Selbstlernende Werkzeugmaschine für die Einzelstückfertigung
Die steigende Nachfrage nach kundenspezifischen Produkten mit kleinen Losgrößen stellt die Fertigungsindustrie vor neue Herausforderungen, die nur durch hochautomatisierte Prozesse bewältigt werden können. Als wichtiger Teil der Prozesskette können autonome Werkzeugmaschinen dazu beitragen, diese Anforderungen zu erfüllen. Das Verbundprojekt AICoM erforscht daher die Entwicklung einer selbstlernenden und autonomen Werkzeugmaschine.
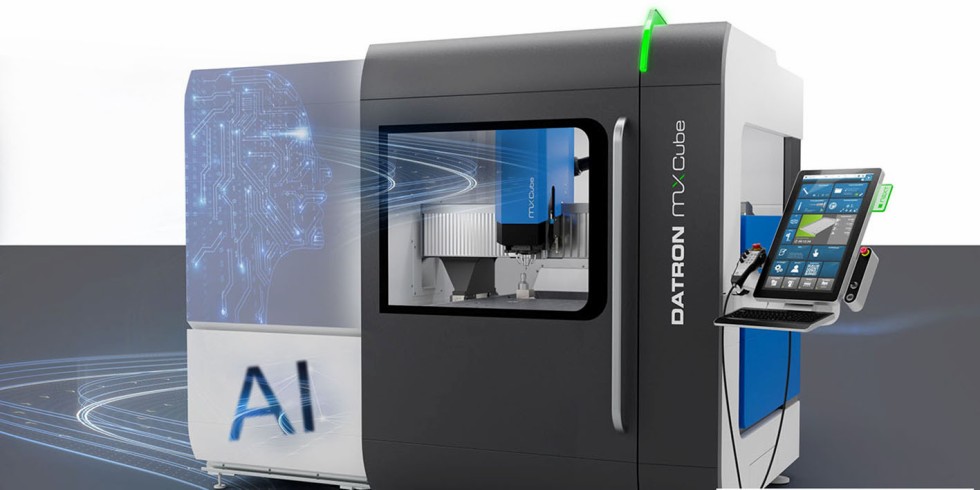
Bild 1. „AICoM“-Demonstrator mit Übersicht der Projektpartner. Grafik: PTW & Datron AG
Self-Learning Machine Tool for One-off Production
Abstract: The increasing demand for customized products with small batch sizes poses new challenges for the manufacturing industry, which can only be met by highly automated processes. As an important part of the process chain, autonomous machine tools can help to meet these requirements. Therefore, the joint project AICoM is researching the development of a self-learning and autonomous machine tool.
1 Einleitung & Motivation
Moderne Werkzeugmaschinen (WZM) für die spanende Bearbeitung sind hochautomatisierte Fertigungsmittel, für deren kosteneffizienten Einsatz ein hohes Maß an Prozessverständnis und Prozessplanung mit entsprechender Anwenderqualifikation erforderlich ist. Insbesondere bei kleinen Losgrößen und teuren Werkstücken erfolgt die Fertigung mit konservativ gewählten Prozessparametern, die weit unterhalb des Produktivitätsoptimums liegen. Dies beruht einerseits auf der Tatsache, dass für die Fertigung auf das technologische Verständnis und die Erfahrung des Maschinenbedieners zurückgegriffen wird und andererseits beim Nutzer kein nachhaltiges Prozessverständnis aufgrund stark variierender kundenindividualisierter Produkte gebildet werden kann. Der Einsatz von Industrie 4.0-Technologien in der WZM kann den Nutzer bereits bei der Optimierung ausgewählter Prozessparameter durch die Visualisierung von Messdaten aus maschineninterner Sensorik zusammen mit Warnschwellen am Bedienpult unterstützen [7, 8]. Um jedoch auch eine Optimierung der Prozessplanung zu ermöglichen, müssen die Informationen aus den Messdaten mit anderen vor- und nachgelagerten Teilprozessen der Fertigung zum Beispiel dem CAM-System und dem Qualitätsmanagement verknüpft werden. Aktuell werden die Steuerbefehle der WZM in Form von NC-Programmen übergeben, die speziell bei komplexeren Werkstücken zuvor offline in CAM-Systemen zeitaufwendig generiert wurden. Neben dem hohen nötigen Expertenwissen für deren Bedienung fehlen den CAM-Systemen ebenfalls Informationen über die Werkzeugmaschine, wie zum Beispiel Maschinenzustand, Werkzeuge und Aufspannsituation. Darüber hinaus besitzen aktuelle Maschinensteuerungen nicht die Fähigkeiten, mögliche Prozessunsicherheiten zu erkennen, zu interpretieren und selbstständig Gegenmaßnahmen einzuleiten. Dadurch werden die Potenziale von WZM nicht vollständig ausgenutzt. In Unternehmen besteht somit der Bedarf an intelligenten, lernenden und intuitiv zu bedienenden WZM, mit der Fähigkeit selbstständig Fertigungsprozesse nach kundenindividuellen Anforderungen zu planen und durchzuführen.
2 Verbundprojekt AICoM
Die vom Bundesministerium für Bildung und Forschung veröffentlichte Bekanntmachung: „Lernende Produktionstechnik – Einsatz künstlicher Intelligenz (KI) in der Produktion“ fokussiert die Erhöhung der Leistungsfähigkeit und Funktionalität von Maschinen und Ausrüstungen der Fertigungstechnik durch den verstärkten Einsatz von KI. In diesem Rahmen startete im Juni 2021 das Projekt „AICoM“ mit dem Ziel eine lernende Werkzeugmaschine zur autonomen Fertigung kundenindividueller Werkstücke zu entwickeln. Das Konsortium besteht aus sechs Unternehmenspartnern (davon vier kleine und mittlere Unternehmen) aus den Bereichen Werkzeug- und Maschinenherstellung, NC-Kernel und CAM-Modul Entwicklung sowie KI-Software-Entwicklern. Zusätzlich komplettieren zwei Forschungsinstitute der Technischen Universität Darmstadt das Konsortium, um die zugrundeliegenden Forschungsfragestellungen für AICoM zu beantworten. Eine vollständige Übersicht aller Projektpartner ist in Bild 1 dargestellt.
AICoM steht als Akronym für „Artificial Intelligence controlled Milling“ und bildet das Herzstück der geplanten Entwicklungen. AICoM ist eine KI-basierte modular aufgebaute System- und Steuerungsarchitektur, welche im Zusammenschluss mit einer Werkzeugmaschine das Gesamtsystem einer lernenden Werkzeugmaschine erschafft. Das Gesamtsystem wird in die Lage versetzt, den Prozess autonom anzupassen und auf erlerntes „Wissen“ beziehungsweise erlernte „Erfahrung“ zurückzugreifen. Je nach Zielstellung kann die lernende Werkzeugmaschine sich schließlich während dem Prozess an die aktuellen Randbedingungen anpassen.
3 Ziele des Forschungsprojekts
Ziel des Forschungsvorhabens AICoM ist die Entwicklung einer lernenden Werkzeugmaschine für die spanende Fertigung. Dies soll durch die Integration von neuartigen Methoden der KI in die WZM erfolgen. Ein 3D-Modell inklusive Qualitätsanforderungen wird der Maschine übergeben und anschließend unter Berücksichtigung von Zielgrößen automatisiert gefertigt. Mit der zu entwickelnden KI-basierten Prozessregelung adaptiert sich die WZM selbstständig auch bei verändernden Prozessbedingungen an die vom Nutzer gewählte Zielgröße. Bei erfolgreichem Projektabschluss ermöglicht AICoM eine signifikant vereinfachte Maschinenbedienung bei einer erhöhten Produktivität und verkürzten Anlaufzeiten. Zusätzlich wird durch die In-Prozess Adaption die Qualität der Produkte erhöht und die Anzahl der Ausschussteile drastisch reduziert. Erreicht wird dies durch die Entwicklung von AICoM, das auf Basis von KI automatisiert die Steuerbefehle für die Fertigung des gewünschten Werkstückes generiert. Dabei greift AICoM auf aktuelle und historische Prozessinformationen (Wissensspeicher) zurück. Bild 2 zeigt die beiden zugrundeliegenden Regelkreise. Der innere Echtzeitregelkreis beziehungsweise der echtzeitnahe Regelkreis greifen in den Fertigungsprozess ein. Die im Zentrum stehende KI wird befähigt neben den Prozessparametern ebenfalls die zuvor berechneten Bahnpunkte während des Fertigungsprozesses anzupassen, um auf etwaige Änderungen von Maschinenzuständen reagieren zu können. Die dazu notwendigen Informationen werden AICoM durch aufbereitete maschineninterne beziehungsweise externe Sensordaten sowie durch ein skalierbares und echtzeitfähiges Prozessmodell zurückgeführt.
W_BMBF_AICoM_Sarikaya_Bild 2.jpgDer äußere Erfahrungs-Regelkreis ermöglicht der Maschine das Lernen aus Erfahrungen und damit den Aufbau von Prozesswissen. Dies geschieht durch Aufnahme und Kontextualisierung von Daten aus unterschiedlichen Quellen. Insbesondere die Korrelation von Motorströmen der Spindel und Bewegungsachsen, Schleppfehler sowie Bahngeschwindigkeit in Bezug auf die Position im Bearbeitungsprogramm gibt einen detaillierten Eindruck, ob die Prozessparameter optimal gewählt wurden. In Kombination mit simulierten Zerspanvolumina aus dem integrierten CAM-System entsteht so eine Erfahrungsdatenbank zu Prozessparametern, angepasst auf die jeweilige Maschine und Konfiguration. Für die Generierung der Erfahrung im Erfahrungsregelkreis kommen neu zu entwickelnde Verfahren des automatisierten Maschinellen Lernens (AutoML) zum Einsatz. Diese sind neben der automatischen Auswahl der Algorithmen in der Lage die Merkmalauswahl (Feature Engineering) und Datenbereinigung (Data Cleaning) zu automatisieren. Ziel dabei ist es, die Zusammenhänge zwischen den Datenströmen zu erkennen und passende Vorhersagemodelle zu erstellen und den Wissensspeicher beziehungsweise die Erfahrung stetig wachsen zu lassen. Um die Algorithmen noch schneller zu verbessern, werden zusätzlich Verfahren zur künstlichen Erweiterung der Trainingsdaten (Data Augmentation) entwickelt und eingesetzt [9–11]. Für die automatisierte Prozessplanung kann AICoM auf die Erfahrung aus vorangegangenen Aufträgen zurückzugreifen, womit die intelligente Maschine befähigt wird, sich ständig zu verbessern und automatisiert die Fertigungsprozesse zu optimieren. Diese Innovation legt den Grundstein für die selbstlernende und adaptierende Werkzeugmaschine. Das Domänenwissen der Experten wird somit in die Maschinen gespiegelt, womit die steigende Komplexität und die hohe notwendige Anpassungsfähigkeit an sich immer ändernde Umstände bei kleinen Losgrößen und kurzen Innovationszyklen für den Nutzer beherrschbar werden.
4 Systemarchitektur zur Intelligenten Prozessplanung
Der Erfahrungsregelkreis ist verantwortlich für die automatisierte Prozessplanung auf Basis von kundenspezifischen CAD-Informationen und Produktanforderungen. Zunächst wird die geometrische Information durch einen Feature-Erkennungsalgorithmus verarbeitet, der die Werkstücktopologie untersucht und in ihre geometrischen Merkmale wie planare Flächen, Taschen, Nuten und Bohrungen unterteilt [12]. Gemäß STEP-NC hat jede Geometrie ihre selbstbeschreibenden Attribute, die das geometrische Merkmal vollständig charakterisieren. Basierend auf diesen Attributen wurde ein hierarchisches Informationsmodell erstellt, das die CAM-Software für die Werkzeugauswahl benötigt.
Wie in Bild 3 dargestellt, erfolgt die endgültige Werkzeugauswahl zusammen mit den entsprechenden Schnittparametern durch das Prozessplanungsmodul [13]. Typischerweise enthält jedes Werkzeug herstellerspezifische Angaben über den Bereich der empfohlenen Schnittparameter. Dies liefert bereits einen vordefinierten Bereich, in dem die Prozessplanung die technologischen Parameter optimieren kann. Die Ausgabe des Moduls beschreibt die Strategie, die verwendeten Werkzeuge und die technologischen Parameter für die CAM-Software, welche die jeweiligen Operationen erstellt. Im Rahmen der Prozesssimulationsschleife, die in Bild 3 grün dargestellt ist, wird die erstellte Operation im KI-basierten Simulationsmodell verarbeitet, um zukünftig die Zielgrößen Werkstückqualität, Bearbeitungszeit und Effizienz in Bezug auf den Ressourcenverbrauch vorherzusagen. Im derzeitigen Fokus steht lediglich die Werkstückqualität. Die modellbasierte Vorhersage wird als Feedback verwendet, um die Prozessplanung zu einer optimalen Lösung zu führen.
![Bild 3. Intelligente Systemarchitektur der selbstlernenden autonomen Werkzeugmaschine, gemäß Sarikaya et al. [13]. Grafik: PTW aus [13]](https://www.ingenieur.de/wp-content/uploads/2023/06/W_BMBF_AICoM_Sarikaya_Bild-3.jpg)
Bild 3. Intelligente Systemarchitektur der selbstlernenden autonomen Werkzeugmaschine, gemäß Sarikaya et al. [13]. Grafik: PTW aus [13]
Dieses Verfahren wird für alle erkannten geometrischen Merkmale des Werkstücks durchgeführt. Der Postprozessor generiert anschließend das NC-Programm für die WZM. Dabei reichert der Postprozessor das NC-Programm mit zusätzlichen Metainformationen an, so dass eine Zuordnung der erfassten Prozessdaten sowohl werkzeug-, als auch feature- und bauteilbasiert möglich ist. Dadurch entsteht während des normalen Produktionsbetriebs eine strukturierte Datenbasis, welche in Zukunft auch das Training weiterer KI-Modelle ermöglichen soll.
Wenn die WZM in den Betriebsmodus wechselt, übernimmt der echtzeitfähige innere Regelkreis die Kontrolle. Hier werden Maschinendaten in Echtzeit verarbeitet, um Prozessunsicherheiten auszugleichen. Nach dem Bearbeitungsprozess wird eine Qualitätskontrolle entweder manuell oder mittels Koordinatenmessgerät durchgeführt. In beiden Fällen müssen die Qualitätsdaten in die Datenbank integriert werden, um sie mit der vorhergesagten Zielgröße, in dem Fall Werkstückqualität, des Simulationsmodells vergleichen zu können. Schließlich wird im Zyklus jedes produzierten Werkstücks das KI-basierte Prozessmodell neu antrainiert.
5 Fazit und Ausblick
Das Verbundprojekt AICoM, bestehend aus Werkzeug- und Maschinenherstellern, NC-Kernel und CAM-Modul Entwicklern sowie KI-Software-Experten, leistet einen wichtigen Beitrag für die Entwicklung und Erforschung von selbstlernenden und autonomen Werkzeugmaschinen. Die vorgestellte Systemarchitektur beschreibt einen industrienahen Ansatz, welcher keine Sonderlösung darstellt und somit auch auf weitere Anwendungen übertragen werden kann.
In aktuellen Arbeiten wird das Konzept und die Systemarchitektur in einer Demonstratormaschine implementiert und anschließend prototypisch in Betrieb genommen. Dabei werden bereits alle relevanten Daten an der Demonstratormaschine erfasst, so dass eine kontinuierlich wachsende Datenbasis über reale Produktionsdaten entsteht. Diese Datenbasis wird derzeit für das Training erster KI-Modelle herangezogen. Die einzelnen Module müssen im weiteren Prozess ganzheitlich als zusammenwirkendes System validiert werden.
Dieses Forschungs- und Entwicklungsprojekt wird mit Mitteln des Bundesministeriums für Bildung und Forschung (BMBF) im Programm „Zukunft der Wertschöpfung – Forschung zu Produktion, Dienstleistung und Arbeit“ (Förderkennzeichen 02P20A060 bis 02P20A065) gefördert und vom Projektträger Karlsruhe (PTKA) betreut. Die Verantwortung für den Inhalt dieser Veröffentlichung liegt bei den Autoren.
Literatur
- Statistisches Bundesamt: Inlandsproduktsberechnung – Vierteljahresergebnisse – Fachserie 18 Reihe 1.2 – 3. Vierteljahr 2022 (2022), S. 18
- Reip, M.: Komplexe Herausforderungen an produzierende Unternehmen. Internet: https://www.vdi-wissensforum.de/news/komplexe-herausforderungen-an-produzierende-unternehmen/. Zugriff am 03.02.2020
- Spath, D. (Hrsg.): Produktionsarbeit der Zukunft – Industrie 4.0. Studie. Stuttgart: Fraunhofer-Verl. 2013
- Abele, E.; Reinhart, G.: Zukunft der Produktion. Herausforderungen, Forschungsfelder, Chancen. s.l.: Carl Hanser Fachbuchverlag 2011
- Knitterscheidt, K.: Mit neuer Technologie sollen deutsche Fabriken so günstig produzieren wie in China. Internet: https://www.handelsblatt.com/technik/hannovermesse/intelligente-hallen-mit-neuer-technologie-sollen-deutsche-fabriken-so-guenstig-produzieren-wie-in-china/24179716.html?ticket=ST-1068280-dTcVfChQC4rx4H1cDj6q-ap3. Zugriff am 03.02.2020
- Schenk, M.: Digitale Intelligenz im Maschinen- und Anlagenbau. 23. Industriearbeitskreis 2015 Kooperation im Anlagenbau. Internet: https://www.iff.fraunhofer.de/content/dam/iff/de/dokumente/publikationen/industriearbeitskreis-anlagenbau-2015–22–23-arbeitsbericht-fraunhofer-iff.pdf. Zugriff am 03.02.2020
- CELOS Apps – Monitoring. Internet: https://celos.dmgmori.com/de/3-apps.html#section-41. Zugriff am 05.02.2020
- promicron wireless solutions: spike_easyinline. Kräfte messen direkt am Werkzeug. Internet: https://www.pro-micron.de/spike/. Zugriff am 05.02.2020
- Bach, S. H.; Rodriguez, D.; Liu, Y. et al.: Snorkel DryBell: A Case Study in Deploying Weak Supervision at Industrial Scale. Proceedings. ACM-Sigmod International Conference on Management of Data 2019 (2019), pp. 362–375
- Kotthoff, L.; Thornton, C.; Hoos, H. H. et al.: Auto-Weka 2.0: Automatic model selection and hyperparameter optimization in Weka. Journal of Machine Learning Research 18 (2017) 25, S. 1–5
- Nathaniel Weir et al.: DBPal: Weak Supervision for Learning a Natural Language Interface to Databases. Proceedings. ACM-Sigmod International Conference on Management of Data 2020 (2020)
- ISO International Organization for Standardization: ISO 14649–10:2004–12. ISO 14649–1: Industrial automation systems and integration – Physical device control; Data model for computerized numerical controllers – Part 1: Overview and fundamental principles. 2003–03
- Sarikaya, E.; Fertig, A.; Öztürk, T. et al.: An Implementational Concept of the Autonomous Machine Tool for Small-Batch Production. In: Liewald, M.; Verl, A.; Bauernhansl, T. et al. (Hrsg.): Production at the Leading Edge of Technology. Cham: Springer International Publishing 2023, S. 535–544
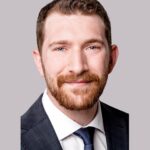
W_BMBF_AICoM_Autor Sarikaya.jpgErkut Sarikaya, M. Sc.
Foto: TU Darmstadt / PTW
Prof. Dr.-Ing. Matthias Weigold
Technische Universität Darmstadt
Institut für Produktionsmanagement
Technologie und Werkzeugmaschinen (PTW)
Otto-Berndt-Str. 2, 64287 Darmstadt
Tel. +49 6151 8229-758
e.sarikaya@ptw.tu-darmstadt.de
www.ptw.tu-darmstadt.de
Eduardo Reis
Prof. Dr. Carsten Binnig
Data and AI Systems
Hochschulstr. 10, 64289 Darmstadt
carsten.binnig@cs.tu-darmstadt.de
www.informatik.tu-darmstadt.de/systems/systems_tuda/dai
Dr. Dipl.-Ing. Steffen Lan
Gühring KG
Hahnstr. 53, 72461 Albstadt
Tel. +49 7431 17 25-474
steffen.lang@guehring.de
www.guehring.de
Dr. rer. nat. Valentina König
ModuleWorks GmbH
Henricistr. 50, 52072 Aachen
Tel. +49 241 990004687
valentina@moduleworks.com
www.moduleworks.com
Dipl.-Ing. Tim Hoyer
ISG Industrielle Steuerungstechnik GmbH
Gropiusplatz 10, 70563 Stuttgart
Tel. +49 711 22992 56
tim.hoyer@isg-stuttgart.de
www.isg-stuttgart.de
Volker Marquardt
Synop Systems UG (haftungsbeschränkt)
Fichtenstr. 7, 71088 Holzgerlingen
Tel. +49 721 94538 11
marquardt@synop-systems.com
www.synop-systems.com
Dipl.-Ing (FH) Andreas Hoffmann
Lorenz Hoffmann GmbH
Am Grund 4, 74594 Kreßberg-Oberstelzhausen
Tel. +49 795 924930
andreas.hoffmann@hoffmanngmbh.com
www.hoffmanngmbh.com
Dipl.-Ing. Patrick Gunsch
Datron AG
In den Gänsäckern 5, 64367 Mühltal
Tel. +49 6151 1419 449
patrick.gunsch@datron.de
www.datron.de