Dank Lasertechnologie 20 % leichtere Karosserien aus dünnerem Stahl
Mit einer neuen Lasertechnik aus Dresden könnten Autokarosserien künftig um bis zu 20 Prozent abspecken: Forschern ist es gelungen, aus dünnen und deshalb leichten Stahlblechen dennoch sehr crashstabile Bauteile zu fertigen. Der Trick: Per Laserbehandlung entstehen im Stahl verfestigte Bereiche.
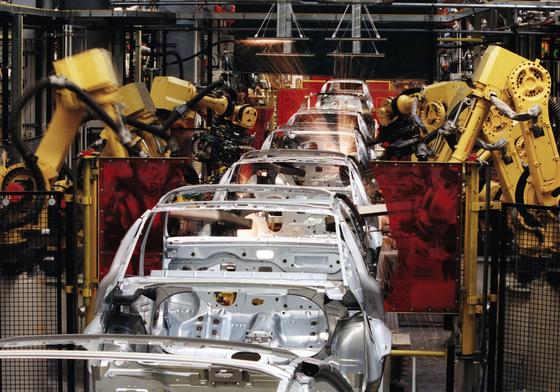
Karosserie-Fertigung im Opel-Werk in Rüsselsheim: Dresdner Forscher haben nun eine neue Technik entwickelt, um Karosserien aus dünneren Blechen mit gleicher Stabilität zu bauen. Das Gesichtsersparnis soll bei 20 Prozent liegen.
Foto: Opel
In den vergangenen Jahren hielt in der Automobilbranche der Trend an, immer schwerere Autos zu bauen – mit dem Fokus auf Leistung, Komfort und Sicherheit. Das Problem: Moderne Fahrzeuge, im Schnitt über 500 Kilo wuchtiger als ihre Vorfahren um 1980, haben einen entsprechend höheren Kraftstoffverbrauch und Kohlendioxid-Ausstoß.
Eine für die EU nicht hinnehmbare Entwicklung. Deswegen zwingt sie die Automobilindustrie mit immer schärferen Emissionswerten, der Kraftstoffverbrauch und damit den CO2-Ausstoß der Neuwagen zu senken.
Um beim Abnehmen auf begehrte Zusatzausstattungen wie Klimaanlage, Zusatz-Airbags und elektrische Sitzverstellungen nicht verzichten zu müssen, setzen Konstrukteure vor allem bei der Karosserie an, um Gewicht zu sparen. Doch hier stoßen sie bislang schnell an eine Grenze: Denn Karosserien sind in der Regel homogen gebaut. Die Wandstärke des Blechs richtet sich dabei nach den Stellen mit der höchsten lokalen Belastung. Dadurch sind weniger belastete Bereiche häufig überdimensioniert und unnötig schwer.
Revolution in der Leichtbauweise: Laser verfestigt Stahlblech an Belastungsstellen
Forscher des Fraunhofer Instituts für Werkstoff- und Strahltechnik IWS in Dresden haben jetzt eine Leichtbautechnologie entwickelt, mit der sich die Fahrzeugmasse senken lässt: Zum Einsatz kommen dabei kostengünstige, niedrigfeste Stahlbleche mit minimierter Wanddicke. Diese lassen sich mit Hilfe der lokalen Laserverfestigung an stark beanspruchten Stellen verfestigen, so dass sie bei Crashbelastungen einen höheren Deformationswiderstand haben.
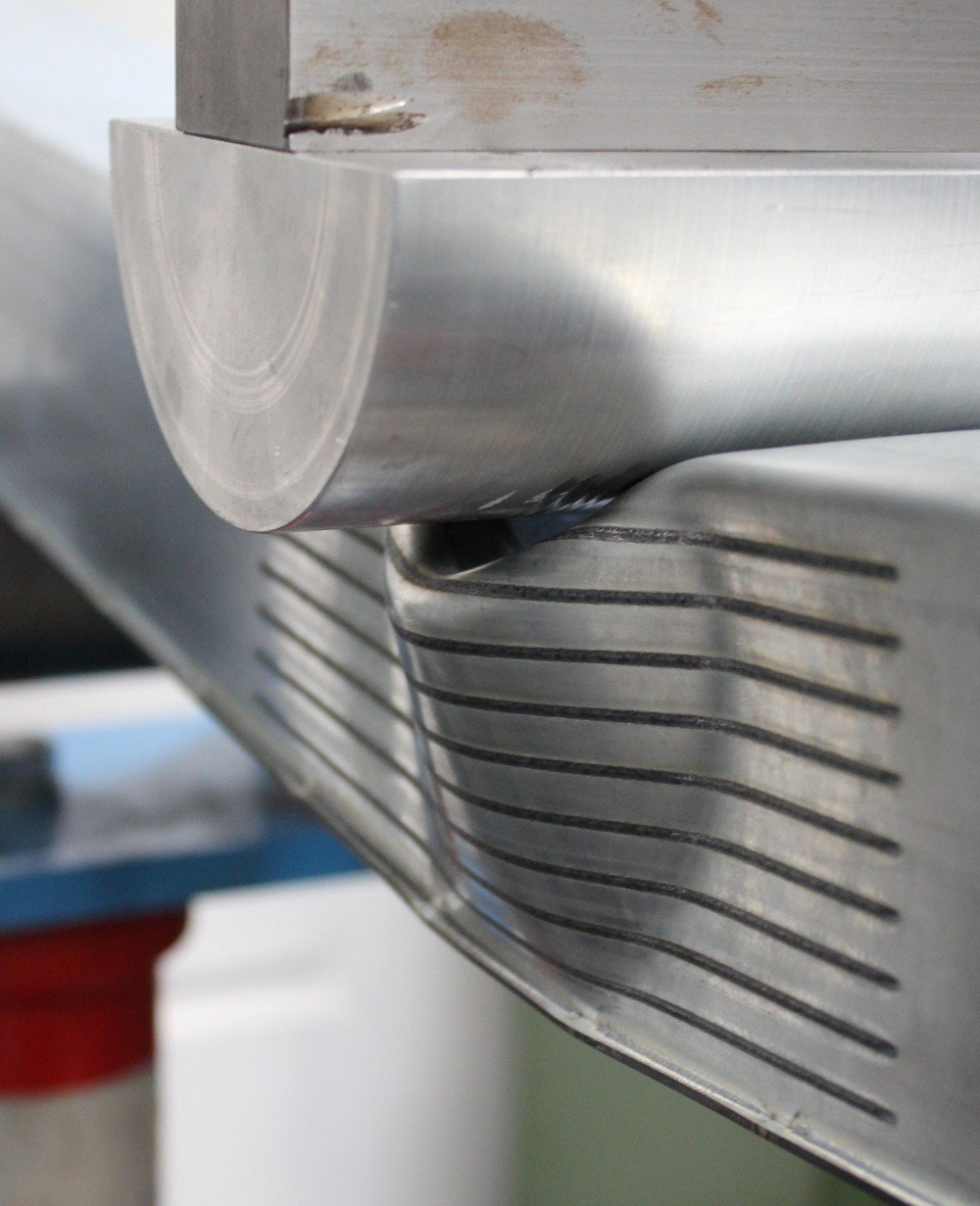
Mit Lasertechnik ist es Fraunhofer-Forschern in Dresden gelungen, auch Karosserieteile aus dünnen Stahlblechen mit sehr guten Crasheigenschaften herzustellen. Im Bild ein Karosserieteil im Crashtest.
Quelle: Fraunhofer IWS
Die Forscher führen einen fokussierten Laserstrahl über die Oberfläche des unbehandelten Blechs. Die Zonen erwärmen sich und erstarren anschließend. „Wir erreichen Festigkeiten von bis zu 1500 Megapascal. Das entspricht etwa dem zweifachen des unverfestigten Grundwerkstoffs“, erklärt Markus Wagner, Wissenschaftler am IWS. Vor allem Stoßträger, B-Säule und Versteifungsprofile ließen sich so gewichts- und belastungsoptimiert gestalten. Wagner ist überzeugt: „Sicherheit und Leichtbau müssen kein Widerspruch sein.“
100 Prozent bessere Crashperformance bei 20 Prozent leichteren Bauteilen
Gleichzeitig können die Forscher die Position der ersten plastischen Deformation vorgeben und somit das Versagensverhalten der Bauteile beeinflussen. Damit dies gelingt, ermitteln sie am Computer optimale Lage und Geometrie der Verfestigungsspuren des Lasers und bestimmen, ob sie spitz, schräg oder längs verlaufen sollen. Wagner: „Mit unseren Simulationen sind wir in der Lage, Praxistests abzubilden. Versuch und Simulation weichen nur um wenige Millimeter voneinander ab.“
Mit einer solchen Simulation ließ sich beispielsweise ein crashoptimiertes Spurdesign für eine Biegebelastung entwickeln, die beim Frontalaufprall auf einen Baum auftritt. Der Laser übertrug anschließend das Spurdesign auf das echte Bauteil. „Wir konnten die Durchbiegung eines lokal laserverfestigten Rohrprofils im Vergleich zur Referenz halbieren – und das, obwohl wir nur drei Prozent des Bauteilvolumens lokal verfestigt haben. Die Crashperformance wurde also verdoppelt.“
Schon viele Crashprofile erprobt
Durch die neue Gestaltung lässt sich die Wandstärke deutlich reduzieren. Automobilhersteller können somit bis zu 20 Prozent Bauteilgewicht einsparen, ohne dabei die Crashsicherheit aus den Augen zu verlieren. Im Kundenauftrag haben die Forscher des IWS das Verfahren bereits auf diverse Crashprofile und Sitzkomponenten angewendet. Im nächsten Schritt wollen Wagner und seine Kollegen die Technologie perfektionieren, indem sie das Optimieren der Spurgeometrie automatisieren.
Ein Beitrag von: