Extrem effektive Polsterung aus dem 3D-Drucker
US-amerikanische Forschende haben für Polsterungen eine neue Geometrie entwickelt. Sie soll in der Lage sein, Stöße besser abzufangen. Die Herstellung kann über einen 3D-Drucker erfolgen. Ein erster Praxistest ist viel versprechend gelaufen.
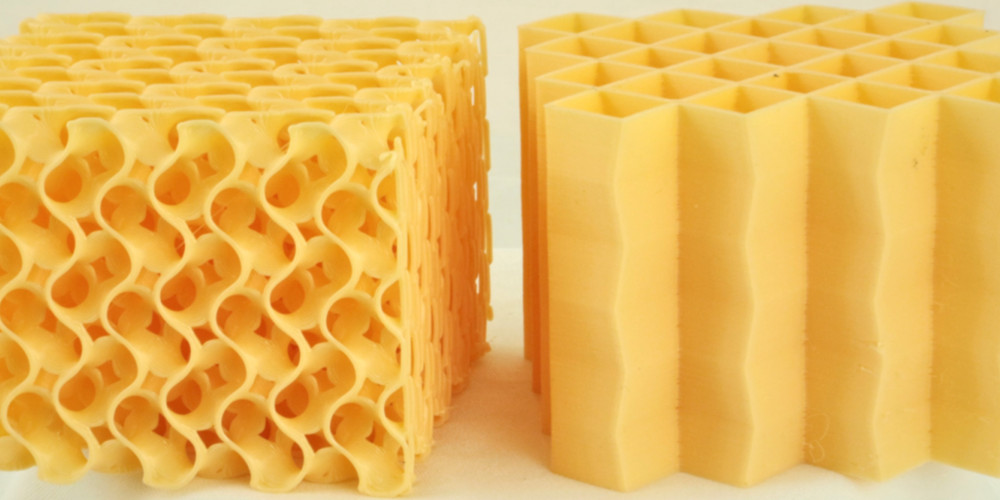
Das neue Polsterdesign (rechts) im Vergleich zu einem herkömmlichen Schaumstoff (links).
Foto: Lawrence Smith
Polstermaterialien spielen im Alltag eine größere Rolle, als es vielen Menschen bewusst ist. Sie schützen nicht nur zerbrechlich Ware, die in Paketen verschickt wird, sondern stecken zum Beispiel in Fahrradhelmen, in Leitplanken an Straßen oder in Schutzausrüstungen beim Sport. Sie bestehen in der Regel aus Schaumstoffen und erfüllen ihre Aufgaben gut, aber sie haben auch einen Nachteil: Wenn man einen Schaumstoff fest genug zusammendrückt, wird er schließlich zu einer starren Form zusammengepresst. Ein Forschungsteam der University of Colorado in Boulder und der Sandia National Laboratories will dieses Prinzip verbessern. Die Wissenschaftler und Wissenschaftlerinnen haben dafür die Geometrie der Polsterungen angepasst.
Die Form entscheidet über den Aufprallschutz einer Polsterung
Nicht jede Polsterung funktioniert gleich gut, beziehungsweise ist für jeden Zweck geeignet. Im ersten Schritt haben die Forschenden daher damit begonnen, Schaumstoffe im Detail zu analysieren – die besondere Form ist für die Federung zuständig, vor allem die kleinen Ecken und Ritzen. „Wenn man einen Schwamm zusammendrückt, schließen sich diese leeren Räume, wodurch die Aufprallenergie absorbiert wird“, erklärt Robert MacCurdy, Assistenzprofessor am Paul M. Rady Department of Mechanical Engineering an der CU Boulder. Das ist natürlich bekannt. Viele Wissenschaftler und Wissenschaftlerinnen haben bereits neue Strukturen entwickelt. Ein Beispiel sind Polsterungen, die aus einem Netzwerk sechseckiger Türme oder Plattengitter bestehen, die ein wenig wie Bienenwaben aussehen. Bei einem Aufprall brechen diese Waben in einem wellenförmigen Muster regelrecht zusammen und fangen den Stoß so auf.
Das Team um MacCurdy suchte aber nach einer Technologie, die nicht nur viel Kraft absorbiert, sondern auch viele verschiedene Arten von Kräften mit der gleichen Finesse auffangen kann. „Wenn Sie mit dem Fahrrad fahren und in einen Unfall geraten, wissen Sie nicht, ob es sich um einen Aufprall mit geringer Geschwindigkeit oder mit hoher Geschwindigkeit handelt. Aber trotzdem erwartet man, dass der Helm gut funktioniert“, sagte MacCurdy. Sein Ziel ist also eine Geometrie, die in all diesen Szenarien gut funktioniert.
Strukturen der neuen Polsterung brechen kontrolliert zusammen
Die Forschenden haben eine Simulations-Software verwendet, um das Innere der Schaumstoffe im Detail umzugestalten, und zwar bis auf einen Millimeter genau. Diese Form haben sie so verwendet, dass das Netzwerk von Waben einige Knicke aufweist, ähnlich wie die Bälge bei einem Akkordeon.
Diese Knicke tragen dazu bei, die Waben zu führen, wenn sie bei einem Aufprall zusammengedrückt werden. Der Zusammenbruch erfolgt dadurch deutlich sanfter. „In dem Moment, in dem man beginnt, diese Strukturen zusammenzudrücken, absorbieren sie eine gewisse Kraft“, sagt MacCurdy. „Die besten Absorberkonstruktionen halten eine konstante Kraft über den gesamten Kompressionsbereich aufrecht.“
Mit anderen Worten: Anders als ein Schaumstoff verhalten sich diese Kissen immer gleich, unabhängig davon, wie stark man sie zusammendrückt – oder zumindest bis zu einem bestimmten Maximum.
Struktur würde auch bei harten Materialien funktionieren
Die Forschenden beließen es aber nicht bei der Theorie. Sie benutzten einen handelsüblichen 3D-Drucker, um Blöcke in der Größe eines kleinen Ziegelsteins aus einem elastischen Material herzustellen, nämlich thermoplastischem Polyurethan. Diesen pressten sie mit einer Aufpralltestmaschine zusammen. Dabei stellte sich nach Angaben der Wissenschaftler und Wissenschaftlerinnen heraus, dass der Block etwa sechsmal mehr Energie absorbieren konnte als Standardschaumstoffe aus demselben Material und bis zu 25 Prozent mehr als andere Wabenkonstruktionen.
Das Team arbeitet jetzt daran, die neuen Strukturen weiter zu optimieren. Grundsätzlich sind die Forschenden davon überzeugt, dass diese Konstruktionen auch mit härteren Materialien wie Aluminium funktionieren könnten.
Ein Beitrag von: