KI-Roboter druckt selbstständig die perfekten Stoßdämpfer
US-Forschende haben einen autonomen Roboter entwickelt, der dank künstlicher Intelligenz perfekte Formen für Stoßdämpfer schafft, die kein Mensch je besser hätte machen können. Auf diese Weise lassen sich Helme, Verpackungen und Stoßstangen mit sehr hoher Sicherheit herstellen.
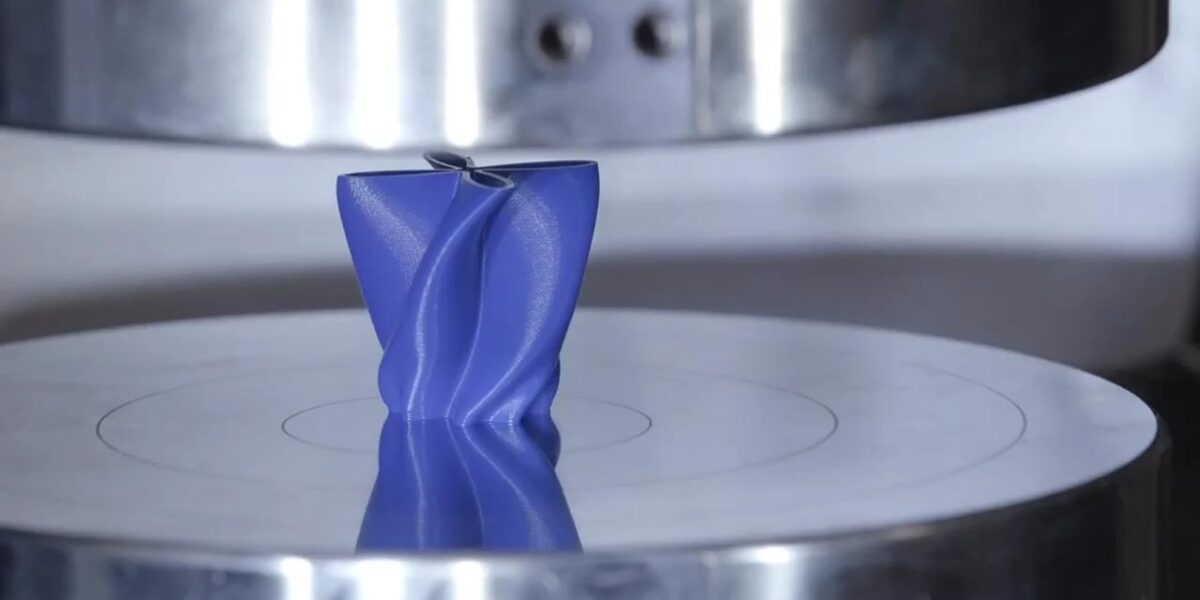
Der Roboter MAMA BEAR der Universität Boston erstellt und testet autonom energieabsorbierende Strukturen und erreichte kürzlich einen Rekordwirkungsgrad von 75 %.
Foto: Devin Hahn, Boston University Productions
In einem Labor des College of Engineering der Boston University lässt ein Roboterarm kleine Kunststoffobjekte in eine perfekt platzierte Box fallen. Diese winzigen Strukturen, federleichte, zylindrische Teile, nicht größer als ein Zentimeter, füllen die Box eine nach der anderen. Einige sind rot, andere blau, lila, grün oder schwarz. Jedes Objekt stammt aus einem Experiment zur Roboterautonomie. Der Roboter sucht selbstständig nach der effizientesten energieabsorbierenden Form. Dabei lernt er ständig dazu und versucht, das ideale Objekt zu bauen, das es noch nie zuvor gegeben hat.
So arbeitet der Roboter
Auf der Suche nach dem besten Schockabsorber stellt der Roboter mit einem 3D-Drucker eine kleine Kunststoffstruktur her. Er erfasst ihre Form und Größe, platziert sie auf eine flache Metalloberfläche und zerdrückt sie mit einem Druck, der dem Gewicht eines ausgewachsenen Araberpferdes auf einer Münze entspricht. Anschließend misst der Roboter, wie viel Energie die Struktur absorbiert hat und wie sich ihre Form verändert hat. Alle Details speichert er in einer umfangreichen Datenbank.
Dann lässt der Roboter das zerdrückte Objekt in die Box fallen und wischt die Metallplatte sauber. Er druckt und testet das nächste Teil, das sich nur geringfügig vom vorherigen unterscheidet. Das Design und die Abmessungen werden vom Computeralgorithmus des Roboters auf Grundlage aller früheren Experimente optimiert. Dieser Prozess, bekannt als Bayessche Optimierung, verbessert die 3D-Strukturen mit jedem Experiment, um den Aufprall besser zu absorbieren und nicht zerquetscht zu werden.
Aktuelle Iteration läuft ununterbrochen seit drei Jahren
Diese Experimente sind dank der Arbeit von Keith Brown, einem außerordentlichen Professor für Maschinenbau, und seinem Team im KABlab möglich. Der Roboter, genannt MAMA BEAR, steht für „Mechanics of Additively Manufactured Architectures Bayesian Experimental Autonomous Researcher“. Seit seiner ersten Konzeption durch Brown und sein Labor im Jahr 2018 hat sich MAMA BEAR stetig weiterentwickelt.
Bis 2021 hatte das Labor den Roboter auf die Suche nach einer Form geschickt, die Energie effizient absorbiert. Diese Eigenschaft ist als mechanische Energieabsorptionseffizienz bekannt. Die aktuelle Iteration läuft seit über drei Jahren ununterbrochen und hat bereits Dutzende von Boxen mit mehr als 25.000 3D-gedruckten Strukturen gefüllt.
Warum so viele Formen?
Laut Forschungsteam gibt es unzählige Verwendungsmöglichkeiten für Strukturen, die Energie effizient absorbieren können. Beispiele sind Polsterungen für empfindliche elektronische Geräte oder Schutzausrüstung wie Knieschoner und Handgelenkschützer für Sportler. „Man könnte aus dieser Datenbibliothek auch bessere Stoßstangen für Autos oder Verpackungsmaterial herstellen“, sagt Brown.
Um optimal zu funktionieren, müssen die Strukturen ein perfektes Gleichgewicht finden. Sie dürfen nicht so stark sein, dass sie das zu schützende Objekt beschädigen, aber stark genug, um Stöße zu absorbieren. Vor MAMA BEAR war die beste beobachtete Struktur zu etwa 71 Prozent energieabsorbierend, sagt Brown. Doch an einem kühlen Januarnachmittag im Jahr 2023 erreichte der Roboter eine Effizienz von 75 Prozent und brach damit den bekannten Rekord. Die Ergebnisse wurden kürzlich in Nature Communications veröffentlicht.
„Als wir anfingen, wussten wir nicht, ob wir diese rekordverdächtige Form erreichen würden“, sagt Kelsey Snapp, eine Doktorandin in Browns Labor, die MAMA BEAR beaufsichtigt. „Langsam, aber sicher steigerten wir uns und brachen schließlich durch.“
Rekordstruktur sieht anders aus als erwartet
Die rekordverdächtige Struktur sieht anders aus als erwartet: Sie hat vier Spitzen, die wie dünne Blütenblätter geformt sind, und ist höher und schmaler als die ersten Entwürfe. „Wir sind begeistert, dass wir aus den zahlreichen mechanischen Daten allgemeine Designprinzipien ableiten können“, sagt Brown.
Diese umfangreichen Daten finden bereits ihre erste praktische Anwendung. Sie fließen in die Entwicklung neuer Helmpolsterungen für Soldaten der US-Armee ein. Brown, Snapp und Emily Whiting, eine außerordentliche Professorin für Informatik am BU College of Arts & Sciences, arbeiteten mit der US-Armee zusammen. Sie führten kürzlich Feldtests durch, um sicherzustellen, dass die Helme mit der zum Patent angemeldeten Polsterung bequem sind und ausreichend Schutz bieten. Die 3D-Struktur für die Polsterung unterscheidet sich von der rekordverdächtigen Form. Sie ist in der Mitte weicher und kürzer, um den Komfort zu erhöhen.
Ein Beitrag von: