasst werden. Grafik: Fraunhofer IFAM, Designs Cutmetall Sales GmbH
Da die Verarbeitbarkeit des FeCr10V extrem gering ist, arbeitet Cutmetall mit dem Fraunhofer IFAM Dresden zusammen, dass dieses Material mittels Selektivem Elektronenstrahlschmelzen (Powder Bed Fusion by Electron Beam, PBF-EB), einem additiven Fertigungsverfahren, endformnah zu Schneiden verdruckt. Aufgrund der hohen Vorheiztemperaturen von ca. 850 °C kann der Werkstoff rissfrei verarbeitet werden und weist anschließend ein homogenes und feinkörniges Gefüge auf [3].
Aufgrund der hohen mechanischen Beanspruchung der Messer in den Schredderanlagen kommt dem Fügeverfahren eine besondere Bedeutung zu. Neben einer klassischen Verschraubung wird die Firma Drei Bond GmbH, ein Systemanbieter in den Bereichen Hochleistungskleb- und Dichtstoffe sowie Öle und Schmieren [4], eine Klebeverbindung entwickeln, die höchsten Lasten standhält und zudem lösbar ist.
Kritisch sind hier die relativ kleinen Klebespalte zur Übertragung der hohen Lasten und die anschließende Lösbarkeit ohne Verletzung des Trägers. Durch das unweigerliche Einbringen von Störstoffen wie Metalldrähte, Schrauben etc., die wie Geschosse auf die Schneiden wirken, entsteht ein komplexes Beanspruchungsbild.
Ergebnisse
Die Entwicklung erster Schneidenvarianten (siehe Bild 2), die einem Realtest unterzogen werden sollten, erfolgte unter den Randbedingungen des zu erwartenden Verschleißbildes, Bild 3, der einwirkenden Lasten bzw. einer bestmöglichen Belastung der späteren Klebeflächen.
Der Druck der Schneiden erfolgt in der hochtemperaturgeeigneten Elektronenstrahlschmelzanlage „Arcam A2X“ (Colibrium Additive, Tochterunternehmen der GE Aerospace) mit einem gasverdüsten Pulver der Firma Deutsche Edelstahlwerke (Material: PM-V10), wobei die Bauteile auf einer 10 mm dicken Grundplatte mit einer Kantenlänge von 150 mm gedruckt werden. Stützstrukturen zwischen Substrat und Bauteilen sorgen dabei für einen minimierten Verzug der wiederverwendbaren Platte und ein vereinfachtes Entfernen der Bauteile, Bild 4.
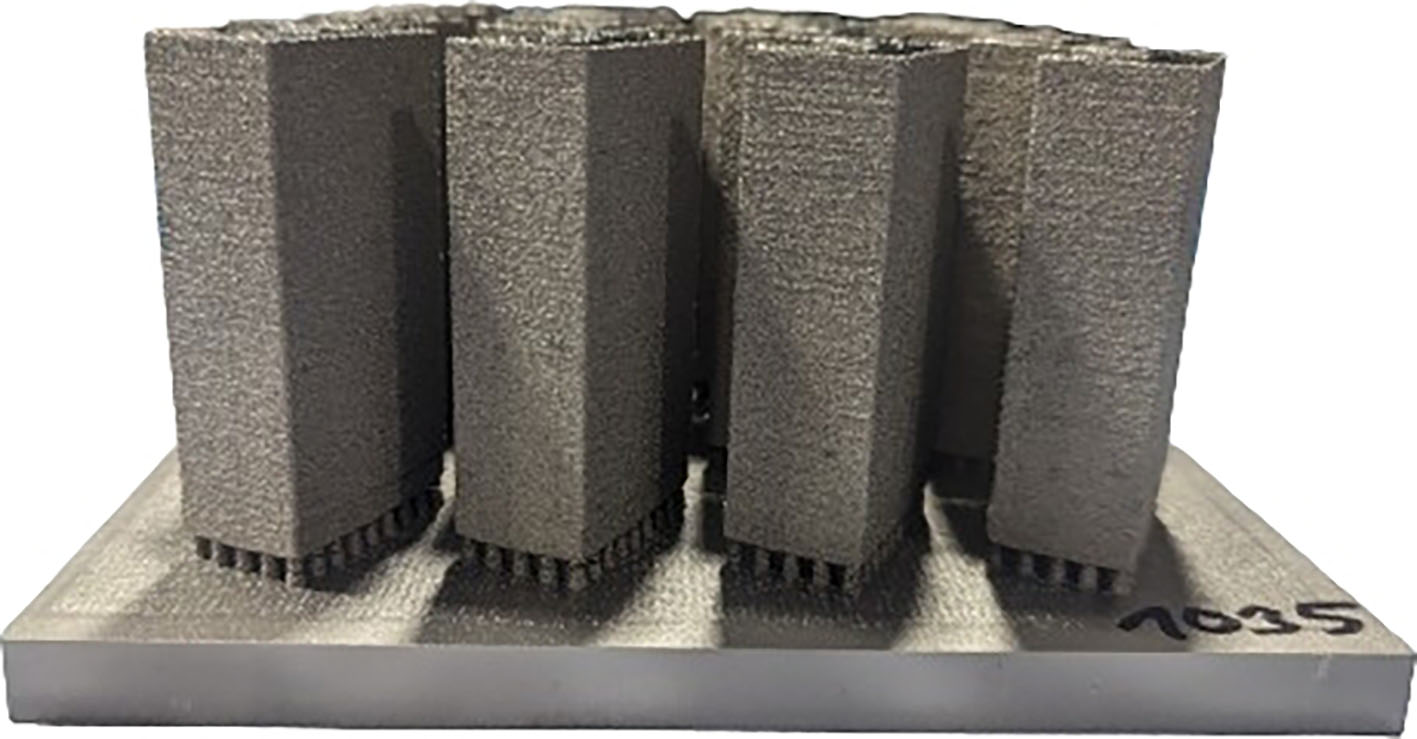
Bild 4. Druck von Schneiden (Maße jeweils: 57 x 28 x 17 mm³) auf einer Grundplatte mit 150 mm Kantenlänge und Säulen-Stützstrukturen zur vereinfachten Entfernung und zur Verzugsminimierung,
Foto: Fraunhofer IFAM
Im gedruckten Zustand liegt die Materialhärte bei etwa 50 ± 3 HRC. Mit einer Härtebehandlung lässt sich die Härte bis über 65 HRC steigern, wodurch es jedoch viel spröder wird. Ein ausgewogenes Verhältnis aus für die Anwendung notwendiger Restzähigkeit und Härte kann über eine Anlassbehandlung erzielt werden, bei der die Teile nach dem Härten erneut oberhalb von 400 °C ausgelagert werden. Ermittelte Biegefestigkeiten liegen oberhalb von 1500 MPa. Das entwickelte zugehörige Anlassschaubild ist in der Bild 5 dargestellt.
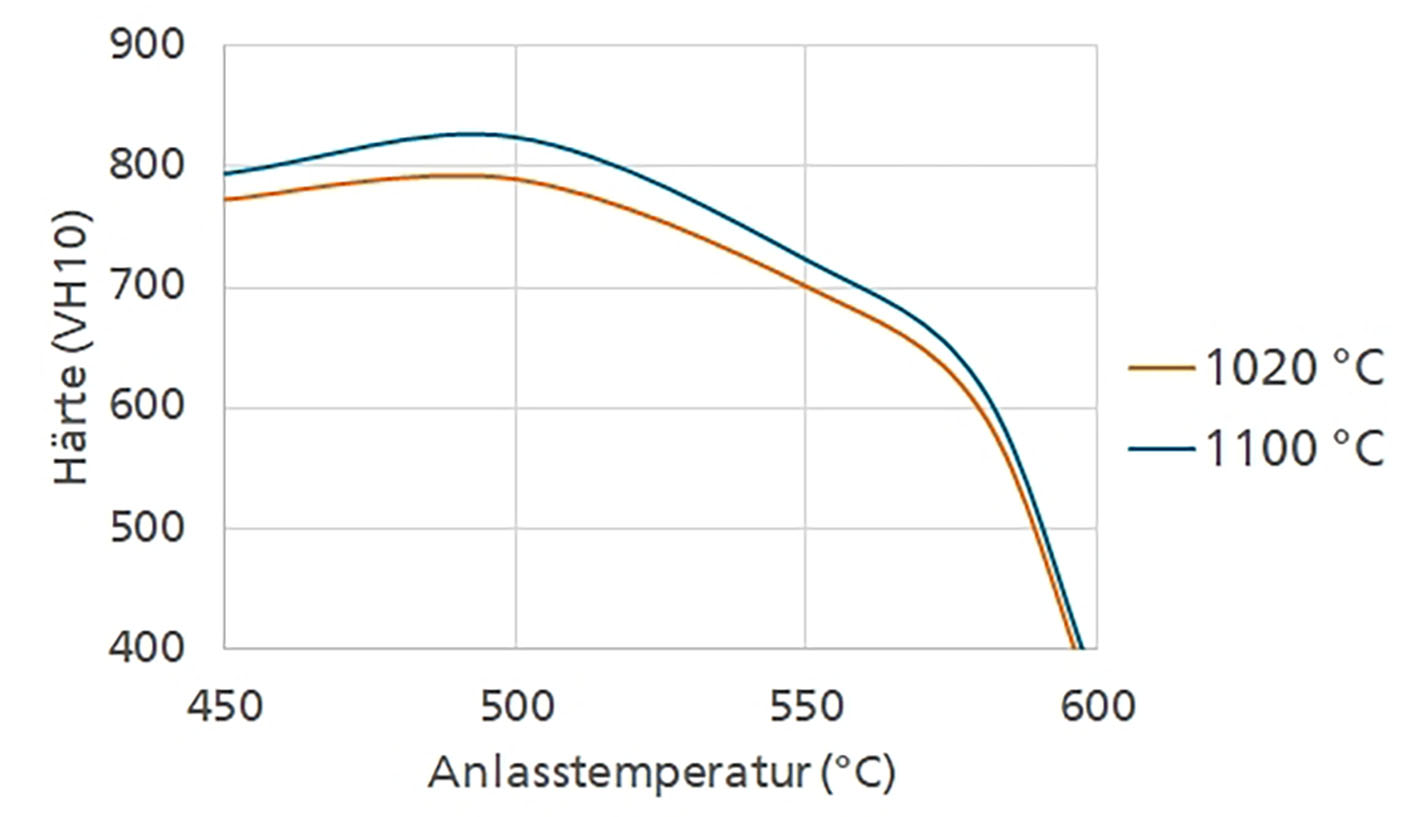
Bild 5. Anlassschaubild des FeCr10V hergestellt via PBF-EB für die Härtetemperaturen 1020 und 1100 °C.
Foto: Fraunhofer IFAM
Eine umfassende Analyse der Praxisversuche erfolgt anhand der drei Wärmebehandlungszustände as-built, gehärtet bei 1020 °C bzw. 1100 °C mit anschließendem zweimaligem Anlassen bei 550 °C für 60 min unter Argon-Schutzgas.
Für die Klebstoffentwicklung wurden quasistatische Druckscher- sowie Schlagfestigkeitsuntersuchungen durchgeführt. Hierbei erfolgt der eigens bei der Drei Bond GmbH entwickelte Versuchsaufbau an geklebten Proben aus dem Träger- (1.0570) und dem Schneidenmaterial (FeCr10V). Für einen im Rahmen des Projekts neu entwickelten Klebstoff konnten in beiden Prüfungen Ergebnisse erzielt werden, die über den Standard hinausgehen. So erreichte die Neuentwicklung auf 1K-epoxy-Basis im Pendelschlagversuch sehr gute Werte von über 40 kJ/m² ohne dabei zu brechen, siehe Bild 6.
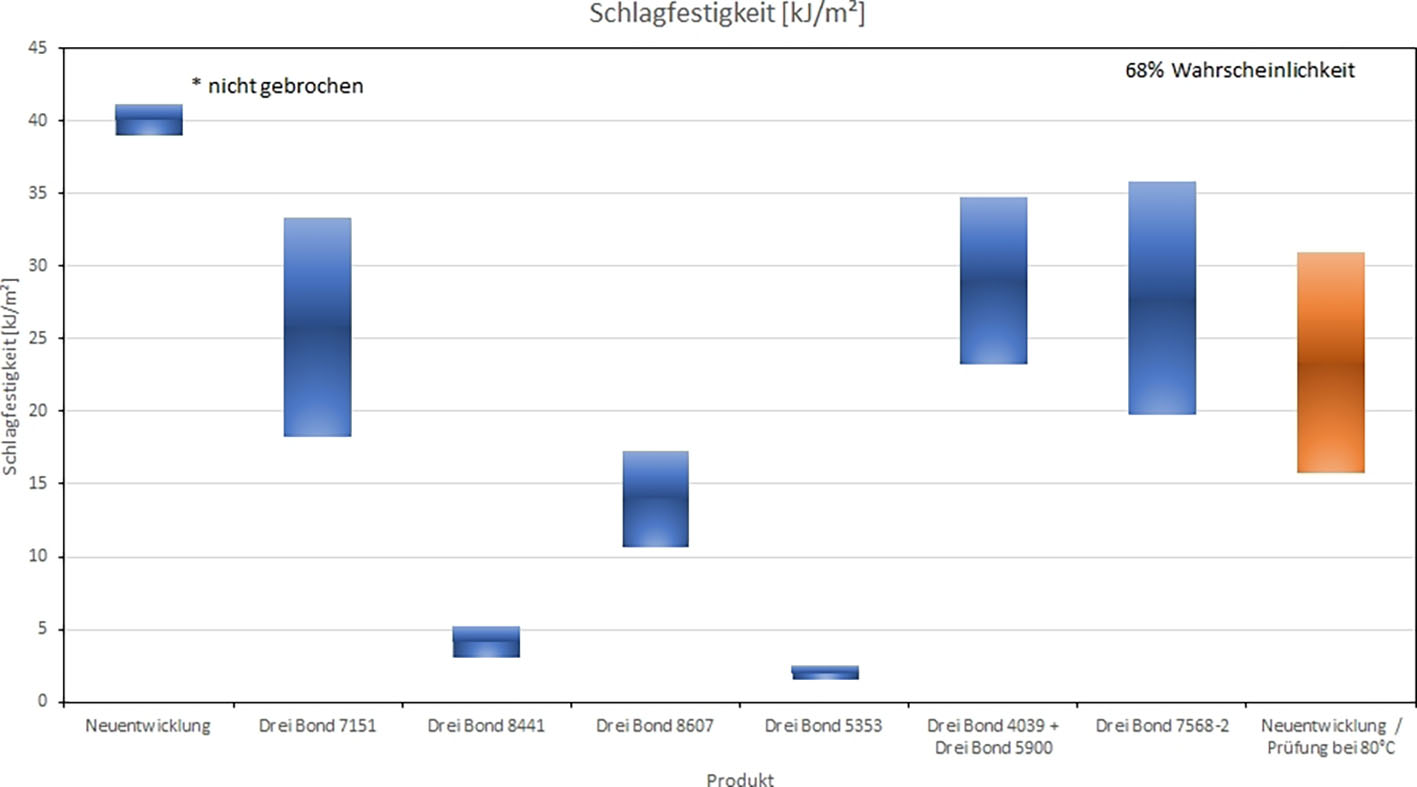
Bild 6. Schlagfestigkeitsprüfung verschiedener Klebstoffe bei Raumtemperatur und für die Neuentwicklung bei 80 °C mit guten Restfestigkeitsverhalten. Grafik: Drei Bond GmbH
Für eine Beurteilung der darüberhinausgehenden Festigkeit kann standardmäßig eine Schwächung der Proben durch Temperatur, hier 80 °C erfolgen. Mit im Mittel immer noch guten 23 kJ/m² liegt das Ergebnis im Bereich der anderen Klebstoffe bei Raumtemperatur. Neben der Zusammensetzung des Klebstoffs scheint auch die Anbindung zu den metallischen Fügepartnern einen Beitrag zur hohen Festigkeit zu leisten. Entsprechend waren aufgrund der vorteilhaften Rauigkeit der mittels PBF-EB gedruckten Proben keine weiteren Oberflächenvorbehandlungen notwendig. Daher sollte die Neuentwicklung im ersten Praxisversuch an echten Schneiden getestet werden.
Das finale Fügen der Schneiden für die Realversuche zeigt Bild 7.
Bei der Klebevariante wurden drei Schneiden pro Träger appliziert, wobei der Klebstoff aufgetragen und in einem Ofen unter Druck und bei einer Peak-Temperatur von 150 °C für 30 min ausgehärtet wurde.
Der Praxistest erfolgte in Paderborn bei der Pader Entsorgung GmbH. Hierbei wurden acht Messerhalter auf dem Stator mit je zwei Messern bestückt und nach jeweils 5 h eine optische Kontrolle durchgeführt. Nach manueller Einstellung des Nullspaltes bei 30 U/min, konnten die Maschine auf 250 U/min hochgefahren, Abfälle hinzugefügt und schließlich Ersatzbrennstoffe erzeugt werden, siehe Bild 8.
Ein Versagen aller Schneiden trat nach immerhin etwa 3 Mio. Schnittvorgängen bzw. Schlägen auf die Messer auf, wobei in der Regel die Fügeverbindung versagte. Bis dahin war im Vergleich zu Standardmessern ein geringerer Verschleiß der Schneiden zu beobachten.
Zusammenfassung
Aus den vorgestellten Ergebnissen des vom Bundesministerium für Bildung und Forschung geförderten Projekts „ReHaRecy“ wird ersichtlich, dass die Verwendung von hochverschleißfestem FeCr10V für Recyclingwerkzeuge zielführend ist. Ein derartiges Messerkonzept kann bis zu 40 % an Material einsparen. Da das Schneidenmaterial härtbar ist, kann die Restzähigkeit auf den Einsatzfall angepasst werden. Die Fügeverbindung lässt sich ohne weitere Oberflächenvorbereitung erzeugen und bietet mit Werten von über 40$kJ/m² eine beachtliche Festigkeit. Die Praxisversuche führten zu einer Standzeit von über 3 Mio. Schnittvorgängen. Noch erreichen die Fügeverbindungen jedoch nicht die gewünschten Laufzeiten. Zum Vergleich entspricht eine solche Lastzyklenzahl durchaus einer Lebenszeit in Klebstoffstandardanwendungen. Ein erfolgreicher Einsatz von Klebstoffen in Zerkleinerungsmaschinen kann daher als Königsklasse bezeichnet werden.
Ausblick
Die Ergebnisse sind als Grundlage für eine iterative Anpassung des Schneiden-Designs hin zu größeren Klebspalten und höheren Belastbarkeiten zu sehen, die in einem weiteren Test im Lauf der Projektlaufzeit evaluiert werden sollen. Hierbei wird auch stärker auf die geometrischen Freiheiten der Additiven Fertigung geachtet, die das Potential bieten, ohne Mehraufwand eine größere Schnittfläche bereitzustellen oder gar nachschärfende Elemente einzubringen. Neue PBF-EB-Anlagentechnik verspricht zudem größere Bauplattformen, sodass ein jährlicher Aufbau von etwa 10.000 Schneiden realistisch ist.
Dieses Forschungs- und Entwicklungsprojekt „ReHaRecy – Ressourceneffiziente Herstellung hybrid-additiver Recyclingwerkzeuge” wird mit Mitteln des Bundesministeriums für Bildung und Forschung (BMBF) im Programm „Zukunft der Wertschöpfung – Forschung zu Produktion, Dienstleistung und Arbeit“ (Förderkennzeichen 02P22K020 bis 02P22K022) gefördert und vom Projektträger Karlsruhe (PTKA) betreut. Die Verantwortung für den Inhalt dieser Veröffentlichung liegt beim Autor.
Literatur
- Internet: https://ec.europa.eu/eurostat/databrowser/view/env_wasmun/default/bar?lang=de. Zugriff am 07.08.2024
- Internet: https://www.cutmetall.com/, zuletzt geprüft am 07.08.2024
- Franke-Jurisch, M.; Mirz, M.; Wenz, T.; Kirchner, A.; Klöden, B.; Weißgärber, T.: PBF-EB of Fe-Cr-V Alloy for Wear Applications. In: Materials 2022, 15, 1679. https://doi.org/10.3390/ma15051679
- Internet: https://dreibond.de/. Zugriff am 07.08.2024
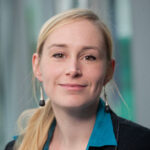
Dr. rer.nat. Florian Menk
Drei Bond GmbH
Carl-Zeiss-Ring 13, 85737 Ismaning
Dr.-Ing. Marie Franke-Jurisch
Foto: Autorin
Fraunhofer-Institut für Fertigungstechnik
und Angewandte Materialforschung IFAM
Teilinstitut Dresden
Winterbergstr. 28, 01277 Dresden
marie.franke-jurisch@ifam-dd.fraunhofer.de
www.ifam-dd.fraunhofer.de
Michael Oeffner
CUTMETALL Sales GmbH
Industriering 24 , 96149 Breitengüßbach
Dr.-Ing. Alexander Kirchner
Fraunhofer-Institut für Fertigungstechnik
und Angewandte Materialforschung IFAM
Teilinstitut Dresden
Winterbergstr. 28, 01277 Dresden
www.ifam-dd.fraunhofer.de