3D-gedruckte Fasern sollen Fahrzeugbau nachhaltiger machen
Das Fraunhofer-Institut für Betriebsfestigkeit und Systemzuverlässigkeit LBF präsentiert auf der Hannover Messe 2024 fortschrittliche naturfaserverstärkte Compounds. Diese sind für die High Speed Additive Manufacturing Technologie optimiert und sollen insbesondere den Fahrzeugbau nachhaltiger machen.
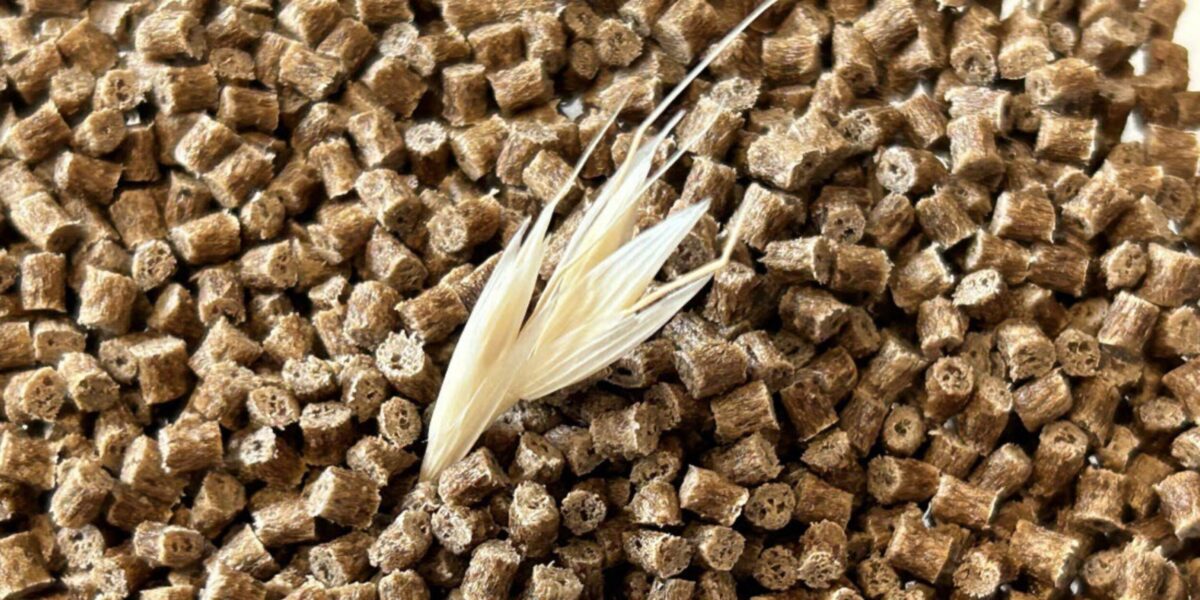
Expertenteams am Fraunhofer LBF haben neuartige naturfaserverstärkte Compounds für die Verarbeitung im High Speed Additive Manufacturing entwickelt.
Foto: Fraunhofer LBF
Das Forschungsprojekt „ECO2-LInE“ hat zum Ziel, schwere Metallkonstruktionen in Landfahrzeugen durch leichtere naturfaserverstärkte Kunststoffbauteile zu ersetzen. Das Projekt wird vom Bundesministerium für Wirtschaft und Klimaschutz im Rahmen des Technologietransferprogramms Leichtbau (TTP LB) gefördert. Die neue Fertigungsmethode, die am Fraunhofer LBF in Darmstadt entwickelt wird, gewährleistet die Langzeitstabilität und Witterungsbeständigkeit dieser Bauteile. Ergebnisse und Verfahren werden auf dem Fraunhofer-Gemeinschaftsstand B24 in Halle 2 der Hannover Messe vorgestellt.
Beitrag zum Klimaschutz
Im Projekt „ECO2-LInE“ steht die Gewichtsreduzierung durch neuartige Leichtbaukomponenten im Vordergrund. Ziel ist es, den Herstellungsprozess ökobilanziell günstig zu gestalten und eine verbesserte Recyclingfähigkeit zu erreichen. Damit wird ein wesentlicher Beitrag zum Klimaschutz geleistet. Hauptanwendungen sind unter anderem Sitzstrukturen für Elektrofahrzeuge, Zugwagenübergänge und Aufbauten für Pickups.
Neues Verfahren für mehr Beständigkeit
Um die Ersatzteile herzustellen, nutzen die Forscherinnen und Forscher das am Fraunhofer-Institut für Werkzeugmaschinen und Umformtechnik IWU entwickelte additive Hochgeschwindigkeitsverfahren SEAM. Dieses 3D-Druckverfahren ist achtmal schneller als herkömmliche Methoden. Das Fraunhofer LBF hat zudem ein spezielles Verfahren entwickelt, um die Fasern zu hydrophobieren und ihre Temperaturbeständigkeit zu erhöhen. Die Fasern werden durch Acetylierung modifiziert und mit Epoxidharz beschichtet.
Naturfasern in neuen Dimensionen
Durch die Beschichtung mit Epoxidharz wird eine Temperaturbeständigkeit der Fasern erreicht, die eine Integration in Polyamide ermöglicht. Dies war bisher nicht möglich. Die ökologischen Vorteile des Verfahrens sind beachtlich: Bei einem Hochgeschwindigkeitszug mit vierzehn Übergängen und einer Laufleistung von 12,5 Millionen Kilometern können pro nachhaltigem Übergangssystem 160 Kilogramm eingespart werden. Das entspricht einer CO2-Einsparung von fast 115 Tonnen für den gesamten Zug.
Ein Beitrag von: