Überblick in komplexen Anlagenstrukturen behalten
Demonstratoren zeigen am Beispiel des Digitalisierten Asset Managements den Mehrwert von Antrieb 4.0 für Anwender und Hersteller.
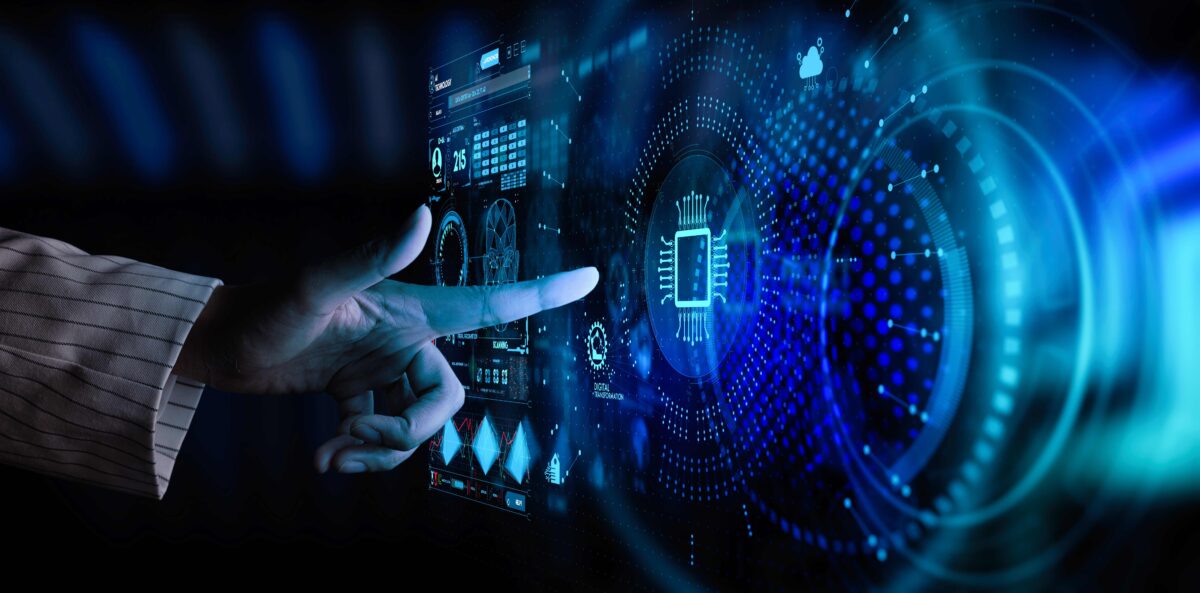
Auf der Hannover Messe veranschaulicht das Forschungsprojekt eine herstellerübergreifende und einheitliche Datenbereitstellung im Datenraum Antrieb 4.0.
Foto: PantherMedia/happysuthida
Effizienz ist der Erfolgsfaktor für Automatisierung – insbesondere in der industriellen Produktion. Doch mit der steigenden Anzahl an Maschinen, Komponenten und Merkmalen in den Anlagen wird es, so die Forschungsvereinigung Elektrotechnik beim ZVEI e. V. (FE), zunehmend schwieriger, den Überblick zu behalten. Wie die dringend benötigte Transparenz in der Fabrikhalle hergestellt werden kann, will das Forschungsprojekt Antrieb 4.0 auf der Hannover Messe zeigen.
Am Beispiel des Use Case „Digitalisiertes Asset Management“ präsentiert das Forschungsprojekt nach eigenen Angaben am Stand des ZVEI, wie Betreiber, Antriebshersteller oder Maschinen- und Anlagenbauer zu jeder Zeit den Überblick über eine komplexe Anlagenstruktur behalten können. „Dank des multilateralen Datenteilens wird es nun möglich, alle wichtigen Informationen eines Assets über seinen gesamten Lebenszyklus hinweg an einer zentralen Stelle und in einem standardisierten Format im Datenraum 4.0 bereitzustellen“, erklärt Konsortialleiter Dr. Falk Eckert von der Forschungsvereinigung Elektrotechnik beim ZVEI e. V. Mehrere Demonstratoren, die herstellerübergreifend miteinander kommunizieren können, veranschaulichen, wie die Industrie von mehr Effizienz, Zeit- und Kosteneinsparungen profitieren kann.
Komplexe Anlagen transparent visualisieren
Produktionsanlagen sind komplexe Systeme, die sich aus einer Vielzahl von Einzelantrieben und anderen Baugruppen zusammensetzen. Entsprechend umfassend fällt dabei die Anlagendokumentation aus. Während des laufenden Betriebs fällt eine Reihe an Informationen an, die heutzutage in herstellerspezifischen Systemen und unterschiedlichen Formaten bereitgestellt werden. Dies führt zu Informationsasymmetrien bei Entscheidungsfindern und hat unter anderem zur Folge, dass Unternehmen den Betrieb und den Energieverbrauch einer Anlage nicht zielgerichtet optimieren können.
Mithilfe des Digitalisierten Asset Managements hat der Maschinenbetreiber den Aufbau seiner Anlage transparent visualisiert und einen zentralen standardisierten Zugriff auf alle relevanten Informationen. Aufgrund der übersichtlichen Überwachung des Zustands und des Energieverbrauchs können Stillstandzeiten reduziert, der Betrieb optimiert und Kosten eingespart werden. Für den Antriebshersteller oder den Maschinen- und Anlagenbauer ergibt sich, wie es weiter heißt, der große Vorteil, spezifisch auf die Anforderungen seiner Kunden eingehen zu können. Während der Antriebshersteller qualitativ hochwertige sowie energiesparsame Komponenten zu marktgerechten Preisen anbieten möchte, baut der Maschinen- und Anlagenbauer entsprechende Anlagen nach den Bedürfnissen des Auftraggebers.
Die Entwicklung erfolgt derzeit auf Basis von Erfahrungswerten, aufwendigen Simulationen, langfristigen und kostenintensiven Tests und Prototypenentwicklungen. Komponenten werden dabei häufig überdimensioniert. An dieser Stelle können belastbare Daten aus dem laufenden Betrieb Abhilfe schaffen. Über den Datenraum Antrieb 4.0 können exemplarisch Metadaten abgerufen, nach Komponenten oder Maschinen und Anlagen gefiltert und der Zugriff auf Betriebs- oder Energiedaten beim Betreiber angefragt werden.
Das Digitalisierte Asset Management hilft also dabei, Komponenten hinsichtlich ihrer Qualität und Energieeffizienz weiter zu optimieren, Simulationen zu verbessern und Komponenten optimal zu dimensionieren. Gleichzeitig werden im Entwicklungsprozess Zeit, Kosten und Ressourcen reduziert, heißt es weiter.
Antriebe unterschiedlicher Hersteller an verschiedenen Standorten vernetzen
Antrieb 4.0 zeigt die Möglichkeiten der horizontalen Vernetzung zwischen Antrieben unterschiedlicher Hersteller an verschiedenen Standorten und Produktionsanlagen sowie der vertikalen Vernetzung vom Antrieb in den Datenraum auf. Voraussetzung dafür ist eine herstellerunabhängige und einheitliche Datenbereitstellung. Viele Unternehmen nutzen bereits intern standardisierte Vorgehensweisen, die aber mangels einheitlicher Semantik nicht interoperabel sind. Dort setzt Antrieb 4.0 an und möchte durch Einbindung vieler Hersteller einen Standard setzen, um die nahtlose Übertragung von Daten und Informationen herstellerübergreifend zu ermöglichen.
Antrieb 4.0-Systemarchitektur als Modell für die Zukunft
Wie das in Zukunft aussehen könnte, zeigt die Antrieb 4.0-Systemarchitektur, führt die Forschungsvereinigung aus. Sie ermögliche eine vertikale Vernetzung vom Feld über die Edge in die Cloud mit Zugriffsberechtigungen für beteiligte Akteure wie den Betreiber, den Antriebshersteller oder den Maschinen- und Anlagenbauer. Mit einer entsprechenden Authentifizierung können den verschiedenen Nutzergruppen über den Datenraum und Verwaltungsschalen (Asset Administration Shells, AAS) benötigte Daten auch horizontal für eine definierte Nutzungsart und Dauer zur Verfügung gestellt werden. Durch den einfachen Zugriff auf die in einer Anlage verbauten Antriebe und Komponenten könne in Zukunft im laufenden Betrieb die Transparenz in der Fabrikhalle hergestellt werden.
ZVEI auf der Hannover Messe 2025: Halle 11, Stand B54
Quelle: Forschungsvereinigung Elektrotechnik beim ZVEI e. V. (FE)
Ein Beitrag von: