Elektrofahrzeuge sind Lithium-Lagerstätten der Zukunft
Mitten im idyllischen niedersächsischen Harz läuft eine der weltweit ersten Anlagen zur Lithium-Rückgewinnung aus Fahrzeugbatterien. Noch handelt es sich dabei um ein staatlich gefördertes Pilotprojekt. Doch ihre bisherigen Ergebnisse lassen darauf hoffen, dass das Batterierecycling eines der kleineren Probleme der Elektromobilität sein wird.
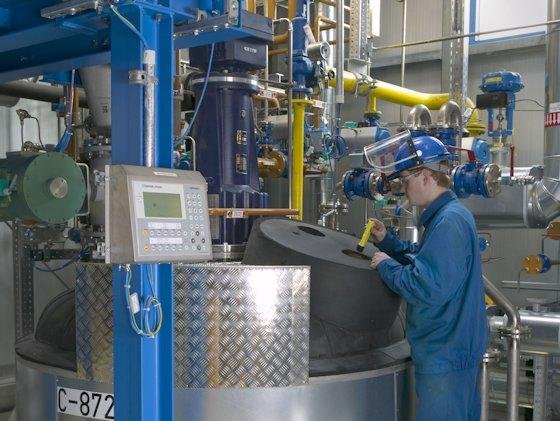
Im Reaktor wird das Aktivmaterial der Kathoden unter Einsatz von Säuren in eine Lithiumsalzlösung überführt.
Foto: Rockwood Lithium
Katrin Wessels öffnet die Tür zur Anlage. Erster Eindruck: Ein leicht stechender Geruch. Als die Prozesschemikerin der Rockwood Lithium GmbH die nächste Tür öffnet, fällt der Blick in eine Halle voller Tanks und Rohrleitungen. Hier nimmt ein vielstufiger Aufbereitungsprozess seinen Anfang, auf dem große Hoffnungen der Automobilindustrie ruhen.
Wessels und ihr Team wollen hier, in dem äußerlich unscheinbaren Sechsgeschosser im Chemiepark Langelsheim nachweisen, dass sich Lithium aus ausgedienten Akkus von Elektrofahrzeugen zurückgewinnen lässt. Und zwar mit Reinheitsgraden, die den erneuten Einsatz in Fahrzeugbatterien erlauben. Durch einen solchen Materialkreislauf würde die Elektromobilität zur runden Sache.
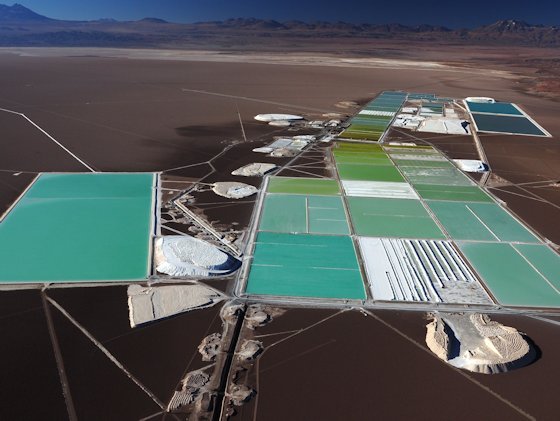
Elektrofahrzeuge sind Lithium-Lagerstätten der Zukunft
Bis 2050 will Deutschland seinen CO2-Ausstoß um 80 % senken. Pkw sollen dann im Schnitt unter 40 g/km CO2 ausstoßen. Das ist weniger als ein Drittel des heutigen Flottendurchschnitts. Allein mit Verbrennungsmotoren wird das nicht machbar sein. Traktionsbatterien werden Kraftstofftanks schrittweise verdrängen. Bis 2020 sollen Steckdosen-Hybride und reine Elektroautos Massenmarkt-tauglich sein. Spätestens nach 2030 dürfte dann die Menge ausgedienter Batterien zunehmen. Je nach Typ bergen sie über 20 kg Lithium-Carbonat-Äquivalente, die zu etwa einem Fünftel aus Lithium bestehen. Diesen Schatz gilt es zu heben.
2030 klingt weit hin. Doch wo ein komplett neues Recyclingverfahren entwickelt und auf Industriemaßstab skaliert werden muss, vergehen Jahre wie im Flug. Schon 2009 haben sich deshalb Unternehmen und Hochschulen in staatlich geförderten Forschungsprojekten aufgemacht, um Recyclingpfade für Lithium-Ionen-Batterien zu erkunden. Die Pilotanlage hier im niedersächsischen Städtchen Langelsheim zählt zu ihren ersten steingewordenen Ergebnissen.
Lithium wird seit den 1920er Jahren in Niedersachsen gewonnen
Gerahmt von einem Harz-Idyll mit bewaldeten Hügeln und blühenden Rapsfeldern betreibt Rockwood Lithium hier mit weiteren Unternehmen einen Chemiecampus. Lithium wird in Langelsheim seit den 1920er-Jahren verarbeitet. Die 9 Mio. € teure Anlage, zu welcher der Bund ein Drittel beisteuerte, ist seit gut anderthalb Jahren in Betrieb. „Grob gesagt scheiden wir hier Lithium aus Kathodenmaterial ab und stellen hochreines Lithium-Hydroxid für die Batterieproduktion daraus her“, erläutert Katrin Wessels. Zudem würden sogenannte Übergangsmetallsalze aus dem Batterieschrott gewonnen – etwa Cobalt-, Nickel- und Mangansulfate, die ebenfalls zur Herstellung neuer Batterien eingesetzt werden können.
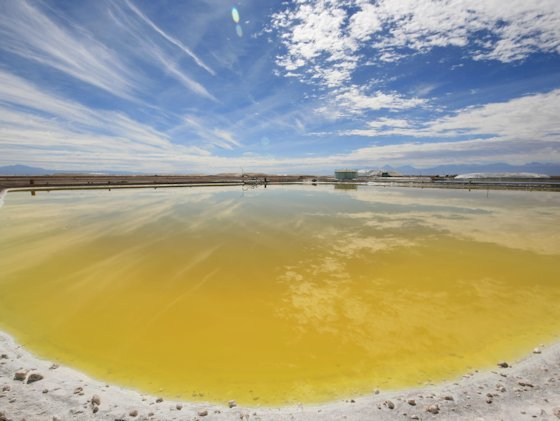
Elektrofahrzeuge sind Lithium-Lagerstätten der Zukunft
Was einfach klingt, ist ein komplexes Zusammenspiel aus über 60 Apparaten und Reaktoren, 2,5 km Rohrleitungen und 15 km Kabel, die unter anderem ein Netzwerk von 400 Mess- und Regeleinheiten verbinden. „Wir nehmen hier jede Sekunde einen Messwert“, berichtet die junge Chemikerin. Allerdings räumt sie ein, dass für den Probebetrieb noch nicht genug Material aus Batterien bereitsteht. Stattdessen bereite man stark verunreinigte Lithium-Chlorid-Lösung vom Campus auf, die aber dem Gehalt von Proben aus zerlegten Batterien sehr nahe komme.
Wegen der Rostgefahr: Werkhalle aus Holz
In der ebenerdigen Eingangshalle mit dem Tank- und Rohrgewirr wird die Lösung vorbereitet. Beim Blick nach oben fällt unerwartet eine hölzerne Decke ins Auge. „In der Anlage werden hoch korrosive Medien verarbeitet. Holz rostet nicht“, erklärt Wessels.
Künftig wird hier der erste Aufschluss stattfinden. „Einerseits geht es darum, alle metallischen Inhaltsstoffe des Aktivmaterials in Lösung zu bringen und andererseits die festen Inhaltsstoffe abzuscheiden“, so Wessels. Wenn Batteriematerialien verarbeitet werden, werden sich in den Abscheidern alle erdenklichen Batteriereste sammeln: Graphit, Elektrolyt, Binder, Partikel der metallischen Anoden- und Kathodenfolien. Die Anlage ist die finale Stufe einer langen Prozesskette, die im Förderprojekt „LithoRec“ entwickelt wurde.
Zunächst sollen die Batterien ausgebaut, entladen und teil-automatisch demontiert werden. Während Metallgehäuse, Kunststoffe und Kabel ins übliche Recycling wandern, werden die vereinzelten Batteriezellen tief-entladen, um das Lithium möglichst komplett in der Kathode zu sammeln. Danach gehen die Zellen durch Schredder und mehrere Sortieranlagen. Übrig bleibt ein schwarzes Pulver: das Lithium-haltige Aktivmaterial der Kathode. In Salzsäure gelöst, gleicht es der hier verarbeiteten Lithium-Chlorid-Lösung.
In der Halle startet der Prozess, bei dem zunächst Aktivmaterial und Säuren exakt dosiert zusammengebracht werden sollen. Ein Stockwerk darüber folgt eine zweite, feinere Filterung in Dutzenden hüfthohen Tanks. Die Lithium-Salzlösung durchfließt darin Taschenfilter, um feinste organische und anorganische Reste abzuscheiden. Nebenan werden Konzentration und ph-Wert der Lösung nachjustiert. Nun ist die Lösung bereit für den entscheidenden Teil des Prozesses: die Salzspaltung.
Exakter Produktionsprozess – Details bleiben geheim
In diesem Teil der Anlage fallen die Erläuterungen der Rockwood Lithium-Experten kurzsilbig aus. Der hohen Ströme, Säuren und Laugen wegen bleibt Besuchern der Zutritt verwehrt. Und wohl auch ein wenig, weil sich hinter der Glasfront nicht nur Lithium-Lauge, sondern auch geballtes Know-how konzentriert. Im Abschlussbericht der ersten „LithoRec“-Projektphase ist nachzulesen, was bei dieser Salzspaltung prinzipiell vor sich geht: aus Lithium-Chlorid (LiCl) und Wasser (H2O) entsteht per Elektrodialyse Lithium-Hydroxid (LiOH) und Salzsäure (HCl). Alternativ wandelt der Prozess Lithium-Sulfat und Wasser in LiOH und Schwefelsäure.
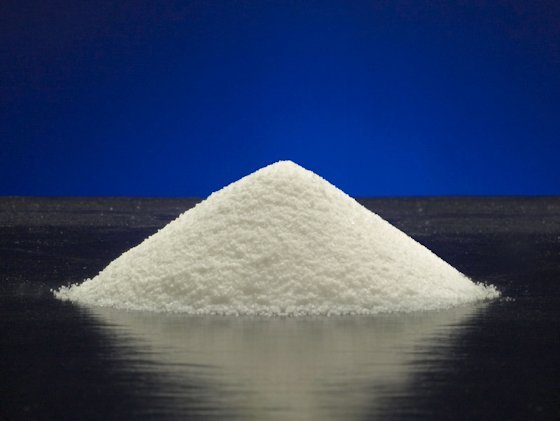
Elektrofahrzeuge sind Lithium-Lagerstätten der Zukunft
Die Lithium-Salze werden in bipolaren Membranen mit Strom in Lauge (LiOH) und die jeweils korrespondierende Säure gespalten. Die Forscher hatten hierbei lange mit unerwünschten Ionenflüssen durch die Membranen zu kämpfen. Ergebnis waren Verunreinigungen des Lithium-Hydroxids. Diese Nuss ist inzwischen geknackt. Wie genau möchte die Chemikerin nicht an die große Glocke hängen.
Offener wird Wessels einige Treppenabsätze höher. Hier oben endet der Prozess in einer Vakuum-Kristallisationsanlage, die sich mit gut 2,5 m Durchmesser über drei Stockwerke nach unten zieht. Weil sie in das vorher leer stehende Gebäude nicht hineinpasste, wurde eigens ein Neubau geplant und dann um den „Kristaller“ und seinen ebenfalls meterlangen Wärmetauscher gebaut. „In den Altbau ließen sich viele Aggregate nur per Kran durch das Dach hieven“, erinnert sich Wessels an die teils nervenaufreibende Bauphase.
Nur reines Lithium-Hydroxid bildet Kristallgitter
Mittlerweile verblasst diese Erinnerung. Der „Kristaller“ arbeitet und führt das gelöste Lithium-Hydroxid in hoch reinen kristallischen Feststoff über. Dabei senkt das Vakuum den Siedepunkt der eingeleiteten Lauge auf etwa 80 °C. Vorteil dieser abschließenden Kristallisation: nur reines Lithium-Hydroxid bildet Kristallgitter, die verbliebenen Verunreinigungen bleiben in der Flüssigkeit und können abgeleitet werden.
Drei Stockwerke tiefer spuckt die Anlage nach dem abschließenden Zentrifugieren festes Lithium-Hydroxid mit über 99-prozentigem Reinheitsgrad aus. Auch wenn die Pilot-Anlage nicht wirklich Aktivmaterial aus Altbatterien verarbeitet, sind die Forscher zuversichtlich, dass ihr Verfahren Elektrofahrzeuge zu einer wichtigen Lithium-Lagerstätte der Zukunft macht.
Eine günstige Alternative wäre es, Lithium-Akkus durch Kombination pyro- und hydrometallurgischer Prozesse zur recyceln. Die Batteriezellen gehen hier komplett in Schmelzöfen, die ihre brennbaren Materialanteile befeuern. Recycelt werden nur die Metalle, die als polymetallurgische Mixtur anfallen und hydrometallurgisch aufbereitet werden. Das Lithium sammelt sich in Schlacke, die in der Zementindustrie für schnell bindenden, wasserdichten Beton begehrt ist. Forscher arbeiten an Verfahren, das Lithium aus der Schlacke nasschemisch zu isolieren.
Pro Batterie gehen bis 5 kg Lithium verloren
Solange ihnen das nicht gelingt, gehen pro Batterie 4 kg bis 5 kg reines Lithium verloren. Ein mühsam gewonnenes Element, das wahlweise im Bergbau oder in Salzwüsten isoliert wird. Mehr als ein Jahr braucht Rockwood Lithium in seiner Anlage in Chile, um den Lithium-Gehalt von Salzlauge in riesigen Becken durch Verdunstung von 0,16 % auf 6 % zu steigern, um dann Lithium-Salze daraus zu gewinnen.
Zwar wachsen die Produktionskapazitäten weltweit, und Lithium gilt nicht als Mangelware, doch die Lagerstätten liegen aus europäischer Sicht geostrategisch ungünstig. Ohne Recycling bleibe Mobilität in ähnlichem Maße importabhängig wie beim Erdöl. Die Rückgewinnung aus Fahrzeugbatterien drängt sich also auf.
Das gilt umso mehr, als bisher drei Viertel der globalen Produktion in Bereiche gehen, in denen Recycling nicht machbar ist. Größter Absatzmarkt sind Kochfelder, in denen Lithium-Zusätze die Ausdehnung des Glases minimieren. Daneben gibt es Dutzende Nischenanwendungen – vom Zusatz zu Airbag-Zündern, LED-Farbstoffen, Schmierstoffen, Pflanzenschutzmitteln, Schnellzement oder Antidepressiva bis zur Nutzung als CO2-Absorptionsmittel, das in U-Booten, Raumschiffen oder Bergbauschächten Atemluft aufbereitet.

Elektrofahrzeuge sind Lithium-Lagerstätten der Zukunft
Mit der Elektromobilität entsteht nun ein Markt, der die globale Lithium-Nachfrage zwischen 2012 und 2020 nicht nur auf über 300 000 t verdoppeln könnte, sondern in dem nahezu geschlossene Lithium-Kreisläufe möglich scheinen. Die kleine Langelsheimer Pilotanlage könnte dann weltweite Bedeutung erlangen.
Ein Beitrag von: