Audi ersetzt Fließband durch 200 Montageinseln
So funktionieren Smart Factories: Audi trennt sich von der Fließband-Fertigung. Stattdessen setzt der Autobauer in Ingolstadt auf autonome Transport-Roboter, welche die Karosserie an 200 Montageinseln vorbeifahren. Jedes Auto wird dadurch so einzigartig wie ein Maßanzug.
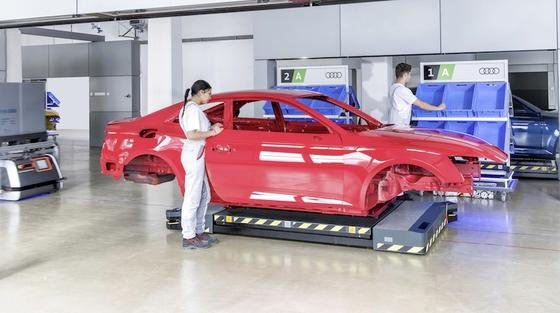
Die Karosserien fahren eigenständig zu den benötigten Montageinseln. Die Reihenfolge kann variieren – je nachdem, wo gerade Kapazitäten verfügbar sind. Das steigert die Produktivität und entlastet Mitarbeiter vom Fließbandstress.
Foto: Audi AG
Henry Ford hätte Bauklötze gestaunt. 103 Jahre nach seiner Einführung des Fließbandes verabschiedet sich Audi von der einst revolutionären Idee, welche die Massenfertigung von Autos ermöglicht hat. Warum? Weil Autos keine Stangenware mehr sind. Gerade in der Oberklasse sind individuelle Ausstattungen gefragt, es laufen praktisch keine zwei Fahrzeuge mehr identisch vom Band. „Nur mit dem einen, immer gleichen Produkt ergab die Fließband-Fertigung vor 100 Jahren Sinn“, sagt Audi-Vorstand Hubert Waltl. „Heute wolle unsere Kunden genau das Gegenteil: Jeder Audi soll so einzigartig sein wie ein Maßanzug.“
Audi setzt auf Smart Factory
Audi schafft deswegen das Fließband ab. Im Werk in Ingolstadt wird es stattdessen zukünftig 200 Montageinseln geben. Roboter heben die Karosserie auf autonome Transportwagen, die verschiedene Insel-Routen abfahren. „Wie vor den Kassen im Supermarkt, wo sich der Kunde an der kürzesten Warteschlange anstellt, steuert das vernetzte Fahrzeug zunächst die Stationen an, wo die Auslastung niedriger ist“, erklärt Ingenieur und Innovationsmanager Fabian Rusitschka, der Audi bei der Umstellung unterstützt.
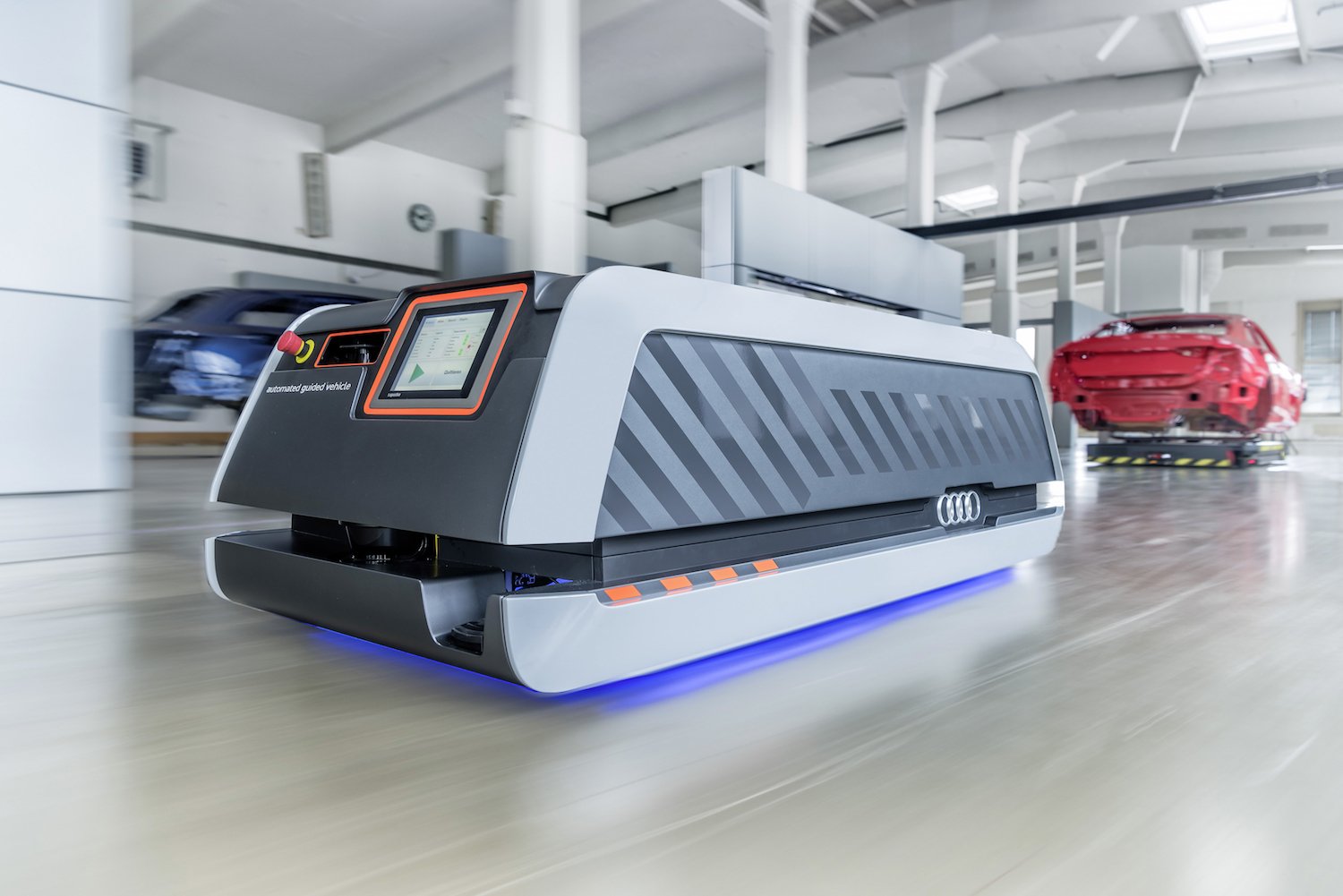
Autonome Fahrzeuge fahren Karosserien durch die Produktion. Mit dieser Alternative zum Fließband steigert Audi die Produktivität um 20 %.
Quelle: Audi AG
Im Werk in Neckarsulm hat Audi das Fließband schon abgeschafft – der Sportwagen R8 entsteht in modularer Montage. Als nächstes testet Audi sie im ungarischen Motorenwerk in Györ. Waltl: „Sie stellt also keine Zukunftsmusik mehr dar.“ Bei den Konkurrenten Daimler und BMW sind vergleichbare Pläne hingegen nicht bekannt. Audi positioniert sich als Vorreiter.
Produktivität steigt um 20 %
Der Umstieg auf Montageinseln sorgt für deutlich höhere Produktivität. Ist eine Station nicht erforderlich, lässt sie das Fahrzeug aus. „Der Kunde in Afrika hat keine Sitzheizung bestellt, also umfährt das Fahrzeug diese Einbaustation“, sagt Rusitschka. Bei Zweitürern seien die Türdichtungen schneller montiert als im Viertürer. „Das Fahrzeug verlässt die Station schneller, die gesamte Auslastung wird höher – am Ende des Tages haben wir mehr Fahrzeuge produziert.“ Waltl rechnet mit rund 20 % mehr Produktivität: „Wir würden´s nicht machen, wenn´s teuer wäre.“
Verzicht auf Fließband entlastet Mitarbeiter
Auch die Mitarbeiter profitieren von den Montageinseln. Jeder Fabrikarbeiter „weiß, was für ein Stress entsteht, wenn man taktgebunden arbeiten muss“, sagt Waltl.
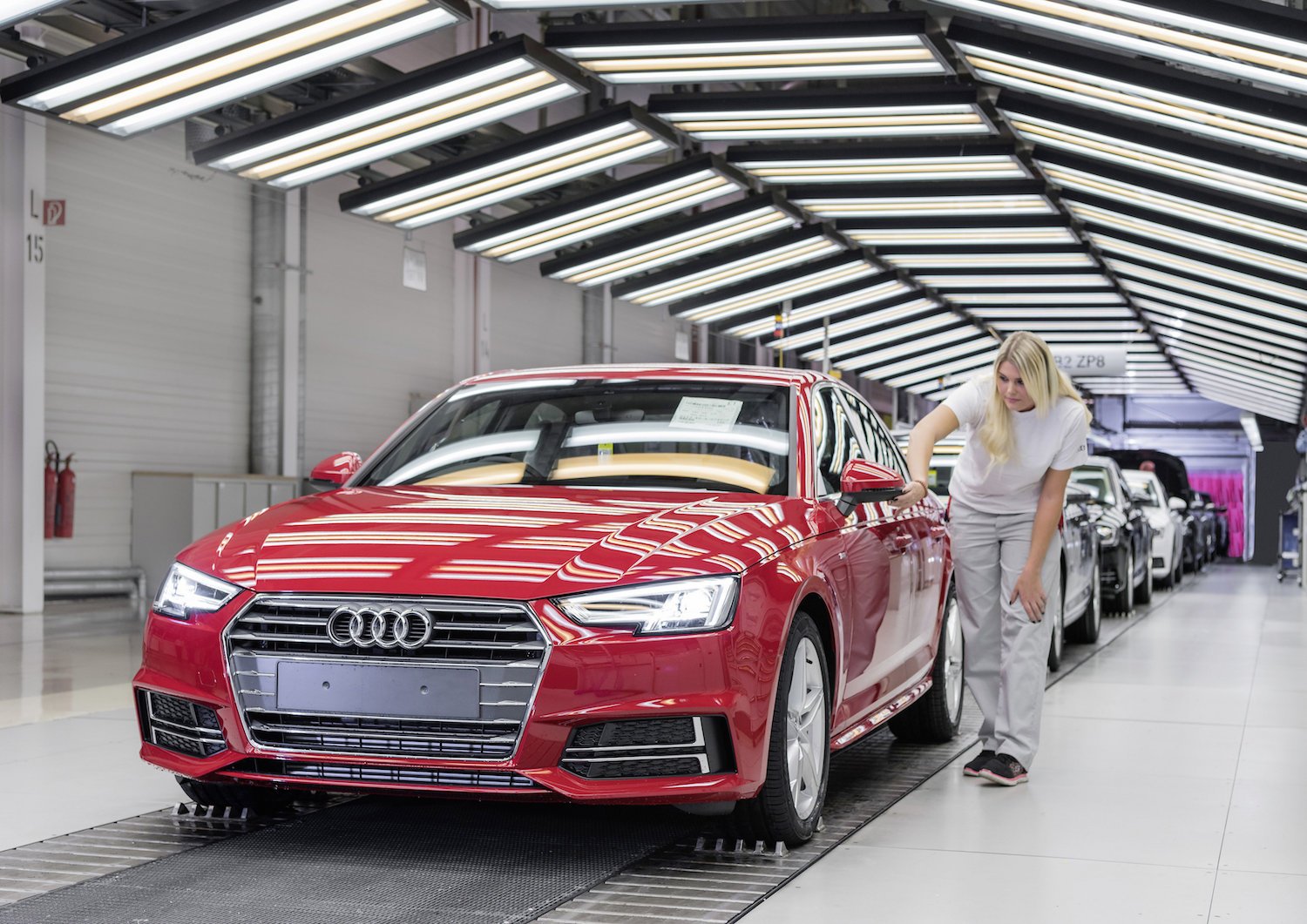
Tschüss, Fließband. Weil heutzutage quasi keine zwei Fahrzeuge mehr identisch vom Band laufen, verabschiedet sich Audi von der klassischen Produktionsmethode.
Quelle: Audi AG
Während an manchen Bändern im VW-Konzern ein 60-Sekunden-Takt gefahren wird, können auf den Montageinseln auch alte und behinderte Mitarbeiter mithalten. Niemand muss mehr befürchten, die Anderen aufzuhalten. Rusitschka: „Psychologen sagen, das ist positiv für die Gesundheit der Mitarbeiter.“
In nur vier Stunden lässt sich der Elektrolaster Charge von nur einer Person montieren. Mit diesem Truck, der leicht, leise und umweltfreundlich ist, will der Unternehmer Denis Sverdlov den britischen Lkw-Markt von hinten aufrollen. “ 2017 soll der Charge in unterschiedlichen Größen gebaut werden.
Ein Beitrag von: