Batterierecycling: Wie Akkus von Elektroautos recycelt werden
Wie werden Batterien aus Elektroautos recycelt? Wir stellen Unternehmen vor, die Akkus aus E-Autos recyceln. Jedes nutzt ein anderes Verfahren zum Batterierecycling.
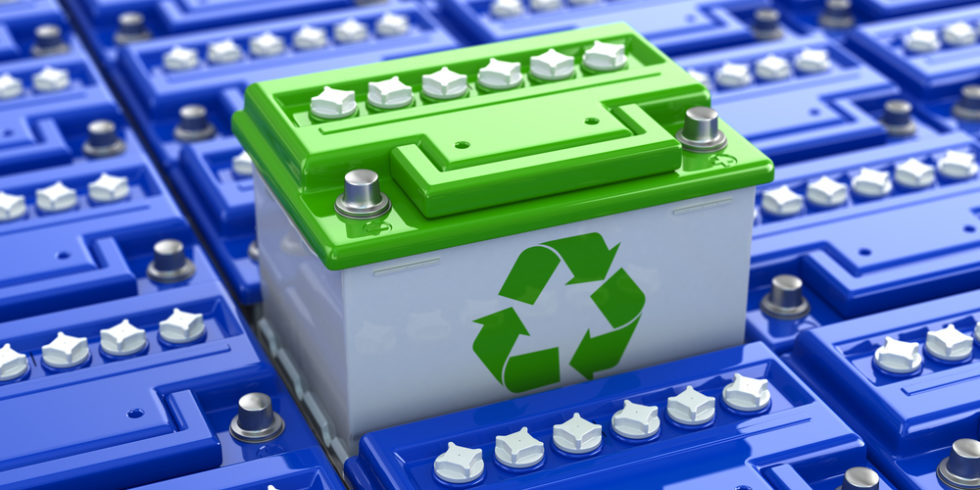
Foto: panthermedia.net/maxxyustas
Batteriebetriebene Elektroautos stehen in der Kritik. Nicht nur wegen ihrer für viele Menschen mangelhaften Reichweite, sondern vor allem wegen ihrer zweifelhaften Umweltbilanz. Die verbauten Akkus versammeln in ihrem Inneren nämlich eine Vielzahl wichtiger und seltener Rohstoffe, die am Ende des Lebenszyklus meist nicht weiter genutzt werden. Schuld sind die im Aufbau befindlichen Recyclingverfahren und der in den Kinderschuhen verweilende Rohstoffkreislauf. Doch das wird nicht so bleiben. Weltweit arbeiten Unternehmen und Forschungseinrichtungen daran, ausgediente Akkus aus Elektroautos zu recyceln und die Rohstoffe wieder nutzbar zu machen. Wir stellen einige Ansätze vor.
Umicore verbrennt die Akkus
Das belgische Unternehmen Umicore ist Marktführer des Batterierecyclings der bisher gängigsten Art, der thermischen Aufschmelzung. Dabei wird der Akku zunächst verbrannt und schließlich zermahlen. So können Kobalt, Nickel und das Kupfer der Batterie wiedergewonnen werden. Nicht wiederzuverwerten sind jedoch die Rohstoffe Lithium, Graphit, Aluminium sowie der Elektrolyt. All diese Rohstoffe können dem Kreislauf nicht wieder zugeführt werden. Audi ist im vergangenen Jahr eine Forschungskooperation mit Umicore eingegangen, um einen geschlossenen Kreislauf für Hochvoltbatterien zu entwickeln. Dabei soll die Wiederverwertung von alten Akkumaterialen im Vordergrund stehen. Ergebnisse liegen noch keine vor.
Duesenfeld zeigt, wie man Akkus verschrottet
Das deutsche Chemieunternehmen Duesenfeld hat derweil einen Schredder unter Stickstoff gesetzt und zerlegt darin die ansonsten leicht entzündliche Lithium-Ionen-Batterie bis nur noch eines bleibt: Geschreddertes und Elektrolyt. Aus dem geschredderten Material gewinnt Duesenfeld die einstigen Rohstoffe Graphit, Mangan, Nickel, Kobalt und Lithium. Sie gehen in die (Re-)Produktion, um daraus neue Antriebsakkus zu bauen. Das Verfahren wird im folgenden Video erklärt. Der Erfolg:
- 96 % aller Batteriebestandteile werden so einem neuen Kreislauf zugeführt
- der CO2-Fußabdruck bei der Produktion neuer Akkus verringert sich um 40 % im Vergleich zur Neuproduktion
Fraunhofer IWKS separiert Funktionsmaterialien
Die Fraunhofer-Einrichtung für Wertstoffkreisläufe und Ressourcenstrategie IWKS möchte nicht nur einzelne Metalle oder Rohstoffe zurückgewinnen, sondern zusammenhängende Funktionsmaterialien, also Werkstoffe. Dafür setzt das IWKS auf einen mechanischen Prozess, der wenig Energie verbraucht. Bei der ektrohydraulischen Zerkleinerung kommen kontrollierte Schockwellen zum Einsatz, die die gängigsten aller Batterien zerlegen können, nämlich die Lithium-Ionen-Batterien.
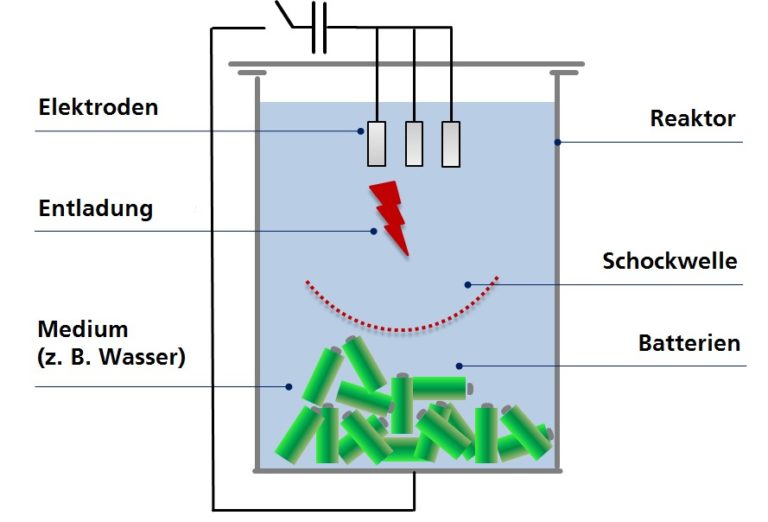
Foto: Fraunhofer IWKS
Der Prozess der elektrohydraulischen Zerkleinerung sieht wie folgt aus. Zunächst gehen die Batteriezellen in Wasser schwimmen. Durch Entladung provoziert die Anlage eine Schockwelle, die einzelne Bestandteile der Zellen abtrennt. Das System nutzt dafür bestehende Schwachstellen in Materialverbünden. Um ein Kilo Batterien zu zerlegen, benötigt die elektrohydraulische Zerkleinerungsanlage rund 1,5 Kilowattstunden Strom. Nach rund 2.000 bis 5.000 Pulsen ist eine handelsübliche Rundzelle in ihre Einzelteile zerlegt. Gehäuseteile, Elektrodenfolien, Separatoren und natürlich Aktivmaterialien der Elektroden (Nickel-Kobalt-Mangan-Oxid) lassen sich nun mit Trennverfahren wie Sieben oder Flotation separieren und wiederverwenden. Die chemisch aktiven Substanzen nach der Methode des IKWS können, anders als einzelne Elemente, direkt wieder eingesetzt werden.
Parallel dazu arbeitet das Fraunhofer IWKS an der Weiterentwicklung seines Recycling-Verfahrens, um auch alternative Akku-Technologien, etwa Lithium-Schwefel-Akkus oder Festkörperakkus auf Lithiumbasis wirtschaftlich recyceln zu können.
PBT setzt auf Reinigung statt Trennung der Metalle
Pure Battery Technologies (PBT) aus Brisbane hat gemeinsam mit der University of Queensland zwei umweltfreundliche, kostengünstige Prozesse zur Herstellung von nickelbasierten aktiven Vorläuferkathodenmaterial (pCAM) für EV-Batterien zur industriellen Reife entwickelt. Diese Prozesse sind sowohl für die Neuproduktion von Kathodenmaterial geeignet als auch für das Recycling der Black Mass, also dem aus alten Batterien zurückgewonnenen Kathodenabfall. Die Kombination des Selective Acid Leaching (SAL) und Combined Leaching (CL) produziert pCAM effizienter und kostengünstiger, mit wesentlich niedrigerem Energieverbrauch und mit erheblich geringerer CO2-Belastung.
Wie bereits erwähnt, eignet sich die Technologie zum Recycling, aber auch für die Verarbeitung von Rohstoffen. Der Unterschied zu anderen Herstellern liegt in der Herstellung der Batteriematerialien. Mischmetall-Legierungen mit Nickel, Kobalt und Mangan kommen im Erdreich vor. Diese werden konzentriert. Im Raffinerieprozess zum Batteriematerial fokussiert sich das SAL-Verfahren von PBT auf das Absondern der Unreinheiten anstatt auf die individuelle Trennung der einzelnen Metalle. Mit anderen Worten: Die drei Metalle werden nicht voneinander getrennt und anschließend wieder zusammengefügt, sondern nur von Unreinheiten befreit. Die Energie- und CO2-intensive Zuführung von Wärme und Druck wird damit reduziert. Das gleiche gilt für Recycling der sogenannten Black Mass.
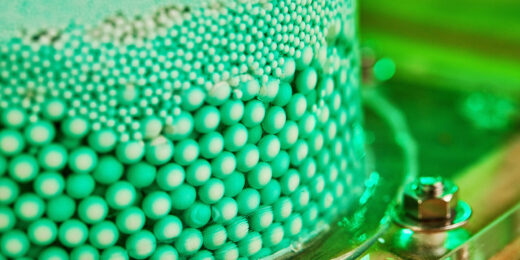
Nahaufnahme der Ionenaustauscher-Säule.
Foto: PBT
„Bei K&E in Hagen können wir sofort im industriellen Maßstab Minenmaterial als auch Recyclingmaterial zu pCAM verarbeiten. Dahin sind wir durch Cronimet gelangt, Cronimet in Karlsruhe ist weltweit führend in der Verarbeitung von Metallschrott. Sie haben die Vorteile unserer Technologie sofort erkannt und sich an PBT als Gesellschafterin beteiligt und dann Wege mit aufgezeigt und angebahnt“, erklärte Björn Zikarsky, CEO der Pure Battery Technologies (PBT).
„Die EU-Richtlinien schreiben den geschlossenen Kreislauf vor. Unsere Technologien liefern dazu einen wertvollen Beitrag. Wir können die Black Mass aus allen Quellen verarbeiten: gebrauchten Batterien und Abfall aus der Batterieproduktion, zudem Metallschrotte aus der Industrieproduktion und Stahlwerken“, ergänzte Björn Zikarsky.
Empa sucht den idealen Recyclingprozess für Akkus
In der Schweiz suchen Rolf Widmer und sein Team der Eidgenössischen Materialprüfungs- und Forschungsanstalt, kurz Empa, nach dem perfekten Verfahren. Gemeinsam mit der Stiftung Autorecycling der Schweizer Automobilimporteure wollen sie die verschiedenen Formen des Batterierecyclings, dessen Kosten, Erträge und ökologischen Impact untersuchen. Dabei werden sie Umicore und Duesenfeld unter die Lupe nehmen, aber auch das Verfahren der Schweizer Batrec Industrie AG. Sie führt zunächst eine thermische Behandlung der Akkus durch, bevor sie die Bestandteile einer Abgas-Nass- sowie Abgas-Trockenreinigung unterziehen.
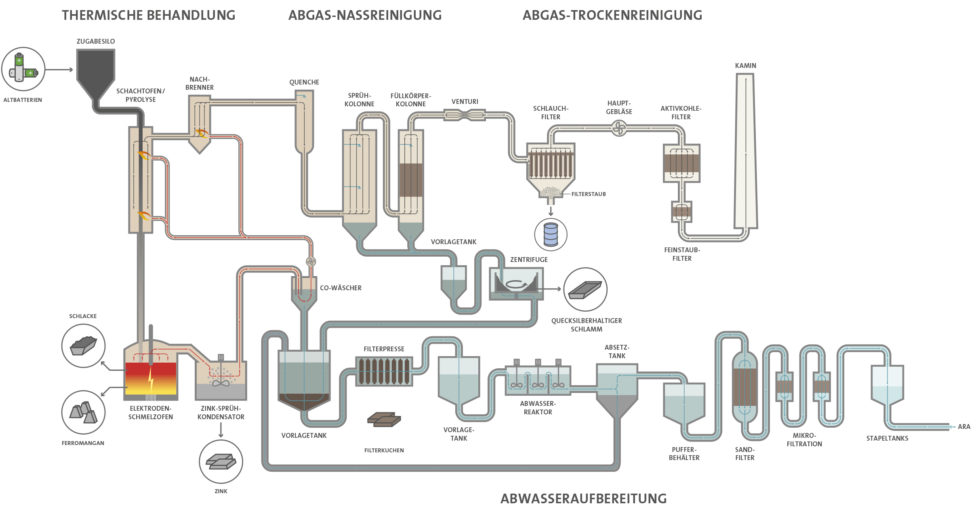
Der Batrec-Verfahren des Batterierecyclings.
Foto: Batrec Industrie AG
Am Ende der Empa-Untersuchungen soll eine Strategie stehen, wie Antriebsakkus idealerweise zu entsorgen wären.
Second Life für ausrangierte Akkus
Wenn Akkus nach 8 bis 10 Jahren ihren Zenit in Elektroautos erreicht haben und ausgebaut werden müssen, gibt es noch eine andere Möglichkeit als sie direkt zu zerlegen und die Bestandteile zu recyceln. Immerhin sprechen wir von einer großen Anzahl von Akkus: Das IWKS rechnet damit, dass allein in den USA bis 2020 rund 500 Millionen Lithium-Ionen-Batteriezellen entsorgt werden müssen. Ein Teil davon ist sehr wohl noch in der Lage, Leistung zu bringen, wenn auch nicht mehr genug für die batteriebetriebene Mobilität. Anstatt sie zu recyceln wäre ein alternativer Einsatz denkbar, etwa als stationärer Energiespeicher.
Dieses Konzept des second life verfolgen etwa VW, Daimler, Audi und BMW. Die ausgedienten Akkus mit reduzierter Ladekapazität sollen als Powerbank weiterverwendet werden. So soll die mobile Schnellladesäule von VW ab 2020 in Serie hergestellt werden.
Lesen Sie auch:
Recycling für Mobilgeräte – es gibt ein Leben nach dem Smartphone-Tod
Magnete trennen Gemische von Seltenerdmetallen
Können Lebewesen unseren Plastikmüll eliminieren? Das hat ingenieur.de Wolfgang Streit, Professor für Allgemeine Mikrobiologie und Biotechnologie an der Universität Hamburg, gefragt.
Empfehlungen zum Schutz vor Ressourcenknappheit gibt Matthias Buchert vom Öko-Institut im Artikel „Verschärfen Elektroautos den Kampf um Rohstoffe?“
Ein Beitrag von: