Große Rotorblätter auf dem Prüfstand
In den Offshore-Windparks sollen Rotoren mit mehr als 150 m Durchmesser zum Einsatz kommen. Ob die Rotorblätter der neuen Generation mindestens 20 Jahre lang den Belastungen des Offshore-Einsatzes gewachsen sind, muss durch statische und dynamische Prüfungen ermittelt werden, die insgesamt möglichst nicht länger als ein Jahr dauern sollen.
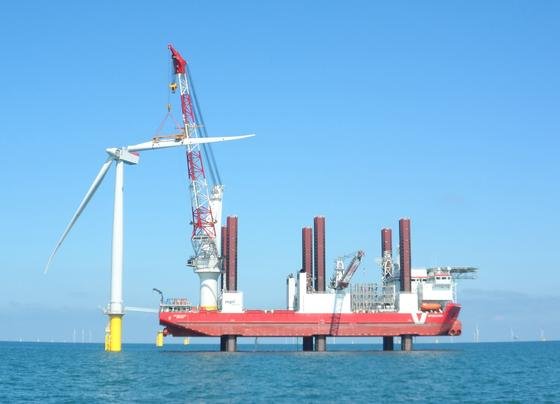
Die Windturbinen von London Array, dem größten Offshore-Windkraftwerk der Welt, werden in Wassertiefen bis zu 23 Metern installiert. Der Standort weist eine durchschnittliche Windgeschwindigkeit von 9,2 Metern pro Sekunde auf. Das Foto zeigt die Installation des zweiten Rotorblatts an einer Windturbine.
Foto: Siemens
Mit der Errichtung zweier Windenergieanlagen in der Themsemündung hat Siemens im vergangenen Januar mit der Erprobung der neuen Offshore-Leistungsklasse auf See begonnen. Es handelt sich um Windenergieanlagen mit einem Rotordurchmesser von mindestens 150 m und einer Leistung von 6 MW und mehr.
Im vergangenen Sommer hatte bereits Alstom einen 6-MW-Prototyp an der französischen Atlantikküste errichtet und die Erprobung des zweiten Prototyps im Meer soll in Kürze folgen.
Der koreanische Konzern Samsung entwickelt einen Prototyp mit 7 MW Leistung. Dessen Rotorblatt hat eine Länge von 83,5 m und wird zurzeit durch das Fraunhofer-Institut für Windenergie und Energiesystemtechnik (Iwes) am Standort Bremerhaven getestet.
Größere Halle nötig
Das 2009 gegründete Fraunhofer-Forschungsinstitut begann mit einer Halle für 70 m lange Rotorblätter, doch diese reichte schon bald nicht mehr aus, so dass schon zwei Jahre später eine zweite Halle errichtet wurde, in der 90 m lange Rotorblätter getestet werden können.
Rotorblätter dieser Größe stellen alles in den Schatten, was bisher aus glasfaserverstärktem Kunststoff (GFK) hergestellt wurde. Die Anzahl der Lastwechsel, denen sie standhalten müssen, übertrifft das Niveau von Strukturen aus der Luftfahrt und dem Schiffbau bei Weitem.
Rotorblätter sollen 20 Jahre lang halten
Ob die Rotorblätter der neuen Generation mindestens 20 Jahre lang den Belastungen des Offshore-Einsatzes gewachsen sind, muss durch statische und dynamische Prüfungen ermittelt werden, die insgesamt möglichst nicht länger als ein Jahr dauern sollen.
Eine extrem starke Windbö verursacht eine statische Last, die auf dem Prüfstand nachgebildet werden muss.
Zunächst wird die Belastung der kompletten Windenergieanlage mithilfe spezieller Software simuliert, und es werden entsprechend der Prüfrichtlinien über 200 Lastfälle durchgerechnet.
Anschließend sind für alle Punkte des Rotorblattes die Lasten bekannt, die bei einem Extremwindereignis auftreten können. Auf diese Lasten werden Sicherheitsbeiwerte aufgeschlagen und die sich daraus ergebenden Maximalkräfte werden im Test geprüft.
Bei maximaler Belastung biegt sich ein 90 m langes Rotorblatt bis zu 30 m durch
Die extreme Durchbiegung des Blattes wird also regelrecht konstruiert, denn man legt nicht nur an einem, sondern an mehreren Punkten gleichzeitig die errechneten Maximalkräfte des Blattes an. Das waagerecht eingespannte, von mehreren Lastscheren umklammerte Rotorblatt wird durch Dyneema-Seile mit Hydraulikzylindern verbunden, die im Boden verankert sind. Kraftmessdosen zwischen Rotorblatt und Belastungsseil kontrollieren die Kraftaufbringung der einzelnen Zylinder, um die gewünschten Lasten während des statischen Tests sicherzustellen.
Der rund 1000 t schwere Einspannblock wird nun langsam geneigt, so dass sich das Blatt immer weiter durchbiegt und mithilfe der Hydraulikzylinder immer größer werdende, aber definierte Kräfte auf das Blatt übertragen werden. Bei maximaler Belastung biegt sich ein 90 m langes Rotorblatt bis zu 30 m durch.
Wesentlich weniger Kraftaufwand erfordert der dynamische Test. „Denn auch ein extrem langes Rotorblatt ist so elastisch, dass man es, wenn man an der Blattspitze steht, mit Daumen und Zeigefinger zum Schwingen bringen kann“, beschreibt Arno van Wingerde, der Business Leader Research des Iwes, die erstaunlichen Eigenschaften des Prüflings. Aber weil die Eigenschwingungen langer Rotorblätter im Bereich von nur 0,3 Hz bis 0,5 Hz liegen, braucht ein Dauerschwingversuch viel Zeit.
Um Lastzyklen und damit Zeit zu sparen, muss man die Belastung deutlich erhöhen, was relativ einfach möglich ist, denn durch Anregung der Eigenschwingung sind sehr hohe Belastungen möglich.
Keine Prüfung bis zum Bruch
Eine Prüfung bis zum Bruch ist aber nicht beabsichtigt. Die dynamische Belastung soll lediglich das Äquivalent der Ermüdungslasten während der Lebensdauer abbilden. Die millionenfachen Lastwechsel mit unterschiedlichen Amplituden, die das Rotorblatt innerhalb von 20 Jahren „erlebt“, werden auf maximal 5 Mio. Lastwechsel konstanter Amplitude reduziert.
Für die Anregung genügt ein Hydraulikzylinder, der im Boden verankert und mit dem Blatt fest verbunden ist. Die gewünschte Verteilung des Biegemoments entlang des Rotorblattes kann durch Zusatzmassen oder eine leichte Variation der Testfrequenz erreicht werden.
Um die konstante Amplitude zu berechnen, die letzten Endes entscheidend ist für die Aussage über die Lebensdauer des Blattes, setzt man für alle Abschnitte des Rotorblattes ein Lastspektrum an und berechnet daraus die Ermüdung.
„Wenn man alles richtig macht und alle Lasten auf dem Blatt stehen, dann hat man die richtige Biegemomentenverteilung auf dem Blatt und man kann für jeden Teil des Blattes die äquivalente Ermüdungsbelastung ausrechnen“, erklärt Arno van Wingerde.
Bis zu fünf Millionen Zyklen
„Anschließend addiert man eine Testbelastung, so dass die während des Betriebs auftretende Schädigung überschritten wird. Wenn das Rotorblatt auch diesem Test standhält, der 1 Mio. bis 5 Mio. Zyklen umfasst, dann schließen wir daraus, dass das Blatt 20 Jahre lang halten wird.“ Die Schwingung in Schlagrichtung (also senkrecht zur Rotorebene) wird ebenso getestet wie die Schwingung in Schwenkrichtung, die beispielsweise bei einer Notbremsung auftritt.
Der Testzeitraum lässt sich im Prinzip verkürzen, wenn man das Blatt gleichzeitig in beide Richtungen schwingen lässt, so dass seine Spitze eine Lissajous-Figur beschreibt. Dieser biaxiale Ermüdungstest kommt der tatsächlichen Belastung, der das Rotorblatt im Betrieb ausgesetzt ist, deutlich näher, ist jedoch noch nicht ausgereift. Dieses neue Testverfahren wird zurzeit am Fraunhofer Iwes erprobt.
Ein Beitrag von: