Effizienter Leichtbau: 3D-Tapes legen und fügen in einem Arbeitsschritt
Eine materialeffiziente Faserverstärkung von Bauteilen wird per UD-Tapes möglich. Deren Verarbeitung gelingt jetzt noch einfacher, und zwar mit Hilfe von 3D-Tape-Legen. Insbesondere für Leichtbaukomponenten, die in geringer Stückzahl gefertigt werden, bietet die Methode einige Vorteile.
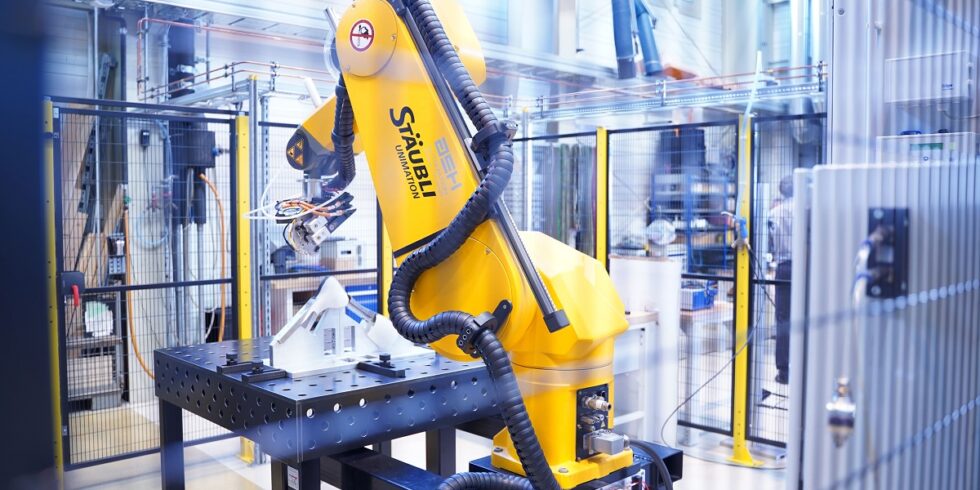
Der F3-Compositor ermöglicht die 3D-Ablage und gleichzeitiges Fügen von thermoplastischen UD-Tape-Halbzeugen.
Foto: Fraunhofer IMWS
Durch den Einsatz von UD-Tapes lassen sich Bauteile lastpfadgerecht und materialeffizient faserverstärken. Wenn diese Tapes in der Produktion dreidimensional positioniert werden, eröffnen sich zahlreiche Gestaltungsmöglichkeiten, vor allem für Leichtbaukomponenten, die in kleineren Mengen produziert werden.
In Kooperation mit dem Fraunhofer-Institut für Mikrostruktur von Werkstoffen und Systemen IMWS hat die Automation Steeg & Hoffmeyer GmbH (ASH) den F³-Compositor entwickelt. Dieser wurde erfolgreich im Polymer-Pilotanlagenzentrum PAZ umgesetzt. Das Besondere am F³-Compositor ist sein innovativer Ansatz, der das Ablegen von Tapes und das Verbinden der Halbzeuge kombiniert – und das mit hoher Reproduzierbarkeit und Materialeffizienz.
UD-Tapes bieten zahlreiche Möglichkeiten
Leichtbau hat sich weit über die Automobil- und Luftfahrtbranche als Megatrend etabliert. In vielen Bereichen besteht Bedarf an Bauteilen, die trotz geringen Gewichts eine hohe Belastbarkeit aufweisen. Hier bieten Thermoplast-Systeme, speziell mit unidirektional endlosfaserverstärkten Tapelagen (UD-Tapes), einige Vorteile. Die Verstärkungsfasern in diesen Tapes werden so platziert, dass sie optimal zum späteren Lastverlauf des Bauteils passen, wodurch besonders belastungsintensive Bereiche gezielt verstärkt werden können.
UD-Tapes lassen sich über diverse Verfahren verarbeiten. Das Tapelegeverfahren ist eines davon, hier erhitzt in der Regel ein Laser das UD-Tape und anschließend bringt eine Konsolidierungseinheit das Tape in die gewünschte Form. Auf ähnliche Weise lassen sich auch dreidimensionale Bauteile herstellen, und zwar mit der Wickeltechnik.
Ein weiteres Verfahren ist das Thermoformen von UD-Tapes. Dabei wird das Material mithilfe von Vakuum, Druckluft oder einer hydraulischen Presse in einem Spannrahmen erwärmt, bis es formbar wird. Danach formt man es mit speziellen Werkzeugen, Vakuum oder Druckluft, um die gewünschte Form zu erzielen.
3D-Tape-Legen für kleine Stückzahlen
Das 3D-Tape-Legen ist nach Meinung des Forschungsteams besonders für die Fertigung von Leichtbaukomponenten in kleineren Stückzahlen geeignet. Dabei können individuelle Designlösungen effizient und materialsparend umgesetzt werden. Ein Beispiel hierfür sind Orthesen aus der Medizintechnik: Durch das 3D-Tape-Legen können sie maßgeschneidert für Patienten hergestellt werden, wobei sie nicht nur extrem leicht, sondern auch hoch belastbar sind.
Moritz Vyhnal, Verantwortlicher für das Thema „Thermoplast-Tapelegen“ beim Fraunhofer IMWS erklärt: „Damit dies gelingt, muss allerdings das genaue Ablegen auf komplexen und 3D-geformten Geometrien möglich sein. Denn das Ablegen bestimmt die Position der Tapes und die Orientierung der darin enthaltenen Verstärkungsfasern in Bezug auf das Bauteil. Nur die korrekte Ablage stellt also sicher, dass tatsächlich die gewünschte Faserorientierung und damit die angestrebte Belastbarkeit im späteren Bauteil erreicht wird.“
F3-Compositor ermöglicht 3D-Ablage und gleichzeitiges Fügen
Wie bereits eingangs geschrieben, hat ASH in Zusammenarbeit mit dem Fraunhofer IMWS ein Gerät namens F3-Compositor entwickelt. Dieses Gerät gewährleistet bei der Fertigung von kleinen Stückzahlen eine hohe Reproduzierbarkeit und nutzt dabei die Vorzüge des 3D-Tape-Legens. Mit dem F3-Compositor können thermoplastische UD-Tape-Halbzeuge automatisiert, multiaxial abgelegt und zugleich in-situ verbunden werden.
Dank eines Sechs-Achs-Roboters und einem Lege-Kopf, der über eine umweltfreundlich optimierte Wasserstoff-Sauerstoff-Heizquelle verfügt, ist eine lastpfadgerechte und materialeffiziente Faserverstärkung von Bauteilen möglich. Dies geschieht durch das linienförmige oder flächige Ablegen von Tape-Einzelbahnen oder -Patches mit Geschwindigkeiten von bis zu 1 m/s.
„Die konstante Lege-Geschwindigkeit im komplexen 3D-Raum ist von entscheidender Bedeutung für die Qualität der Ergebnisse. Dafür bieten wir nun eine Lösung, die zudem sehr materialeffizient ist und mit geringem Aufwand für verschiedene Tape-Breiten angepasst werden kann. Durch den materialeffizienten Ansatz ist auch der Einsatz von kostenintensiven Materialien wie Kohlefaser-Verstärkungen wirtschaftlich möglich“, erläutert Vyhnal.
Bislang Verarbeitung von zwei Tapebreiten möglich
Im Technikum des Fraunhofer-Pilotanlagenzentrums für Polymersynthese und -verarbeitung PAZ in Schkopau ist derzeit mit dem F3-Compositor die Verarbeitung von Tapes mit einer Breite zwischen 3 mm und 12 mm realisierbar.
Eine eigens von der Firma SWMS Systemtechnik entwickelte Software erleichtert dabei die Programmierung und ermöglicht eine Prozess-Simulation basierend auf CAD-Daten. Diese berücksichtigt Aspekte wie Materialverbrauch, Kollisionsprüfung und Zykluszeit-Berechnung.
Zudem ist geplant, das Technikum bis Ende 2023 um einen 2D-Leger zu erweitern. Dieser wird in der Lage sein, belastungsoptimierte, flache Tape-Laminate mit minimalem Schnittabfall zu produzieren.
Ein Beitrag von: