Schutzhelm zeichnet Vibrationen von Baumaschinen auf
Wer am Steuer von schweren Baufahrzeugen sitzt, ist heftigen Schwingungen ausgesetzt. Die Belastung birgt auf Dauer Gesundheitsrisiken. Ein neuartiger Schutzhelm mit Schwingungssensor könnte für mehr Arbeitsschutz in der Baubranche sorgen.
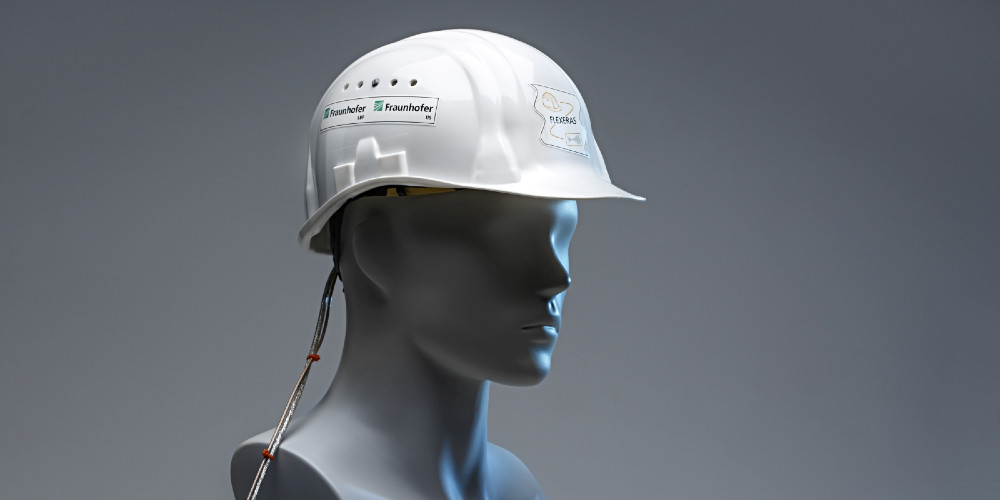
Ein Sensor kann vor Gesundheitsschäden durch die schweren Schwingungen schützen, denen Menschen in Baufahrzeugen ausgesetzt sind.
Foto: © Ursula Raapke / Fraunhofer LBF
Wer im Job Planierraupe, Radlader, Bagger oder Traktor fährt, kennt das Gefühl, wenn die Vibrationen den ganzen Körper durchrütteln. Die schweren Fahrzeuge erzeugen im Betrieb niederfrequente Schwingungen, die auf Dauer Gefahren bergen. Dazu zählen Schäden an der Wirbelsäule, am Sehvermögen und am Gehirn. In Arbeitsschutzverordnungen spielt das Ausmaß der Belastung durch Vibrationen deshalb eine große Rolle.
Aber was könnte betroffene Beschäftigte vor Risiken bewahren? Eine mögliche Lösung haben haben Forscherinnen und Forscher am Fraunhofer-Institut für Betriebsfestigkeit und Systemzuverlässigkeit LBF in Darmstadt gefunden. Im Rahmen des Projektes „Flexeras“ hat das Team einen Schutzhelm mit Beschleunigungssensor entwickelt, der die Schwingungen erfasst, die durch die Baumaschine auf den Körper treffen. Die Analyse übernimmt ein externer Rechner. Wie belastet der Fahrzeugführer oder die Fahrzeugführerin durch die Vibrationen ist, zeigt der Computer in Echtzeit mit einer Visualisierung an, sodass augenblicklich klar ist: Jetzt muss etwas passieren.
Laut Björn Seipel, Experte für Elektromechanik und Automatisierung am Fraunhofer LBF, erreichen Ganzkörperschwingungen, denen Führerende von Baumaschinen ausgesetzt sind, durchschnittlich Beschleunigungswerte von 0,2 Meter pro Quadratsekdunde (m/s²) bis 1,5 m/s², in Belastungsspitzen deutlich höhere. „Mit unserer Helm-Sensorik ist es auf einfache Art möglich, die Vibrationsbelastung im täglichen Betrieb exakt zu messen“, so Seipel. „Auf der Basis lässt sich der Gesundheitsschutz deutlich verbessern.“
Sensor wandelt Beschleunigung in Spannung um
So funktioniert der Schutzhelm mit Messfunktion: Im seinem Inneren ist eine flexible Polypropylen-Folie in einen Befestigungsriemen an der Kopfoberseite eingearbeitet. Die Folie fungiert als Sensor und ist physikalisch gesehen ein Piezo-Elektret-Wandler. Das bedeutet: Die Schwingungen, die von der Baumaschine ausgehen, treffen als Beschleunigungskräfte auf die Folie und verformen diese. Je nach Grad der Verformung generiert die Piezo-Elektret-Folie eine Spannung. Diese wiederum wird als Signal an ein Elektronikmodul weitergegeben, in dem die Signale aufbereitet, an eine am Körper des Fahrzeugführenden befestigte Sendeeinheit geleitet und schließlich an einen Rechner geschickt werden. Eine Software zeichnet die Signale auf und stellt die Vibrationen relevanter Frequenzbereiche in Echtzeit dar. „Frequenzen zwischen 4 und 6 Hertz sind beispielsweise kritisch für die Wirbelsäule, im Bereich zwischen 20 und 30 Hertz sind Kopf und Augen besonders betroffen“, erklärt Denis Becker vom Projektteam.
Unterstützung bei der Auswertung der Daten erhielt das Projektteam aus Darmstadt von Kolleginnen und Kollegen des Fraunhofer-Instituts für Integrierte Schaltungen IIS in Erlangen. Diese brachten ihre Expertise im Bereich der Datenanalyse für medizinische Sensorsysteme in das Projekt ein. So ist es nun möglich, festzustellen, in welchen Frequenzbereichen die Schwingungen besonders stark sind. Dadurch kann für jede Baumaschine eine Art individuelles Schwingungsprofil erstellt werden.
Arbeitsschutz durch Pausen oder Dämpfungselemente
Die neue Fraunhofer-Technologie könnte jetzt dazu beitragen, die Gesundheit von Personen besser zu schützen, für die die Fahren schwerer Baumaschinen zum Alltag gehört. Erkennt die Software, dass eine Belastungsgrenze erreicht ist, ist sie in der Lage, dem oder der Mitarbeitenden eine Erinnerungsnachricht zu schicken, dass es höchste Zeit für eine Pause ist.
Die Handlungsoptionen reichen noch weiter. Arbeitgeber könnten durch den Einbau zusätzlicher Dämpfung am Fahrersitz belastende Schwingungen reduzieren und dadurch für besseren Arbeitsschutz sorgen. Denkbar ist es laut dem Projektteam auch, die Empfangseinheit mit der Auswertungsprogramm in die Bordelektronik der von Baumaschinen zu integrieren. Schließlich könnte die Fraunhofer-Entwicklung dazu beitragen, dass die Schwingungen erst gar nicht so ausgeprägt auftreten, so Fraunhofer-Experte Denis Becker: „Bei der Entwicklung neuer Baumaschinen hilft die Technik, schon bei frühen Prototypen das Niveau der Vibrationen zu messen und anschließend durch gezielte Maßnahmen zu reduzieren.“
Das Fraunhofer LBF brachte bei Flexeras sein Know-how im Bereich von Wandlersystemen ein. Die Expertinnen und Experten entwickeln unter anderem Konzepte und Ideen, um vorhandene Wandlersysteme wie etwa Piezo-Elektret-Folien in neue Anwendungen zu überführen.
Arbeitsschutz ist auch ein Kostenfaktor
In der Baubranche ist das Interesse laut Fraunhofer groß. Das erstaunt nicht: Wie in jeder anderen Branche bedeuten kranke Mitarbeitende für eine Firma schlicht Kosten. Zudem haben die Unternehmen mit Blick auf den Arbeitsschutz eine Fürsorgepflicht für ihr Personal. Aber auch Berufsgenossenschaften könnten die Belastung von Beschäftigten im Bau künftig differenzierter als bisher bewerten – mithilfe der generierten Daten. Weitere Anwendungen seien denkbar, sagt Fraunhofer-Experte Björn Seipel: „Die Technik eignet sich generell für alle Menschen und Berufsgruppen, die häufig hohen biomechanischen Belastungen ausgesetzt sind.“
Interessierte können den neuen Sensor-Schutzhelm in Kürze persönlich in Augenschein nehmen: auf der Hannover-Messe (22. Bis 26. April 2024), am Gemeinschaftsstand der Fraunhofer-Gesellschaft.
Ein Beitrag von: