Neue Herausforderungen für die Produktionstechnik
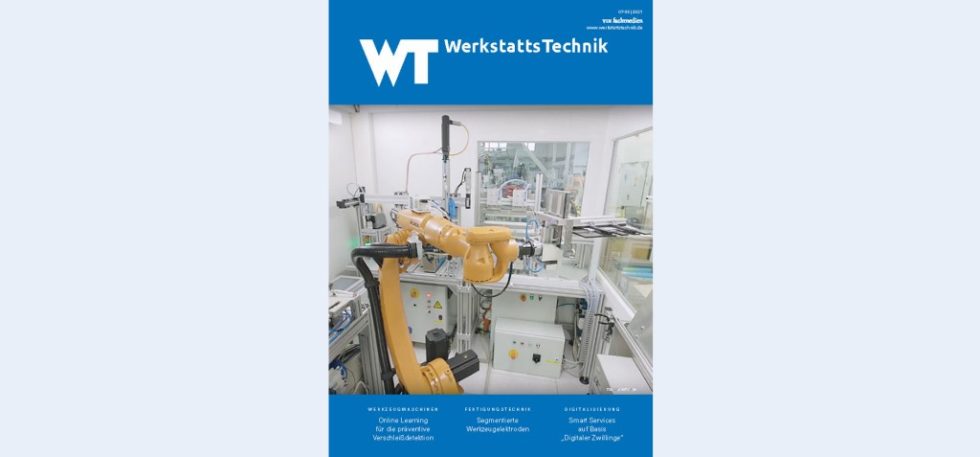
Seit dem Frühjahr 2020 wird das tägliche Leben durch die Corona-Pandemie bestimmt. Dies stellt insbesondere die Produktionstechnik vor neue Herausforderungen. Die Krisensituation zeigt auf, dass das deutsche produzierende Gewerbe aktuell noch ein Ausbaupotenzial hinsichtlich der Reaktionsfähigkeit auf ein wechselhaftes Umfeld aufweist. Um in Zukunft auch unvorhersehbaren Situationen Stand halten zu können und die Produktion unter unbekannten Umständen aufrechtzuerhalten, müssen Produktionssysteme zunehmend flexible und wandlungsfähige Strukturen annehmen.
Modularisierung auf allen Ebenen einer Produktionsanlage
Ein vielversprechendes Konzept zur Realisierung flexibler Produktionsstrukturen, die kurze Rekonfigurationszeiten mit sich bringen, bietet der Ansatz der Modularisierung auf allen Ebenen einer Produktionsanlage. Auf physikalischer Ebene kann die Modularisierung durch eine Aufteilung des Gesamtprozesses in seine Teilprozesse und die Umsetzung dieser in einzelnen Produktionszellen realisiert werden. Abhängig vom Kundenauftrag lassen sich die Produktionszellen in der erforderlichen Reihenfolge und Quantität auswählen und dem Produktionsprozess hinzufügen. Durch die Implementierung einer serviceorientierten Steuerungsarchitektur kann die Modularität auch aus informationstechnologischer Sicht gewahrt werden. Im Beitrag „Agile Batteriezellfertigung als Antwort auf volatile Märkte und Technologien“ wird detailliert dargestellt, wie ein solches agiles Produktionssystem realisiert werden kann. Nicht nur für die Batteriezellproduktion sind flexible und skalierbare Ansätze von hoher Relevanz. Zur Unterstützung des Wandels von konventionellen Antriebstechnologien hin zu einer nachhaltigen und klimaneutralen Mobilität müssen innovative Produktionskonzepte für die Fertigung leistungsstarker sowie effizienter elektrischer Transaktionsantriebe eingeführt werden. Ein Beispiel hierfür stellt die Herstellung von Elektromotor-Statoren durch das flexible Twisten von Hairpins mithilfe kinematischer Prozessführung dar.
Steigerung der Anlagenverfügbarkeit
Neben der Einführung neuer Prozesse müssen unter dem Aspekt der ökologischen Verantwortung auch bestehende Produktionssysteme und -anlagen durch Modernisierung von Bestandsmaschinen den Anforderungen angepasst werden. Insbesondere durch digitale Nachrüstlösungen besteht ein hohes Potenzial zur Steigerung der Anlagenverfügbarkeit. Eine Studie in dieser Ausgabe zeigt auf, dass dieses Potenzial aktuell noch nicht vollständig ausgeschöpft ist. Nicht nur Digitalisierungsansätze optimieren die Produktivität bestehender Prozesse. Auch die Weiterentwicklung des Prozesswissens, wie beispielsweise die gezielte Umverteilung von Funkenentladungen durch segmentierte Werkzeugelektroden, erhöht die Produktivität maßgeblich.
Ebenso eröffnet die Einführung neuer Materialien und Oberflächenbearbeitungsmethoden neue Herangehensweisen für die konstruktive Auslegung. Hierdurch werden weitere Freiheitsgrade für die Optimierung der Fertigung geschaffen, was ebenso einen Beitrag zur Flexibilität einer Produktion leistet. Eine Neuheit stellt in diesem Kontext das Finishing keramischer Oberflächen mittels Bürstenwerkzeugen mit gebundenem Schleifmittel dar.
Diese Ausgabe verdeutlicht, dass durch die Maximierung der Flexibilität die Komplexität von Produktionsprozessen minimiert werden kann. Dies erlaubt eine schnelle Ein- und Ausgliederung von Fertigungsschritten, was dem Unternehmen auch auf übergeordneten Ebenen eine große Flexibilität verschafft. Durch dieses Neu-Denken auf einer breiten Front, beginnend bei der Digitalisierung, hinweg über neue Produktionsprozesse und die Einbeziehung neuer Materialien, bis hin zur Schaffung komplett neuer Produktionskonzepte, wie agile Produktionssysteme, wird auch an Hochlohnstandorten eine hohe Effizienz ermöglicht. Einem hohen Wertschöpfungspotenzial steht somit auch in Deutschland nichts im Wege.

Prof. Dr.-Ing. Jürgen Fleischer ist Institutsleiter Maschinen, Anlagen und Prozessautomatisierung am wbk Institut für Produktionstechnik des Karlsruher Instituts für Technologie (KIT). Foto: wbk / KIT