Nachhaltige Elektronik: Bio-Platinen aus Holzfasern
Ein Forscher der Empa beschäftigt sich seit Jahren mit nachwachsenden Rohstoffen, aus denen er elektronische Komponenten herstellt. In einem neuen internationalen Forschungsprojekt kann er seine Erkenntnisse nun einbringen und „grüne“ Elektronik vielleicht alltagstauglich gestalten.
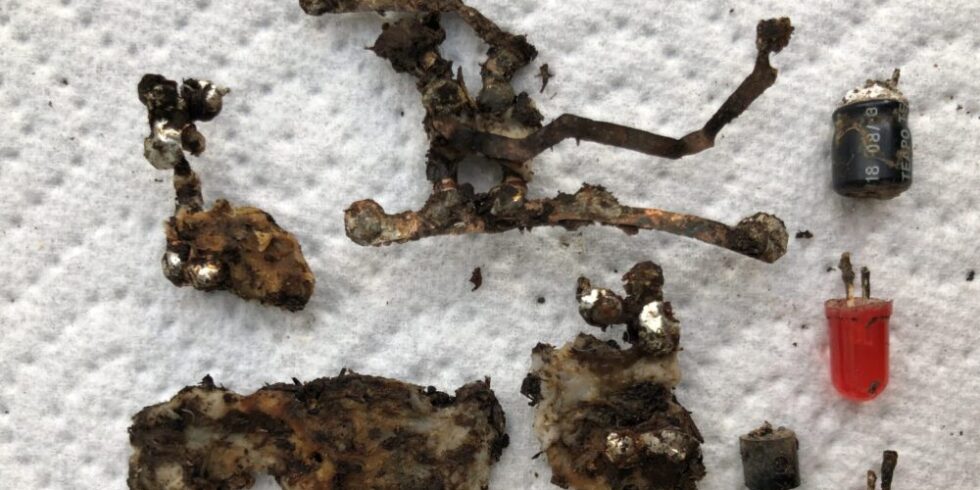
Da die Versuchsplatine aus Holzfasern besteht, wird sie nach der Kompostierung zu Biomüll.
Foto: Empa
Leiterplatten als Träger elektronischer Bauteile kommen vielfach zum Einsatz. Sie sind auch als Platinen bekannt und als erstes hat man natürlich den Computer im Kopf. Betrachtet man ihren ökologischen Fußabdruck, wird schnell klar, dass der nicht besonders vorzeigbar ist: Die meisten Leiterplatten bestehen aus Glasfasern, die zudem in Epoxidharz getränkt sind. Diese Kombination sorgt dafür, dass sie nicht recycelt werden können. Darüber hinaus sind auch noch spezielle Anlagen notwendig, damit sie überhaupt sachgemäß entsorgt werden können. Gerade in diesem Bereich steckt deshalb eine Menge Potenzial für mehr Nachhaltigkeit in der Produktion und damit einhergehend einer Dekarbonisierung der Industrie.
Nachhaltigkeit in der Industrie: Was bewegt die Unternehmen in der Zukunft?
An der Eidgenössischen Materialprüfungs- und Forschungsanstalt, Empa, befasst sich Thomas Geiger seit Jahren mit alternativen Materialien, die sich für die Elektronik eignen. Sein Fokus liegt dabei auf sogenannten Cellulosefibrillen. Das sind besonders feine Fasern, die zum Beispiel aus Holzabschnitten oder landwirtschaftlichen Abfällen hergestellt werden können. Ihr Vorteil: Sie wachsen praktisch CO2-neutral, lassen sich ohne Rückstände verbrennen und sogar kompostieren. Darüber hinaus sind wie vielseitig einsetzbar, zum Beispiel als Faserverstärkung in Pumpenmembranen.
Nachhaltige Elektronik: Bio-Platinen, die sich selbst auflösen
Der Forscher hatte bereits schon einmal den Beweis angetreten und Computerplatinen aus diesen Cellulosefasern hergestellt. Dazu vermengte er die Fasern mit Wasser. Das Ergebnis: ein dickflüssiger Schlamm, der sich in einer Spezialpresse entsprechend entwässern und verdichten ließ. Auf diese Art und Weise gelang es Geiger gemeinsam mit einer Kollegin, 20 Versuchsplatinen herzustellen. Diese mussten im Anschluss diverse Tests durchlaufen und das Forscher-Team befestigte sogar elektronische Komponenten darauf. Die Versuchsreihe war nach Angaben des Teams erfolgreich – und die aufgelöteten Bauteile lösten sich einige Wochen danach von der Bio-Platine praktisch von selbst.
Thomas Geiger hat nicht nur ökologische Platinen entwickelt, sondern auch Gehäuseteile für Computermäuse. Eigentlich hatte der Forscher gehofft, einen Hersteller von seinen Ideen überzeugen zu können. Doch bislang gelang ihm das nicht. Nun ergibt sich ein neuer Ansatz: Das schwedische Materialforschungsinstitut RISE hat ein EU-Forschungsprojekt begonnen. Es heißt „Hypelignum“. Ziel ist es, neue Wege für nachhaltig produzierte Elektronik zu finden. Neben der Empa-Nachhaltigkeitsspezialistin Claudia Som gehört nun auch Thomas Geiger zum Team des Forscherkonsortiums. Hinzu kommen weitere Wissenschaftlerinnen und Wissenschaftler aus Österreich, Slowenien, Spanien, den Niederlanden, Schweden und der Schweiz.
Bio-Platinen müssen spezielle Vorgaben erfüllen
Gemeinsam wollen die Forschenden Öko-Leiterplatten herstellen – und zwar möglichst aus verschiedenen Materialien: nanofibrillierte Zellulose (CNF), Holzwolle und Zellstoff aus Pappelholz. Thomas Geiger produziert die Leiterplatten, damit seine Kolleginnen und Kollegen die entsprechenden Tests durchführen können. Das schwedische Team hat bereits erste Erfolge mit elektronischen Komponenten aus bioabbaubaren Materialien erzielt, zum Beispiel Batterien und Displays. Bei den Platinen kommt es nun vor allem darauf an, dass diese eine hohe mechanische Festigkeit aufweisen. Desweiteren dürfen sie bei feuchten Bedingungen nicht aufquellen oder Risse bilden, wenn sie in einem Umfeld mit sehr niedriger Luftfeuchtigkeit verwendet werden.
„Cellulosefasern können eine sehr gute Alternative zu Glasfaser-Verbundwerkstoffen sein“, erklärt Thomas Geiger. „Wir entwässern das Material in einer Spezialpresse mit 150 Tonnen Druck. Dann kleben die Cellulosefasern ohne weitere Hilfsstoffe von alleine zusammen. Wir nennen das Hornifizierung. Das Entscheidende dabei ist, bei welchem Druck welcher Temperatur und für wie lange der Pressprozess stattfinden muss, um optimale Ergebnisse zu erzeugen.“
Nachhaltige Elektronik: Weitere Entwicklungen geplant
Das Forschungsprojekt „Hypelignum“ will im ersten Schritt die Leiterplatten aus nachwachsenden und kompostierbaren Rohstoffen untersuchen. Doch damit nicht genug. Es soll auch leitfähige Tinte für die elektrischen Verbindungen zwischen den Bauteilen entwickelt werden. Sie basieren häufig auf Silber-Nanopartikeln. Stattdessen wollen die Forschenden nicht nur günstigere und besser verfügbare Materialien einsetzen, sondern auch ein möglichst ökologisches Herstellungsverfahren entwickeln.
Mehr zum Thema Nachhaltigkeit in der Produktion:
- Nachhaltige Chemie- und Werkstoffindustrie baut auf Recycling, Biomasse & CO2
- 6 innovative nachhaltige Materialien für biologisch abbaubare Produkte
- Mit dem virtuellen Zwilling nachhaltige Produktionsprozesse fördern
Ein Beitrag von: