3D-Druck: Aktoren und Sensoren in Bauteile integrieren
Forscher am Fraunhofer LBF nutzen 3D-Druck um bei individualisierten Baugruppen die Zahl der Komponenten zu reduzieren und auf diese Weise den Herstellungsprozess zu vereinfachen. Auch der notwendige Bauraum nimmt durch diese Entwicklung ab.
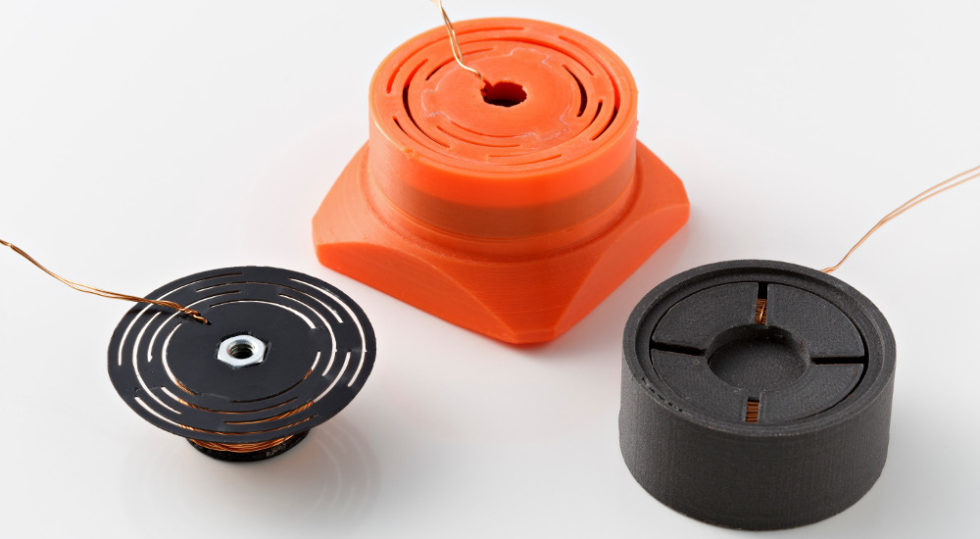
Diese mehrteiligen Tauchspulenaktoren wurden über die additive Fertigung hergestellt.
Foto: Fraunhofer LBF, Ursula Raapke
Der 3D-Druck rückt für viele Herstellungsprozesse immer stärker in den Fokus. Denn ein großer Vorteil der additiven Fertigung liegt auf der Hand: Wenn es gelingt, verschiedene Materialien in einem einzigen Arbeitsgang Schicht für Schicht aufzutragen, ist es deutlich leichter, einzelne Bauteile direkt zu integrieren. Das erspart unter anderem spätere Arbeitsgänge, bei denen sonst verschiedene Bauteile zusammengefügt würden. Auch die Langlebigkeit der Bauteile könnte sich durch solch ein Verfahren verbessern. Denn die Produktion aus einem Guss birgt in der Regel weniger Schwachstellen als herkömmliche Herstellungsweisen, bei denen mehrere Bauteile kombiniert werden. Das Fraunhofer-Institut für Betriebsfestigkeit und Systemzuverlässigkeit LBF möchte diese Vorteile auch für mechatronische Systeme nutzen. In mehreren Projekten suchen die Wissenschaftler nach einem Weg, Aktoren und Sensoren über 3D-Druck schon im ersten Arbeitsgang zu integrieren.
Materialeinsatz und Energiebedarf würden sinken
Während Sensoren als Messeinheiten in Leichtbaustrukturen beispielsweise störende oder schädigende Vibrationen detektieren sowie die Funktionsfähigkeit von Strukturen überwachen, ist es Aufgabe der Aktoren, mechanische Regelungsvorgänge durchzuführen. Nach Ansicht der Forscher könnte sich ihr Einsatzgebiet durch die additive Fertigung deutlich verbessern. „Sensoren können an kritischen Stellen integriert werden, die vorher nicht zugänglich waren: Davon können vor allem leichtbauoptimierte Strukturbauteile profitieren“, sagt Torsten Bartel, der die verschiedenen Projekte im Fraunhofer LBF leitete.
Bei den Aktoren wäre es seiner Ansicht nach möglich, sie in Bezug auf die erforderliche Kraft und den Bauraum erheblich zu individualisieren. Überdimensionierte Aktoren ließen sich so vermeiden – Materialeinsatz und Energiebedarf würden sinken. Er sieht einen weiteren Vorteil: „Schließlich ermöglichen es elektrisch leitfähige Materialien, auf externe Leitungen zur Signalführung und entsprechende Lötarbeiten zur verzichten. So lassen sich kompakte, funktionsintegrierte Systeme mit geringem Montageaufwand herstellen.“
Mechatronische Systeme mit Fused Filament Fabrication drucken
Im ersten Schritt suchten die Fraunhofer-Wissenschaftler nach einem geeigneten Gerät, mit dem sich parallel verschiedene Materialien im 3D-Druck verarbeiten lassen. Entschieden haben sie sich für sogenannte Fused Filament Fabrication (FFF)-Drucker. Sie verfügen über unterschiedliche Druckköpfe, sodass es möglich ist, in einem Arbeitsgang mehrere Kunststofffilamente zu drucken. Für die additive Fertigung mechatronischer Systeme verwendeten die Forscher auf der einen Seite Standardthermoplasten wie Acrylnitril-Butadien-Styrol-Copolymere (ABS) und Polypropylen (PP). Auf der anderen Seite benutzten sie Funktionsmaterialien wie elektrisch leitfähige oder weichmagnetische Materialien sowie Formgedächtnispolymere.
Dabei ist es ihnen gelungen, mit demselben Drucker elektrisch leitfähige Schichten zu drucken sowie Pasten, die piezoelektrisch wirksam sind, bei denen also eine elektrische Spannung auftritt, sobald sie elastisch verformt werden. Die Aushärtung des Materials erfolgte unter UV-Licht. Tests mit weiteren Materialien sollen folgen. Ziel ist es, über die additive Fertigung Funktionsbauteile herstellen zu können, bei denen alle benötigten Strukturen bereits enthalten sind.
Bauteile aus dem 3D-Drucker: Zwei erfolgreiche Praxistests
Die Forscher sind zwar noch weit davon entfernt, ihr System für die Serienproduktion einsetzen zu können, aber erste Erfolge konnten sie bereits verbuchen: Im Rahmen des Projektes Open Adaptronik haben sie einen Tauchspulenaktor entworfen und mit einem FFF-Drucker produziert. Dieser Linearantrieb war dafür gedacht, die Schwingungen an der Kamera einer Drohne zu mindern. Die Wissenschaftler verwendeten dafür ABS für den Spulenträger mit integrierter Feder und ein ferromagnetisches Filament zur Führung des magnetischen Flusses im Gehäuse des Aktors. Der Magnet wurde während der Herstellung in das Gehäuse eingedruckt. Die magnetischen Kräfte seien nach Aussage der Wissenschaftler vergleichbar gewesen mit Aktoren, die auf herkömmliche Weise hergestellt wurden.
In einem weiteren Projekt integrierten die Forscher über den 3D-Druck sensorische Funktionen in Bauteile, um den Strukturzustand in autonomen Fluggeräten zu überwachen. Dafür testeten sie verschiedene elektrisch leitfähige Kunststofffilamente. Mit diesen Erkenntnissen gelang es ihnen anschließend, Dehnungsmessstreifen und Kraft- beziehungsweise Beschleunigungssensoren im 3D-Druck zu produzieren. Nun suchen sie nach besser geeigneten Materialien, um Sensoren mit höherer Empfindlichkeit über die additive Fertigung produzieren zu können.
Weitere Beiträge zum 3D-Druck:
Ein Beitrag von: