Effizientere Batterien bald marktreif?
Die Wissenschaftler des Max-Planck-Instituts für medizinische Forschung haben ein Verfahren entwickelt, das demnächst die Herstellung von Batterien revolutionieren kann. Batterien sollen dadurch viel leichter, effizienter und sicherer werden.
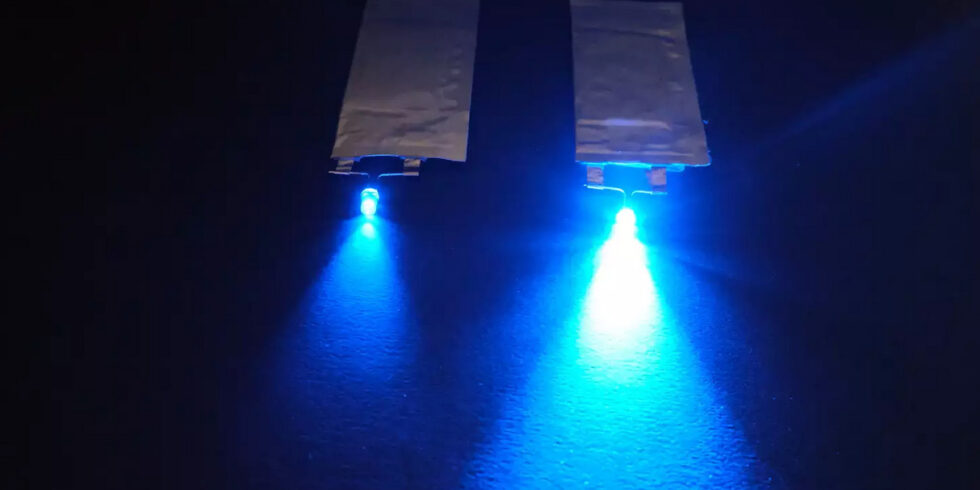
Der Unterschied zwischen der Standard Batterie (links) und der Batene Fleece-basierende Batteriezelle (rechts).
Foto: Batene GmbH
Das Forscherteam des Max-Planck-Instituts hat herausgefunden, wie man sehr feine Metallvliese herstellen kann. Sie dienen als Stromkollektoren in Batterien und können sie leistungsfähiger machen.
Die Technik, mit der sich sehr feine Metallfasern herstellen lassen, sei bereits über die Technologietransfer-Organisation Max-Planck-Innovation von der Batene GmbH lizenziert. Das Start-Up wird sie vermarkten und hat dafür eine erste Finanzierung von zehn Millionen Euro erhalten.
Neue Generation der Akkumulatoren
„Der neue Ansatz ermöglicht die Herstellung einer neuen Generation von Akkumulatoren. Die metallischen Vliese erfüllen den Wunsch nach leichteren Batterien mit hoher Energiedichte, schnelleren Ladezeiten, längeren Batterielaufzeiten und einer längeren Lebensdauer. Darüber hinaus werden durch einen deutlich reduzierten Materialverbrauch und einen äußerst energiesparenden Herstellungsprozess natürliche Ressourcen geschont“, erklärte Martin Möller, der Geschäftsführer der Batene GmbH in einer Pressemitteilung. All das helfe der Gesellschaft bei der Transformation weg von fossilen Brennstoffen hin zu einer CO2-freien Wirtschaft. „Eben dieser Schutz von Klima und Umwelt spielte in unseren Überlegungen eine ebenso wichtige Rolle wie wirtschaftliche Faktoren.“
Was steckt hinter der neuen „Batene Technologie“?
In Batterien gibt es zwei von einem Separator getrennte Elektroden (Kathode und Anode). Darin befindet sich das sogenannte Aktivmaterial, das beispielsweise aus verschiedenen Lithium-Verbindungen besteht und die Energie speichert und auf einem gut leitenden Stromkollektor aufgebracht ist. In der Regel sei an der Kathode eine Aluminiumfolie, an der Anode – eine Kupferfolie. Indem sich die Lithiumionen von einer Elektrode zur anderen bewegen, sorgen sie für den gewünschten Elektronen- beziehungsweise Stromfluss. Dafür werden die Schichten von unter 0,2 Millimeter Dicke verwendet. Und gerade an dieser Stelle setzt die neue Technologie ein: Das neu entwickelte Verfahren, mit dem sich sehr feine Metallfasern herstellen lassen, ermöglicht es, dickere Zellen zu verwenden.
So haben die amorphen metallischen Fasern eine sehr gute elektrische Leitfähigkeit und werden zu einem dichten, leitfähigen Metallgewebe verarbeitet und mit dem jeweiligen Aktivmaterial von Anode und Kathode gefüllt. Damit können die Batteriezellen sogar über zwei Millimeter dick sein – also zehn Mal so dick, wie die üblichen Zellen, was das verbaute nicht aktive Material drastisch reduzieren kann. Mit anderen Worten: Der Metallanteil wird auf ein Zehntel reduziert, doch der Anteil des Aktivmaterials wird am Gesamtgewicht der Batterie auf über 90 Prozent gesteigert.
Die Metallvliese haben eine deutlich größere Oberfläche, deshalb lassen sich Batterien mit solchen Stromkollektoren wesentlich schneller be- und entladen.
Die neuen Batterien können überall eingesetzt werden
„Die neue Technologie von Batene besitzt erhebliches wirtschaftliches Potential, da die Nachfrage nach Batterien in den kommenden Jahren weiter stark zunehmen wird, und Batteriehersteller daher auf der Suche nach neuen effizienteren Technologien sind“, sagt Bernd Ctortecka, Patent- und Lizenzmanager bei Max-Planck-Innovation, der zentralen Technologietransfer-Organisation der Max-Planck-Gesellschaft.
„Die Batene Technologie findet in jede Batterie Eingang, d.h. wir sprechen sowohl von Batterien für Autos, Power Tools, mobile Telefone und Kopfhörer oder medizinische Implantate, um einige Beispiele zu nennen. Die Batene Technologie macht jede Batteriezelle besser – unabhängig von deren Chemie und Design“, kommentierte der Direktor am Max-Planck-Institut für medizinische Forschung und Erfinder der Batene Technologie Professor Joachim Spatz unsere Anfrage.
Die neue Technologie soll in zwei Jahren marktreif entwickelt werden. Dieser Optimismus basiert, wie Spatz erklärt, insbesondere darauf, dass die Technologie eine „drop in“ Technologie darstellt. Und das heißt – sie kann direkt mit existierenden Produktionsanlagen der Batteriezell-Hersteller produziert werden.
Ein Beitrag von: