Wie arbeiten Mensch und Roboter sicher nebeneinander?
Mit der Freilassung der Roboter wächst die Bedeutung der Arbeitssicherheit in den Fertigungshallen. Die kollaborierenden Maschinen arbeiten längst Seite an Seite mit ihren menschlichen Kollegen. Mensch-Roboter-Kollaboration verspricht große Vorteile für Unternehmen wie Arbeiter. Aber sie birgt auch gewaltige Herausforderungen…
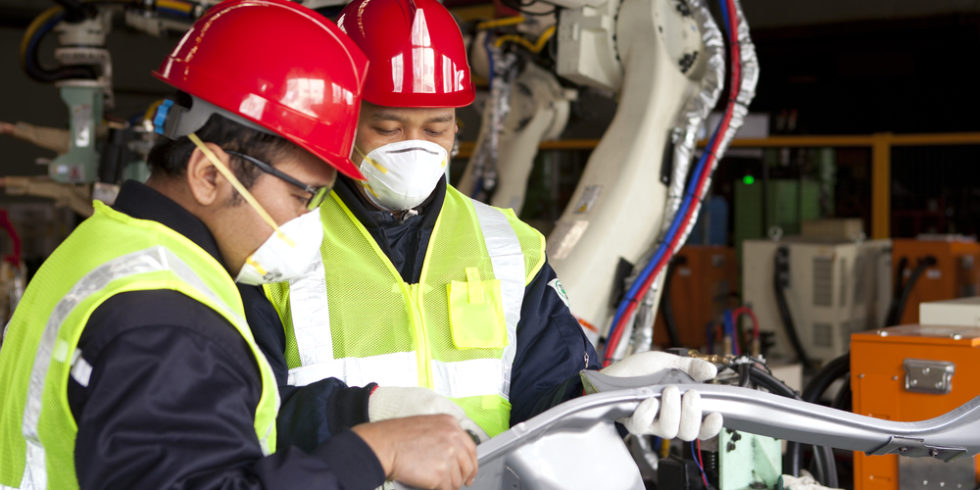
Foto: panthermedia.net/ndoeljindoel
Was ist Mensch-Roboter-Kollaboration?
Früher war es vergleichsweise einfach: Setzte ein Betrieb in der Fertigung einen autonomen Roboter ein, baute er zuvor einen Käfig um ihn herum. Der Mensch durfte nur hinein, wenn er zuvor einen Notausschalter betätigte. So war er vor Verletzungen geschützt. „Mit der Mensch-Maschine-Kollaboration ist der Arbeitsschutz komplizierter geworden“, sagt Andreas Kaulen vom TÜV Rheinland. Heute arbeiten Roboter und Menschen Seite an Seite und teilen sich den Raum, in dem sie ihre Tätigkeit verrichten. Montiert auf mobilen Plattformen, unterstützen vernetzte Maschinen Facharbeiter bei der Produktion, arbeiten ihnen zu, helfen beim Tragen schwerer Lasten. Sie heben schwere Werkstücke an und bringen sie in eine vorgegebene Position, während ein menschlicher Arbeiter leichte Eisenhaken anschweißt. Diese enge Zusammenarbeit und Automatisierung sind auch deshalb nötig, um dem Wunsch des Verbrauchers nach immer stärker individualisierten Gütern gerecht zu werden.
Die trennende Schutzvorrichtung fällt bei der Mensch-Roboter-Kollaboration (MRK) weg. Damit unterscheidet sich die MRK auch von der Arbeitsform, die man als Koexistenz zwischen Mensch und Maschine bezeichnet und bei der zwar der Schutzzaun entfällt, beide aber in unterschiedlichen Bereichen arbeiten und nicht zusammen. Bei einer Kooperation wiederum arbeiten Mensch und Industrieroboter in einem Arbeitsraum am gleichen Bauteil, aber nicht gemeinsam, sondern zeitversetzt. Man bezeichnet kollaborierende Roboter auch als Cobots.
Sicherheit bei der Mensch-Roboter-Kollaboration
Bei der Mensch-Roboter-Kollaboration kommt es mitunter zum direkten Kontakt zwischen menschlichem und maschinellem Mitarbeiter. Immer gilt dabei der Grundsatz: Der Mensch darf nicht verletzt werden. „Daraus ergeben sich zwei Fragestellungen“, so Andreas Kaulen vom TÜV Rheinland. Die erste beschäftigt sich dem Experten für Arbeitssicherheit zufolge damit, wie der Roboter den Menschen wahrnehmen soll. Welche Sensoren sind geeignet? Besitzt der Roboter selbst Sensoren oder wird die ganze Umgebung von außen abgetastet? „Und wenn der Roboter den Menschen erkannt hat, wie verhält er sich dann?“, fährt Kaulen fort. Denkbar sei, dass die Maschine stehen bleibt. Das bedeutete den größtmöglichen Schutz für den Menschen – wäre aber schlecht für die Produktivität.
Wissenschaftler vom Fraunhofer IWU haben daher einen Geschwindigkeitsregler sowie ein multimodales, umfassendes Wahrnehmungssystem entwickelt. Damit müssen die Roboterbewegungen zwar auch weiterhin verlangsamt werden, sobald sich ein Mensch nähert, aber deutlich weniger als zuvor. Roboterbewegungen, die bei menschlicher Annäherung um 25 Prozent schneller sind als vorher, machen den Einsatz eines Cobots sehr viel effizienter.
Speziell Cobots mit hoher Traglast sind ein potenzielles Sicherheitsrisiko. Fällt ein Endwerkzeug des Roboters herunter, zum Beispiel bei einem Stromausfall, besteht erhebliche Verletzungs- oder gar Lebensgefahr. Moderne Cobots verfügen daher über einen elektromagnetischen Bremsenschutzmechanismus, der bei einem Stromausfall automatisch aktiviert wird, um zu verhindern, dass Werkzeuge unkontrolliert herunterfallen. In diesem Szenario ist es außerdem wichtig, dass beim An- und Ausschalten des Roboters keine Verschiebungen auftreten.
Für Personen, die Hand in Hand mit einer Maschine arbeiten, ist es wichtig, die Roboterbewegungen vorhersehen und sich darauf einstellen zu können, um Verletzungen zu verhindern. Permanent wachsam und aufmerksam müssen sie sein, was nicht nur körperlich ermüdend ist, sondern auch psychisch. In die Kategorie der psychischen Belastungen, die aus der engen Zusammenarbeit mit Industrierobotern entstehen können, gehört auch das Gefühl der sozialen Isolation — ein netter Plausch mit Kollege Roboter am Arbeitsplatz ist schlicht nicht möglich.
Sicherheitsspezifikationen für kollaborierende Roboter
Die Sicherheitsanforderungen an kollaborierende Roboter sind entsprechend hoch, um jegliches Verletzungsrisiko bis auf ein Minimum zu senken. Definiert werden die sicherheitstechnischen Anforderungen durch die überarbeitete Norm EN ISO 10218, Teile 1 und 2, sowie die Spezifikation ISO/TS 15066.
Herausforderungen der Mensch-Roboter-Kollaboration
Gegenüber konventionellen Industrierobotern haben Cobots den Vorteil, dass sie oftmals leichter zu installieren und flexibler in den Anwendung sind. Allerdings können sie in punkto Traglast und Armlänge nicht mithalten. Zudem ist der Planungs- und Implementierungsaufwand von Mensch-Maschine-Kollaborationen sehr hoch; die Prozesse müssen von Experten manuell durchgeführt werden.
Ohne den Faktor Mensch geht es nicht — weder in der Planungsphase noch im Betrieb. In der industriellen Fertigung werden menschliche Arbeiter weiterhin benötigt, um Fehler der Maschinen zu beheben. So kommt es beispielsweise im Betrieb manchmal zu Problemen mit einer komplexen Kabelführung, die die Bewegungen des kollaborierenden Roboters beeinträchtigt.
Vorteile der Mensch-Maschine-Kollaboration
Vorrangige Ziele der Mensch-Maschine-Kollaboration sind Prozessoptimierung und Kosteneinsparung. Wenn sich Arbeiter und Roboter frei bewegen und ergänzen, arbeiten sie schneller und produktiver, so das Credo. Die Effizienz in der Produktion wird dadurch gesteigert, die Kosten werden reduziert. Vor allem sind kollaborative Roboter in der Lage, die Flexibilität von Montageprozessen zu erhöhen, bei denen kleine Losgrößen in kurzen Zyklen hergestellt werden müssen.
„In vielen industriellen Bereichen ist in den letzten zehn Jahren ein klarer Trend von der Massenproduktion hin zur ‚Massenspezialanfertigung‘ zu beobachten“, so Jan Schmitt und Tobias Kaupp von der Hochschule Würzburg-Schweinfurt, die die Mensch-Roboter-Kollaboration in der Montage komplexer Bauteile erforschen. Die Variantenvielfalt von Industrieprodukten steige, ihr Lebenszyklus dagegen sinke. „Mensch-Roboter-Kollaboration trägt dazu bei, Prozesse deutlich effizienter zu gestalten, Fehler zu minimieren und die Arbeitsbedingungen für Mitarbeitende zu verbessern“, meint Kaupp. So können etwa kollaborative Schwerlastroboter den Werkern bei der Handhabung von schweren Geräten und Gegenständen enorm helfen, ihren Rücken und ihre Gesundheit schonen — leistungsstarke Sensorik und Steuerungstechnik machen es möglich.
Industrieroboter und Cobots sind auch beliebte Gegenmittel für die demographische Alterung der Gesellschaft und den damit zusammenhängenden Fachkräftemangel. Zwar werden weiterhin Menschen benötigt, um die Roboter zu installieren, betreiben und reparieren, aber repetitive, gefährliche oder schwere Aufgaben können die Cobots übernehmen und menschliche Arbeitskraft dadurch erleichtern oder ersetzen. Dies ist in Deutschland genauso zu beobachten wie in Japan oder Südkorea, zwei alternden asiatischen Industriegesellschaften, deren Industrien schon heute eine enorm hohe Roboterdichte aufweisen.
Auf diese Weise können Cobots außerdem den Trend zum Reshoring beschleunigen. Reshoring ist das Gegenteil von Offshoring, also die Rückverlagerung von Produktionsprozessen und Arbeitsplätzen aus Billiglohnländern ins hochpreisige Deutschland und Europa. Durchaus denkbar ist beispielsweise, dass Teile der Textilindustrie unter freundlicher Mithilfe spezialisierter Cobots wieder in Europa ansässig werden.
Praxisbeispiele für die Mensch-Roboter-Kollaboration
Eine typische Anwendung von Cobots ist das Beladen und Entladen von CNC-Maschinen. Kollaborative Roboter können Artikel palettieren oder kleine Teile in geringer Stückzahl schweißen. Hier sind 4 weitere konkrete Praxisbeispiele aus der Welt der Mensch-Roboter-Kollaboration:
- Einen Roboter-Greifer mit Feingefühl hat das Fraunhofer IEM entwickelt und auf der Hannover Messe 2023 vorgestellt. Der Greifer kann empfindliche Lebensmittel wie Schaumküsse, Eier, Fleischbällchen oder Kekse so sanft transportieren, sortieren und verpacken, dass keine Druckstellen oder andere Makel entstehen. Und er ist wegen seiner sensorbasierten Umfelderkennung für die Mensch-Roboter-Kollaboration geeignet. »Die Finger mit kunststoffbasierter, nachgiebiger, flexibler Oberfläche greifen empfindliche Materialien sensitiv, sodass Beschädigungen vermieden werden. Gleichzeitig agiert der Roboter-Greifer hochdynamisch und passt sich dadurch problemlos an Produktionsabläufe an. Die erforderliche Balance zwischen Schnelligkeit und Feingefühl ist jederzeit gewahrt«, sagt Christian Henke, Abteilungsleiter Scientific Automation am Fraunhofer IEM. »Durch dieses Multisensorsystem, bestehend aus Abstands- und Thermografiesensoren, wird die komplette Anordnung aus Cobot und Achsen kollaborativ. Auf Schutzzäune können Unternehmen somit verzichten«, so Henke.
- An die Kunststoffindustrie verkauft der Augsburger Roboterhersteller Kuka einen Cobot namens „LBR iisy“. Dieser prüft für einen Kunden DataMatrix-Codes auf Qualität und Vollständigkeit, arbeitet Hand in Hand mit Vorarbeitern der Laserabteilung zusammen. Die Vorarbeiter legen Kunststoffteile mit den Codes unter die Kameras des Cobots. Dieser prüft die Qualität der Codes und zeigt an, ob und welches Kunststoffteil fehlerhaft ist. Der Vorarbeiter tauscht das fehlerhafte Teil per Hand aus und lässt daraufhin den Cobot seine Arbeit wieder aufnehmen. Zuvor hatten die Vorarbeiter jedes Teil manuell scannen müssen — ein aufwändiger Arbeitsprozess, der durch den kollaborativen Roboter enorm verschlankt wurde.
- Das Schweizer Unternehmen ABB vertreibt den Cobot „YuMi“, der in der Kleinteilmontage in der Elektronikindustrie sowie für Montageaufgaben bei der Herstellung von Uhren, Spielzeug und Automobilkomponenten eingesetzt wird. YuMi hat zwei Arme, flexible Hände, eine kamerabasierte Teileerkennung und Teilezuführungssystem. Sobald der Cobot einen unerwarteten Kontakt registriert, zum Beispiel bei einer Kollision mit einem menschlichen Kollegen, stoppt er seine Bewegung binnen Millisekunden. Per Knopfdruck nimmt er seine Bewegung wieder auf.
- Cobots des dänischen Herstellers Universal Robots hat Siemens im Einsatz. Im Gerätewerk Erlangen wurde bereits im Jahr 2017 der erste Cobot in Betrieb genommen. Seine Aufgabe war es, Kartonagen von einem Anlieferstapel auf eine Palette umzuschichten. Heute sind nach Angaben von Universal Robots mehr als 70 Cobots im Erlanger Siemens-Werk im Einsatz. Die Mensch-Maschine-Kollaboration funktioniert offenbar so gut, dass die Menschen ihren Kollegen eigenen Namen gegeben haben. Der Cobot „Schorsch“ arbeitet mit Gehäusen, „Waltraud“ und „Mariechen“ verpacken Geräte.
Ein Beitrag von: