Inline-fähige Prüftechnik von Lithium-Ionen-Batterien
Bei der Fertigung von Batteriezellen in millionenfacher Anzahl ist eine gleichbleibend hohe Qualität von großer Bedeutung und die Sicherstellung eine ebensolche Herausforderung. Daneben sind Aspekte wie Kostenreduktion und Ressourcenschonung entscheidend für die zukünftige Verbreitung von Lithium-Ionen-Batterien für die Elektromobilität aber auch für den vermehrten Anwendungsfall der stationären Energiespeicherung. Produktionsintegrierte Prüfsysteme gekoppelt mit KI-basierten Datenkonzepten sind ein zentrales Element für eine effektive Qualitätssicherung und damit eine erhöhte Gesamtwirtschaftlichkeit in einer digitalen Batterieproduktion.
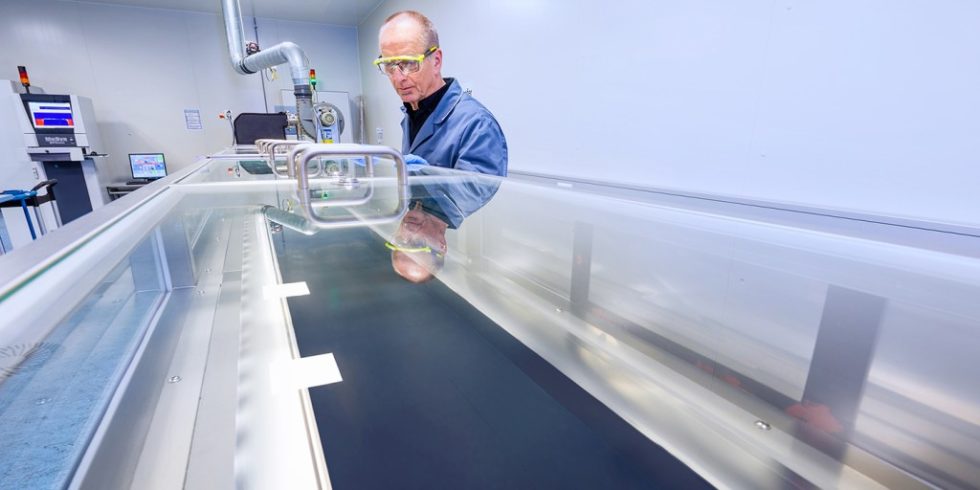
Bild 1. Elektrodenherstellung für Lithium-Ionen-Batterien im Pilotmaßstab am „Applikationszentrum Batterietechnologie“.
Foto: Fraunhofer IKTS
Ausgabe 5-2021, S. 291
1 Einleitung
Leistungsfähige und kostengünstige Energiespeicher sind eine Schlüsselkomponente für die Energiewende. Für den breiten Massenmarkt und die zukünftige Verbreitung von Lithium-Ionen-Batterien zur mobilen oder stationären Energiespeicherung müssen die Fertigungskosten für Batteriezellen weiter reduziert werden. Einen wichtigen Beitrag zur Reduzierung der Herstellkosten stellt die Senkung von Produktionsfehlern und daraus resultierenden hohen Ausschussraten dar. Um eine größtmögliche Qualität in der Batterieproduktion bei minimalem Ausschuss sicherzustellen, müssen Mängel bereits früh im Fertigungsprozess und noch vor der Weiterverarbeitung detektiert werden. Auch im Hinblick auf die ökologische Nachhaltigkeit ist eine ressourcenschonende Batteriefertigung elementar. Bisher werden die Elektroden erst am Ende der Wertschöpfung im sogenannten End-of-Line-Test auf funktionelle Fehler geprüft. Nur vereinzelt finden Prüfungen in früheren Herstellungsstadien an den Batterieslurries oder Elektrodenfolien statt. Hierbei handelt es sich hauptsächlich um prozessbegleitende, visuelle Prüfungen der Oberflächen sowie stichprobenartige Untersuchungen der Rohmaterialien, Beschichtungsdicken, Flächenbeladungen oder Prozessparameter aus der Assemblierung beziehungsweise dem Cell-Finishing. Eine vollständige und wirtschaftliche Funktionsprüfung aller Zellkomponenten auf Defekte und Fehler kann bisher nicht erfolgen.
2 Inline-fähige Prüfverfahren für die Zellfertigung
Um Produktionsfehler frühzeitig zu erkennen, entwickelt das Fraunhofer-Institut für Keramische Technologien und Systeme IKTS produktionsintegrierte Prüfsysteme, die im „Applikationszentrum Batterietechnologie“ validiert und optimiert werden. Die Wissenschaftler greifen dabei auf zerstörungsfreie optische, akustische und elektromagnetische Verfahren zurück und adaptieren diese anforderungsspezifisch an die einzelnen Produktionsschritte. Für die Auswertung der dabei gewonnenen Datenmengen werden KI-basierte Konzepte zur intelligenten Aggregation, Strukturierung und Auswertung genutzt. Somit ist es möglich, Fehlermuster zu erkennen, Produktionsabläufe zu optimieren und ein ganzheitliches Produktionsdatenmanagement zu etablieren. Dies eröffnet die Definition völlig neuer Qualitätskriterien und Standards in der Batteriezellfertigung.
Lithium-Ionen-Batteriemodule sind aus mehreren Batteriezellen zusammengesetzt. Jede Batteriezelle besteht dabei aus Anode, Kathode, einem Separator sowie dem flüssigen, ionenleitfähigen Elektrolyten. Die Grundstoffe für die einzelnen Schichten werden zu sogenannten Slurries aufbereitet und über Foliengieß- oder innovative Extrusionsverfahren auf dünne, metallische Trägerfolien aufgetragen. Anschließend werden die beschichteten Elektrodenfolien getrocknet, kalandriert, auf die entsprechende Größe zugeschnitten und zu Batteriezellen assembliert. Mit den nachfolgenden inline-fähigen Prüfsystemen ist es zukünftig möglich, die Elektroden bereits während ihrer Herstellung zerstörungsfrei auf Defekte, funktionelle Änderungen in der Materialzusammensetzung und daraus resultierende Eigenschaften oder den maßgenauen Zellaufbau zu prüfen (Bild 2).
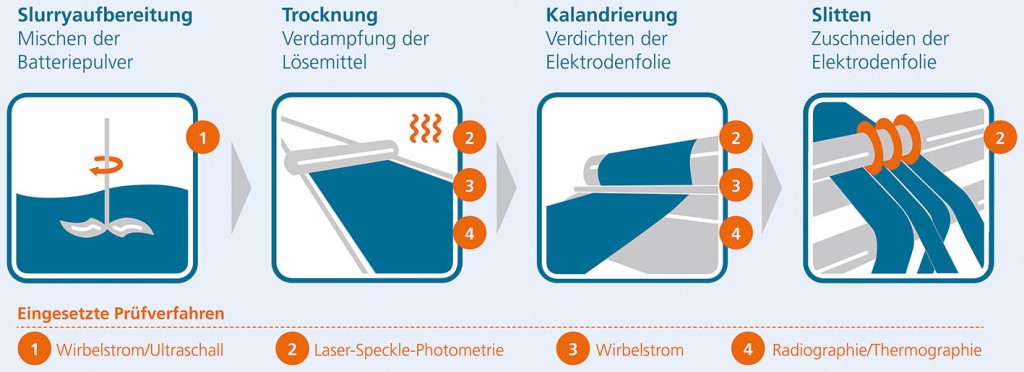
Bild 2. Neuartige, inline-fähige Prüfverfahren für die Elektrodenherstellung. Mithilfe dieser am Fraunhofer IKTS entwickelten speziellen Prüftechnik lassen sich die Qualität der Schlicker- und Folienherstellung kontinuierlich verbessern und neue Materialsysteme effektiv skalieren.
Foto: Frauhofer IKTS
2.1 Bewertung von Mischprozessen bei der Slurryaufbereitung
2.1.1 Kombiniertes Wirbelstrom- und Ultraschallverfahren
Die Mischung und Dispergierung von multimodalen Batteriepulvern zu einem homogenen Batterieslurry mit speziellen Elektrodeneigenschaften ist ein wesentlicher Prozessschritt in der Elektrodenherstellung. Dieser wird derzeit vorrangig als Batch-Prozess realisiert. Durch gezielte Verarbeitungsschritte wird am Ende des Mischprozesses eine bestimmte Partikelverteilung im Slurry erreicht und eine Reagglomeration verhindert. Eine Herausforderung stellt dabei die kontinuierliche Qualitätsüberwachung der hergestellten Elektrodenmaterialien dar. Derzeit gibt es keine geeignete Inline-Prüftechnik, welche die Prozessführung nicht beeinflusst. Das entwickelte Prüfsystem zeichnet sich durch seine kompakte Bauart sowie dessen flexible Integrationsmöglichkeiten aus. Durch die Kombination von Wirbelstrom- und Ultraschallverfahren lassen sich gleichzeitig elektrische, dielektrische und mechanische Materialeigenschaften erfassen. Dieses große Parameterspektrum liefert damit einen hohen Informationsgehalt für die Bewertung des Mischprozesses. Die integrierten Wirbelstromsensoren und Ultraschallwandler stehen nicht in direktem mechanischen Kontakt mit dem Elektrodenmaterial, so dass der Prozessfluss nicht beeinträchtigt wird. Das Prüfsystem kann ebenso Anwendung in neuartigen Extrusionsprozessen finden (Bild 3).
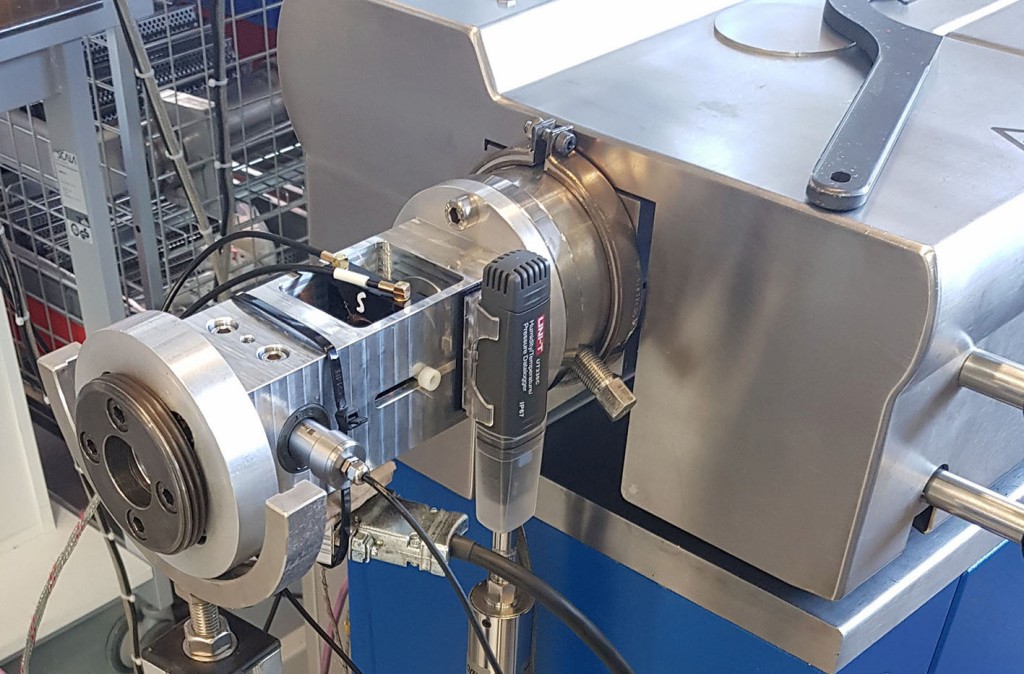
Bild 3. Multiparametrisches Prüfsystem basierend auf Wirbelstrom und Ultraschall für die Qualitätsüberwachung von Batterieslurries, Bewertung von Mischprozessen von Elektrodenmaterialien am Austritt eines Laborextruders.
Foto: Fraunhofer IKTS
2.2 Inline-Überwachung von Trocknung, Kalandrierung und Slitten
Während der Lösungsmittelverdampfung im Trocknungsprozess entstehen die funktionellen Eigenschaften der Elektroden. Gerade dieser Prozess eröffnet signifikante Kostensenkungspotenziale durch optimierte Temperaturprofile innerhalb der Trocknungszonen sowie die Detektion von Agglomeraten, Trocknungsrissen und Porositäten. Im nachfolgenden Verdichtungsprozess der Kalandrierung lässt sich die finale Porosität der Elektroden einstellen. Mit den nachfolgenden Prüfverfahren können Elektrodenfolien in den unterschiedlichen Prozessstufen geprüft werden.
2.2.1 Laser-Speckle-Photometrie
Bei der Laser-Speckle-Photometrie (LSP) wird eine optisch raue Oberfläche mit einem Laserstrahl beleuchtet und es entstehen Interferenzmuster durch Reflexion, die sogenannten Speckles. Diese werden mit einer Kamera aufgenommen. Die extrem kurzen Messzeiten der LSP prädestinieren das berührungslose Verfahren für die Inline-Charakterisierung beim Trocknen, Kalandrieren und Slitten von Lithium-Ionen-Batterien. Die LSP-Methode wurde bereits in Serienversuchen im Laboraufbau an Elektroden getestet. Anhand der Speckle-Parameter konnten Defekte wie Agglomerate, Poren und Einschlüsse von bis zu 30 µm nachgewiesen werden. Die Messdaten wurden unter Verwendung von Bildverarbeitungsverfahren ausgewertet. Durch die Erarbeitung geeigneter Algorithmen ist es zudem möglich, Messgrößen zur Identifikation der Verdichtungsdichte festzulegen (Bild 4).
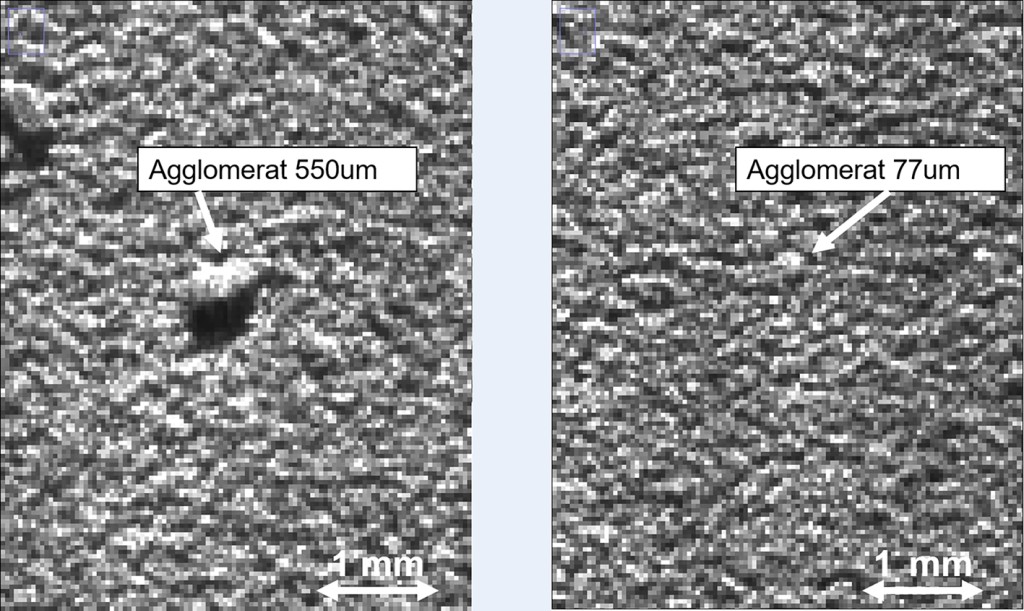
Bild 4. Mithilfe der Laser-Speckle-Photometrie können verschiedene Defekte nachgewiesen werden, wie diese Agglomerate mit einem Durchmesser von 550 µm und 77 µm.
Foto: Fraunhofer IKTS
2.2.2 Wirbelstromverfahren
Während der verschiedenen Trocknungsstadien im Trocknungsprozess ändert sich die elektrische Leitfähigkeit des Elektrodenmaterials. Daher ist die Wirbelstromprüfung ein potenzielles Verfahren, um Fehlerbilder zu ermitteln. Erste Versuche zeigten vielversprechende Korrelationen des Trocknungsverhaltens zum Wirbelstromsignal. Die leistungsstarken und modularen Prüfsysteme der „EddyCus“ Pro-II Serie eignen sich besonders für die Integration in den Automationsprozess einer Produktionslinie. Am Fraunhofer IKTS wird erprobt, wie mithilfe dieses Prüfsystems der Trocknungsverlauf inline überwacht werden kann. Dafür werden die Sensoren an mehreren verschiedenen Positionen im Trocknungstunnel integriert. Das Prüfsystem kann ebenso nach dem Trocknen und Kalandrieren eingesetzt werden, um Fehler wie Schichtinhomogenitäten (Dicke, Zusammensetzung, Leitfähigkeit) über die gesamte Beschichtungsbreite zu detektieren.
2.2.3 Aktive Thermographie und Radiographie
Mit der aktiven Thermograpie und Radiographie können flache, planare Strukturen wie Elektroden für Lithium-Ionen-Batterien während der Fertigung berührungslos untersucht werden. Durch die hohe Geschwindigkeit beider Verfahren eignen sie sich hervorragend für eine Inline-Prüfung während der Trocknung sowie vor und nach der Kalandrierung. Derzeit werden beide Verfahren am Fraunhofer IKTS auf ihre Eignung bewertet. Mit beiden Verfahren können grundsätzlich Inhomogenitäten wie Poren, Einschlüsse, Agglomerate, Risse, aber auch Dichte- und Dickenschwankungen der Elektrodenfolie abgebildet und ausgewertet werden. Durch ihre Kombination ist eine sehr hohe Detektionssicherheit möglich, bei gleichzeitig reduzierter Anfälligkeit für Fehlmessungen. Während der grundsätzliche Aufbau beider Verfahren im Inline-System sehr ähnlich ist, unterscheiden sie sich im physikalischen Messeffekt. Während bei der Thermographie geringfügige thermische Effekte im Material analysiert werden, detektiert die Radiographie Materialveränderungen, die sich im Absorptionsverhalten von Röntgenstrahlen äußern. So lassen sich die Vorteile beider Methoden in vollem Umfang nutzen (Bild 5).
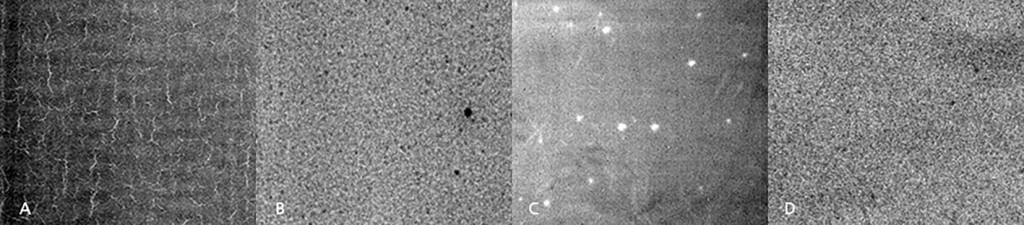
Bild 5. Mit der einfachen Durchstrahlung der dünnen Batteriefolien mittels Radiographie können Fehler wie dünne Risse (A) oder zu große Agglomerate (B) detektiert werden. Mit der Thermographie lassen sich Defekte wie Fischaugen (C) oder verschieden große Agglomerate in der Folie (D) frühzeitig entdecken.
Foto: Fraunhofer IKTS
3 Digitalisierung der Batteriefertigung
Mit Blick auf den Transformationsprozess in der Automobil- und Energiewirtschaft spielt eine vernetzte, digital unterstützte Produktion und Qualitätssicherung von Batteriezellen und -modulen zukünftig eine große Rolle. Die umfassende Digitalisierung der industriellen Produktion ist ein Schlüssel, um die gesamte Fertigungskette zu optimieren und somit die Wettbewerbsfähigkeit von Unternehmen zu steigern. Daher erprobt das Fraunhofer IKTS auf industrienahen Pilotlinien innovative datengetriebene Ansätze der Prozessüberwachung, Steuerung und Qualitätssicherung. Mittels neuester Methoden der Künstlichen Intelligenz und Einbindung in Machine-Learning-Konzepte ist es so möglich, Batteriefertigungsprozesse modular und bedarfsgerecht auszulegen, die Produktqualität signifikant zu erhöhen und so die Gesamtwirtschaftlichkeit der Batterieproduktion zu steigern. Durch die Nutzung industrieller Standardschnittstellen wie OPC-UA und Softwareframeworks wird das Übertragen der Softwarelösungen auf andere industrielle Prozesse wesentlich vereinfacht. Neben spezifischen Fragestellungen der Batterieentwicklung lassen sich die Erkenntnisse in Zukunft auch auf die Fertigung von Brennstoffzellen für die Wasserstoffwirtschaft adaptieren.
Das könnte Sie auch interessieren:
Live Soll-Ist-Abgleich mit Augmented Reality
Prof. Dr.-Ing. Henning Heuer
, Dipl. Ing. Marcel Wild
, Dr.-Ing. Sebastian Reuber
, Susanne Hillmann, M. Sc. (NDT)
, Dr.-Ing. Beatrice Bendjus
, Dr.-Ing. Ulana Cikalova
, Martin Schulze, M. Sc. (NDT)
Fraunhofer-Institut für Keramische Technologien und Systeme IKTS
Maria-Reiche-Str. 2, 01109 Dresden
Tel. +49 351 / 88815-630
henning.heuer@ikts.fraunhofer.de
www.ikts.fraunhofer.de