Erneuerbare Energien inspirieren Leistungselektronik
Immer leistungsfähigere Windturbinen und Solaranlagen sowie in ein Smart Grid zu integrierende Elektroautos stellen neue und hohe Anforderungen an die verbaute Leistungselektronik. Die Branche reagiert mit neuen Ideen, wie sich auf der Hannover Messe vom 23. bis 27. April 2012 im Rahmen der Messen „Energy“ und „MobiliTec“ zeigen wird. Einen ersten Vorgeschmack gab es auf einem Expertenworkshop der Branche vor Ostern in Frankfurt/Main.
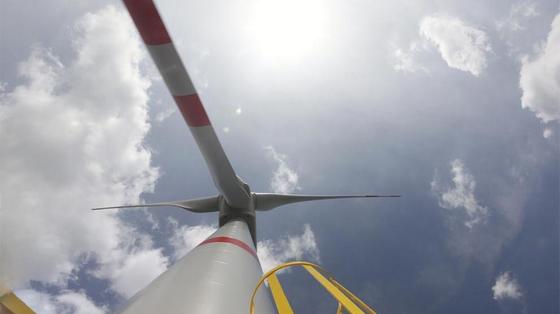
Windturbinen werden immer leistungsfähiger.
Foto: BARD-Gruppe
Immer leistungsstärker werden Windkraft- und Solarstromanlagen, immer mehr von ihnen gibt es – so will es die deutsche Energiewende. „Das bedeutet neue, erhöhte Anforderungen an die Leistungselektronik, an die sich die Hersteller von Systemen und Bauelementen anpassen müssen“, betonte Norbert Graß, einer der beiden Leiter des Instituts für leistungselektronische Systeme ELSYS an der Georg-Simon-Ohm-Hochschule Nürnberg.
Hochstrom-Leiterplatten: Höhere Stromtragfähigkeit für die Leistungselektronik
Tatsächlich, so wurde vor Ostern auf einem Expertenworkshop in Frankfurt am Main deutlich, ist die Branche um neue Ideen nicht verlegen. Ein Beispiel dafür sind neuartige Hochstrom-Leiterplatten. Zwischen üblichen, kunststoffbasierten Leiterplattenmaterialien sind hier 1 mm bis 3 mm dicke Kupferadern eingebettet. Deren Kontakte können direkt an die Oberfläche geführt werden. So lässt sich eine höhere Stromtragfähigkeit erreichen.
„Der Einsatzbereich dieser Leiterplatten fängt bei 150 A an und reicht derzeit bis 1000 A. Sie eignen sich für Anwendungen mit wenig Platz bei viel Strom und Abwärme“, erklärt Thomas Mang, Geschäftsführer der Pronova Leistungselektronik. Er hält die Patente für die Technologie.
Weiterer Vorteil des neuen Designs: Steuer- und Leistungselektronik können direkt auf die Kupferkontakte der Leiterplatte aufmontiert werden. Außerdem lassen sich die hohen Ströme mit den aus der Leiterplatte herausgeführten Kupferadern oder -bändern beispielsweise um Ecken und Kanten leiten. Auch flexible Leiterplatten sind möglich.
„Wir können den Platzbedarf und die Kosten für die realisierten Funktionen oft um etwa die Hälfte verringern“, freut sich Mang. Aus der Solarbranche gibt es bereits Interesse: So soll der Weltmarktführer bei Wechselrichtern, SMA, das kupferbasierte Hochstromdesign testen.
Infineon: Breite Bandleiter für höhrere Stromfestigkeit
Ähnliche Wege geht Infineon: Statt einzelner Leiterbahnen zu jedem Bauelementekontakt will der Hersteller vor allem breite Bandleiter einsetzen, mit denen die nebeneinander befindlichen Bauelemente sämtlich verbunden sind. Der Lohn ist eine höhere Stromfestigkeit bei gleichzeitiger Platzersparnis.
Auch Infineon setzt auf mehr Kupfer, obwohl dessen Preis vorhersehbar ansteigen wird. „Wir haben einfach keine bezahlbare Alternative dazu, die hohen Leistungsanforderungen zu erfüllen“, erklärt Martin Schulz, Manager Application Engineering Industrial Power bei Infineon. Schließlich gehe es bei Offshore-Windturbinen mittlerweile um Standzeiten von 25 bis 30 Jahren.
So befestigt der Hersteller bei einigen neuen Produkten Bauelemente mit Kupferdraht auf der Leiterplattenoberfläche, die ebenfalls mit Kupfer statt Silber kaschiert ist. Gelötet wird mit Diffusionsverfahren, die Zinn und Kupfer intensiver miteinander verbinden als konventionelles Löten.
Bei den Bauelementen werden wohl IGBTs (Insulated Gate Bipolar Transistors) in Siliciumcarbid(SiC)-Technologie zukünftig in vielen Wechselrichtern und anderen Leistungselektronik-Topologien ältere Bauelementetypen ersetzen. So will der US-Halbleiterspezialist Fairchild Semiconductor noch in diesem Jahr eine Serie von SiC-IGBTs auf den Markt bringen, die unter anderem auf die wachsenden Ansprüche der Erneuerbaren-Branche zugeschnitten sind.
Sie können hohe Stromdichten sowie Temperaturen bis 175 °C verkraften und haben nur geringe Schaltverluste. „Zunächst unterstützen wir 1200 V Spannung, aber es sind durchaus 1700 V möglich“, sagt Martin Haaf, Technical Marketing Manager bei Fairchild Semiconductor. Das bedeutet mehr Abwärme, die zuverlässig abgeführt werden muss.
Leistungselektronik: Neue Lösungen für Wärmeleitpaste
„Die Komponentenhersteller schöpfen wegen des Sparzwangs beim Design die Toleranzen für die Genauigkeit der Oberflächen bis zum Rand aus. Wärmeleitpaste schafft deshalb keine ausreichende Kontaktfläche mehr, und so braucht man neue Lösungen“, erklärt Wolfgang Reitberger, Geschäftsführer von Kunze Folien. Das Unternehmen entwickelt maßgeschneiderte Wärmeleitfolien für die Branche.
Mal wird eine wärmeleitwachsbeschichtete Polyimidfolie genutzt, die bei der ersten Erhitzung die Kontaktflächen lückenlos benetzt und so für zuverlässige Hitzeabfuhr sorgt. Mal ist eine besonders hohe Durchschlagfestigkeit nötig – verwendet wird dafür millimeterdickes Softsilikon.
In Wechselrichtern mit besonders leistungsfähigen, kleinen Siliziumcarbid-Schaltkreisen muss die Abwärme nicht nur von oben nach unten abfließen, sondern sich auch von der kleinen Schaltkreis- auf die viel größere Kühlkörperfläche umverteilen. Die Lösung: Karbonfolie mit einem Phasenwechselmaterial.
Aber das ist nicht der einzige Weg, lästige Wärme wegzubringen: Infineon etwa ersetzt solche Zwischenmaterialien komplett durch einen in den Schaltungsunterbau integrierten Kühler aus Aluminiumnitrit.
Ein Beitrag von: