Fraunhofer IPT’s Multi-Technologie-Plattform mit Laser und Lichtbogen
Das Fraunhofer IPT entwickelt innovative Verfahren für präzise und kostengünstige Bearbeitung großer Bauteile mit Laser und Lichtbogen. Die Integration von drei Technologien in einen Industrieroboter ermöglicht adaptive Fertigungsprozesse, die die Herstellung, Beschichtung, Reparatur von Metallbauteilen und die Bearbeitung von Glasdisplays einschließen.
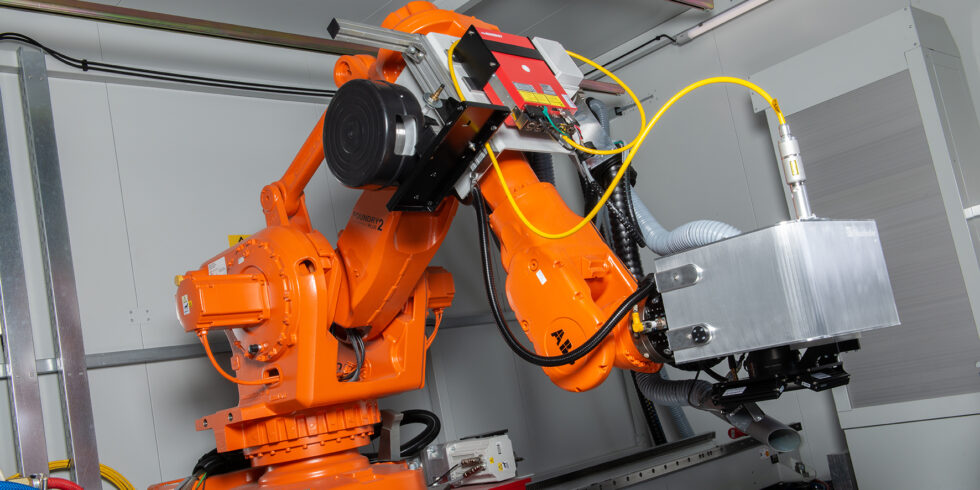
Innovative Fertigungstechnologien bei Fraunhofer IPT: Präzise Bearbeitung großer Bauteile mit Laser und Lichtbogen für vielseitige Anwendungen.
Foto: Fraunhofer IPT
Laser und Lichtbogen stellen effiziente und nachhaltige Verfahren zur Reparatur und Verbesserung von Oberflächen dar. Allerdings sind herkömmliche Anlagen für Strukturierung oder Auftragschweißen oft mit hohen Investitionskosten verbunden, die viele Unternehmen scheuen. Das könnte sich nun ändern.
Das Fraunhofer-Institut für Produktionstechnologie IPT hat erfolgreich drei Verfahren – Laserstrukturieren, Laser-Auftragschweißen und Lichtbogen-Auftragschweißen – in einen handelsüblichen Industrieroboter integriert. Diese Entwicklung ermöglicht es dem Fraunhofer IPT Auftragsforschung anzubieten, die sich auf die schnelle, präzise und kostengünstige Bearbeitung großer Bauteile aus Metall und sogar Glas erstreckt, mit Abmessungen von bis zu 2,5 x 4 Metern.
WAAM-Bearbeitungskopf setzt neue Maßstäbe in der Industrierobotik
In einer aktuellen Pressemitteilung hat das Fraunhofer IPT verkündet, erfolgreich einen neuen Bearbeitungskopf für das Lichtbogenauftragschweißen (WAAM – Wire Arc Additive Manufacturing) qualifiziert zu haben. Damit wurde bereits das dritte Bearbeitungsverfahren erfolgreich in die Anwendung mit einem konventionellen Industrieroboter umgesetzt.
Dieser innovative Kopf nutzt ein anwendungsoptimiertes System der Fronius Deutschland GmbH und wurde erfolgreich in einen hauseigenen Industrieroboter integriert. Vor diesem Erfolg hatten die Experten des Fraunhofer IPT bereits Bearbeitungsköpfe für das Laserstrukturieren sowie das Laserauftragschweißen mit Draht (LMD-w – Laser Metal Deposition with wire) in das Robotersystem eingefügt.
Viele Anwendungsmöglichkeiten
Das Fraunhofer IPT arbeitet mit der Industrie zusammen, um kostengünstige und anpassungsfähige Fertigungsprozesse zu entwickeln. Dabei sollen diese Prozesse in bestehende Produktionsumgebungen integrierbar sein. Die Anwendungen umfassen nicht nur die Herstellung, Beschichtung und Reparatur von Metallbauteilen, sondern erstrecken sich auch auf die Bearbeitung von Glasdisplays mit funktionalen Oberflächenstrukturen. Dank der großzügigen Arbeitsfläche und der hohen Beweglichkeit des Roboterarms sei diesen Informationen zufolge sogar die Bearbeitung großer Bauteile möglich, beispielsweise Rotorblätter von Wasserkraftwerken, wobei eine hohe Designfreiheit gewährleistet ist.
Präzise und flexible Bauteilbearbeitung
Die Systemflexibilität ermöglicht eine reibungslose Kombination unterschiedlicher Technologien, ohne dass eine Neuspannung des Bauteils erforderlich ist. Der einfache Austausch des Bearbeitungskopfes erlaubt eine schnelle und unkomplizierte Kombination von Verfahren wie dem Laserauftragschweißen und dem Strukturieren, sei es additiv oder subtraktiv.
Um im Wettbewerb mit bestehenden hochpräzisen Anlagen zu bestehen, wurde der Laserstrukturierkopf für automatische Erkennung und eigenständige Korrektur von Positionsabweichungen optimiert. Funktionstests bestätigen die präzisen Ergebnisse des neuen Systems mit integrierten Kompensationsmethoden auf verschiedenen Oberflächentypen wie matten, lackierten, reflektierenden, flachen und gekrümmten Oberflächen. Der Bearbeitungskopf ist zudem mit einem integrierten Messsystem ausgestattet, das Qualitätsschwankungen während des laufenden Prozesses erkennt und aktiv gegensteuert.
Zusätzlich wird eine Modellierungssoftware in das Bahnplanungssystem integriert, um Oberflächenreflexionen für verschiedene Werkstoffe und Positionen des Bearbeitungskopfes präzise vorherzusagen. Diese Integration verbessert signifikant die Präzision des Prozesses und minimiert die Fehleranfälligkeit.
Digitale Innovationen für das Lichtbogenauftragschweißen
Im Rahmen des öffentlich geförderten Forschungsprojekts „KI4ToolPath“ entwickelt das Fraunhofer IPT eine digitale Bahnplanung für das Lichtbogenauftragschweißen. Die Planungssoftware erkennt und korrigiert automatisch Prozessschwankungen mithilfe von umfangreichen Prozessdaten, die durch integrierte Sensoren gesammelt werden. Um die großen Datenmengen in Echtzeit zu verarbeiten, nutzt das Fraunhofer IPT 5G-Mobilfunktechnologie vom 5G-Industry Campus Europe in Aachen.
Im Projekt „Vitamine_5G“ entsteht ein System zur dezentralen Prozessüberwachung, das es Anwendern ermöglicht, die laufende Bearbeitung aus der Ferne zu kontrollieren. Die Sensordaten werden in einem Edge-Cloud-System gespeichert, aufbereitet und in einer Virtual-Reality-Umgebung dargestellt. Mithilfe einer VR-Brille können Maschinenbediener den Prozess beobachten, überwachen und korrigieren, ohne vor Ort präsent zu sein.
Ein Beitrag von: