Neues Batteriegehäuse hilft Elektroautos beim CO2-Sparen
Forschende entwickeln im Projekt COOLBat innovative Batteriegehäuse für E-Autos. Ziel ist es, die Reichweite zu erhöhen und den CO2-Ausstoß bei der Herstellung um 15 Prozent zu senken. Durch Leichtbau, Integration von Funktionen und neue Materialien sollen die Gehäuse leichter und effizienter werden. Das Fraunhofer IWU koordiniert das vom BMWK geförderte Vorhaben.
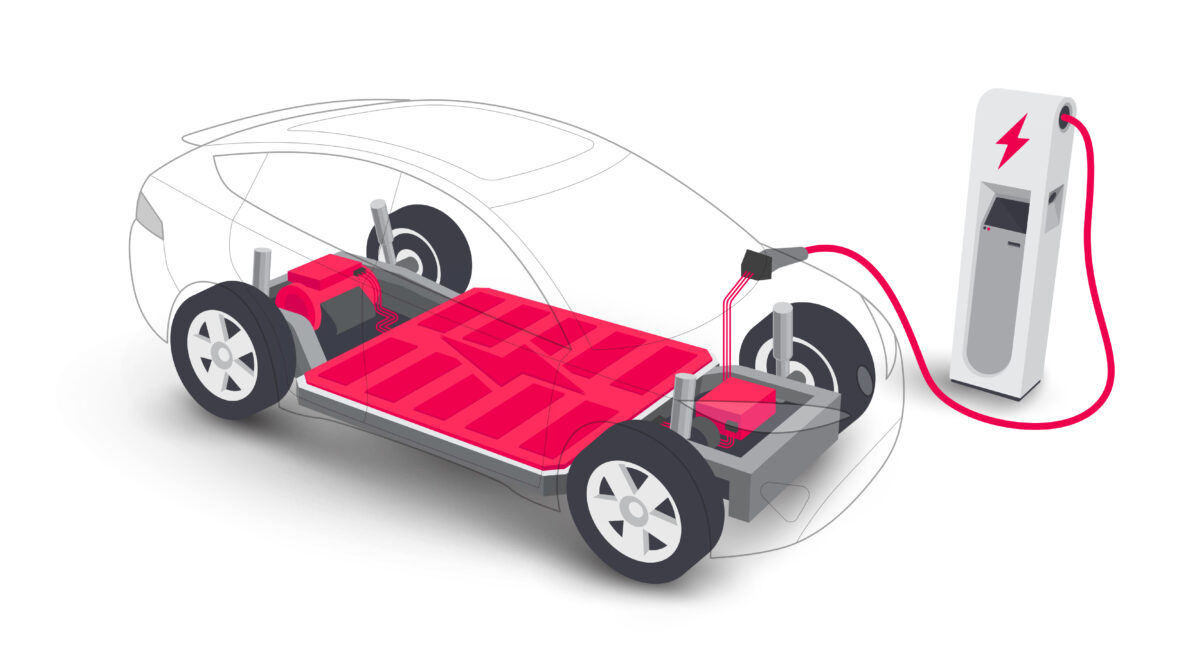
Das neue Batteriegehäuse soll E-Autos effizienter machen.
Foto: PantherMedia / petovarga
Forschende des Fraunhofer-Instituts für Werkzeugmaschinen und Umformtechnik IWU entwickeln gemeinsam mit Projektpartnern zukunftsweisende Batteriegehäuse für Elektrofahrzeuge. Das Verbundprojekt COOLBat will die zentrale Komponente des E-Autos optimieren. Ziele sind eine Gewichtsreduktion sowie eine CO2-Einsparung von 15 Prozent bei der Herstellung.
Um das zu erreichen, konzentrieren sich die Projektpartner darauf, Einzelsysteme zu kombinieren, zusätzliche Funktionen auf begrenztem Raum einzubauen sowie neue Wärmeleitwerkstoffe einzusetzen und biobasierte Flammschutzbeschichtungen zu verwenden.
Batteriegehäuse: Verschiedene Aspekte tragen dazu bei, CO2 zu sparen
Das Projekt CO2-einsparende Leichtbaulösungen am Demonstrator Batteriegehäuse der nächsten Generation (COOLBat) vereint 15 Partner aus Industrie und Forschung. Die Forschenden konzentrieren sich auf die Optimierung bestehender Strukturen zur Lastverteilung und Temperaturregulierung, einschließlich Rahmen, Deckeln und Bodenplatten.
Ihr interdisziplinärer Ansatz umfasst neuartige Leichtbau-Konstruktionen, fortschrittliche Materialien und effiziente Produktionsverfahren. Dabei berücksichtigen sie Aspekte wie Kreislauffähigkeit, Reparierbarkeit, Ressourcen- und Energieeffizienz sowie Sicherheit und Brandschutz.
CO2 durch Leichtbau-Batterien reduzieren
Die Gewichtsreduktion der Batteriegehäuse steigert die Reichweite von Elektroautos durch geringeren Stromverbrauch. Rico Schmerler, Projektleiter am Fraunhofer IWU, betont das Potenzial zur Erhöhung der Energiedichte heutiger Batteriesysteme. Durch die Integration neuer Leichtbauweisen und die Verdichtung von Funktionen auf kleinerem Raum bei gleichzeitiger Reduzierung von Schnittstellen lässt sich nicht nur Gewicht einsparen, sondern auch der CO2-Ausstoß um 15 Prozent verringern. Da für den Gehäusedeckel Faserverbundmaterialien verwendet werden, wird dadurch bereits eine Gewichtsreduktion um mehr als 60 Prozent im Vergleich zur Stahlreferenz möglich.
Die Forschenden erzielen weitere Gewichtseinsparungen, indem sie bisher getrennte Systeme im Gehäuse kombinieren. So integrieren sie Temperierkanäle direkt in tragende Strukturen wie Querträger. Zusätzlich vereinen sie die Funktionen der Kühleinheit und des Unterfahrschutzes in der Bodenplatte. Ein Aluminiumschaum absorbiert Energie bei Steinschlag und Unfällen. In Verbindung mit einem Phasenwechselmaterial reduziert er zudem den Energieaufwand zur Kühlung der Batterie. Die Bodenplatte schützt die Batteriezellen sowohl vor mechanischen Belastungen als auch vor Überhitzung.
Elektroautos mit optimierter Batterie-Technologie
Um die Wärmeableitung von Batterien zu verbessern, entwickeln die Projektpartner neue Lösungen. Anstelle herkömmlicher leitfähiger Pasten kommen nun umweltfreundliche Wärmeleitstoffe zum Einsatz. Das Fraunhofer-Institut für Schicht- und Oberflächentechnik IST metallisiert dafür offenporige, wiederverwendbare Schäume mittels Plasmaverfahren. Diese werden als Matten zwischen Batterie und Gehäuse eingelegt und optimieren die thermische Anbindung. Eine neuartige Brandschutzbeschichtung, entwickelt vom Fraunhofer-Institut für Holzforschung, Wilhelm-Klauditz-Institut WKI, erhöht die Sicherheit des Batteriegehäuses. Auf der Unterseite des Gehäusedeckels aufgetragen, verhindert sie, dass sich Feuer aus darunter liegenden Batteriezellen ausbreiten kann.
Die Beschichtung enthält das biobasierte, nicht brennbare Material Lignin als Ersatz für erdölbasierte Werkstoffe. Der Gehäusedeckel aus Stahl wurde durch eine leichtere Faserverbund-Deckelstruktur aus Kohlenstoff und Harz ersetzt. Diese Neuentwicklung ermöglicht nicht nur eine signifikante Gewichtsreduktion, sondern macht es möglich, den Deckel wiederzuverwenden. Das gesamte System aus Deckel, Rahmen und Bodenplatten lässt sich zerstörungsfrei bis auf Komponentenebene demontieren. Dieser Ansatz folgt dem Prinzip der Kreislaufwirtschaft und zielt auf Materialreduktion durch Leichtbau und wiederverwendbare Werkstoffe ab.
Die Ergebnisse versprechen einen geringeren CO2-Fußabdruck und reduzierte Kosten im Reparaturfall. Die Projektergebnisse sollen in Zukunft auf weitere Anwendungsbereiche und Branchen übertragen werden, in denen große Batterien zum Einsatz kommen. Potenzielle Einsatzgebiete sind Züge, Flugzeuge und Boote. Zudem könnten die entwickelten Kühlsysteme für Lebensmittel- und Medizintransporte adaptiert und die Brandschutzlösungen in Gebäuden eingebaut werden.
Ein Beitrag von: