Lean Manufacturing – Verschwendung vermeiden
Lean Manufacturing wurde ursprünglich durch den japanischen Autohersteller Toyota entwickelt. Es bezeichnet die Verschlankung der Produktion, was jedoch nicht mit Personalabbau verwechselt werden darf.
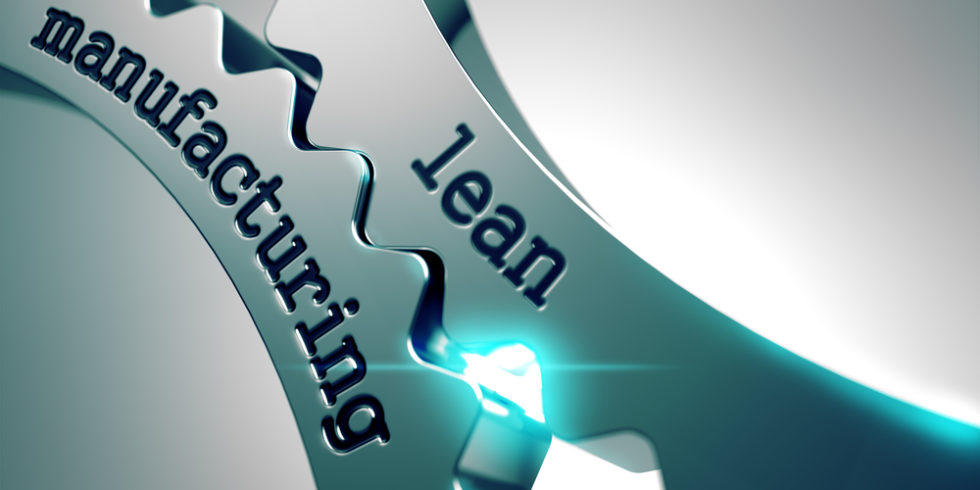
Foto: panthermedia.net / tashatuvango
Inhalte dieses Artikels:
- Definition von Lean Manufacturing
- Lean Management
- Lean Thinking
- Lean Enterprise
- Ziele von Lean Manufacturing
- Die Methoden von Lean Manufacturing
- Die Grundprinzipien wie Pull, Takt und Perfektion
- Was Lean Manufacturing für die Produktion bedeutet
Die Definition von Lean Manufacturing
Lean Manufacturing, auch Lean Production genannt, bezeichnet eine bestimmte Form der Produktionsorganisation. Entstanden ist Lean Manufacturing in den Betrieben des japanischen Automobilherstellers Toyota. Im Deutschen wird der Begriff mit „schlanke Produktion“ übersetzt, eine alternative gebräuchliche Bezeichnung ist „ganzheitliche Produktionssysteme“. Erstmals benutzt wurde der Begriff „Lean Manufacturing“ in der MIT-Studie „The Machine that Changed the World“ von James P. Womack, Daniel T. Jones und Daniel Roos, die in den Jahren 1985 bis 1991 durchgeführt wurde. Sie entdeckten die Methode in Japan. Im Kern basiert Lean Manufacturing oder Lean Production auf Dezentralisierung und Teamwork.
In den vergangenen Jahren und Jahrzehnten wurden die Begriffe des Lean Manufacturing und der Lean Production sukzessive erweitert. Zusätzlich Sparten entstanden:
- das Lean Management
- das Lean Thinking
- die Lean Enterprise
Oftmals werden diese Bezeichnungen gleichbedeutend zum Lean Manufacturing verwendet. Das ist aber nicht richtig.
Lean Management bezieht sich beispielsweise auf die administrativen Bereiche eines Unternehmens – im Gegenteil zu den produzierenden Abteilungen. Es geht dabei um die Art und Weise, wie ein Betrieb von oben gesteuert wird. Als ideal gelten eine schlanke Unternehmensführung und flache Hierarchien.
Lean Thinking hingegen bezeichnet keine eigene Form unter den Lean-Methoden, sondern den grundsätzlichen Charakter dieses Konzepts. Es geht darum, das Denken und Handeln der Mitarbeiter dahingehend zu verändern, dass sie eigenständig Verschwendung erkennen und vermeiden.
Lean Enterprise hingegen beschreibt das erreichte Ziel: ein Unternehmen, das die Lean-Methoden vollständig anwendet und sich selbst quasi perfektioniert hat. Es wird über Lean Management geführt, arbeitet mit Lean Manufacturing und die Mitarbeiter wenden das Lean Thinking im Arbeitsalltag konsequent an.
Ziele von Lean Manufacturing
Ziele von Lean Manufacturing sind eine Verbesserung der Produktivität, der Produktionsfaktoren, der Produktqualität und der Produktionsflexibilität. Im Idealfall wird Verschwendung jeder Art vermieden: von Zeit, Arbeitskraft, Geld, Material und Raum. Daraus resultieren schnellere und flexiblere Prozesse. So ist es dem Unternehmen möglich, seinen Kunden zu den geringstmöglichen Kosten das zu bieten, was diese haben wollen – bei gleichzeitig bester Qualität und zum gewünschten Zeitpunkt.
In Deutschland führte die Übersetzung „schlanke Produktion“ zunächst zu Missverständnissen. Schlanke Produktion wurde von einigen als eine Produktion mit weniger Mitarbeitern verstanden, Kritiker befürchteten einen starken Personalabbau. Tatsächlich ist das Ziel des Lean Manufacturing aber genau das Gegenteil: Ein Unternehmen soll so erfolgreich werden, dass es expandieren und neue Arbeitsplätze schaffen kann. Was nicht bedeutet, dass es in Ausnahmefällen nicht doch notwendig sein kann, kurzfristig Personal abzubauen, um das Unternehmen zunächst wieder wettbewerbsfähig zu machen.
Die Methoden des Lean Manufacturing
Die Methoden des Lean Manufacturing haben zwar ihren Ursprung in der japanischen Automobilproduktion, gelten aber inzwischen aufgrund des großen Erfolgs in verschiedenen Branchen weltweit als Industriestandard. Kaum ein Unternehmen kann es sich heutzutage leisten, auf Lean Manufacturing zu verzichten. Das Lean Manufacturing ist, auch wenn der Begriff das vermuten lässt, nicht auf die Produktion begrenzt. Das Prinzip ist ein Regelwerk, das für alle Prozesse eines Unternehmens gilt:
- Kernprozesse
- Führungsprozesse
- Unterstützungsprozesse
Je nach Wirtschaftszweig können die Methoden variieren, für produzierende Unternehmen gleichen sie sich jedoch stark. Hauptziel des Lean Manufacturing ist die Vermeidung von Verschwendung, die über verschiedene Wege erreicht wird. Das gewünschte Ergebnis sieht vor, alle sogenannten nicht-wertschöpfenden Tätigkeiten in der Produktion auszuschalten. Hingegen sollen wertschöpfende Aktivitäten gefördert werden. Das sind alle Tätigkeiten, die letztendlich den Wert des Produktes für den Kunden erhöhen (Qualitätskontrolle und -optimierung, möglichst Fehlervermeidung oder sofortige Fehlerbehebung). Alles andere gilt als Verschwendung.
Es kann jedoch sein, dass es nicht-wertschöpfende Tätigkeiten gibt, die außerhalb der direkten Produktion liegen und dennoch notwendig für die Entstehung eines Produktes sind – seien es Forschung und Entwicklung oder Produktionsplanung.
Zu den Grundprinzipien von Lean Manufacturing gehören unter anderem die Folgenden:
Mitarbeiterführung
Die Führung der Mitarbeiter muss an die Ansprüche des Lean Manufacturing angepasst werden. So müssen Mitarbeiter lernen, eigenständig Verschwendung zu erkennen und die Prinzipien und Methoden des Lean Manufacturing anzuwenden. Denn auch die Mitarbeiter sind nach den Ansprüchen der Lean Production vor allem Ressourcen, die effizient eingesetzt werden sollen. Es muss daher eine Arbeitsweise von Führungskräften und Mitarbeitern sichergestellt sein, die frei von Verschwendung ist. Nur so lassen sich die gewünschten Ergebnisse erzielen. Gibt es eindeutige Vorgaben und Zielstrukturen im täglichen Zusammenspiel zwischen Führungskraft und Mitarbeiter profitieren davon alle Beteiligten.
Perfektion/Verbesserung
Ein kontinuierlicher Verbesserungsprozess gehört ebenso zu den Methoden des Lean Manufacturing. Das Streben nach Perfektion ist eines der Grundziele. Um dies zu erreichen, sollten sämtliche Mitarbeiter in den Verbesserungsprozess eingebunden sein. Nur wenn alle Angestellte eines Unternehmens zu jeder Zeit Prozesse und Methoden hinterfragen, um diese zu verbessern, können dauerhaft Fehler und Verschwendung entdeckt und vermieden werden. Die Einbindung aller Mitarbeiter kann auf verschiedene Weise erfolgen, beispielsweise über ein betriebsinternes Ideenmanagement. Zu dieser Methode gehört im weitesten Sinne auch das Null-Fehler-Prinzip. Es sieht vor, dass einmal entdeckte Fehler gar nicht erst an nachfolgende Produktionsschritte weitergegeben werden, um so die Produkt- und Prozessqualität zu erhöhen.
Pull
Nach dem Pull-Prinzip wird der Kundenauftrag durch den Produktionsprozess gezogen (engl. to pull = ziehen). Es zielt darauf ab, den Steuerungsaufwand und die Bestände zu minimieren. Bei Störungen bedeutet es beispielsweise, dass ein System so lange angehalten wird, bis die Ursache des Fehlers gefunden und behoben ist. Das sorgt zwar für eine verzögerte Produktion, verhindert aber gleichzeitig die Produktion von Ausschuss oder den Aufbau von Bestand. Bestand wiederum würde die Durchlaufzeit verlängern, den Takt stören und den Prozess nur schwierig steuerbar machen. In Japan wird dieses Prinzip „Jidoka“ genannt, die „Kultur des Anhaltens“.
Ressourceneinsatz
Die bessere Nutzung von Ressourcen verhindert Verschwendung. Werden Ressourcen effektiv eingesetzt, können Prozesse effizienter ablaufen. Es werden insgesamt weniger Ressourcen benötigt. Das führt parallel zur Steigerung der Wettbewerbsfähigkeit und auch zu besseren Umweltbilanzen. Davon profitiert ein Unternehmen mehrfach: Der Unternehmenserfolg erhöht sich ebenso wie die soziale Außenwirkung des Betriebs aufgrund der guten Umweltbilanzen. Das wiederum fördert gesellschaftliche Akzeptanz und Image.
Standard
Beim Lean Manufacturing ist die Standardisierung einzelner Prozesse wichtig, um die Prozessstabilität zu verbessern. Standardisierung bedeutet im Falle der Produktion die Festlegung von Handlungsschritten für Arbeitsabläufe, Planungsaufgaben, sich wiederholende Prozesse und Fertigungsschritte. Mithilfe der Standardisierung können nicht-wertschöpfende Arbeitsschritte aufgedeckt und ausgeschlossen werden.
Takt
Die richtige Taktung, auch Fließprinzip genannt, gehört ebenfalls zu den Optimierungsmethoden. In der Praxis erfolgt in diesem Zuge eine Produktionssegmentierung und darauf basierend eine Ressourcentrennung. Jede Produktgruppe nutzt eigene Ressourcen, um so ein eigenes, in sich geschlossenes System mit kurzen Durchlaufzeiten zu erreichen. Jedes Produkt wird ohne Unterbrechung fertig bearbeitet und hat für sich die kürzest mögliche Durchlaufzeit, bevor es ohne Zwischenlagerung zum nächsten Prozessschritt transportiert wird.
Visualisierung
Eine bildliche Darstellung von Prozessen und Arbeitsabläufen ist das Hauptziel des visuellen Managements. So soll mehr Transparenz über Ziele und Prozesse innerhalb des Lean Manufacturing erreicht werden. Über eine bildliche Darstellung ist es allen Mitarbeitern und Führungskräften jederzeit möglich, schnell Informationen über produktionsrelevante Prozesse zu erhalten. Auch durch die Visualisierung profitiert ein Unternehmen in mehrfacher Hinsicht: zum einen durch die gewünschte Verschlankung der Prozesse, zum anderen von einer stärkeren Identifikation der Mitarbeiter mit dem Unternehmen, die durch die Einbindung der Angestellten erreicht wird. Außerdem sorgt die bildliche Darstellung der Prozesse dafür, dass Abweichungen schnell erkannt werden und zeitnah Abhilfe geschaffen werden kann.
Was Lean Manufacturing für die Produktion bedeutet
Für den Produktionsprozess bedeutet Lean Manufacturing oder Lean Production, dass Bestände besser überwacht und gezielt eingesetzt werden können. Auch Personal- und Maschinenkapazitäten können früher und genauer geplant werden. Manuelle Arbeiten lassen sich mithilfe von Assistenzsystemen optimieren, zum Beispiel die manuelle Kommissionierung mittels Unterstützung von Datenbrille und Headset. Die größte Herausforderung liegt für die Unternehmen darin, die nach dem Taylorismus übliche Trennung von geistiger und körperlicher Arbeit zu beenden. Sie müssen allen operativ tätigen Angestellten zutrauen, dass sie unter den idealen Bedingungen – und gerade dann – ihre Aufgaben gut erfüllen, auch bei Selbstorganisation.
Für die Mitarbeiter eines Unternehmens kann Lean Manufacturing sowohl Vor- als auch Nachteile haben. Je nach Prozess werden Arbeitsschritte gestückelt und dadurch die Taktung erhöht. Für die Mitarbeiter bedeutet das, dass sie einen einzelnen Prozessschritt immer wieder und in kürzerer Zeit machen müssen. Das kann zu fehlender Abwechslung und höherer Belastung führen. Umgekehrt gibt es aber auch Prozesse, die ursprünglich getrennt erledigt wurden, aber für das Lean Manufacturing zusammengelegt werden. Das wiederum erhöht dann die Vielseitigkeit der Arbeit.
Tipp: Grundsätzlich sollten Unternehmen das neue System des Lean Manufacturing zusammen mit ihren Angestellten entwickeln. Denn die Mitarbeiter kennen ihre alltäglichen Arbeitsschritte am besten. Sie können so wichtiges Wissen in die neuen Produktionsprozesse einbringen. Arbeitgeber können darüber hinaus durch das Einbinden der Angestellten sicherstellen, dass die Arbeitsbedingungen erträglich bleiben.
Die größte Änderung, die Lean Manufacturing für die Produktion mit sich bringt, sind veränderte Prioritäten bei den Optimierungskriterien. Ging es früher darum, dass möglichst alle Ressourcen gleich ausgelastet sind, steht bei der Lean Production der Kundenauftrag im Vordergrund. An ihm richten sich alle Prozesse aus. Ist er ideal nach Lean-Manufacturing-Kriterien geplant, ist die Auslastung einzelner Ressourcen automatisch mit gewährleistet.
Mehr Managementkonzepte:
Methoden des Projekt- und Prozessmanagements: Kaizen sowie Kanban und Scrum
Ein Beitrag von: