Smarte Robotergreifer verbrauchen bis zu 90 % weniger Energie
Die Robotergreifer der Universität des Saarlandes sparen bis zu 90 % Energie. Auf der Hannover Messe wird gezeigt, wie Formgedächtnislegierungen dabei helfen.
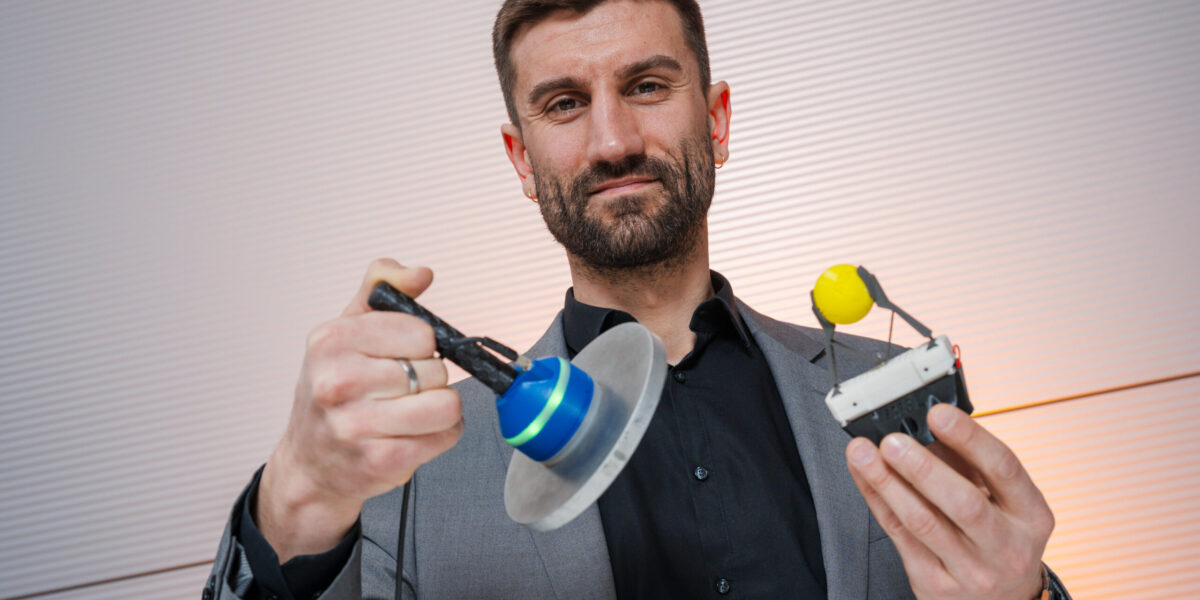
Professor Paul Motzki (Foto) und sein Team zeigen auf der Hannover Messe Prototypen von Robotergreifsystemen, die Werkstücke energielos festhalten und handhaben können, darunter Vakuumgreifer (links, dieser hält eine Stahlplatte) und Zangengreifer (r.).
Foto: Oliver Dietze / Universität des Saarlandes
Energieeffizienz ist ein entscheidender Faktor in der modernen Industrie. Smarte Robotergreifer, die auf Formgedächtnismaterialien basieren, könnten den Stromverbrauch in der Produktion drastisch senken. Ein Forschungsteam der Universität des Saarlandes zeigt auf der Hannover Messe, wie diese Technologie funktioniert. Dank intelligenter Steuerung und sensorloser Erfassung benötigen die Greifer nur minimale Energieimpulse, um Werkstücke sicher zu halten und flexibel zu bewegen.
Inhaltsverzeichnis
Mit Formgedächtnislegierungen zu mehr Energieeffizienz
In modernen Produktionshallen erledigen Roboterarme eine Vielzahl an Aufgaben: Sie greifen, halten, transportieren und montieren Bauteile. Doch viele dieser Systeme verbrauchen kontinuierlich Energie, insbesondere wenn sie mit pneumatischen Greifmechanismen arbeiten. Druckluftsysteme sind nicht nur laut, sondern auch schwer und verschleißanfällig. Zudem lassen sie sich nur schwer anpassen und sind oft nicht für eine enge Zusammenarbeit mit Menschen ausgelegt.
Forschende der Universität des Saarlandes und des Saarbrücker Zentrums für Mechatronik und Automatisierungstechnik (ZeMA) haben eine Alternative entwickelt. Ihre Greifsysteme basieren auf Formgedächtnismaterialien und bieten eine energieeffiziente, flexible und kompakte Lösung für industrielle Anwendungen.
Wie funktioniert die neue Technologie?
Die neuartigen Greifer nutzen feine Drähte aus der Formgedächtnislegierung Nickel-Titan. Dieses Material besitzt die besondere Eigenschaft, seine Form bei Temperaturänderung zu ändern. Ein kurzer Stromimpuls erwärmt die Drähte, wodurch sie sich zusammenziehen. Schaltet man den Strom ab, kühlen sie ab und kehren in ihre Ausgangsform zurück. Dadurch lassen sich präzise Bewegungen steuern.
Paul Motzki, Professor für smarte Materialsysteme an der Universität des Saarlandes, erklärt: „Unsere Methode kann den Energieverbrauch erheblich senken und gleichzeitig die Flexibilität in der Produktion steigern.“
Hohe Kraft bei minimalem Energieeinsatz
Nickel-Titan hat die höchste bekannte Energiedichte unter den Antriebsmechanismen. Bereits ein 500 Mikrometer dicker Draht kann eine Kraft von über 100 Newton aufbringen. Durch das Bündeln mehrerer feiner Drähte erhöht sich die Effizienz weiter. Diese feinen Drähte kühlen schneller ab, wodurch hohe Frequenzen und schnelle Bewegungen erreicht werden.
Die Forscher haben eine Technik entwickelt, mit der sie 20 Drähte von jeweils 25 Mikrometern Durchmesser kombinieren. Dadurch entsteht eine Zugkraft von fünf Newton, die mit einer Frequenz von 200 Hertz angesteuert werden kann. Das System lässt sich flexibel an verschiedene Anforderungen anpassen, sei es für hohe Kraft oder hohe Geschwindigkeit.
Intelligente Widerstandsmessung
Ein besonderes Merkmal der neuen Greifsysteme ist ihre sensorlose Steuerung. Normalerweise benötigen Industrieroboter zahlreiche externe Sensoren, um Bewegungen zu erfassen und zu korrigieren. Hier hingegen erfolgt die Messung direkt im Draht. Die Forschenden nutzen den elektrischen Widerstand der Drähte als Informationsquelle.
„Die Drähte liefern selbst alle nötigen Daten. Ein Halbleiterchip wertet die Widerstandsänderungen aus und ermittelt die genaue Position des Greifers“, erklärt Motzki. Künstliche Intelligenz ordnet jedem Messwert eine bestimmte Verformung der Drähte zu. So können Bewegungen präzise gesteuert und schnell angepasst werden.
Praktische Anwendungen auf der Hannover Messe
Auf der Hannover Messe präsentieren die Forschenden verschiedene Prototypen ihrer Greifsysteme. Einer davon ist ein Zangengreifer, der Werkstücke sicher greifen und halten kann. Der Prototyp erreicht eine Greifkraft von vier Newton, lässt sich aber je nach Anwendung skalieren. Die Technologie kann sowohl für winzige als auch für große Greifsysteme eingesetzt werden.
Ein weiteres Beispiel ist der Vakuumgreifer. Hier kombinieren die Ingenieurinnen und Ingenieure bewegliche Greiferfinger mit Vakuumsaugern an den Fingerspitzen. Durch einen kurzen Stromimpuls wird ein tragfähiges Vakuum erzeugt, das ein Werkstück sicher festhält. Sobald der Strom abgeschaltet wird, bleibt das Vakuum erhalten. Erst ein weiterer Impuls löst es wieder auf. Diese Methode spart erheblich Energie, da während des Haltens kein Strom verbraucht wird.
Potenzial für die Zukunft
Die Technologie könnte zahlreiche industrielle Anwendungen revolutionieren. Durch die kompakte Bauweise sind kleinere und leichtere Greifsysteme möglich. Zudem lassen sich Produktionsprozesse effizienter gestalten, da die Greifer flexibel an neue Aufgaben angepasst werden können.
Die Forschenden der Universität des Saarlandes suchen auf der Hannover Messe nach Industriepartnern, um ihre Technologie weiterzuentwickeln und in die Praxis zu überführen. Ihr langfristiges Ziel ist es, energieeffiziente, kostengünstige und anpassungsfähige Greifsysteme für verschiedenste Produktionsumgebungen bereitzustellen.
Die Universität des Saarlands auf der Hannover Messe: Halle 2, Saarland-Stand B10
Ein Beitrag von: