Mobile Roboter zur freien Verkettung von Montagestationen
Moderne Produktionssysteme müssen stetig steigenden Herausforderungen, zum Beispiel durch die Individualisierung von Produkten oder gestiegene Variantenvielfalt, genügen und daher hoch flexibel sein. Die klassische, verkettete Produktion stößt dabei zunehmend an ihre Grenzen. Das Werkzeugmaschinenlabor WZL der RWTH Aachen und das Fraunhofer-Institut für Produktionstechnologie entwickeln daher im BMBF-geförderten Forschungsprojekt „freeMoVe“ gemeinsam mit Industrieunternehmen eine Montageorganisationsform, die „freie Verkettung“.
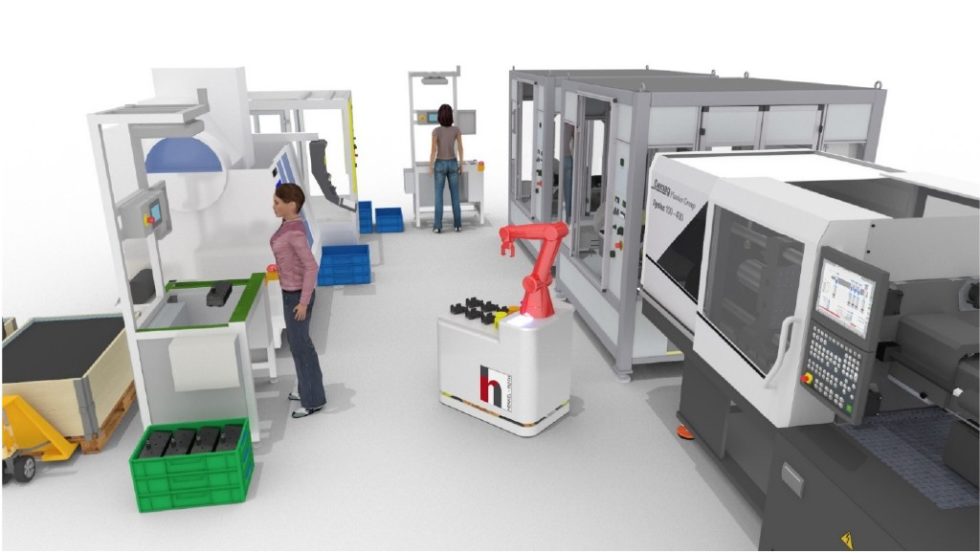
Eine Darstellung der typischen Einsatzumgebung der Mensch-Roboter-Koexistenz Bild: WZL der RWTH Aachen
Der Beitrag beschreibt den Einsatz mobiler Roboter für Transport und Handling in frei verketteten Montagesystemen. Beschrieben werden die Anforderungen an mobile Roboter, die technischen und organisatorischen Herausforderungen, die Sicherheit für den Menschen beim Einsatz mobiler autonomer Roboter, die Ansteuerung der Roboter mittels eines Flottenmanagers sowie die Einbindung der Roboter in das Gesamtkonzept der frei verketteten Montage
1 Wandlungsfähige und hochflexible Transportsysteme zur Montage kleiner Losgrößen
Globale Megatrends, beispielsweise der effizientere Umgang mit natürlichen Ressourcen, sind zentrale Treiber für die Weiterentwicklung der Produktionstechnik [1]. Faktoren wie kundenindividuelle Produkte, große Variantenvielfalt und kürzere Produktlebenszyklen sorgen dafür, dass moderne Produktionssysteme stetig steigenden Anforderungen genügen müssen [2]. Die industrielle Montage als zentraler Ort der Wertschöpfung in produzierenden Unternehmen ist dabei besonders stark von diesen Herausforderungen betroffen [3–5]. Die klassische Form der Montage als lineare Verkettung von Stationen wird den Anforderungen nicht mehr gerecht, wenn zusätzliche Prozesse, Änderungen im Prozessablauf oder in der Bearbeitungszeit erforderlich sind. Grund dafür sind physikalische Einschränkungen bei den klassischen spurgebundenen Transportsystemen, sowie weitere montagespezifische Herausforderungen, zum Beispiel die Taktzeitspreizung [2].
Als Lösungsansatz wurde die Entwicklung einer neuen Organisationsform für wandlungsfähige und hochflexible Montagesysteme gewählt, die im Rahmen des vom Bundesministerium für Bildung und Forschung geförderten Forschungsprojektes „freeMoVe“ vom WZL der RWTH Aachen und vom Fraunhofer IPT in Kooperation mit Industrieunternehmen erforscht, gestaltet und umgesetzt wird. Kern dieser neuen Montageform ist die freie Verkettung der einzelnen Montagestationen, welche neben einer schnellen Reaktion auf sich ändernde Anforderungen auch die Montage kundenindividueller Produkte bis Losgröße 1 erlaubt [6].
Um die freie räumliche Verkettung realisieren zu können, wird ein flexibles Transportsystem benötigt, welches in der Lage ist, dynamische Auftragsrouten umzusetzen und somit die kurzfristige Erstellung und Umsetzung von Transportaufträgen ermöglicht. Dabei sollen keine Restriktionen in Bezug auf die Flexibilität der Verkettung durch das Transportsystem entstehen. Jede Montagestation soll von jeder anderen Montagestation aus zeitlich und räumlich flexibel erreichbar sein [2]. Die Umsetzung des flexiblen Transportsystems kann auf verschiedene Arten erfolgen. Entweder mit Fahrerlosen Transportfahrzeugen (FTF), die als flurgebunden sowie automatisch gesteuert definiert sind und ausschließlich dem passiven Materialtransport dienen [7], oder durch den Einsatz eines mobilen Roboters. Ein mobiler Roboter ist eine autonome Fahrplattform mit integriertem Leichtbauroboter und Ablagefläche für Transportgüter oder Transporthilfsmittel, der zusätzlich zum Materialtransport durch den Roboterarm auch die Möglichkeit der Handhabung der transportierten Güter bietet [8]. Der bisherige Einsatz von mobilen Robotern im produktionstechnischen Bereich beschränkt sich auf Aufgaben in der Intralogistik mit begrenzter Produktvarianz und keinem Einsatz von Mensch-Roboter-Kollaboration (MRK).
Der Beitrag beschreibt den Einsatz von mobilen Robotern direkt im Montageumfeld, was eine flexible und freie Verkettung von Montagestationen ermöglichen soll.
Zunächst werden die Anforderungen an mobile Roboter aufgezeigt. Neben allgemeinen, anwendungsspezifischen Anforderungen, wie beispielsweise der Handhabungstechnik, werden insbesondere die Möglichkeiten und Rahmenbedingungen der Sicherheitstechnik diskutiert. Im Anschluss folgen Erörterungen zu anwendungsfallübergreifenden Fragestellungen zur Energietechnik, Mobilität und der Schaffung universeller Schnittstellen.
Auf den allgemeinen Anforderungen und Konzepten aufbauend werden anschließend die Integrationsaspekte und die Herausforderungen bei der technischen Umsetzung dargelegt.
Folgend wird die Vorgehensweise bei der Einbindung mobiler Roboter in eine bestehende Montageumgebung unter dem Aspekt der MRK sowie in das spezifische Architekturkonzept der frei verketteten Montage diskutiert. Abschließend erfolgt eine Zusammenfassung zum Einsatz von mobilen Robotern in der frei verketteten Montage sowie ein Ausblick auf künftige Entwicklungen und Forschungsvorhaben.
2 Mobiler Roboter zur Flexibilisierung des Produkt- und Teiletransports
Die Kernkompetenz eines mobilen Roboters ist der flexible Produkttransport [9]. Die Kombination aus Fördertechnik und Handhabung ermöglicht den Verzicht auf starre Transfersysteme und ortsfeste Handling- und Positioniersysteme. Der Transport findet nur dort statt, wo er zum jeweiligen Zeitpunkt benötigt wird. Der zum Transport benötigte Raum wird effektiver genutzt. Damit ist auch eine zeitnahe Reaktion auf sich verändernde Produktionsszenarien, zum Beispiel eine Skalierung der Ausbringung oder die einfache Integration neuer Produktvarianten, möglich. Als Folge wird die Wandlungsfähigkeit der Anlage durch Modularität sowie durch den Einsatz eines solchen flexiblen Transports verbessert.
2.1 Anforderungen an mobile Handhabungs- und Logistikroboter
Mit der zusätzlichen Möglichkeit der Handhabung lassen sich weitere Aufgabenfelder erschließen: Ein Materialtransport zur Verkettung von Stationen, der bisher eine auch körperlich belastende Aufgabe darstellte oder aufwendige, unflexible sowie platzraubende Transfertechnik erforderten ist so effizient umsetzbar. Damit kann der mobile Roboter auch als Ergonomiehilfe dienen und die ermüdungsfreie Positionierung von schwereren Bauteilen realisieren. Montageautomaten lassen sich ohne zusätzliche mechanische Schnittstelle be- oder entladen, womit zum Beispiel auch ein One-Piece-Flow aufwandsarm und flexibel umgesetzt werden kann. Weiterhin können klassische Aufgaben der Intralogistik wie die Zuführung von Schüttgut oder die Kommissionierung übernommen werden.
In Experteninterviews wurden diese technischen Aufgabenstellungen diskutiert und die zur Realisierung notwendigen Anforderungen abgeleitet. Diese Anforderungen basieren auf speziellen Anwendungsszenarien, sind jedoch allgemeingültig aufbereitet und lassen sich somit auf eine große Bandbreite von Anwendungsfällen übertragen. Die Themenbereiche der Anforderungen sowie eine Darstellung der Integration eines mobilen Roboters in eine Montageumgebung ist im nächsten Bild zu sehen.
Der mobile Roboter muss mit kompakten Abmessungen entwickelt werden, um auch in engen Umgebungen zu agieren, die ursprünglich nicht für den Einsatz fahrerloser Transportfahrzeuge geplant wurden. Weiterhin muss für solche Umgebungen eine freie Navigation gewährleistet sein, damit eine flexible Wahl der Fahrtroute getroffen werden kann. Auch müssen Ausweichmanöver und Hindernisumfahrungen möglich sein.
Die Traglast des Roboters sowie der mobilen Plattform richtet sich nach dem jeweiligen Anwendungsfall. Aufgrund der Notwendigkeit eines geteilten Arbeitsraumes zwischen Mensch und Roboter bietet sich jedoch der Einsatz von für die MRK geeigneten Robotern an. Gängige auf dem Markt verfügbare Systeme bieten eine Traglast im Bereich von 10 kg. Die Transportlast der Plattform sollte um mehrere auch schwere Produkte mit Werkstückträger oder magazinierte Produkte tragen zu können, im Bereich von 100 kg sein. Die angegebenen Lasten stellen einen universellen Bereich dar, der eine Großzahl von Anwendungen und möglichen Erweiterungen abdeckt. Diese Angaben können als Hilfestellung für eine erste Analyse dienen, wenn der Einsatz mobiler Roboter in der Montage diskutiert wird.
Allgemein darf durch den mobilen Roboter die Sicherheit der Mitarbeiter in der Montageumgebung nicht beeinträchtigt sein. Außerdem sollten sich die Mitarbeiter weiterhin frei bewegen können und im Idealfall mit dem mobilen Roboter kollaborieren, was in bestimmten Anwendungsfällen einen wirtschaftlichen Vorteil bedeuten kann.
Die Greiftechnik des Roboters ist so auszulegen, dass verschiedene Produktvarianten gehandhabt werden können und dies nicht limitierend für die Durchführung des Transportauftrags ist.
Das Energiemanagement sollte eigenständig sein und der mobile Roboter sollte autonom und ohne manuellen Akkuwechsel betrieben werden können.
Weiterhin sollte die Integration in eine bestehende Montageumgebung ohne große Beeinträchtigung der Produktion erfolgen und der flexibel einzusetzende mobile Roboter sollte vorhandene mechanische Schnittstellen, aber auch bereits bestehende Kommunikations-Schnittstellen nutzen.
Neben der Erfüllung der technischen Anforderungen müssen die mobilen Roboter eine allgemeine Entlastung und Vereinfachung des Warenflusses ermöglichen – der Einsatz von mobilen Robotern darf keine zusätzliche Belastung beziehungsweise ein unverständliches und kompliziertes, schwer zu beherrschendes System sein. Schlussendlich muss der Einsatz für die Betriebsabläufe einen kalkulierbaren Mehrwert bieten und eine Produktivitätssteigerung muss gewährleistet sein.
2.2 Herausforderungen bei der technischen Konzeption mobiler Roboter
Im Folgenden werden die Integrationsaspekte beziehungsweise die Herausforderungen, die bei der technischen Umsetzung der Anforderungen auftreten, beschrieben. Auf Basis der betrachteten Anwendungsfälle wird von einer Integration des mobilen Roboters in ein bestehendes Produktionsumfeld ausgegangen, woraus sich spezielle Herausforderungen ergeben. Logistik und Materialtransport sind für Menschen geplant und ausgelegt, daher muss der Arbeitsraum des Roboters angepasst werden.
Zum Transport verschiedener Aufträge muss eine modulare Transportfläche entwickelt werden, die in der Lage ist, variierende Werkstückträger oder Produktschnittstellen aufzunehmen.
Um eine flexible Handhabung von Varianten zu gewährleisten ist ein Einsatz von wechselbaren Robotergreifern oder -fingern beziehungsweise Universalgreifern sinnvoll. Die Transportfläche und die Variation der Robotergreifer können in einem modularen Baukasten zusammengefasst werden. Zum Erkennen von Bauteilen, zum Positionieren des Robotergreifers und zum Ausgleich von Toleranzen bei der Navigation kommen Kamerasysteme zum Einsatz.
Zur freien Navigation und Beweglichkeit auch in engen Umgebungen muss ein flächenbewegliches Fahrwerk eingesetzt werden. Damit ist auch eine Rotation des mobilen Roboters auf der Stelle möglich. Zur eigenständigen Navigation wird eine Referenzierung und Orientierung an Landmarken, also auffälligen und wiedererkennbaren Objekten, in der Umgebung mittels eines Laserscanners eingesetzt. Wenn eine Energieversorgung für autonomen Betrieb gewährleistet werden soll, muss ein autark agierendes System sich selbstständig mit Energie versorgen. Hierfür müssen Ladestationen autonom und dem Bedarf entsprechend angesteuert werden können.
Weiterhin müssen die Sicherheitseinrichtungen flexibel ausgelegt werden. Vorhandene, fest installierte Umgebungselemente wie Schutzzäune, aber auch dynamische Elemente wie Personen oder Rollwagen, stellen Hindernisse dar und müssen erfasst werden. Die Laserscanner, welche die Navigation durch das Erkennen der Umgebung ermöglichen, können gleichzeitig als berührungslos wirkendes Schutzsystem eingesetzt werden. Die Laserscanner erkennen Hindernisse im Fahrweg oder in der Sicherheitszone beim Handling und stoppen oder verlangsamen die Maschine, wenn sich Personen oder andere Objekte der Gefahrenzone annähern. Die Schutzfelder passen sich geschwindigkeitsabhängig und geometrisch an die Umgebung an. Das heißt, je nach Fahrtroute wird vorausschauend die vor dem mobilen Roboter liegende Strecke gescannt. So fährt ein virtueller und adaptiver Schutzzaun immer mit dem Fahrzeug mit.
Wird ein mobiler Roboter wie beschrieben als Transportsystem zwischen den Montagstationen eingesetzt, handelt es sich um eine „Mensch-Roboter-Koexistenz“. Zusätzlich zu einer Handhabung durch den Roboter besteht auch die Möglichkeit einer MRK. Die Umsetzung einer MRK ist abhängig vom jeweiligen Anwendungsfall, dem zu montierenden Produkt sowie den äußeren (räumlichen) Umgebungsbedingungen. Die Mensch-Roboter-Koexistenz hingegen kann allgemein betrachtet werden, da Mensch und Roboter nicht in direktem Kontakt zueinanderstehen. Beispielsweise ist die Kraft, ab welcher der Roboter bei Kontakt mit dem Menschen abschalten muss, bei jedem Anwendungsfall und in jeder Umgebung identisch [10]. Beiden Einsatzszenarien von (mobilen) Robotern ist gemein, dass sie insbesondere jegliche Gefahr für den Menschen minimieren und nach Möglichkeit gänzlich ausschließen sollen [10, 11].
Aufgrund der genannten Forderungen an mobile Roboter sowie des Einsatzes von Mensch und Robotern in einem gemeinsam genutzten Arbeitsraum sind solche Systeme insbesondere bei großen, schweren oder scharfkantigen Bauteilen wie beispielsweise Blechen schwierig umsetzbar. Zwar können Greifer und Roboter für den koexistenten oder kollaborativen Einsatz entsprechend ausgelegt werden, allerdings gelten die gleichen Anforderungen auch an das zu fertigende, montierende oder transportierte Bauteil. Ebenfalls müssen beispielsweise die Taktzeiten beziehungsweise eine festgelegte Durchlaufzeit eingehalten oder nur gering beeinflusst werden, weshalb der Einsatz kollaborativer oder kooperativer Handhabungs-, Logistik- und Montageaufgaben nicht immer wirtschaftlich ist und im Vorfeld der Implementierung geprüft werden muss.
Generell kritisch sind Lastübergabestellen, also Stellen, an welchen der Roboter nah an Wänden, Ecken oder Maschinenkanten rangieren muss. Hier besteht potentiell die Gefahr von Quetsch- und Scherstellen, die es mit verschiedenen Maßnahmen zu verhindern gilt. Das können Stehverhinderer in Form von beispielsweise schrägen Bodenelementen oder Schaumstoffpuffern sein, die diese harten Scherstellen eliminieren. Im Stationär- und Handlingbetrieb muss die Umgebung lückenlos abgesichert werden. Beispielsweise dürfen sich keine Personen unerkannt im Gefahrenbereich aufhalten. Je nach Umgebung können Anpassungen an den vorhandenen Maschinen notwendig werden, wie zusätzliche Verkleidungsteile unter Förderbändern.
Die Detailkonstruktion, Auslegung der Greifer und Roboterbewegungen werden durch die Aufgabenstellung und Werkstückgeometrie bestimmt. Eine redundante Robotersteuerung erlaubt sicher überwachte Bewegungen des Greifers. So werden nicht nur Geschwindigkeiten überwacht, sondern auch der Arbeitsraum des Roboters. Er wird für die jeweilige Aufgabe so konfiguriert, dass sich der Roboter nur in Richtung der zu bearbeitenden Station mit begrenzter, notwendiger Reichweite bewegt. Auch bei der Handhabung müssen Quetsch- und Scherstellen minimiert und gegebenenfalls abgesichert werden. Dies betrifft besonders die Werkstückträger und Ablagen, aber auch Kanten von Kisten. Greifer und Roboterbewegungen mit sicherer Kraftbegrenzung oder zusätzliche Sensorik können dann notwendig werden.
Die Integrationsaspekte und die aus den Anforderungen resultierenden Herausforderungen lassen sich wie folgt zusammenfassen:
– Modulare Transportfläche und flexible Greiftechnik zur Aufnahme verschiedenster Varianten.
– Flächenbewegliches Fahrwerk zu Navigation in engen Umgebungen.
– Sicherheitseinrichtungen, zum Beispiel in Form eines Laserscanners, von in der Umgebung installierten Maßnahmen oder einer angepassten Greiftechnik.
3 Einbindung mobiler Roboter in das Architekturkonzept frei verketteter Montagesysteme
Die neue Montageorganisationsform der frei verketteten Montage bedingt aufgrund der geänderten Rahmenbedingungen neue Anforderungen an den Einsatz und die Einbindung eines oder mehrerer mobiler Roboter in der Produktion. Im Folgenden wird daher die vereinfachte Architektur des Gesamtsystems mit dem Fokus auf dem parallelen Einsatz von mobilen Robotern vorgestellt. Der Einsatz mehrerer mobiler Einheiten in der Montageumgebung wird betrachtet, da diese redundante Auslegung die Verfügbarkeit und den Durchsatz maßgeblich erhöht. Dies führt wiederum zu einer erhöhten Komplexität des Steuerungskonzepts und folglich zu der Notwendigkeit eines Flottenmanagers.
Das nachfolgende Bild zeigt das grundlegende Architekturkonzept der frei verketteten Montage sowie das Steuerungskonzept eines integrierten mobilen Roboters.
Den zentralen Baustein einer frei verketteten Montageorganisationsform bildet das Leitsystem. Hauptaufgabe des Leitsystems ist die kontinuierliche Planung der individuellen Auftragsrouten für ein Produkt. Das Leitsystem erhält alle relevanten Informationen zur Montage von dem übergeordneten Planungssystem (zum Beispiel einem ERP-System) und übergibt die spezifischen Auftragsdaten über die Logistiksteuerung an den sogenannten Flottenmanager (vgl. [12]).
In der vorgestellten Architektur ist die Anbindung von verschiedenen Montage- oder Transportressourcen sowie von externen Systemen (zum Beispiel Informationssystem) abgebildet. Die Softwareagenten, die zur Anbindung dienen, fungieren dabei als digitales Abbild aller Ressourcen innerhalb des Leitsystems und werden zur Steuerung der Ressourcen genutzt. Verschiedene bestehende und neue Ressourcen werden durch ein „Integration Framework“ in das Agentensystem integriert [6]. Das Planungssystem übermittelt Auftragsdaten sowie einen Digitalen Schatten, welcher einem Datenmodell entspricht, das alle produkt- und produktionsspezifischen Informationen enthält, an das Leitsystem. Das Leitsystem berechnet dann unter Beachtung aller möglichen Routen, des aktuellen Systemzustands und definierter Zielgrößen die optimale Route für das Produkt. Der Flottenmanager erhält im Anschluss den Transportauftrag für die spezifische (Teil-) Auftragsroute in Form eines Start- und Zielpunktes sowie weitere Informationen über den Transport, wie beispielsweise die Größe und das Gewicht des Produkts. Im Anschluss bestimmt der Flottenmanager auf Grundlage des Wissens über alle Verfügbarkeiten, Zustände und Positionen aller im System bekannten mobilen Roboter denjenigen Roboter, welcher die Aufgabe im Gesamtkontext möglichst effizient durchführen kann. Der Flottenmanager bildet somit ein peripheres spezialisiertes zweites Leitsystem, welches spezifisch auf die Anforderungen der Einsatzplanung von mobilen Robotern angepasst ist. Dies erlaubt die Trennung der Aufgaben und dient einem modularen Aufbau, da das Leitsystem ausschließlich die primäre Routenfindung koordiniert, während der Flottenmanager die – nicht zwingend in jedem Szenario des Einsatzes der freien Verkettung notwendige – Steuerung der mobilen Roboter übernimmt.
Der Informationsaustausch zwischen dem Flottenmanager und den gekoppelten mobilen Robotern ist mittels einer Input-Output-Schnittstelle (I/O) realisiert. Der gewählte Roboter erhält unter anderem die Auftragsdaten sowie Informationen zum Status der Peripherie. Das Zentrum des internen Steuerungskonzepts des mobilen Roboters bildet ein Industrie-PC (IPC), welcher auch die Eingabe- und Ausgabeinformationen bei der Kommunikation mit dem Flottenmanager verantwortet. Der IPC umfasst Module zur Navigation, Signalverarbeitung sowie Steuerung. Navigationsinformationen werden in Drehzahl, Leitwinkel, etc. übersetzt und an die jeweiligen Antriebe weitergegeben, die ihren Zustand, besonders in Ausprägung der Drehzahl, an die Sicherheitssysteme weitergeben. Die Sicherheitssysteme prüfen in Echtzeit die vorliegenden internen und externen Bedingungen und nutzen diese ebenfalls zur Steuerung der Antriebe, wobei sie die Anweisungen des leitenden IPC überschreiben können. Erst durch die so ermöglichte verringerte Reaktionszeit des Systems wird ein Betrieb in Koexistenz mit dem Menschen ermöglicht. Die Laserscanner und Sicherheitssysteme melden zudem permanent Landmarken und weitere Informationen zum IPC zurück, sodass dieser mithilfe der globalen Informationen weitere Handlungsbefehle an die Antriebe erteilen kann.
Das Modul der Signalverarbeitung und Steuerung des IPC ermöglicht darüber hinaus, unter Zuhilfenahme eines gängigen Industrieroboters, die Ansteuerung des Greifsystems. Das Greifsystem befindet sich außerhalb des direkten Einflusses des mobilen Roboters. Der Roboter steuert somit den hier als externes System betrachteten Greifer durch Handlungsanweisungen. Der Greifer liefert gleichzeitig Informationen zu seinem Status an den Roboter zurück.
Neben den primären Aufgaben des Roboters, das heißt den wertschöpfenden Montageaufgaben sowie den nicht-wertschöpfenden Logistik- und Handhabungsoperationen, sendet das Batterie- und Elektronikmodul permanent den Akkuzustand an den IPC sowie die Ladebereitschaft und Batteriespannung des Roboters an das externe Ladegerät. Diese Informationen werden zeitgleich an den Flottenmanager übergeben. Der Flottenmanager kann so flexibel im Sinne der aktuellen und zukünftigen Auftragslage sowie des Zustands des Gesamtsystems entscheiden, zu welchem Zeitpunkt der jeweilige Roboter zum Laden an die Ladestation fahren soll.
4 Zusammenfassung und Ausblick
Die frei verkettete Montage als neue Organisationsform erlaubt eine Flexibilisierung der Produktion aufgrund der Auflösung starr verketteter Produktionssysteme. Integraler Bestandteil zur Gewährleistung der Flexibilität sind mobile Roboter, welche sowohl Logistik- als auch Handhabungsaufgaben durchführen und mit dem Menschen kollaborieren können. Besondere Beachtung gilt der Sicherheit, da Mensch und Maschine im selben Arbeitsraum operieren.
Aufgrund des aktuellen Entwicklungsstadiums liegt das notwendige Erfahrungswissen für die Absicherung eines reibungsfreien Betriebs noch nicht vor. Zur Gewährleistung einer bestimmten Transportkapazität sind beispielsweise Planungen mithilfe von Simulationsstudien durchzuführen. Diese ermöglichten die Bestimmung der theoretischen Auslastung oder die benötigte notwendige Flottengröße. Hierfür ist eine Nutzung der beschriebenen Leitsystem-Infrastruktur mit virtuellen mobilen Robotern, die simulierte Statusrückmeldungen geben, sinnvoll. Im Zuge dessen kann die Leitsystemarchitektur auch auf eventuelle Schwachstellen oder Verbesserungspotentiale getestet werden.
Literatur
[1] ElMaraghy, H.; Schuh, G.; ElMaraghy, W. et al.: Product variety management. In: CIRP Annals – Manufacturing Technology 62 (2013) 2, pp. 629–652
[2] Schmitt, R.; Göppert, A.; Hüttemann, G. et al.: Frei verkettete wandlungsfähige Montage // Internet of Production für agile Unternehmen. In: AWK Aachener Werkzeugmaschinen-Kolloquium, 18.–19. Mai 2017, Aachen: Apprimus, 2017
[3] Hu, S. J.; Ko, J.; Weyand, L. et al.: Assembly system design and operations for product variety. In: CIRP Annals – Man. Tech. 60 (2011) 2, pp. 715–733
[4] Lotter, B.: Montage in der industriellen Produktion. Ein Handbuch für die Praxis. Berlin: Springer, 2006
[5] Brecher, C.: Integrative Production Technology for High-Wage Countries. Berlin: Springer, 2012
[6] Schmitt, R.; Hüttemann, G.; Grunert, D.: Montage. Automatisiert und flexibel. In: WGP. Stand: 2018. Internet: https://wgp.de/de/montage-automatisiert-flexibel/. Zugriff am 15.06.2018
[7] Verein Deutscher Ingenieure: VDI 2510 Blatt 2: Fahrerlose Transportsysteme. Berlin: Beuth, 2013
[8] Henkel + Roth: Der mobile robot beweist Teamgeist. Dynamische Automatisierung – ideal für One-Piece-Flow-Anlagen. Stand: 2018. Internet: https://www.henkel-roth.com/de/unternehmen/news/2014/der-mobile-robot-beweist-teamgeist. Zugriff am 15.06.2018
[9] Kaliappan, S.; Lokesh, J.; Mahaneesh, P. et al.: Mechanical Design and Analysis of AGV for Cost Reduction of Material Handling in Automobile Industries. In: International Research Journal of Automotive Technology (2018) 1, pp. 1–7
[10] Shen, Y.: System für die Mensch-Roboter-Koexistenz in der Fließmontage. Dissertation, Technische Universität München, 2015
[11] DIN EN ISO 10218-1: Industrieroboter – Sicherheitsanforderungen – Teil 1: Roboter. Deutsche Fassung, 2011
[12] Göppert, A.; Hüttemann, G.; Jung, S. et al.: Frei verkettete Montagesysteme. Ein Ausblick. In: ZWF, 113 (2018) 3, S. 151–155
Amon Göppert, M. Sc., Dipl.-Ing. Dipl.-Wirt.Ing. Guido Hüttemann, Prof. Dr.-Ing. Robert H. Schmitt Werkzeugmaschinenlabor WZL der RWTH Aachen Campus-Boulevard 30, 52074 Aachen Tel. +49 (0)241 / 80-27400 g.huettemann@wzl.rwth-aachen.de www.wzl.rwth-aachen.deDennis Grunert, M. Sc. Fraunhofer-Institut für Produktionstechnologie IPT Steinbachstr. 17, 52074 Aachen Tel. +49 (0)241 / 8904-376 dennis.grunert@ipt.fraunhofer.de www.ipt.fraunhofer.deStephan Pöhler, M. Sc. Henkel + Roth GmbH Gewerbepark Am Wald 3D, 98693 Ilmenau Tel. +49 (0)3677 / 6439-30 s.poehler@henkel-roth.de www.henkel-roth.deDieses Forschungs- und Entwicklungsprojekt wird mit Mitteln des Bundesministeriums für Bildung und Forschung (BMBF) im Programm „Innovationen für die Produktion, Dienstleistung und Arbeit von morgen“ (Förderkennzeichen: 02P15A140) gefördert und vom Projektträger Karlsruhe (PTKA) betreut. Die Verantwortung für den Inhalt dieser Veröffentlichung liegt bei den Autoren. Bei diesem Beitrag handelt es sich um einen Fachaufsatz, der von Experten auf diesem Gebiet wissenschaftlich begutachtet und freigegeben wurde (peer-reviewed).