Fabrikneuplanung bei einem Auftragsfertiger für die Wehr- und Luftfahrttechnik
Am Stammsitz Hagen fertigt das Unternehmen Stahlkontor GmbH & Co. KG Bauteile und Baugruppen u. a. für die Industriebereiche Defense und Aviation. Stark steigende Auftragsvolumina und eine in die Jahre gekommene Standortinfrastruktur sowie nicht optimale Abläufe in Produktion und Logistik machen eine Neustrukturierung unabdingbar. Dazu plant Stahlkontor den sukzessiven Neubau einer modernen und flexiblen Fertigungsstätte bei Aufrechterhaltung der Produktion am Stammsitz.
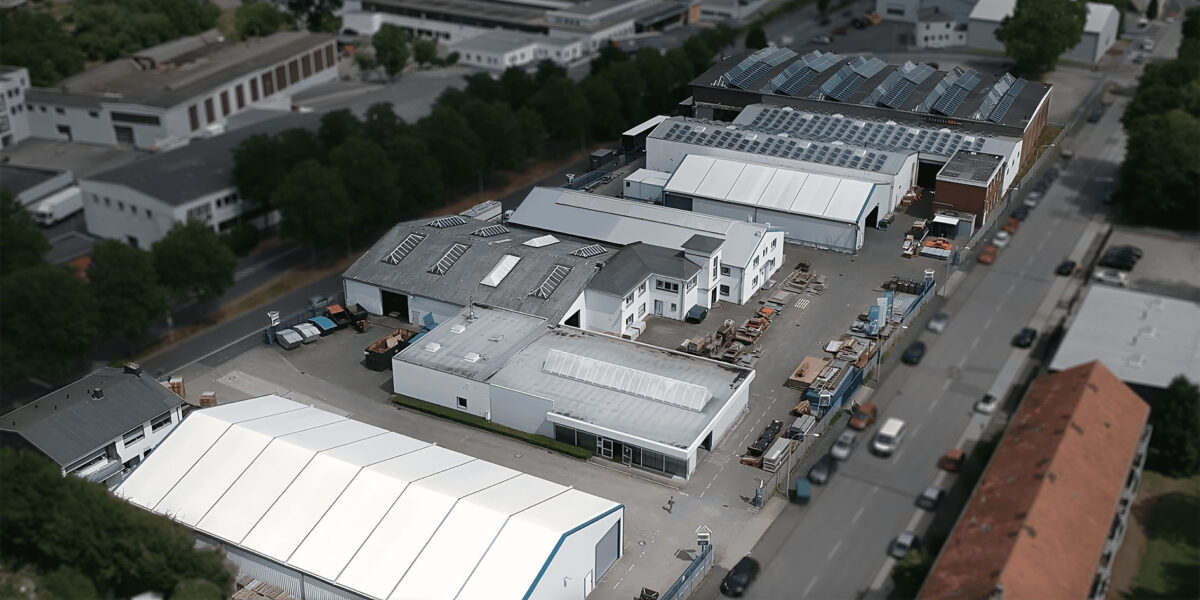
Bild 1. Der östliche Teil des Stahlkontor-Betriebsgeländes vor Start der Bauphase aus der Vogelperspektive.
Foto: Stahlkontor
Factory planning for a manufacturer in the defense and aviation industry
Abstract: At its headquarters in Hagen, Stahlkontor GmbH & Co. KG manufactures components and assemblies for the defense and aviation industries. Strongly increasing order volumes and an aging site infrastructure as well as suboptimal processes in production and logistics make restructuring essential. Therefore, Stahlkontor is planning the successive construction of a new, modern and flexible production facility while maintaining factory operations at the headquarters.
1 Unternehmensvorstellung und Ausgangssituation
Spezialisiert auf die Sonderanforderungen des wehrtechnischen und luftfahrttechnischen Sektors produziert das Unternehmen Stahlkontor GmbH & Co. KG mit Sitz in Hagen als Auftragsfertiger Bauteile und Baugruppen für die Bereiche Defense, Aviation, Industry und Rail. Mit etwa 300 hochqualifizierten Mitarbeitenden ist Stahlkontor im Stande flexibel auf die unterschiedlichsten Kundenanforderungen zu reagieren – von der Unterstützung in Entwicklung und Konstruktion bis hin zur Fertigung von Spezialteilen und Prototypen sowie Baugruppen in Großserien. Zu den Kernkompetenzen des Unternehmens zählen die Trenntechnik, Zerspanung, Kaltumformung, Baugruppenmontage sowie das Fügen von insbesondere hochfest vergüteten Stählen sowie Panzerstählen. Auch für Aluminium-, Titan- und innovative Verbundwerkstoffe hat sich Stahlkontor eine Expertise aufgebaut.
In der jüngsten Vergangenheit ist das Auftragsvolumen durch erhöhte Nachfrage aus den Branchen Defense und Aviation stark angestiegen. Durch die strategische Weiterentwicklung des Unternehmens Stahlkontor hin zum Systemlieferanten für Baugruppen – was kundenseitig zunehmend gefordert wird, u. a. bedingt durch begrenzte Produktionskapazitäten bei den OEMs – steigt zudem die Fertigungstiefe und damit die Komplexität in der Produktion weiter an. Gleichzeitig nehmen die maximalen Bauteildimensionen weiter zu und führen zu einem immer aufwendigeren Materialhandling.
Als Begrenzung für dieses Wachstum wurde die bestehende, historisch gewachsene Gebäudeinfrastruktur des Produktionsstandortes identifiziert. Primäre Herausforderungen liegen dabei in einem nicht ausreichenden Flächenangebot, überwiegend ungerichteten Materialflüssen sowie nicht optimal gesteuerten produktionslogistischen Prozessen. Die zunehmende Mehrstufigkeit der Produktion infolge der Steigerung der Fertigungstiefe verschärft diese Problematik zunehmend. Bild 1 zeigt die aus einzelnen Hallen bestehende, kleingliedrige Gebäudeinfrastruktur, deren Flächenangebot durch den bestehenden Maschinenpark ausgereizt ist und nur eine geringe Flussorientierung ermöglicht. Der innerbetriebliche Materialtransport erfolgt vor allem über Außenflächen.
Durch den schrittweisen Abriss und Neubau der Produktionsgebäude auf dem östlichen Teil des Betriebsgeländes und die Erweiterung des Maschinenparks wird der Produktionsstandort zur effizienten Leistungserstellung eines deutlich steigenden Auftragsvolumens befähigt. Unterstützt durch das Fraunhofer-Institut für Materialfluss und Logistik (IML) wurde vor allem einer effizienten logistischen und produktionstechnischen Gestaltung der neuen Produktionsstätte hohe Bedeutung beigemessen. Dieser Beitrag gibt einen Einblick in die Vorgehensweise und das Planungsergebnis des Fabrikplanungsprojektes.
2 Vorgehensweise im Projekt
In Anlehnung an das in der Praxis etablierte und methodisch abgesicherte Fabrikplanungsvorgehensmodell gemäß VDI-Richtlinie 5200 [1] startete das Projekt mit der Zielfestlegung. Gemeinsam mit der Geschäftsführung des Unternehmens Stahlkontor wurden in einem Zukunftsworkshop die Implikationen der Unternehmensstrategie auf die Produktions- und Logistikrelevanten Planungsprämissen der neuen Fertigungsstätte abgeleitet. Ausgangspunkt der Bebauungsplanung war eine bereits durch das Architekturgewerk grob vorgeplante Gebäudehülle, die sich am größtmöglichen Baufenster des Betriebsgeländes orientiert.
Basierend auf den Prozess- und Materialflussaufnahmen des Ist-Zustandes wurden zunächst Schwachstellen und Handlungsfelder identifiziert. Anschließend wurden umfangreiche Datenanalysen durchgeführt. So wurden die Fertigungsrückmeldungen für einen repräsentativen Zeitraum analysiert, um später die einzelnen Produktionsbereiche entsprechend ihrer Fertigungsprozessabfolge optimal anzuordnen. Ebenso wurde die logistische Systemlast analysiert und um eine Prognose der zukünftigen Entwicklung ergänzt, um die logistischen Prozesse und Ressourcen für den Neubau zu dimensionieren. Anschließend startete die Konzeptplanung, indem sukzessive für jeden der insgesamt drei Bauabschnitte Konzeptvarianten der Produktions- und Logistikstrukturen – zunächst als Grobvarianten – erstellt wurden. Die darauffolgende Detailplanung resultierte in der Empfehlung einer Vorzugsvariante, welche im nächsten Abschnitt skizziert wird.
Im gesamten Planungsprozess nahm das Thema des Interimskonzeptes ein besonderes Augenmerk ein, um die Leistungsfähigkeit des Produktionsbetriebs so weit wie möglich aufrechtzuerhalten. Das Interimskonzept umfasst dabei die Terminierungsplanung sämtlicher mit der Bauphase in Verbindung stehender organisatorischer Maßnahmen in einer sachlogischen Reihenfolge. Insbesondere wurden dabei die Auswirkungen auf die Flächenverfügbarkeit für Produktion und Logistik berücksichtigt, um Engpässe zu identifizieren und entsprechende Gegenmaßnahmen einleiten zu können.
3 Vorstellung des Planungsergebnisses
Da mit Zunahme der Schweiß- und Montageumfänge eine deutlich steigende logistische Systemlast zu erwarten ist, kommt dem Thema Logistik in diesem Fabrikplanungsprojekt eine besondere Bedeutung zu. Neben der hardwaremäßigen Lagertechnik und der informationstechnischen Systemunterstützung steht insbesondere die Konzeption und Dimensionierung der produktionslogistischen Prozesse und Ressourcen im Fokus. Um eine flussorientierte Fertigung zu ermöglichen, sind im Zuge der Fabrikstruktur- bzw. Layoutplanung sämtliche Funktionsflächen so anzuordnen, dass die Auftragsabwicklung durch einen effizienten Materialfluss bestmöglich unterstützt wird. Die Funktionsflächen umfassen die Maschinengrundflächen, Nebenflächen zur Lagerung von Werkzeugen und Vorrichtungen sowie Puffer-, Lager und Transportflächen. Vor allem die zunehmende Mehrstufigkeit der Produktion in Kombination mit den wachsenden maximalen Bauteildimensionen von bis zu 3 m x 7,5 m erfordern – da je nach Fertigungsstufe die Materialien nicht mehr zwangsläufig stapelbar sind – große Flächen, um die Materialversorgung der einzelnen Maschinen sicherstellen zu können.
Die Analyse der Fertigungsrückmeldungen hat typische, werkstoffspezifische Prozessablaufmuster ergeben. Ein beispielhafter Prozessablauf ist der folgende: Trennen, Umformen, Zerspanen, Strahlen, Schweißen, Lackieren (extern), Montage. Eine Anordnung der Produktionsbereiche nach genau diesem typischen Fertigungsablauf ist jedoch aus zwei Gründen nicht möglich. Erstens ist es auf Grund von Fundamentierungen technisch nicht möglich bzw. nicht wirtschaftlich, Maschinen zu verschieben. Dies betrifft vor allem die Trenn- und Schweißbereiche des westlichen Betriebsgeländes, welches nicht Teil der baulichen Restrukturierung ist. Zweitens sind durch die abschnittsweise Bauphase Restriktionen zu beachten (Interimskonzept), welche die Nutzungsoptionen der sukzessiv entstehenden Bauabschnitte vorgeben.
Aus den zu Beginn genannten Anforderungen resultieren die folgenden Gestaltungsgrundsätze für die Fabrikneuplanung, die trotz der zuletzt genannten Restriktionen eine deutliche Effizienzsteigerung der Produktion und Logistik erwarten lassen:
- Der Materialfluss ist werkstoffspezifisch zu segmentieren (Panzerstahl, Titan, Aluminium), u. a. durch getrennte Wareneingänge und eine technische bedingte Zuordnung zu bestimmten Maschinen.
- Eine durchgängige Logistikachse zur effizienten Realisierung des Hauptmaterialflusses verbindet die drei Bauabschnitte untereinander sowie mit den bestehenden Trenn- und Schweißbereichen des westlichen Betriebsgeländes. Die logistische Ver- und Entsorgung der einzelnen Produktionsbereiche erfolgt über Versorgungsstiche, die von der Logistikachse abgehen.
- In einem übergeordneten Standortkonzept werden extern angemietete Standorte eingebunden, um die effiziente Erfüllung der gestiegenen Systemlast auch während der Bauphase sicherzustellen.
Die genannten Gestaltungsgrundsätze spiegeln sich in der Konzeptplanung der drei Bauabschnitte wieder. Im Folgenden werden die wesentlichen Aspekte des Planungsergebnisses, dessen Layout in Bild 2 dargestellt ist, beschrieben.
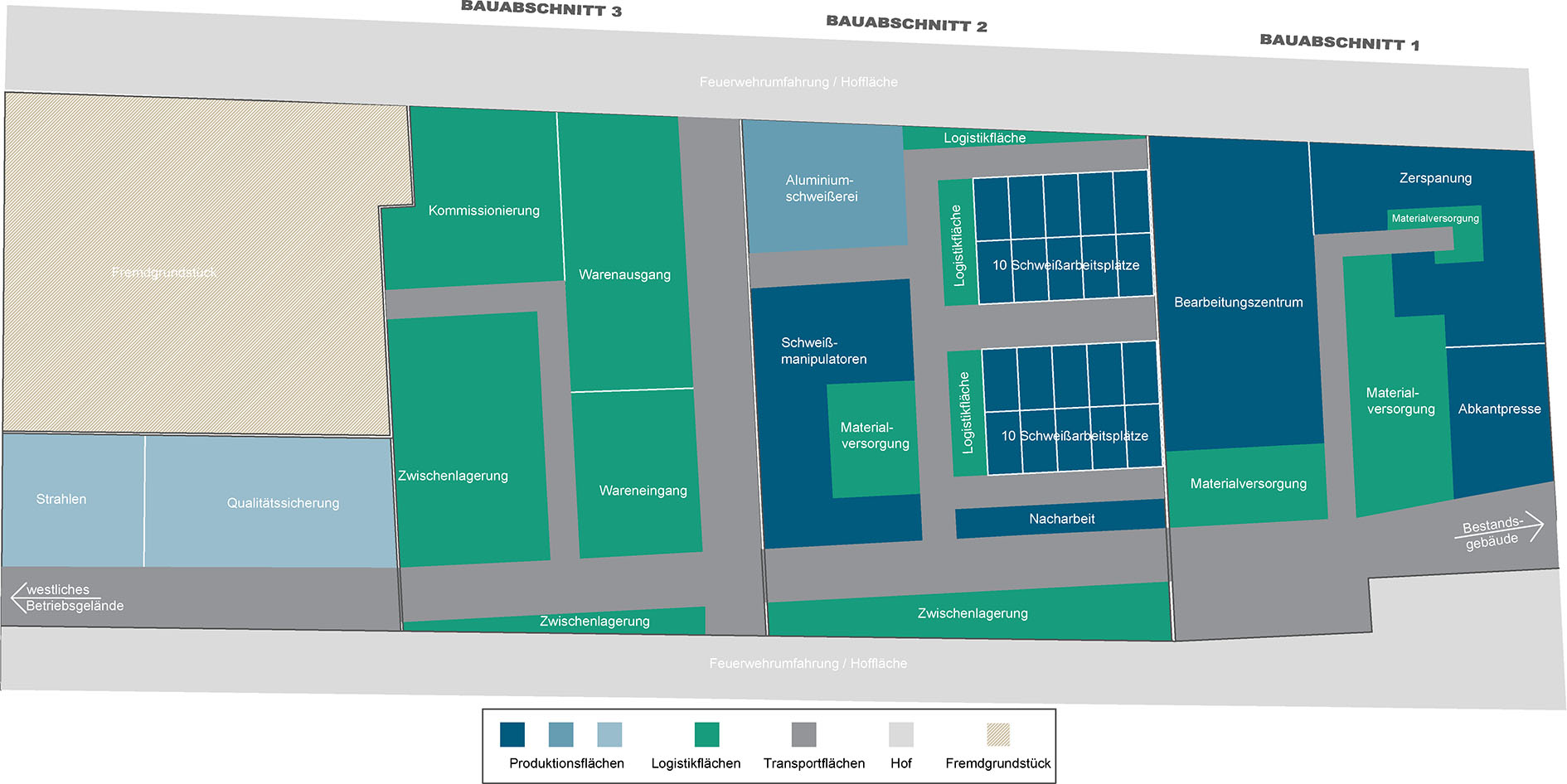
Bild 2. Produktions- und Logistiklayout im Zuge der Bebauungsplanung des neuen Werksteils. Grafik: Stahlkontor, Fraunhofer IML
Bauabschnitt 1 umfasst Maschinen der Technologien Zerspanen und Umformen. Herzstück dieses Bereiches sind eine Abkantpresse mit einer Presskraft von 2500 Tonnen sowie eine Fahrständermaschine für anspruchsvolle Zerspanungsarbeiten mit Bearbeitungslängen von bis zu 20 m bzw. für sog. Pendelbearbeitungen in kleineren Bearbeitungsdimensionen. Diese beiden Anlagen ermöglichen die Bearbeitung von Bauteilen mit einer maximalen Dimension von bis zu 3 m x 7,5 m. Da diese Anlagen besonders aufwendige Fundamentierungsarbeiten erfordern und nachträglich nicht verändert werden können, ist deren optimale Positionierung langfristig besonders wichtig. Hierbei musste zum Planungszeitpunkt die notwendige Flexibilität für einen langen Zeithorizont in verschiedenen Szenarien berücksichtigt werden. Auf Basis der Kapazitätsquerschnitte konnten die Materialeingangs- sowie Materialausgangspuffer dimensioniert werden. Sie sind für die besagten Anlagen so ausgelegt, dass Material auf einem Mafi-Wagen über die Logistikachse an der Anlage bereitgestellt werden kann und per Kran direkt den Anlagen zugeführt werden kann. Eine weitere 320-Tonnen-Biegepresse sowie verschiedene Bearbeitungszentren für die Zerspanung komplettieren den Maschinenpark in diesem Bauabschnitt. Sie werden per Stapler über den Versorgungsstich mit Material ver- und entsorgt.
In Bauabschnitt 2 befindet sich die Schweißerei. Sie umfasst für das Schweißen von Panzerstählen manuelle Schweißarbeitsplätze, die bei Bedarf paarweise zusammengeschoben werden können, Manipulatoren zum Schweißen von Bauteilen mit Abmaßen von bis zu 3 m x 7,5 m und entsprechende Nacharbeitsplätze und Richtpressen. Die manuellen Schweißarbeitsplätze verfügen über jeweils drei Palettenstellplätze – Materialeingangspuffer, Materialausgangspuffer und Bereitstellfläche für Vorrichtungen. Werkzeuge und Vorrichtungen werden in Regalen entlang des Versorgungsstiches gelagert. Zum Schweißen von Materialumfängen aus Aluminium steht eine fertigungstechnologisch bedingt separate, vollständig gekapselte Schweißerei zur Verfügung.
In Bauabschnitt 3 befinden sich die logistischen Funktionsflächen, eine Freifläche zur Durchführung von Qualitätsprüfungen sowie am äußeren Rand der Strahlbereich. Die durch das Strahlen – in der Regel der letzte Prozess vor dem Schweißen – verursachten Staubemissionen auf die Fertigungsbereiche sollen damit möglichst vermieden werden. Das rechte Hallenschiff der Logistikflächen umfasst eine LKW-Durchfahrt zur An- und Ablieferung, einen Wareneingangs- sowie einen Warenausgangsbereich. Fertigware wird auf Paletten bzw. ggf. Sonderpaletten in einem Regallager zur Abholung zwischengelagert. Zur Minimierung der für die Gabelstapler notwendigen Rangierflächen erfolgt die Be- und Entladung der LKW stets von links oder bei großen Bauteilen per Kran. Die LKW-Durchfahrt ist so dimensioniert, dass ein LKW einen parkenden LKW überholen kann. Im linken Hallenschiff befindet sich eine große Zwischenlagerfläche sowie die Kommissionierung. Diese besteht aus einem Regallager mit zwölf Ebenen und einem Behälterlager für Kleinartikel wie z. B. C-Teile. Aufgrund der zukünftig noch höheren Frequentierung der Kommissionierung wird dieser Bereich ein Kernelement der neuen logistischen Struktur. Neben wegeoptimierten Kommissioniervorgängen stehen ergonomisch optimierte Arbeitsplätze im Fokus.
Für die produktionsnahen Mitarbeitenden befinden sich Büros und Sozialräume überwiegend in der zweiten Ebene des Neubaus. Aus Gründen der Übersichtlichkeit sind diese Räumlichkeiten nicht in Bild 2 dargestellt.
Die Intralogistikplanung stützt sich zusammenfassend auf folgende Planungsaspekte. Der Transport von großen Blechzuschnitten erfolgt über die Logistikachse mittels Mafi-Wagen. Umschlag und Materialhandling dieser erfolgen in der Regel mittels Krananlagen, die in allen Bauabschnitten verfügbar sind. Blechzuschnitte werden in der Bodenblocklagerung für die nächste Fertigungsstufe gelagert, wobei die Liegezeiten minimiert werden. Bei besonders großen Blechzuschnitten kann ein Handlingsschritt eingespart werden, indem das Material auf dem Mafi-Wagen direkt auf den Materialeingangspuffer gestellt wird. Für Palettenware wird das Prinzip der Regallagerung bevorzugt umgesetzt, um mit erhöhter Lagerdichte die steigende logistische Systemlast zu bewältigen.
Das Planungsergebnis erfüllt damit in Anlehnung an Wiendahl [2, 3] die Anforderungen an eine hohe Wirtschaftlichkeit, hohe Flexibilität und Wandlungsfähigkeit sowie hohe Attraktivität, wobei sich diese durch motivierende Arbeitsbedingungen, die Erfüllung ökologischer Kriterien zur Gewährleistung geringer Umweltbelastungen und der Umsetzung einer modernen, ästhetischen Industriearchitektur auszeichnet.
4 Ausblick
Mit der Restrukturierung des Produktionsstandortes Hagen begegnet das Unternehmen Stahlkontor dem stark steigenden Auftragsvolumen und zunehmend komplexeren Produktspektrum, welche insbesondere durch die Branchen Defense und Aviation getrieben werden. Auf insgesamt 22 000 m², wovon etwa 7 000 m² auf den Neubau entfallen, schafft Stahlkontor einen modernen und flexiblen Fertigungsstandort und bietet seinen Kunden ein umfangreiches Portfolio an Fertigungstechnologien für die Sonderanforderungen im wehrtechnischen und luftfahrttechnischen Sektor. Der Baustart dieses Projektes ist im August 2023 erfolgt. Die Bauphase, aufgeteilt in drei Bauabschnitte, erstreckt sich über etwa drei Jahre und wird voraussichtlich im August 2026 abgeschlossen sein.
Literatur
- Verein Deutscher Ingenieure: VDI 5200 Blatt 1: Fabrikplanung – Planungsvorgehen. Berlin: Beuth Verlag 2011
- Wiendahl, H.-P.: Grundlagen der Fabrikplanung. In: Betriebshutte – Produktion und Management (Teil 2). Eversheim, W.; Schuh, G. (Hrsg.). Berlin, Heidelberg: Springer-Verlag, 1996
- Wiendahl, H.-P.; Nofen, D.; Klusmann, J.-H.; Breitenbach, F.: Planung modularer Fabriken. Munchen, Wien: Carl Hanser Verlag, 2005
Felix Borgmann, M. Sc.
felix.borgmann@iml.fraunhofer.de
Fraunhofer-Institut für Materialfluss und Logistik IML
Joseph-von-Fraunhofer-Str. 2–4, 44227 Dortmund
Tel. +49 231 / 9743-458
www.iml.fraunhofer.de
Fabian Platte, M. Sc.
fabian.platte@iml.fraunhofer.de
Heiko Drawe Geschäftsführer / Managing Director
h.drawe@stahlkontor.de
Stahlkontor GmbH & Co. KG
Preußerstr. 28, 58135 Hagen
Tel. +49 2331 / 9030-92
www.stahlkontor.com