Das Ziel ist ein Passivhaus aus Altglas
Dämmend, tragfest, wasserdicht, nicht brennbar, extrem langlebig: Schaumglas hat eine Menge guter Eigenschaften, war jedoch bisher für viele Anwendungen zu teuer. Das Weimarer Start-up MinCell will den Baustoff nun preiswerter produzieren und so den Markt erweitern. Mittelfristiges Ziel: ein Passiv-Haus, das fast ausschließlich aus geschäumtem Altglas gebaut wird.
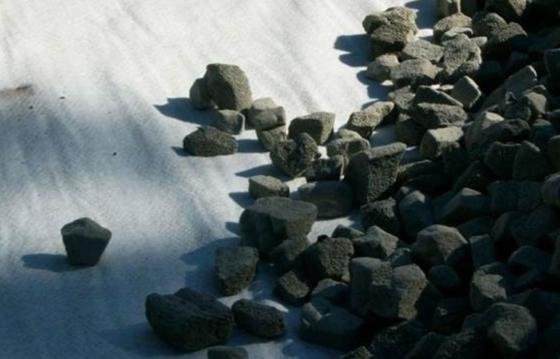
Das Start-up MinCell sieht vielfältige Einsatzmöglichkeiten für Schaumglasschotter.
Foto: MinCell
Der Würfel sieht wie Bimsstein aus, ist aber noch leichter. Kein Wunder: „Er besteht zu über 90 % aus Luft“, sagt Klaus Dvorak, einer der Gründer von MinCell. MinCell steht für „mineralische Zellen“. Das Unternehmen stellt Schaumglas her. Dieses Produkt gibt es in Form von Schotter und Platten. Bei MinCell wird es vollständig aus Altglas produziert.
Wirtschaftsingenieur Dvorak und sein Geschäftspartner Joachim Koch haben den Mineralschaum nicht erfunden – aber sie wollen ihm zum Durchbruch verhelfen. Beide haben sich schon lange vor der Firmengründung damit beschäftigt. „Da wir uns bei unserem früheren Arbeitgeber nicht verwirklichen konnten, haben wir Ende 2010 ein eigenes Unternehmen gestartet“, so Koch. Ihre Idee: Das Verfahren so optimieren, dass es gute Qualität bei deutlich niedrigeren Preis ermöglicht.
Geheimnisvoller Zusatzstoff
Rund 1350 Versuche folgten. Es wurde mit unterschiedlichen Glaspulvern, chemischen Zusatzstoffen, Aktivatoren und Temperaturverläufen experimentiert. Das Prinzip aber ist immer das gleiche: Zunächst wird das Altglas fein gemahlen. Mit Additiven versetzt kommt das Mehl in einen Tunnelofen, wo es bei Temperaturen um die 900 °C wie ein Kuchen aufgeht. Dabei bilden sich im Material Gasblasen. Der Endlosstrang wird dann kontrolliert abgekühlt. „Je nachdem, wie man die Abkühlung steuert, bekommt man Schotter oder Platten heraus“, so Dvorak.
„Wir konnten die Eigenschaften des Endprodukts durch einen gewissen Zusatzstoff verbessern, den wir nicht preisgeben können“, erklärt Koch. Das Material werde großporiger geschäumt, habe dennoch die gleiche Druckfestigkeit und eine geringere Wärmeleitfähigkeit. Die Qualität des Schotters sei zudem durch die geheime Zutat beständiger als bisher üblich. Auch die Kosten wurden gesenkt: Für die Herstellung sei weniger Altglas und Energie nötig.
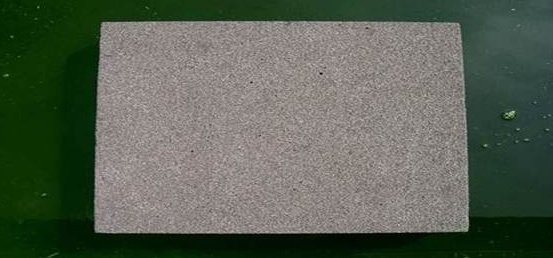
Viele Versuche und ein geheimnisvoller Zusatzstoff waren nötig, bis MinCell mit den Schaumglasplatten zufrieden war.
Quelle: MinCell
Um Energie zu sparen, wurden der Prozessablauf und die Konstruktion des Ofens verändert. Das Glasmehl wird z. B. nicht in Formen gefüllt, sondern zu einem Endlosstrang verarbeitet. Das erlaubt, größere Platten herzustellen. Und vor allem müssen keine massiven Stahlformen mehr erhitzt und danach gekühlt werden. „Bisher gehen je nach Herstellungsverfahren zwischen 40 % und 70 % der Energie nicht ins Produkt. Das haben wir auf etwa 20 % reduziert“, sagt der für die Technologie zuständige Dvorak.
Für den Bau der Produktionsanlage müssen zehn Millionen Euro beschafft werden
Die Gründer haben mit rund 750 000 € die Entwicklung betrieben und Versuchsserien gefahren. Das Startkapital kam aus drei Quellen: dem eigenen Sparschwein, dem Hightech-Gründerfonds und dem Europäischen Fonds für regionale Entwicklung. Nun fehlen den Gründern 10 Mio. €, um ihre Produktionsanlage zu bauen. Denn schon im nächsten Jahr wollen sie auf den Markt. Zunächst im deutschsprachigen Raum, später in Westeuropa, möglicherweise auch in den USA und Russland. „Innerhalb von fünf Jahren wollen wir mindestens einen weiteren Produktionsstandort eröffnen“, sagen sie.
Genug Kunden für alle Schaumglas-Schotter-Produzenten
Beim Schaumglas-Schotter gibt es bereits mehrere Produzenten. MinCell will sein Produkt auf gleichem Preisniveau, aber mit besserer Qualität anbieten. Platten dagegen stellt bisher fast ausschließlich die US-Firma Foamglas her. Diese seien sehr hochwertig und kosteten zwischen 300 € und 1200 € pro m3. Dvorak und Koch wollen deutlich günstiger sein. Die Jungunternehmer sind jedoch nicht auf einen harten Verdrängungswettbewerb aus. Vielmehr sind sie überzeugt, dass es genug Kunden für alle gebe. Koch: „Einschlägige Produkte sind im Sommer, wenn die Hauptsaison auf dem Bau ist, stets ausverkauft. Der Markt hat erkannt, dass Schaumglas etwas Tolles ist.“
Auch im Straßenbau und in der Gartenarchitektur einsetzbar
Bisher wird es hauptsächlich zum Dämmen von Bodenplatten und Flachdächern verwendet. Weitere Anwendungen finden sich im Straßen- und Brückenbau bei problematischen Böden, z. B. im Moor. Da der leichte Baustoff unter der Fahrbahn für Auftrieb sorgt, setzt sich die Straße nicht. In solchen Fällen wurde bisher Styropor oder Blähton genommen. Schaumglas war dafür zu teuer und die Produktionskapazitäten reichten nicht aus. Koch und Dvorak sind jedoch zuversichtlich, dass es ihnen gelingen wird, die Klassiker zu ersetzen. Schaumglas-Schotter sei leichter als Blähton sowie fester und langlebiger als Styropor. Neue Gestaltungsmöglichkeiten eröffne der Schotter auch in der Garten- und Landschaftsarchitektur.
Keine Wärmebrücken mehr
„Als Dämmstoff für die Gebäudesanierung können wir preislich nicht mit Styropor konkurrieren. Es sind allerdings völlig verschiedene Produkte. Schaumglas würde noch in 50 Jahren nachhaltig dämmen und genauso aussehen“, betonen sie. Wenn es aber um einen Neubau ginge, könne die Schaumglas-Platte durchaus mitziehen. „Materialien, die gleichzeitig tragen und dämmen, gibt es wahrlich nicht viele“, sagt Dvorak: „Man kann auch schneller bauen, wenn die Wände aus nur einer Schicht bestehen.“ MinCell sei bereits in der Lage, Platten in allen Stärken mit einer Fläche von bis 2,5 m x 3 m zu produzieren. Die Gründer haben sich vorgenommen, in den ersten fünf Jahren nach Produktionsbeginn monolithische Wände aus Schaumglas erzeugen zu können. Ihr mittelfristiges Ziel: Ein Passiv-Haus, das von der Bodenplatte über die Wände bis zur Dachkonstruktion aus Glasschaum besteht. In so einem Haus, schwärmen die beiden, gebe es keine Wärmebrücken mehr.
Ein Beitrag von: