Spektakuläres Bauen mit dem Beton der Zukunft
Wenn im Juni das neu gebaute „Museum der Zivilisationen Europas und des Mittelmeerraumes“ in Marseille eröffnet wird, gibt es auch für Architekturliebhaber einiges zu bestaunen. Der Museumsneubau mit seiner beeindruckenden Konstruktion besteht aus ultrahochfestem Beton.
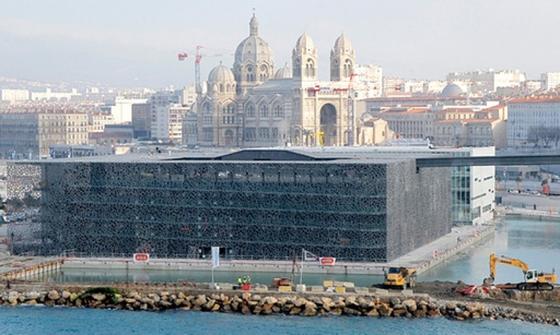
Blick auf das neue Museum der Zivilisationen Europas und des Mittelmeerraums (MUCEM) in Marseille, das aus ultrahochfestem Beton gefertigt wurde.
Foto: dpa
Wie eine filigrane Spitzendecke umhüllt die Außenhaut den quaderartigen Bau am Alten Hafen in Marseille. Für die graue „Spitzendecke“ und die zum benachbarten alten Fort herüberführende Fußgängerbrücke wurde ein ultrahochfester Beton (UHFB) verbaut. Der gegenüber dem einfachen Beton wesentlich verbesserte Werkstoff ist so stabil wie Stahl und hat eine enorme Druckfestigkeit.
Die Rezeptur des klassischen Betons besteht aus einem Gemisch von Zement, Wasser und Gesteinskörnungen. Durch das Wasser bilden die Mineralien im Zement feine Kristalle, die wachsen, sich gegenseitig durchdringen und einen festen Zusammenhalt bilden. Ingenieure versuchen ständig die Eigenschaften und Einsatzmöglichkeiten des Betons durch Beimischen von anderen Materialien zu verbessern. Resultat ist ein immer feineres und dichteres Betongefüge.
Bessere Energiebilanz als Normalbeton
Der seit einigen Jahren entwickelte ultrahochfeste Beton ist besonders dicht gepackt. Statt Kies werden feinster Silicastaub, Quarzmehl, Basaltmehl und Hochleistungsfließmittel verwendet, die sogar im Nanometerbereich jedes kleinste Gasloch ausfüllen. Dazu kommt Natursand mit hoher Festigkeit und einer günstigen Kornform. Der UHFB hält nun sechsmal so viel Druck stand wie Normalbeton. Offiziell spricht man ab 150 Newton pro Quadratmillimeter – das entspricht 15,3 Kilogramm pro Quadratmillimeter _– von UHFB. Durch die hohe Dichtigkeit ist der UHFB außerdem wesentlich witterungsbeständiger als Normalbeton. Chloridionen, wie sie etwa bei Tausalz vorkommen, können kaum eindringen.
Im Vergleich zum Normalbeton hat der UHFB auch eine wesentlich bessere Energiebilanz vorzuweisen, denn er setzt bei der Herstellung 40 Prozent weniger Kohlendioxid frei. Das liegt im Wesentlichen an einem deutlich geringeren Zementverbrauch. Beim Brennen von Kalkstein zu Zement entstehen große Mengen CO2. Etwa fünf Prozent des weltweiten CO2-Ausstoßes soll hierfür verantwortlich sein.
Einsatz im Brückenbau
Zum Einsatz kommt der ultrahochfeste Beton überall dort, wo hohe Belastbarkeiten und feine Strukturen gefordert sind, zum Beispiel im Brückenbau.
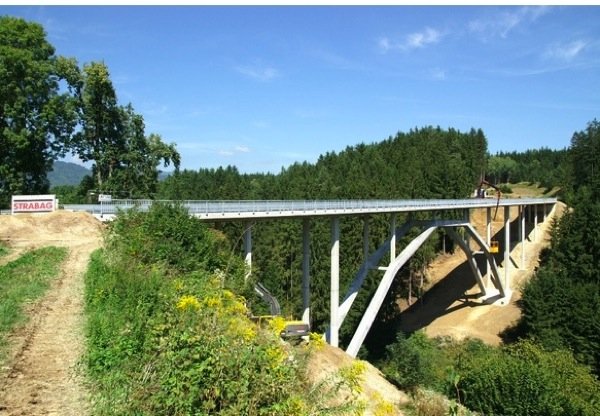
Die Wildbrücke Völkermarkt wurde am 01. Oktober 2010 eröffnet. Sie ist die erste Straßenbrücke der Welt, bei der das Tragwerk aus ultrahochfestem Beton besteht.
Quelle: Stadtgemeinde Völkermarkt
2010 wurde die „Wildbrücke“ im österreichischen Kärnten die erste Straßenbrücke der Welt, bei der das Tragwerk aus ultrahochfestem Beton besteht. Auf einer Höhe von 40 Metern und mit einer Gesamtlänge von 158 Metern überspannt die High-Tech-Brücke eine Talsohle. Die Dauerhaftigkeit des besonderen Betons vergleichen die Kärntner Ingenieure mit Granit, die Nutzungsdauer der Tragwerke sei mindestens fünfmal höher als die von vergleichbaren Strukturen aus Normalbeton. Für den Bogen der Wildbrücke prognostizieren sie eine Lebensdauer von über 200 Jahren.
Ein Beitrag von: