Feine Strukturen für den 5G-Mobilfunk
Die klassische Dickschichttechnik zur Herstellung von Leiterzügen stößt mehr und mehr an ihre Grenzen, denn Firmen benötigen eine höhere Auflösung. Neue Dickschichtpasten und photolithografische Verfahren verschieben die Grenzen nach unten.
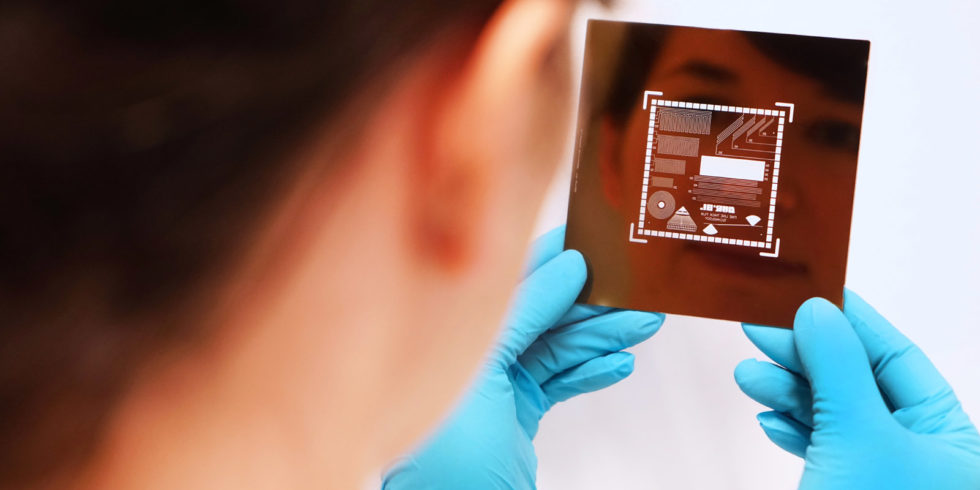
Maske für die Photolithografie, um feine Strukturen im Druckverfahren herzustellen.
Foto: Fraunhofer IKTS
Mobilfunk der fünften Generation (5G) soll Daten fast völlig ohne Verzögerung übertragen, etwa für die Industrie 4.0 oder perspektivisch für Fahrzeuge mit hoher Autonomiestufe. Der neue Standard, er wird beispielsweise in der Schweiz und in mehreren amerikanischen Städten schon eingesetzt, ist mit Herausforderungen verbunden. Hersteller müssen bei ihrer Elektronik mit deutlich feineren Strukturen arbeiten als bisher.
Hier stoßen etablierte Verfahren wie die Dickschicht-Hybridtechnik an ihre Grenzen. Als Trägermaterial dienen Platten aus Aluminiumoxid-Keramiksubstrat oder Keramikfolien. Die Leiterbahnen werden im Siebdruckverfahren aufgebracht. Damit lassen sich Strukturen mit einer Auflösung von etwa 50 Mikrometern herstellen, aber nicht darunter. Für 5G bräuchte man jedoch 20 Mikrometer oder weniger. Wissenschaftler des Fraunhofer-Instituts für Keramische Technologien und Systeme IKTS in Dresden haben zusammen mit der britischen Firma MOZAIK jetzt eine Drucktechnologie entwickelt, um die Auflösung in der gewohnten industriellen Umgebung deutlich nach unten zu verschieben.
Mit Photo-Imgaging-Technologien die 20-Mikrometer-Grenze erreichen
Dabei kommt das etablierte Siebdruckverfahren zum Einsatz: Man presst Dickschichtpaste durch Sieböffnungen. An Stellen, die später keine Schicht tragen sollen, wird das Gewebe undurchlässig gemacht. Anschließend wird der Gegenstand getrocknet und gesintert. Aufgrund des Anstands von Drähten im Sieb stößt die Methode bei einer Auflösung von 50 Mikrometern an ihre bekannten Grenzen.
Genau hier kommt die sogenannte Photo-Imgaging-Technologie (PI) in Form zweier neuer Schritte im Verfahren hinzu. „Nachdem die Dickschichtstrukturen auf dem Substrat getrocknet sind, positionieren wir eine Photomaske mit der gewünschten Endstruktur über dem Substrat“, erklärt Kathrin Reinhardt. Sie forscht am Fraunhofer IKTS. Anschließend belichtet sie das Werkstück mit UV-Strahlung. „Dort, wo die Photomaske Strukturöffnungen aufweist, dringt das UV-Licht in die Schicht ein und härtet das darin enthaltene Polymer aus“, sagt die Wissenschaftlerin. Umgekehrt heißt das: Dort, wo die Maske die aktive Schicht verdeckt, sodass keine UV-Strahlung hindurch kommt, vernetzen sich die Polymere nicht.
Dann folgt Schritt zwei: Das Bauteil wird nasschemisch behandelt. Dabei lösen sich genau die Stellen mit nicht vernetztem Polymer heraus, der Rest bleibt unverändert. Die ursprünglich 50 Mikrometer breiten Strukturen werden durch zwei neue Schritte auf 20 Mikrometer verringert. Reinhardt: „Beide Verfahren nehmen jeweils lediglich 15 bis 30 Sekunden in Anspruch und lassen sich daher problemlos in die Fertigung integrieren.“
Dickschichtpasten: Die Mischung macht´s
Um ihr neues Verfahren in die Praxis umzusetzen, mussten die Fraunhofer-Forscher geeignete Dickschichtpasten entwickeln, die im UV-Licht zuverlässig aushärten, aber bei normalem Tageslicht stabil bleiben. Ziel war, zu vermeiden, dass entsprechende Fertigungsprozesse nur unter energiearmem Gelblicht möglich sind.
Bei Metallisierungspasten griffen die Forscher auf pulverförmige Metalle wie Silber, Gold oder Legierungen dieser Elemente zurück. Diese wurden mit dem UV-empfindlichen Polymer und mit weiteren chemischen Zusatzstoffen angerührt. Wie sich herausstellte, war das Mischungsverhältnis entscheidend. Enthielt die Paste zu viel Metall, verlief die Vernetzung des Polymers zu schleppend. Die Kunststoffmasse würde dann später im Entwicklungsschritt stärker als gewünscht weggespült. Arbeiteten die Forscher mit hohen Polymeranteilen, wurden die Strukturen zu porös.
„Wir mussten bei der Entwicklung der Pasten also zwei Parameter mehr berücksichtigen als üblich: Nicht nur die Funktionalität, sondern auch die Schritte der Belichtung und Entwicklung“, erklärt Reinhardt. Im Falle von Gold und Silber hatte sie bereits Erfolg. Derzeit laufen noch Experimente mit Platin und mit Pasten, die später für einen elektrischen Widerstand sorgen sollen.
Umsetzung mit dem industriellen Partner
„Wir können Leiterbahnen mit einer Strukturauflösung von 20 Mikrometern und kleiner herstellen“, so Reinhardt zu den bisherigen Ergebnissen. „Unser Verfahren ist massen- und industrietauglich, die Investitionskosten sind gering.“
Jetzt geht es rasch in die Anwendung. Die italienische Firma Aurel arbeitet an Produktionsanlagen, welche exakt auf Pasten aus der Fraunhofer-Forschung abgestimmt wurden. dazu gehören Hochleistungsgeräte wie LED-Belichtungs- und Sprühstrahlanlagen für unterschiedliche Kundenansprüche – von der Klein- und Großserienfertigung. Sie könne als Stand-Alone-Module oder als Teil von Fertigungsstraßen eingesetzt werden. Der Hersteller plant, unter anderem HF- und Mikrowellenmodule, Sensoren, Chipkomponenten, 3D-Stapelinterposer und Fan-Out-Substrate zu produzieren.
Mehr zum Thema 5G-Technik
Ein Beitrag von: