Einfaches Bioprinting: Handelsüblicher 3D-Drucker wird zum Gewebedrucker?
Jetzt können auch kleine Labore und Schulen mit einem umgebauten 3D-Drucker biologische Strukturen drucken, dank einer kostengünstigen Bauanleitung. Trotz der Fortschritte bleibt es schwierig, komplexes Gewebe herzustellen.
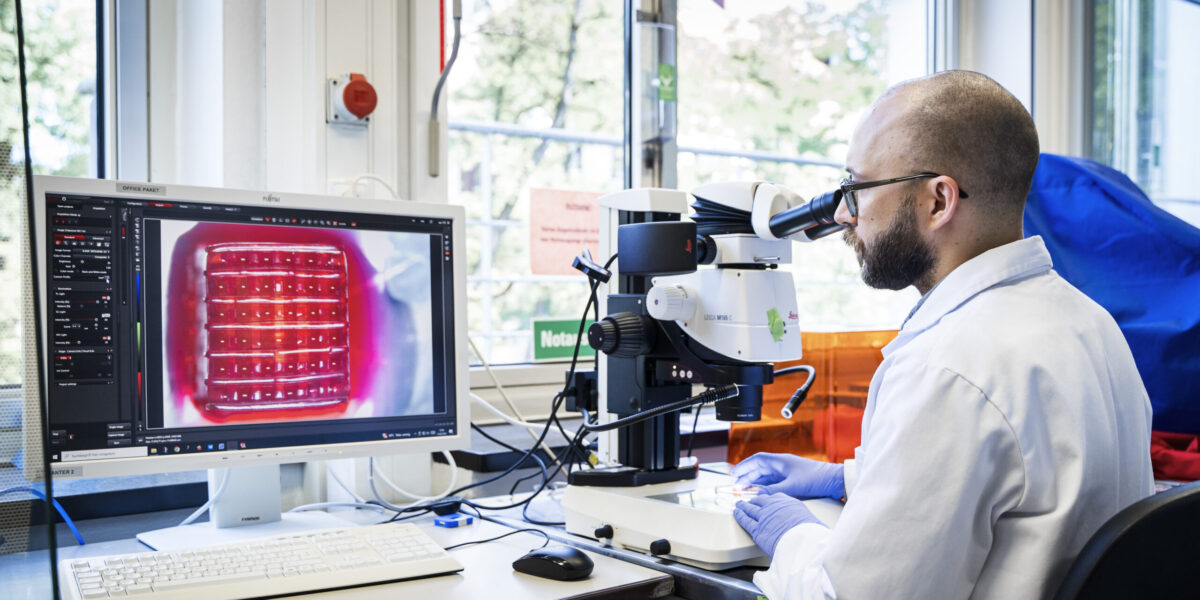
Benedikt Kaufmann von der Hochschule München entwickelte in seiner Dissertation eine kostengünstige Methode zum Drucken von Biostrukturen.
Foto: Johanna Weber
Einen lebendigen Gewebekonstrukt mit einem herkömmlichen 3D-Drucker aus dem Elektromarkt zu drucken, war bislang undenkbar. Bioprinting erforderte bisher kostenintensive Spezialgeräte. Nun ist es Forschenden gelungen, einen handelsüblichen 3D-Drucker so anzupassen, dass er biologische Strukturen auf Knopfdruck erzeugen kann. Dies eröffnet insbesondere kleineren Laboren die Möglichkeit, auf diesem Gebiet zu forschen.
Seit mehreren Jahrzehnten verwenden Forschende verschiedene 3D-Druckverfahren, um aus Biomaterialien und Zellen organische Strukturen zu erzeugen. Diese werden anschließend durch gezieltes Training auf ihre zukünftige Funktion vorbereitet. „Doch trotz aller Erfolge sind wir noch weit von unserem Ziel entfernt, maßgeschneidertes Gewebe im größeren Maßstab herzustellen. Um das Tissue Engineering weiterzuentwickeln, müssten Forschende auf der ganzen Welt kooperieren, Wissen generieren und teilen“, sagt Benedikt Kaufmann, Bioingenieur am Centrum für Angewandtes Tissue Engineering und Regenerative Medizin (CANTER) der Hochschule München. Er ist überzeugt, dass Tissue Engineering eine Zukunftstechnologie ist.
Künstlich hergestelltes Gewebe wie Knorpel, Knochen oder Muskeln hat viele Einsatzmöglichkeiten. Es könnte in der Pharmakologie helfen, Medikamente zu testen, oder in der Medizin, um Gewebeschäden zu behandeln. Die Herstellung von komplexem Gewebe mit den gleichen Eigenschaften wie natürlichem Gewebe ist jedoch schwierig.
Bioprinting ist teuer
Bislang scheitert die Forschung oft schon am Budget, bevor sie richtig beginnt: Bioprinter, mit denen dreidimensionale Zellstrukturen erstellt werden, kosten mehrere zehntausend Euro und sind für kleine Labore oft unerschwinglich. Im Rahmen seiner Promotion hat Kaufmann nun eine günstige Alternative entwickelt. Gemeinsam mit einem Team am CANTER und in Kooperation mit der Technischen Universität München hat er einen einfachen 3D-Drucker aus dem Elektromarkt, der normalerweise für Kunststoffmodelle genutzt wird, so umgebaut, dass damit lebendes Gewebe gedruckt werden kann. Die Open-Source-Bauanleitung ist jetzt für alle kostenlos zugänglich.
Kaufmann erklärt, dass die größte Herausforderung darin bestand, die richtigen Umgebungsbedingungen zu schaffen. Für die Verarbeitung von Proteinen und Zellen sei neben hoher Luftfeuchtigkeit auch eine konstante Temperatur von 37 Grad Celsius nötig gewesen. Nach umfangreichen Tests entschieden sich die Forschenden für eine kostengünstige Lösung: Heizfolien, die an das Aluminiumgehäuse des Druckers geklebt und durch einen Mikrocontroller gesteuert werden, erhitzen den Innenraum auf die benötigte Temperatur. Ein wassergetränkter Zellstoff sorgt dabei für eine Luftfeuchtigkeit von über 90 Prozent. Zudem ersetzten die Forschenden die Druckplattform des Druckers. Bei handelsüblichen Druckern ist diese aus Metall, doch der modifizierte 3D-Drucker verwendet eine Aufhängung, an der ein Glasplättchen befestigt wird. Darauf lassen sich Biomaterialien und Zellen direkt drucken und anschließend unter dem Mikroskop hochauflösend untersuchen.
Wie funktioniert der umgerüstete 3D-Drucker?
Der kompakte Drucker verwendet maskierte Stereolithographie, ein besonders schonendes Verfahren für Zellen. Dabei wird Licht von LEDs nach einem programmierten Muster durch ein Flüssigkristall-Display – ähnlich wie bei einem Handy oder Monitor – auf ein Glasplättchen projiziert, das mit einem gelartigen Hydrogel bedeckt ist. Durch das gezielte Aktivieren einzelner Pixel auf dem Display vernetzen und härten die Proteine im Hydrogel exakt an den gewünschten Stellen aus. So entsteht Schicht für Schicht ein dreidimensionales Konstrukt.
Neben den hochentwickelten Laborgeräten im CANTER-Labor der Hochschule München wirkt der umgerüstete 3D-Drucker fast winzig. „Unsere Versuche haben gezeigt, dass sich mit dem modifizierten 3D-Drucker organische Strukturgerüste mit unterschiedlicher Steifigkeit herstellen lassen – das ist wichtig, weil beispielsweise für Knochensubstanz eine höhere Härte erforderlich ist als für Muskelgewebe“, erklärt Kaufmann. Inzwischen ist es gelungen, Stammzellen während des Druckvorgangs direkt in die Strukturen einzufügen.
Handelsüblichen 3D-Drucker in einen Bioprinter umwandeln
Für Forschungsteams, die bisher keine Möglichkeit hatten, eigene Gewebekonstrukte herzustellen, sind die Nachrichten erfreulich. Sie können jetzt dank der im Internet verfügbaren Bauanleitung einen handelsüblichen 3D-Drucker einfach in einen Bioprinter umwandeln. Kaufmann hebt hervor, dass dafür kein ingenieurtechnisches Fachwissen nötig ist. Dies ermöglicht es auch kleinen Laboren, Erfahrung mit der Herstellung und Optimierung von künstlichem Gewebe zu sammeln, Wissen zu erweitern und zum Fortschritt im Tissue Engineering beizutragen. Sogar Schulen können mit dem modifizierten Drucker erste Erfahrungen im 3D-Druck von Biomaterialien sammeln.
Mehr Infos zu dem neuen Verfahren: https://www.sciencedirect.com/science/article/pii/S2468067224000373?via%3Dihub
Ein Beitrag von: