BMW-Werk München rüstet sich für reine E-Auto-Produktion
BMW-Stammwerk in München wird zur E-Auto-Produktionsstätte: 650 Mio. Euro soll der Umbau kosten, der bei laufendem Betrieb durchgeführt wird. Im Jahr 2026 sollen in München dann nur noch Elektrofahrzeuge gebaut werden.
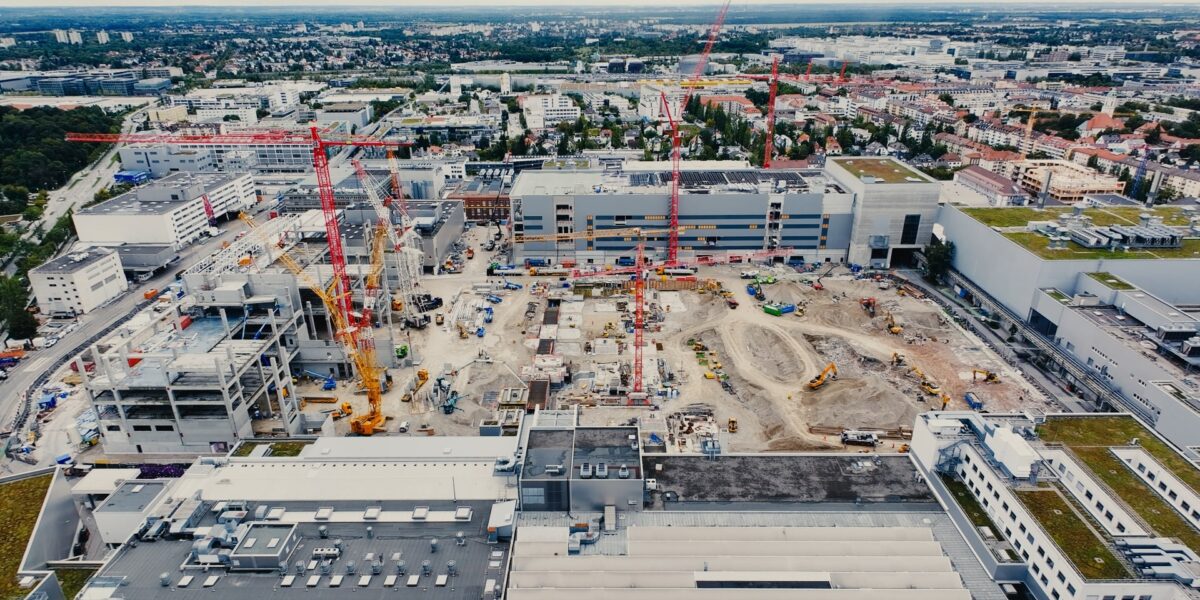
Noch ist das BMW-Werk in München eine riesige Baustelle, doch bereits 2026 sollen hier nur noch E-Autos produziert werden.
Foto: BMW AG
Das traditionsreiche BMW-Werk in München, ein Herzstück des Unternehmens mit täglich rund 1.000 gefertigten Fahrzeugen und knapp 7.000 Mitarbeitenden, bereitet sich auf eine umfassende Transformation vor. Ab 2026 sollen hier ausschließlich Elektroautos der neuen „Neue Klasse“-Architektur produziert werden. BMW plant, dafür 650 Millionen Euro in die Erweiterung und Neustrukturierung von Karosseriebau, Montage und Logistikflächen zu investieren. Der besondere Clou: Die Arbeiten erfolgen im laufenden Betrieb, ohne die derzeitige Fahrzeugproduktion zu unterbrechen.
Innovationspartnerschaft als Schlüssel zum Erfolg
Für das komplexe Projekt setzt BMW auf ein kooperatives Partnering-Abwicklungsmodell. Anders als bei traditionellen Bauprojekten, bei denen Verantwortlichkeiten häufig aufgeteilt und durch mehrere Schnittstellen geführt werden, arbeiten bei diesem Vorhaben alle Partner, darunter BMW selbst, die Drees & Sommer SE sowie die PORR AG, Hand in Hand zusammen.
„Die gemeinsame Verantwortung führt zu einer besseren Kommunikation und höheren Qualität bei Bauprojekten“, erklärt Maximilian Lammel, Senior Teamleiter bei Drees & Sommer. „In konventionellen Abwicklungsmodellen gibt es viele Teilbereichs-Verantwortliche und die Kommunikation läuft über mehrere Schnittstellen. Das führt gerade bei Großprojekten oft zu Missverständnissen und hemmt den Informationsfluss.“
Im Partnering-Modell ist es das Ziel, alle Projektbeteiligten auf Augenhöhe zu bringen. Durch die frühzeitige Integration aller Beteiligten wird ein gemeinsames Verständnis geschaffen, das Missverständnissen vorbeugt und den Informationsaustausch fließend gestaltet. So werden Projektrisiken minimiert und die Effizienz gesteigert.
Lean-Management-Prinzipien
Um den engen Zeitplan zu halten, setzt das Projektteam auf die Prinzipien des Lean Managements. Diese Methode ist eng mit der Automobilindustrie verbunden, wo ein hochgradig koordinierter Produktionsablauf den Standard darstellt. Jeder Schritt wird bis ins Detail geplant, und mögliche Störungen werden sofort analysiert und behoben. „Mit der von uns entwickelten Methode des Lean Construction Managements wird der Ansatz aus der Automobilindustrie auf Bauprojekte übertragen,“ erläutert Florian Langlotz, Partner bei Drees & Sommer und Leiter des Automotive-Bereichs.
Der Lean-Ansatz erlaubt es, den Bauprozess so präzise zu koordinieren, dass alle Gewerke genau zur richtigen Zeit am richtigen Ort arbeiten können. Leerläufe werden vermieden, und es gibt keine Verzögerungen, da alle notwendigen Ressourcen zur Verfügung stehen. Ein Beispiel für die Effektivität des Ansatzes: Innerhalb von nur zehn Tagen entstand das Rohbau-Achsraster für eine neue Montagehalle.
Der digitale Zwilling als zentraler Baustein der Planung
Zur Minimierung von Planungsunsicherheiten kommt die digitale Zwillingstechnologie zum Einsatz. Dabei handelt es sich um ein virtuelles Abbild des Bauprojekts, das sämtliche relevanten Gebäudedaten – von Geometrie über Materialeigenschaften bis zu Brandschutz- und Schallschutzmerkmalen – bündelt. „Um auf der Baustelle keine bösen Überraschungen zu erleben, setzen wir auf virtuelle Planung,“ so Simon Rogalski, Senior Teamleiter bei Drees & Sommer.
Der digitale Zwilling erlaubt eine nahezu fehlerfreie Umsetzung: Konflikte, die sich erst während des Baus zeigen würden, werden bereits im Modell sichtbar und können rechtzeitig angepasst werden. Indem alle Planungs- und Baubeteiligten auf das gleiche Modell zugreifen, bleibt die Planung transparent und in Echtzeit aktuell. Teure Verzögerungen und Planungsfehler, die sich während des Baus oft negativ auf den Zeitplan auswirken, werden somit weitgehend vermieden.
Wenn alles läuft, wie geplant, sollen ab 2026 in München nur noch Elektrofahrzeuge vom Band laufen.
Ein Beitrag von: