Präzisionsbauteile berühungslos vermessen
Mit einem neuen Messgerät lassen sich Nocken- und Kurbelwellen berührungslos vermessen. Das klappt sogar, wenn sie mit ein paar Tausend Umdrehungen pro Minute rotieren.
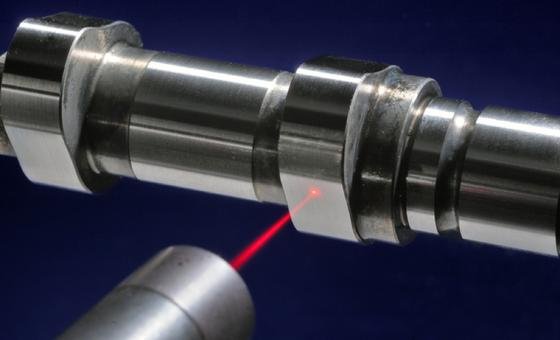
Form- und Rauheitsmessung an einer Nockenwelle mit dem Sensor bd-1.
Foto: Fraunhofer ILT, Aachen
Nocken- und Kurbelwellen sind kompliziert geformte Bauteile. Die Fertigungsgenauigkeit muss im Tausendstel-Millimeter-Bereich liegen, damit der Automotor, für den sie bestimmt sind, leise läuft und wenig Sprit schluckt. Für Messtechniker in der Qualitätskontrolle ist das eine echte Herausforderung, denn die Geräte, mit denen sie die Form überprüfen, müssen noch zehnmal genauer sein. Gemessen wird heute mit feinen Spitzen, die die Bauteile Mikrometer für Mikrometer abtasten. Die Beschaffenheit der Oberfläche, die ebenfalls zur Motorgüte beiträgt, ermittelt in einem zweiten Arbeitsgang ein Perthometer. Das ist ebenfalls ein Mikrotaster, der über die Oberfläche gezogen wird. Seine Ausschläge sind ein Abbild der Oberfläche.
Genauere Ergebnisse mit dem bidirektionalen Sensor
Die beiden zweitaufwändigen Verfahren können sich die Motorenbauer künftig sparen und dennoch genauere Ergebnisse erzielen. Das ist möglich mit bd-1, einem „bidirektionalen Sensor“, der am Fraunhofer-Institut für Lasertechnik in Aachen entwickelt worden ist. In einem einzigen Arbeitsgang vermisst er Kurbel- und Nockenwellen und ermittelt die Rauheit der Oberfläche. Und das, ohne das Bauteil zu berühren. Die fertige Welle wird von einem Laserstrahl abgetastet, während sie mit ein paar Tausend Umdrehungen pro Minute rotiert. Die Oberfläche reflektiert den scharf gebündelten Strahl, der auf dem gleichen Weg ins Messgerät zurückkehrt. Dort erfasst ihn ein Fotosensor. Aus der Laufzeit des Laserstrahls ermittelt ein Computer die Entfernung. Er vergleicht viele Tausend Messdaten mit den Sollwerten. Bei zu großen Abweichungen landet die Welle im Schrott.
70.000 Messungen pro Sekunde
Während herkömmliche Messgeräte regelmäßig justiert werden müssen, damit sie stets präzise arbeiten, entfällt dieser Arbeitsschritt beim bd-1-Sensor, weil die Laserdiode, die den Messstrahl aussendet, und der Fotosensor, der ihn wieder einfängt, im Gerät feste Plätze haben. Pro Sekunde schießt die Diode 70.000 Laserblitze ab. Die Messgenauigkeit liegt bei einer rotierenden Welle im 100-Nanometer-Bereich (ein Nanometer ist ein Millionstel Millimeter). Dabei ist es egal, wie die Oberfläche des Prüflings aussieht, ob sie also geschliffen ist oder gar glänzt.
Nockenwellen öffnen und schließen die Motorventile, durch die die verbrannten Abgase entweichen, mit einer Zeitgenauigkeit von einigen Millionstel Sekunden. Kurbelwellen setzen die Auf- und Abbewegung der Kolben in Rotation um.
Ein Beitrag von: