Leichte Herstellung von Transistoren – Mit dem 3D-Drucker
Empa-Forscher wollen die gedruckte Elektronik einen kräftigen Schritt voranbringen. Mit besonderer Tinte und Spezialtechniken soll es gelingen, Schaltkreise unkompliziert auf flexiblen Oberflächen anzubringen, und das möglichst bald im industriellen Maßstab.
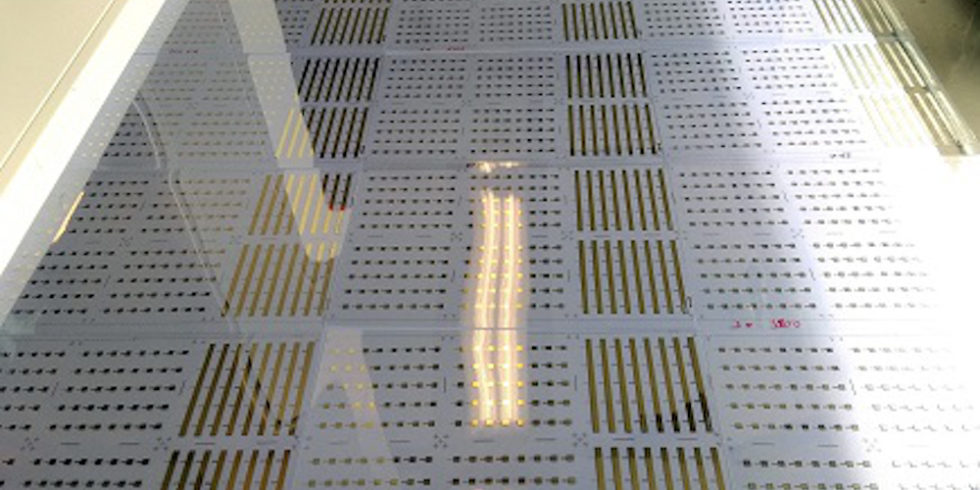
Elektroden für Transistoren. Perfekte Druckprozesse würden die Herstellung erleichtern.
Foto: Empa
Gedruckte Elektronik (Printed Electronics) ist keine neue Idee und ein großer Markt. Schon jetzt soll er laut dem Branchenverband für organische und gedruckte Elektronik bei über 35 Milliarden US-Dollar liegen (etwa 29,6 Milliarden Euro). Derzeit spielen OLED-Displays noch die größte Rolle, aber die wichtigste Nachricht lautet: Der Markt wächst. Vor allem in den Bereichen Internet der Dinge (IoT), Unterhaltungselektronik, Gesundheitswesen und der Automobilindustrie sowie bei smarten Verpackungen.
Mit den neuen Anwendungsgebieten haben sich auch die Anforderungen geändert. Früher mussten die Schaltkreise vor allem möglichst klein und trotzdem schnell sein. Heute stehen Preis und eine einfache Herstellungsweise im Vordergrund. Auch die Anwendungsumgebung ist eine andere. Denn viele Schaltkreise müssen auf dünnen und flexiblen Flächen funktionieren, etwa RFIDs auf Produktverpackungen oder Sensoren auf Lebensmitteln, die anzeigen, ob der Inhalt verdorben ist. Die Eidgenössische Materialprüfungs- und Forschungsanstalt (Empa) arbeitet daher gemeinsam mit Wissenschaftlern des Schweizer Paul Scherrer Instituts und der EPFL Lausanne daran, die Drucktechnik zu verbessern. Für das Projekt Functional OXIdes Printed on Polymers and Pape (FOXIP) haben sie schon einige Erkenntnisse gewonnen. Ziel sind neue Möglichkeiten für eine industrielle Produktion.
Flexible Oberflächen als Herausforderung
Elektronik lässt sich unter anderem mit Tinten drucken, in denen Metalloxide gelöst sind. Über spezialisierte Geräte werden diese auf den Unterlagen aufgebracht, wofür es unterschiedliche Techniken gibt. An diesen Verfahren gibt es allerdings noch eine Menge zu verbessern.
Es beginnt mit der Druckunterlage. Für herkömmliche Elektronikbauteile werden Siliziumscheiben verwendet, die absolut glatt sind. Papier oder Kunststofffolien sind hingegen nicht ganz so perfekt, weswegen die aufgedruckten Bauteile größer sein müssen. „Das heißt aber nicht, dass die Schaltkreise riesig sind: Wir reden beim Drucken von Genauigkeiten im Bereich von zehn Mikrometern, das ist weniger als der Durchmesser eines Haares“, sagt Empa-Forscher Jakob Heier vom Labor für funktionelle Polymere.
Graphen statt Hitze
Heier sieht die Tinte als das größere Problem an, obwohl seine Forschungen ihn schon auf einen guten Weg gebracht haben. Die Tinte muss leitende, halbleitende und isolierende Werkstoffe enthalten. Diese Eigenschaften müssen sie auch nach dem Druck haben oder zurückerlangen. Denn in der Tinte stecken zusätzlich Lösungsmittel, die nach dem Druckprozess verdampfen. Zum Teil kommen Bindemittel und weitere Zusatzstoffe hinein, damit die Tinte stabil bleibt. Außerdem braucht sie eine bestimmte Konsistenz. Diese Inhaltsstoffe können aber die Funktion des späteren Schaltkreises stören, weswegen sie ausgebrannt werden sollten.
Und schon taucht die nächste Herausforderung auf: Wie kann das möglich sein, ohne dem Trägermaterial zu schaden? Heier und sein Team entwickeln dafür eine druckfähige Tinte, in der nur Graphenteilchen und Lösungsmittel stecken, also nichts, was ausgebrannt werden müsste. Außerdem sollen die fertigen Schichten dabei auch ihre Leiteigenschaften behalten, wenn das Trägermaterial gebogen oder verdreht wird.
Hitzeblitze für Metalloxide
Die Forscher arbeiten auch mit Tinten, die auf Metalloxid-Nanopartikeln basieren. Hier kommt das sogenannte Sintern, also die thermische Behandlung der gedruckten Schichten, zum Einsatz. Auf diese Weise werden die Partikel, die in der Tinte gelöst sind, wieder miteinander verbunden. Erneut macht das temperaturempfindliche Trägermaterial Probleme. Yaroslav Romanyuk vom Labor für Dünnfilme und Photovoltaik der Empa ist auf die Idee gekommen, dafür eine Methode namens „Flash Sintering“ zu testen. Er erklärt: „Dabei wird die gedruckte Schicht mit ultrakurzen Blitzen erhitzt, so schnell, dass das Substratmaterial nicht miterhitzt wird.“
Tinte, die auf Metalloxiden basiert, ist für die Wissenschaftler besonders spannend, weil die Elektronen im fertigen Material sehr beweglich sind und daher das Potenzial in sich tragen, die Leistung von gedruckten elektronischen Schaltkreiselementen zu erhöhen. Zudem sind die Materialien an der Luft recht stabil. „Besonders spannend ist Indium-Zinn-Oxid: Es ist zugleich hochleitend und transparent“, sagt Romanyuk. Sein Team hat es bereits geschafft, oxidbasierte Feldeffekt-Transistoren per Tintenstrahldrucker zu drucken. Das Ziel der Forscher ist klar: Ihre Erkenntnisse sollen möglichst schnell zur industriellen Produktion der neuen gedruckten Elektronik führen.
Kennen Sie schon unseren Podcast „Druckwelle“? In diesem ingenieur.de-Podcast in Kooperation mit den VDI nachrichten dreht sich alles um die Additive Fertigung.
Jetzt reinhören
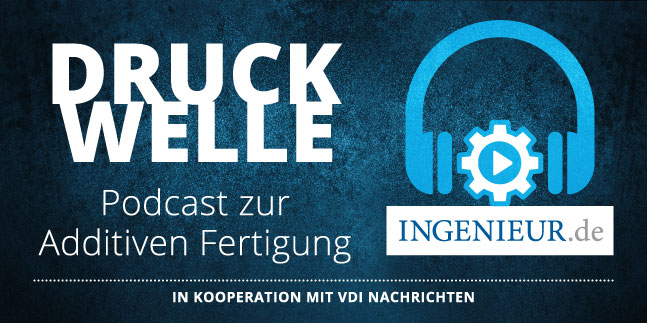
Der ingenieur.de-Podcast zur Additiven Fertigung erscheint alle 14 Tage donnerstags.
Foto: Getty Images | Faysal Ahamed | Stefan Ilic
Mehr zum Thema Produktion im Drucker:
Ein Beitrag von: