Stabile Antireflex-Beschichtungen für die Medizintechnik
Optische Bauteile in der Medizintechnik unterliegen stetig steigenden Anforderungen an die Effizienz und Qualität. Um die Lichtausbeute der Optiken zu steigern, sowie das Auftreten von Geisterbildern zu vermeiden, sind Antireflex-Beschichtungen unverzichtbar. Jedoch unterliegen diese meist extremen Anforderungen bezüglich mechanischer und chemischer Beständigkeit. In einem gemeinsamen vom BMBF geförderten Projekt wurden Antireflex-Beschichtungen für Endoskopfenster entwickelt, die gegenüber Reinigungs-, Desinfektions- sowie Sterilisationsprozessen, wie sie im Krankenhaus angewendet werden, beständig sind.
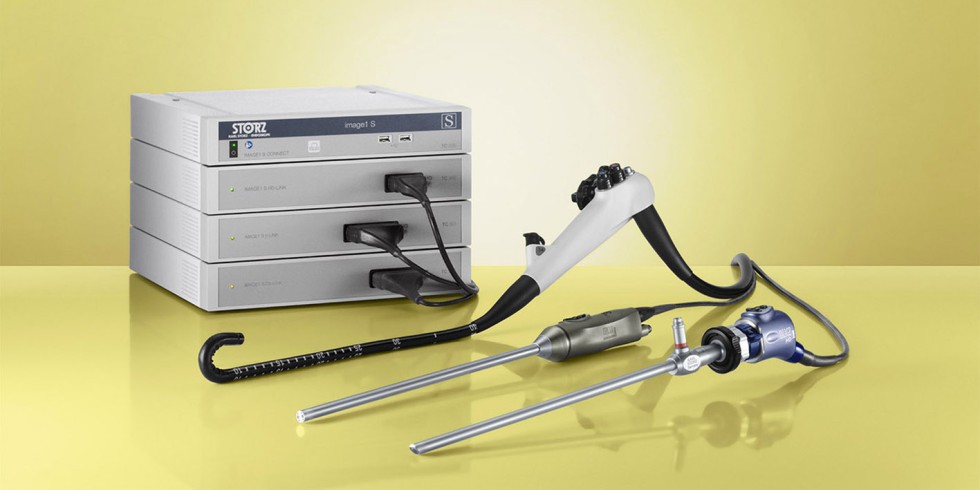
Bild 1. Verschiedene starre Endoskope der Firma Karl Storz SE & Co. KG.
Foto: Karl Storz SE & Co. KG
Ausgabe 11/12-2022, S. 816
Stable anti-reflex coatings for medical applications
Abstract: Optical components in medical technology are subject to constantly increasing demands on efficiency and quality. Anti-reflective coatings are indispensable to increase the light throughput of the optics and to avoid the occurrence of ghost images. However, these coatings are subject to extreme requirements in terms of mechanical and chemical resistance. As part of a BMBF funded joint project, anti-reflective coatings for endoscope windows were developed, which are resistant to cleaning, desinfection and sterilization processes as applied in hospital.
1 Einleitung und Motivation
An viele medizintechnische Geräte mit bildgebender optischer Funktion (wie zum Beispiel Endoskope) werden zunehmend Anforderungen bezüglich einer weiteren Verbesserung der Bildqualität gestellt. So soll die Lichttransmission des gesamten Aufbaus verbessert und Geisterbilder, die durch störende Reflexe entstehen, möglichst vermieden werden, Bild 1.
Antireflex (AR)-Beschichtungen, die Reflexe an den Grenzflächen der einzelnen optischen Elemente verringern, sind notwendig, um die Lichttransmission zu erhöhen und somit eine maximale Lichtausbeute zu erreichen. Für Medizinprodukte wie Endoskope gibt es bisher jedoch keine zufriedenstellenden Lösungen für AR-Beschichtungen auf den stark beanspruchten Außenfenstern, da diese für den Einsatz im klinischen Umfeld besonders hohe mechanische und chemische Stabilitätsanforderungen erfüllen müssen. Neben einer hohen Kratzbeständigkeit müssen Beschichtungen auf Endoskopfenster besonders der Reinigung in chemisch aggressiven Medien sowie der Desinfektion und Dampfsterilisation standhalten [1–4].
Antireflex-Beschichtungen, die eine Entspiegelungswirkung im gesamten sichtbaren Spektralbereich ermöglichen, sind üblicherweise als Stapel aus mehreren sehr dünnen Interferenzschichten mit alternierend hohem und niedrigem Brechungsindex aufgebaut, wobei eine Schicht mit niedrigem Brechungsindex als Abschlussschicht aufgebracht werden muss. Um eine möglichst farbneutrale und effiziente AR-Wirkung zu gewährleisten, ist es wichtig, dass die Schichtdicken aller Einzelschichten sehr genau getroffen werden. Schichtdickentoleranzen müssen dabei im Bereich von nur wenigen Nanometern liegen. SiO2-Schichten, die üblicherweise als niedrigbrechende Komponente in solchen AR-Stacks eingesetzt werden, sind bekannt dafür durch Reinigungs-, Sterilisations- und Desinfektionsverfahren, die für medizintechnische Anwendungen typisch sind, entweder sukzessive abgetragen oder völlig zerstört zu werden. Das würde unweigerlich zu einem Verlust der Entspiegelungswirkung führen und die Gesamtperformance des Instruments erheblich stören. Außerdem muss eine Ablösung der Beschichtung unbedingt vermieden werden, da die Gefahr besteht, dass während der Anwendung des Endoskops Teile der Beschichtung im Körper des Patienten verbleiben könnten. Es ist somit dringend notwendig, bei der Entwicklung von Antireflex-Beschichtungen für die Medizintechnik die Beständigkeit gegenüber den bei der Desinfektion, Sterilisation und Handhabung der Geräte im klinischen Umfeld typischen Bedingungen zu berücksichtigen. Im Rahmen des Verbundprojektes „Star“ (Stabile Antireflex-Beschichtungen für die Medizintechnik) wurde die Entwicklung von Antireflex-Beschichtungen, die sich aufgrund einer deutlich verbesserten chemischen Beständigkeit für den Einsatz in Endoskopen eignen, erfolgreich durchgeführt.
2 Herstellungsmethoden für Antireflex (AR)-Beschichtungen
Für die hochpräzise Abscheidung von dünnen optischen Schichten, wie sie für Antireflex-Beschichtungen notwendig sind, kommen üblicherweise PVD (Physical Vapor Deposition)-Methoden zur Anwendung. Neben dem Aufdampfen im Hochvakuum haben sich vor allem Sputterverfahren in den letzten Jahren zunehmend etabliert. Mit reaktivem Magnetronsputtern können zum Beispiel sehr dicke Filterbeschichtungen mit mehreren 100 Einzelschichten extrem präzise und mit exzellenter Schichtqualität abgeschieden werden. Vakuumbedampfungsverfahren zeichnen sich durch große Flexibilität bezüglich Materialwechsel und der Möglichkeit, sehr hohe Abscheideraten zu erreichen, aus. Damit können Beschichtungszeiten und Kosten niedrig gehalten werden.
Die Beschichtungen im Rahmen dieses Verbundprojektes erfolgten mittels unterschiedlicher PVD-Technologien, die bei den einzelnen Projektpartnern zur Verfügung stehen. Am Fraunhofer-Institut für Angewandte Optik und Feinmechanik IOF wurde sowohl die Plasma-Ionen-unterstützte Vakuumverdampfung (PIAD) an einem „Syrus Pro 1100“ Box Coater der Bühler Alzenau GmbH als auch ein Magnetron-Sputterverfahren (MS) an einem „Precicoat“ von Systec Vacuum Coating Inline-Sputtersystem durchgeführt. Neben einem Screening verschiedener Einzelschicht-Materialien (Al2O3, SiO2, Si3N4 und Ta2O5) kamen im weiteren Projektverlauf vor allem SiO2 und Ta2O5 als Materialien für Antireflex-Beschichtungen zur Anwendung, Bild 2.
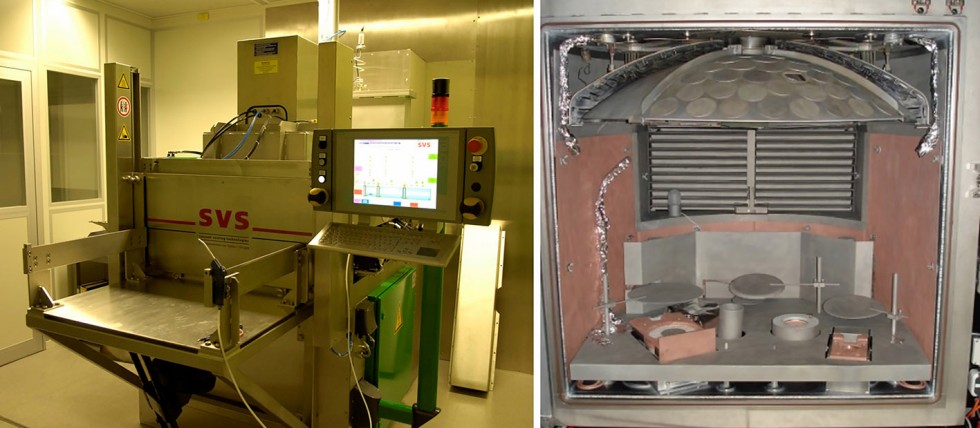
Bild 2. Beschichtungsanlagen am Fraunhofer IOF – links: Magnetronsputteranlage „Precicoat“ von Systec Vacuum Coating, rechts: Vakuumbedampfungs‧anlage „Syrus 1100“ der Bühler Alzenau GmbH.
Foto: Fraunhofer IOF
Bei der Firma Laser Components GmbH standen außer einer Vakuumbedampfungsanlage Syrus Pro 1100 auch eine Ion-Beam-Sputteranlage „Navigator 700“ der Firma Cutting Edge Coatings GmbH für das Projekt zur Verfügung (siehe Bild 3).
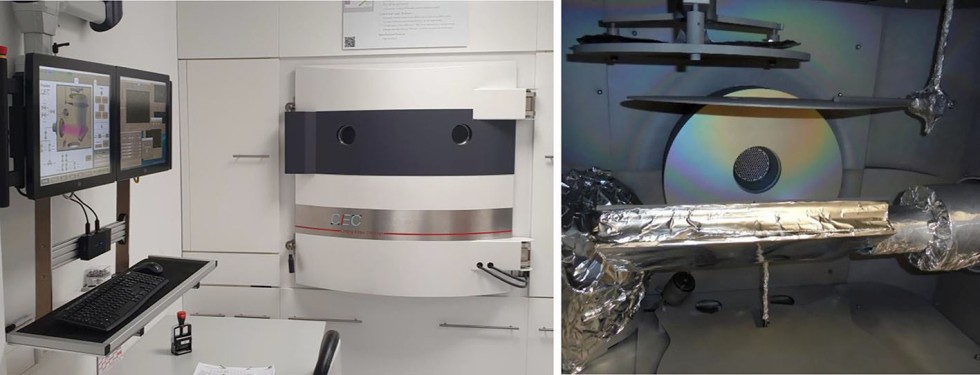
Bild 3. Eine der Beschichtungstechnologien bei der Firma Laser Components GmbH: Ion Beam Sputtering (IBS) Beschichtungsanlage „Navigator 700“ (Cutting Edge Coatings GmbH).
Foto: Laser Components GmbH
Die mit dieser Anlage hergestellten Beschichtungen waren von besonderem Interesse, da mit der IBS-Technologie noch ein zusätzliches Beschichtungsverfahren im Rahmen des Projektes getestet werden konnte. Mit dieser Anlage wurden neben der Entwicklung von Oxynitrid-Schichten, deren Potenzial bezüglich hoher Beständigkeit untersucht wurde, auch Antireflex-Beschichtungen auf Basis von SiO2 und Ta2O5 abgeschieden.
Als ein weiterer Projektpartner mit Beschichtungstechnik war die Firma Bühler Alzenau GmbH im Konsortium vertreten. Neben Beschichtungen auf einer Vakuumbedampfungsanlage Syrus Pro 1100 konzentrierten sich die Versuche bei Bühler auf eine Magnetronsputteranlage „Star“ sowie eine Plasma Assisted Reactive Magnetron-Sputteranlage (PARMS) „Helios 800“. Es wurden die Schichtmaterialien SiO2, Nb2O5, HfO2 und Ta2O5 als Einzelschichten sowie in Antireflex-Beschichtungen abgeschieden, Bild 4.
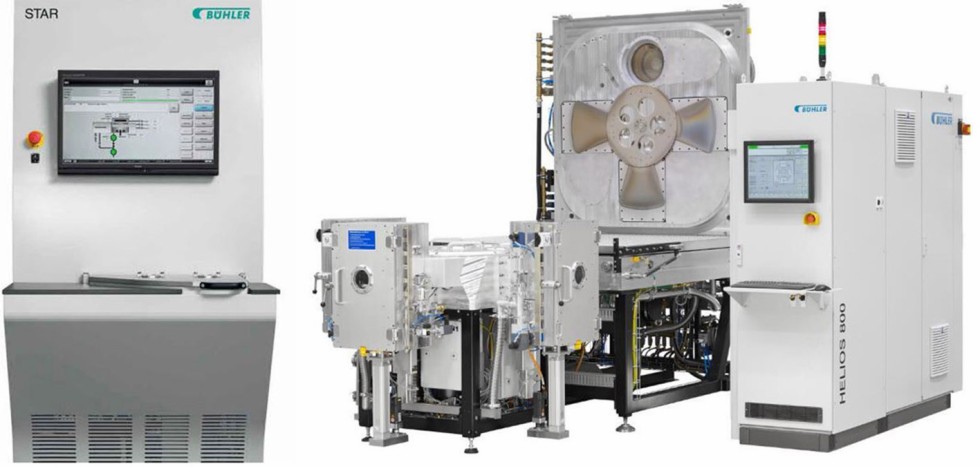
Bild 4. Zwei der Beschichtungsanlagen der Firma Bühler Alzenau GmbH: links: Magnetron-Sputteranlage „Star“, rechts: Plasma Assisted Reactive Magnetron-Sputteranlage „Helios 800“.
Foto: Bühler Alzenau GmbH
Für die Berechnung der Schichtdesigns wird heutzutage üblicherweise Dünnschicht-Berechnungssoftware verwendet. Damit können, ausgehend von einem gewünschten spektralen Reflexions- beziehungsweise Transmissionverlauf, unter Berücksichtigung der verfügbaren Schichtmaterialien, die notwendige Schichtanzahl und die einzelnen Schichtdicken eines solchen Multilayers berechnet werden. Eine gängige Schichtberechnungssoftware, die von den meisten der Projektpartner verwendet wurde, ist „OptiLayer“ von der Optilayer GmbH.
3 Testmethoden zur Untersuchung der Beständigkeit
Das Testen der hergestellten Beschichtungen sollte sich so weit wie möglich an den Anforderungen, die im klinischen Alltag für Endoskope auftreten, orientieren. Bei der Firma Karl Storz SE, dem Hersteller solcher Endoskope, sind derartige Testaufbauten vorhanden und wurden im Rahmen des Projekts genutzt. Es wurden AR-beschichtete Testscheiben genau definierten Zyklen für Reinigung, Desinfektion und Sterilisation unterworfen. Für die Reinigung und Desinfektion kommen stark basische Reiniger (pH > 11) sowie erhöhte Temperaturen zur Anwendung. Dazu wurde bei Karl Storz ein dafür üblicher Reinigungs- und Desinfektionsautomat verwendet, Bild 5.
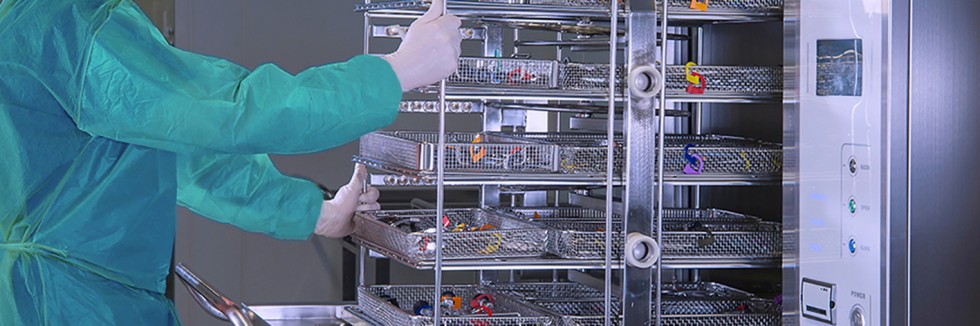
Bild 5. Reinigungs- und Desinfektionsautomat für medizintechnische ‧Geräte.
Foto: Karl Storz SE & Co. KG
Für die Sterilisation wurden verschiedene Methoden angewendet. Eine davon war die Sterilisation mit feuchter Hitze bei 134 °C und 2,1 bar Überdruck in einem Autoklaven, in der Regel als Dampfsterilisation bezeichnet. Derartige Beanspruchungszyklen (siehe Bild 6), wobei ein solcher Zyklus die einmalige Aufbereitung eines starren Endoskops vor der Anwendung darstellt, wurden bei Karl Storz bis zu 500x an einzelnen beschichteten Testscheiben wiederholt.
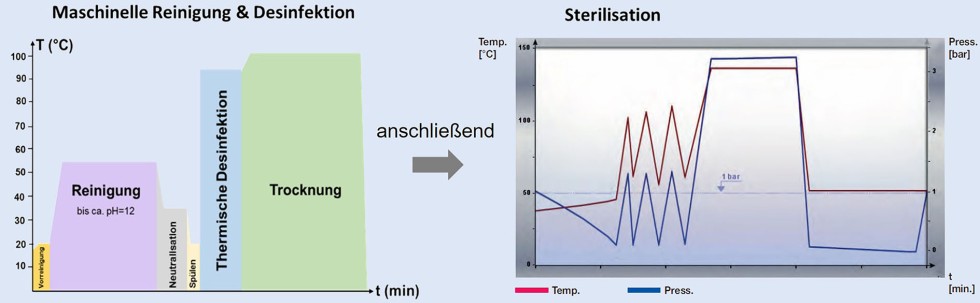
Bild 6. Ablauf und Parameter für Reinigungs-, Desinfektions- und Sterilisationszyklen. Graphik: Karl Storz SE & Co. KG
Am Fraunhofer IOF standen entsprechende Reinigungs- und Desinfektionsautomaten nicht zur Verfügung, daher wurde die reale Beanspruchung durch Einzeltests simuliert. Die Reinigung erfolgte in dem stark basischen Medium zum Beispiel durch das zeitlich gestaffelte Auslagern von Proben in einem Becherglas mit genau diesem Reiniger. Da die Dampfsterilisation zu Anfang des Projekts als die kritischste Beanspruchungsart für Beschichtungen angesehen wurde, beschaffte das Fraunhofer IOF einen entsprechenden Dampfsterilisator, um bei Versuchsreihen mit Variation der Beschichtungsmaterialien und -parametern die Proben unmittelbar auf Beständigkeit zu testen.
Auch bei der Firma Bühler Alzenau GmbH wurden eigene Beständigkeitstests für die beschichteten Testproben durchgeführt, unter anderem Ablaugtests in Kaliumhydroxid-Lösung sowie Abrasion durch Sand mittels eines Bayer-Abrasion-Tests.
4 Entwicklung einer stabilen AR-Beschichtung für Endoskopfenster
Zu Anfang des Projekts war noch unklar, welche Schichtmaterialien überhaupt bezüglich der Beständigkeit gegen Reinigung, Desinfektion und Sterilisation in Frage kommen. Zudem war nicht bekannt, ob das verwendete Abscheideverfahren (Aufdampfen beziehungsweise verschiedene Sputterverfahren) einen Einfluss auf die Beständigkeit der Beschichtung hat.
Daher wurde bei den verschiedenen Projektpartnern ein Materialscreening an Einzelschichten aus verschiedenen Materialien, die zusätzlich noch mit verschiedenen Abscheideverfahren hergestellt wurden, durchgeführt.
Am Fraunhofer IOF wurden zum Beispiel Einzelschichten aus Al2O3, SiO2, Si3N4 und Ta2O5 mittels Vakuumbedampfung und Magnetronsputtern auf Saphir-Testscheiben abgeschieden. An diesen Proben wurde dann unter anderem die Dickenabnahme der Schicht bei Auslagerung in einem stark basischen Reiniger bestimmt. Wie in Bild 7 gezeigt, waren nur die Ta2O5-Schichten stabil gegenüber dem Reinigungsmittel. Alle anderen Schichten wurden zum Teil schon in relativ kurzer Zeit deutlich abgetragen.
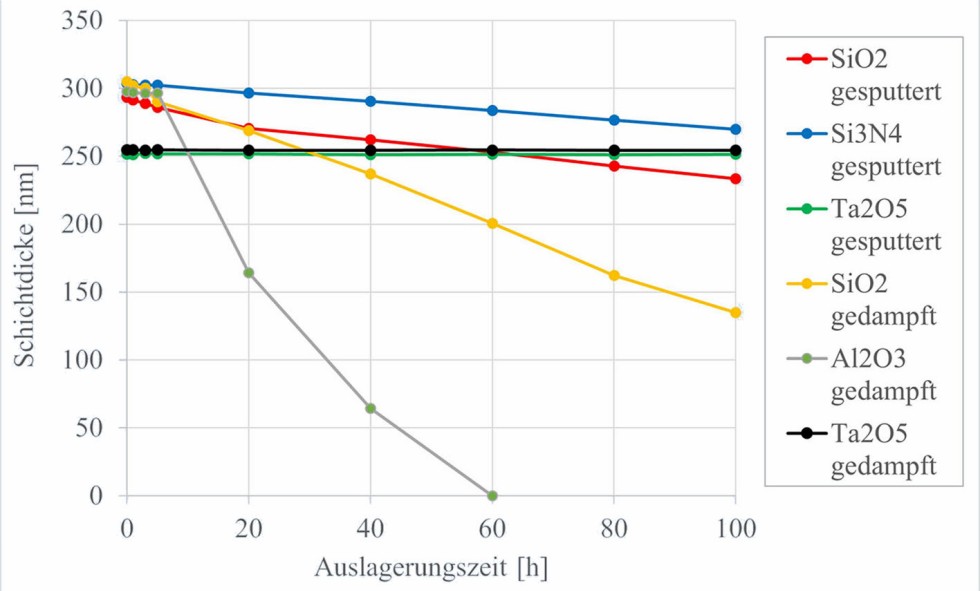
Bild 7. Abtrag an Einzelschichten aus verschiedenen Materialien bei ‧Auslagerung in einem stark basischen Reiniger. Graphik: Fraunhofer IOF
Die Versuche bei den anderen Projektpartnern bestätigten, dass alle niedrigbrechenden Schichtmaterialien (zum Beispiel SiO2, MgF2, Al2O3) deutlich abgetragen wurden, hingegen die meisten hochbrechenden (Ta2O5, HfO2, ZrO2) stabil gegenüber dem basischen Reiniger waren. Alle Einzelschicht-Proben wurden auch mittels Heißdampf-Autoklaven sowie gegenüber Abrieb getestet. Auch beim Autoklavieren schnitten die hochbrechenden Schichtmaterialien deutlich besser als die niedrigbrechenden ab.
Anhand der Ergebnisse aus den Einzelschichtversuchen wurden geeignete Materialien für ein Antireflex-Coating ausgewählt. Als eine geeignete Materialpaarung stellte sich SiO2 als niedrigbrechendes und Ta2O5 als hochbrechendes Schichtmaterial heraus. Es wurden Schichtdesigns mit einer geeigneten Schichtabfolge und entsprechenden Einzelschichtdicken berechnet, um sowohl eine breitbandige Antireflexwirkung als auch eine hohe Stabilität in den Beständigkeitstests zu gewährleisten. Derartige AR-Beschichtungen wurden bei verschiedenen Projektpartnern mit unterschiedlichen Technologien (Vakuumbedampfung, Sputterverfahren) sowohl auf Testscheiben, als auch auf Endoskoplinsen abgeschieden. Die beschichteten Teile wurden bei Karl Storz in zyklischen Wiederholungstests bis zu 500x gereinigt, desinfiziert und sterilisiert. Dabei wurde die spektrale Reflexion der Testscheiben vor Beginn der Tests, nach 300 und nach 500 Zyklen gemessen. In Bild 8 sind diese Spektralkurven für eine am Fraunhofer IOF Jena durch Magnetron-Sputtertechnologie hergestellte Testscheibe gezeigt. Selbst nach 500 Testzyklen ist keine nennenswerte Änderung der Reflexion zu erkennen. Das heißt, die Antireflex-Beschichtung ist noch vollständig vorhanden und wurde weder abgetragen noch beschädigt oder abgelöst. Dies ist auch auf dem Foto der Testscheibe (siehe Bild 8 rechts), das nach den 500 Testzyklen aufgenommen wurde, zu sehen.
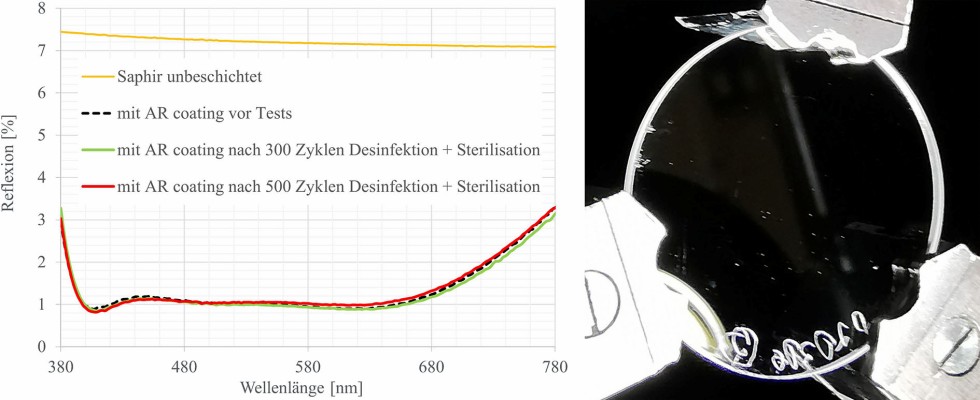
Bild 8. Links: Gemessene Reflexion einer mit dem stabilen AR-Coating am IOF Jena mit Magnetronsputtern beschichteten Saphir Testscheibe vor und nach Desinfektions/Sterilisations Beanspruchungszyklen, rechts: Foto der beschichteten Testscheibe nach 500 Beanspruchungszyklen. Graphik: Fraunhofer IOF
Mit den entspiegelten Endoskoplinsen wurden bei der Firma Karl Storz Bildaufnahmetests unter realen Anwendungsbedingungen durchgeführt. Hier zeigte sich der Vorteil der Entspiegelung an verminderten Geisterbildreflexen sowie einer erhöhten Lichtausbeute. In Bild 9 ist die Aufnahme einer Operationsleuchte durch ein Endoskop ohne und mit AR-beschichteter Frontlinse gezeigt. In den rot markierten Bereichen sind die unerwünschten Reflexe der Leuchte erkennbar. Dieser Reflex wird durch die Entspiegelung deutlich reduziert.
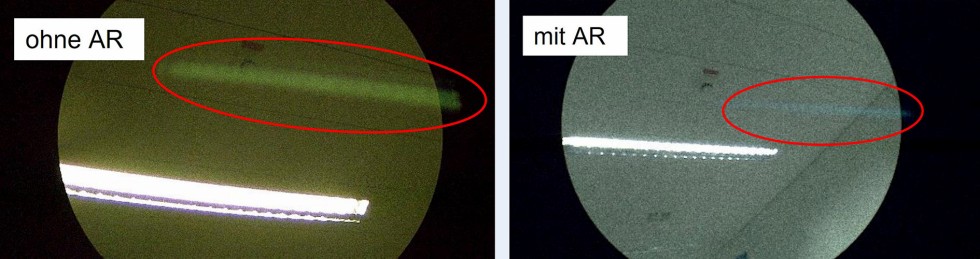
Bild 9. Bildaufnahmetest durch ein Endoskop ohne AR und mit AR auf der Frontlinse.
Foto: Karl Storz SE & Co. KG
5 Zusammenfassung und Ausblick
Antireflex-Beschichtungen gehören in vielen optischen Geräten und Instrumenten mittlerweile zum Standard. Für medizintechnische Anwendungen wie zum Beispiel Endoskope müssen diese Beschichtungen aber die hohen Belastungen, die durch wiederholte Reinigung, Desinfektion und Sterilisation auftreten, unbeschadet überstehen. In diesem Verbundprojekt haben Beschichtungsfirmen zusammen mit einem Hersteller von Medizinprodukten und einem Forschungsinstitut die Entwicklung einer solchen stabilen AR-Beschichtung für die stark beanspruchten Außenflächen von zum Beispiel Endoskoplinsen erfolgreich durchgeführt. Momentan werden Möglichkeiten eines Transfers der Projektergebnisse in die Serienfertigung von Endoskopen in Erwägung gezogen.
Dieses Forschungs- und Entwicklungsprojekt wird mit Mitteln des Bundesministeriums für Bildung und Forschung (BMBF) im Programm „Zukunft der Wertschöpfung – Forschung zu Produktion, Dienstleistung und Arbeit“ (Förderkennzeichen 02P18C110 bis 02P18C114) gefördert und vom Projektträger Karlsruhe (PTKA) betreut. Die Verantwortung für den Inhalt dieser Veröffentlichung liegt bei den Autoren.
Literatur
- Bundesgesundheitsblatt 2012, Hygiene Requirements for the Reprocessing of Medical Devices 55:1244–1310, Springer-Verlag, 2021. DOI 10.1007/s00103–012–1548–6
- Working Group Instrument Reprocessing, Reprocessing Instruments to Retain Value, 11th edition p.33–41;55–57 (2017)
- Nelson, D.B.; Muscarella, L.F.: Current issues in endoscope reprocessing and infection control during gastrointestinal endoscopy, World J Gastroenterol, 12 (2006) 25, p. 3953–64
- Bhatia, V.; Vaishali, B.; Harsh Vardhan, T.: Reprocessing and Reuse of Endoscopic Accessories, Journal of Digestive Endoscopy, 12.04: 214–220 (2021)
Peter Munzert
Fraunhofer-Institut für Angewandte Optik und Feinmechanik IOF
Albert-Einstein-Str. 7, 07745 Jena
Tel. +49 3641 / 807 271
peter.munzert@iof.fraunhofer.de
www.iof.fraunhofer.de
Ralf Staud
Karl Storz SE & Co KG
Dr.-Karl-Storz-Str. 34, 78532 Tuttlingen
Tel. + 49 7461 / 708 714
ralf.staud@karlstorz.com
www.karlstorz.com
Rainer Götzelmann
Bühler Alzenau GmbH
Siemenstr. 88, 63755 Alzenau
Tel. +49 6023 / 500 158
rainer.goetzelmann@buhlergroup.com
www.buhlergroup.com
Sina Malobabic
Laser Components GmbH
Werner-von-Siemens-Str. 15, 82140 Olching
Tel. +49 8142 / 28640
s.malobabic@lasercomponents.com
www.lasercomponents.com
Florian Haacke
GXC Coatings GmbH
Im Schleeke 27–31, 38642 Goslar
Tel. +49 5321 343074
florian.haacke@gxc-coatings.de
www.gxc-coatings.de