Solarzellen: Neues Verfahren verbraucht kaum Material
Eine starke Haftung, die Kosten spart und trotzdem einen hohen Wirkungsgrad garantiert – Fraunhofer-Forschende haben ein neues Verfahren vorgestellt, um Solarzellen flexibel miteinander zu verschalten. Doch ihre Methode kann noch mehr.
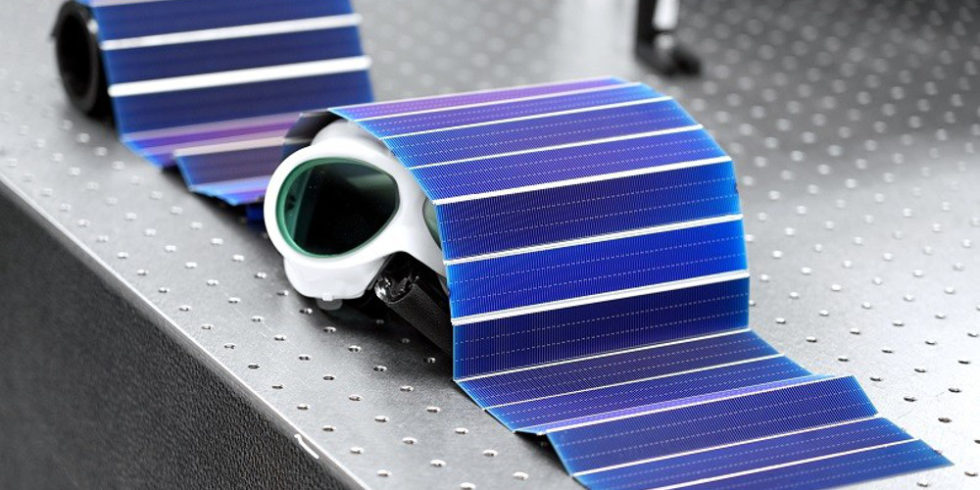
Dieser String aus Schindelzellen wurde mit dem FoilMet®-Verfahren hergestellt.
Foto: Franhofer ISE
Bei Solarmodulen zählt jedes Detail. Denn der Bedarf dürfte in den nächsten Jahren ordentlich wachsen. Schnelle und unkomplizierte Produktionsmethoden sind also gefragt. Wenn es dadurch möglich ist, zusätzlich Material zu sparen – umso besser. Das Fraunhofer-Institut für Solare Energiesysteme ISE hat jetzt eine Methode vorgestellt, mit der es möglich sein soll, Solarzellen flexibel zu verschalten und dabei weniger Ressourcen zu verbrauchen. Statt der Kleber, die meistens verwendet werden, setzen sie auf ein Laserverfahren.
Living Labs: Modellprojekte sollten Agri-Photovoltaik voranbringen
Solarzellen ohne Kleber, aber mit flexibler Verbindung
Ihre neue Methode nennen die Wissenschaftlerinnen und Wissenschaftler FoilMet. Bei der Technologie handelt es sich um ein Laserverfahren, das dafür gedacht ist, Busbarfreie PERC- und TOPCon-Solarzellen miteinander zu verschalten. Der Clou: Weder ein leitfähiger Klebstoff noch ein Lot werden benötigt. Nur eine Aluminiumfolie ist erforderlich. Das spart Ressourcen, denn es wird für ein Solarmodul bis zu 30 % weniger Silber für die Kontakte benötigt. Wir groß der Silberbedarf genau ist, hängt vom jeweiligen Elektrodenlayout ab. Zusätzlich werden die mit bleihaltigem Lot ummantelten Kupferverbinder oder der silberhaltige Klebstoff durch das Aluminium ersetzt.
Im Ergebnis ist die Verbindung mechanisch so flexibel, dass sie auf der einen Seite eine gekrümmte Auslegung des Strings ermöglicht und auf der anderen Seite eine Anordnung als geschindelte Zellen zulässt. Anders gesagt: Die Solarzellen können mit FoilMet mit dem Ziel einer maximalen Energieeffizienz der Module verschaltet werden. Parallel ist eine Bauweise möglich, die auf eine möglichst günstige Produktion der Solarmodule setzt – für die Massenproduktion werden Solarzellen mit einem geringen Abstand nebeneinander angeordnet.
Aluminium ermöglicht hohen Wirkungsgrad der Solarzellen
So funktioniert das Laserverfahren im Detail: Ein dünner Streifen Aluminiumfolie verbindet die benachbarten Solarzellen miteinander. Das funktioniert, weil es den Fraunhofer-Forschenden gelungen ist, die Folie direkt mit den Leiterbahnen zu verbinden, und zwar durch einen speziellen Laser-Mikroschweißprozess. Im Zwischenfingerbereich wird das Aluminium mit der Siliziumnitrid-Oberfläche „verschweißt“.
Die hohe Geschwindigkeit des neuen Laserverfahrens ist ein weiterer Pluspunkt. Denn nach Angaben der Wissenschaftlerinnen und Wissenschaftler brauchen sie für das Verschalten weniger als eine Zehntelsekunde pro Wafer. Was in der Praxis zudem eine große Rolle spielen dürfte: Die Kontaktwiderstände zwischen Folie und Elektroden sollen bei dieser Form der Solarzellen-Produktion sehr gering sein, was eine Voraussetzung für hohe Wirkungsgrade der Module ist.
Produktion kleiner Wafer könnte finanziell interessanter werden
Die Fraunhofer-Forschenden sehen ihr neues Verfahren nicht einfach nur als ressourcensparende Alternative zu den herkömmlichen Produktionsmethoden. Sie haben ein grundsätzliches Problem im Blick: „Verschaltet man viele kleine Zellen anstelle von wenigen Großen, wird der darin generierte Strom und Widerstandsverlust kleiner und die Spannung größer. Trotz dieser vorteilhaften Eigenschaften ist ein Solarmodul aus vielen kleinen Zellen aufwendiger und teurer in der Verschaltung – genau das adressieren wir mit FoilMet®“, sagt Jan Paschen, der als Doktorand zur Gruppe Laserprozesstechnologie des Fraunhofer ISE gehört.
Branchenpreis: Zukunftsweisende Solartechnik gewürdigt
Jan Nekarda, Abteilungsleiter Strukturierung und Metallisierung am Fraunhofer ISE, ist davon überzeugt, dass das neue Solarzellen-Herstellungsverfahren bei der Industrie auf großes Interesse stoßen wird: „Das faszinierende an unserer Technologie ist, dass es einerseits aufgrund der geringen elektrischen Widerstände und der Möglichkeit zum Schindeln hohe Modulwirkungsgrade und Ästhetik verspricht und zusammen mit der sehr hohen mechanischen Flexibilität des Strings für Nischenanwendungen in der integrierten Photovoltaik prädestiniert erscheint. Andererseits macht das hohe Potenzial zur Kosten- und Materialeinsparung das Verfahren zusätzlich interessant für den PV-Massenmarkt.“
Praxistests der Solarzellen laufen an
Aktuell planen die Ingenieurinnen und Ingenieure eine Pilotanlage, mit der sie die Solarzellen in großer Stückzahl herstellen wollen. Parallel sollten die per Laser verbundenen Solarzellen einem Praxistest unterzogen werden. Denn Aluminium ist kein Standardmaterial für die Verschaltung und muss sich erst noch unter Beweis stellen.
Mehr Innovationen zum Thema Solarmodule:
Ein Beitrag von: