Elektrolyse: das Rückgrat von Power-to-Gas
Wohin mit überschüssigem Wind- und Solarstrom? Eine Option ist Power-to-Gas; elektrische Energie wird in Materie gespeichert. Doch kein Power-to-Gas ohne Elektrolyse. Ein Forschungsprojekt soll nun ein Elektrolysesystem entwickeln, das in seiner Leistung und seinen Eigenschaften auch den Anforderungen an kommende Anlagen gerecht wird.
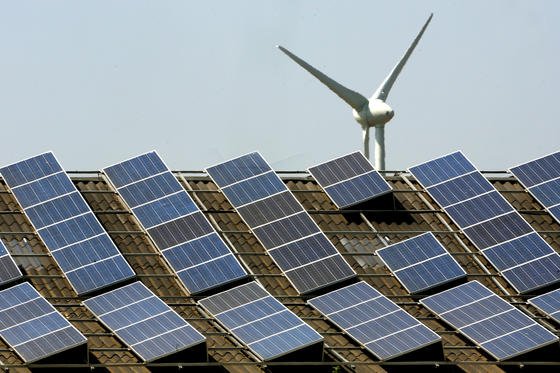
Power-to-Gas gilt als eine Möglichkeit zur Speicherung von überschüssigem Wind- und Solarstrom.
Foto: dpa
Der Erfolg der erneuerbaren Energien hat im Bereich der Stromversorgung eine neue Frage aufgeworfen: Wie lässt sich überschüssiger Strom aus Wind- und Photovoltaikanlagen speichern? Als eine Option gelten Lösungen mit „Power-to-Gas“ (P2G).
Hier wird der Strom verwendet, um in einem ersten Schritt per Elektrolyse Wasserstoff zu erzeugen. Dieser kann entweder direkt genutzt oder im Erdgasnetz beigemischt werden. Er kann aber auch in einem zweiten Schritt für die Speicherung weiter umgewandelt werden, etwa zu Methan – sprich Erdgas.
Dementsprechend vielfältig sind die Forschungsaktivitäten. In einer P2G-Strategieplattform etwa engagieren sich Teilnehmer aus den Bereichen Strom- und Gaswirtschaft, Anlagenbau und Anwendungstechnik, Forschung und Entwicklung sowie Branchenverbände.
Aktuell testet RWE Power am Kraftwerk Niederaußem ein System von Siemens. Ein Teil des erzeugten Wasserstoffs soll genutzt werden, um mit CO2 aus dem Kraftwerksrauchgas Methan herzustellen. So könne die P2G-Prozesskette unter realen Bedingungen erprobt werden.
Mit der direkten Umwandlung des im Biogas enthaltenen CO2 in Methan hat das Fraunhofer-Institut für Windenergie und Energiesystemtechnik IWES am Hessischen Biogas-Forschungszentrum, Bad Hersfeld, eine andere Technologie getestet. Diese neue „Spielart“ von Power-to-Gas erschließe bei einer Leistung von 25 kW nicht nur einen weiteren Pfad zur Methangewinnung. Sie eröffne auch die Möglichkeit, Biogasanlagen in Zukunft flexibler und bedarfsgerechter zu betreiben, unterstreicht Co-Institutsleiter Clemens Hoffmann. Die Technologie wurde vom IWES gemeinsam mit dem Zentrum für Sonnenenergie- und Wasserstoff-Forschung Baden-Württemberg (ZSW) und dem Power-to-Gas-Spezialisten Solar Fuel entwickelt.
Ein zentrales Thema in der Branche ist derzeit aber die Erzeugung von Methan mit anschließender Einspeisung in das vorhandene Gasnetz. So hat das ZSW im Oktober 2012 eine P2G-Anlage mit einer elektrischen Anschlussleistung von 250 kW zur Wasserstoff- und Methanherstellung in Betrieb genommen.
Die Anlage in Stuttgart ist nach Angaben der Betreiber die weltweit größte ihrer Art. Nun soll eine neue, noch leistungsstärkere Elektrolyse in direkter Umgebung dieser Anlage entstehen, sagt der Projektleiter Andreas Brinner. „Die Elektrolyse ist die Schlüsseltechnologie für P2G-Anwendungen.“
Die aktuellen Probleme lägen in den spezifischen Kosten, der Apparategröße, der Möglichkeit zur Serienfertigung, der Lebensdauer und der Wartungsfreundlichkeit. „Mit diesen Themen beschäftigt sich deshalb auch das neue Projekt. Besonders der Kostenaspekt und die Serienherstellbarkeit wurden in dieser Form noch nicht angegangen.“
Zweck der 250-kW-Anlage sei, den Gesamtprozess darzustellen und im Betrieb zu optimieren, sagt Brinner. Kommerziell ist die Anlage nicht. „Sie ist nicht nach Gesichtspunkten der Kostenoptimierung konzipiert, sondern darauf ausgerichtet, im Kleinmaßstab möglichst optimal Wasserstoff herzustellen.“
Die hier eingesetzte Wasserstofferzeugung mit alkalischer Druckelektrolyse sei in der Leistung bei etwa 300 kW begrenzt. „Für künftige Anwendungen in P2G-Anlagen wird aber über 1 MW benötigt. Bei dem neuen Projekt entwickeln wir eine 300-kW-Elektrolyse, die dann auf 1 MW skaliert werden kann.“ So soll die neue Technik künftigen P2G-Anlagen den Weg in eine größere Leistungsklasse ebnen. Partner des Projektes sind Solar Fuel und der Windenergie-Projektierer Enertrag.
Im Gegensatz zu etablierten Industrieanwendungen – dort finden sich einzeln hergestellte Elektrolyseure im MW-Maßstab – ist bei dem neuen Projekt der Wasserstoff nur ein Sekundärenergieträger für die Zwischenspeicherung.
„Dieser muss so preiswert und effizient wie möglich hergestellt werden“, sagt Brinner. Man wolle Druckelektrolysen entwickeln, die im Druckbereich und in der Funktionsweise an die P2G-Prozesse angepasst sind. „Dazu werden wir die Stromdichtebereiche, also die Fläche der Elektrolyse und den Druckbereich, so einstellen, dass sie für P2G optimal sind.“ Zudem müsse die Elektrolyse gegenüber Industrieanlagen auch kompakter werden.
Für Brinner stellt der Kostenfaktor eine besondere technische Herausforderung dar. „Heutige Industrieanlagen kosten zumeist noch 1000 € bis 2000 € pro kW installierter Leistung. Für P2G-Anlagen müssen die Kosten auf wenige hundert Euro pro kW gesenkt werden.“
Auf dem Prüfstand steht die Lebensdauer. Sie liegt bei aktuell eingesetzten Elektrolyseanlagen in der Industrie bei 30 bis 50 Jahren, sagt Brinner. Etwa alle sieben bis zehn Jahre erfolge eine Komplettrevision, Konstantbetrieb sei das Hauptziel. „Bei P2G müssen wir uns an den Lastzyklen der Energieversorger orientieren. Eventuell muss die Anlage bis zu fünfmal am Tag an- und abgefahren werden – je nach Energieprofil.“
Sie wäre dann nicht mehr auf konstanten Dauerbetrieb bei konstanter Betriebstemperatur ausgelegt. Vielmehr müsste sie eine möglichst hohe Zahl an Lastwechseln mit Berücksichtigung kurzzeitiger Abkühl- und Aufheizphasen vertragen können.
Zu den technischen Neuerungen zähle dabei auch eine neue Elektrodenbeschichtung. „Die derzeitigen Beschichtungen haben in der Regel eine zu geringe Langzeitstabilität“, erläutert Brinner. „Alles, was es heute an guten Beschichtungen für einen niedrigen spezifischen Energieverbrauch gibt, ist entweder teuer oder braucht auch im Stand-by-Betrieb Energie.“ Vielfach degradiere die Beschichtung mit wachsender Start-Stopp-Anzahl. Im Extremfall werde sie binnen zwei Jahren unwirksam. „Wir streben aber Wartungsintervalle von fünf bis sieben Jahre an.“
Das ZSW sei kein Elektrolysehersteller, stellt Brinner klar. Doch wolle man schon so nah wie möglich an das Marktziel herankommen. „Dazu konzipieren wir ein erstes Exemplar, bauen es auf und demonstrieren die Machbarkeit im Versuchsbetrieb.“
Für eine Serienfertigung müssten dann noch Unternehmen überzeugt werden. „Die Strategie ist deshalb, möglichst viele Teilsystemhersteller mit einzubeziehen, die mit ihren Fertigungsprozessen die Funktionen, die wir gerne hätten, mit den von uns angestrebten Rahmenbedingungen umsetzen.“ Das Problem sei, dass man zwar eine Vorstellung habe, wo man hin wolle, aber es müsse auch ein kostengünstiger Herstellungsprozess dafür gefunden werden.“ ROBERT DONNERBAUER
Ein Beitrag von: